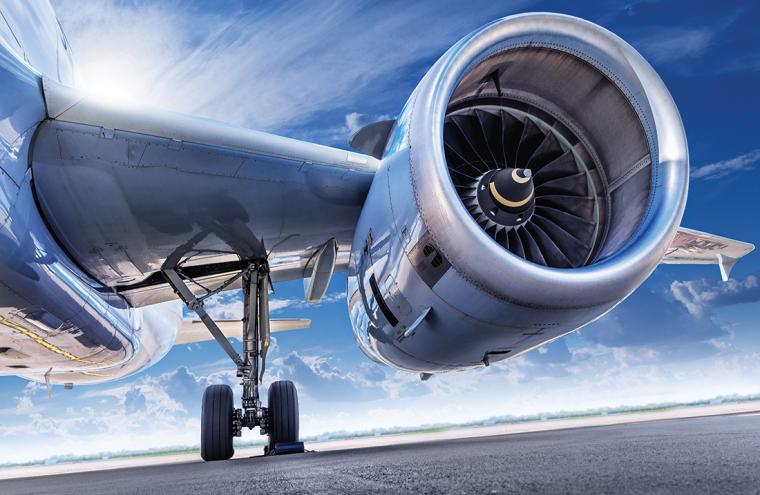
Industry Composition. This article will explore trends shaping the aerospace industry and the roadmap to select favorable locations for new (or relocated) operations. The aerospace industry is composed of several segments, as noted below.
The industry embraces both commercial and defense sectors. Moderate to strong growth has taken hold since the pandemic. Global revenue (including commercial and defense) reached $856 billion in 2023. Per annum growth from 2024-2030 is forecast to be around eight percent.
The Trends Fueling Changes in the Industry
Underlying drivers fueling industry growth include:
1. Increasing air travel
2. Rising defense spending including military modernization
3. Renewed interest in space exploration
4. Popularity of unmanned aerial vehicles (UAVs)
5. Strong demand from emerging economy nations
6. The onset of Advanced Air Mobility (AAM):
• An air transportation system that moves people and goods between points using specialty aircraft such as remotely piloted, autonomous and vertical take-off/landing. This category includes aircraft powered by electric or hybrid electric propulsion systems in both controlled and uncontrolled airspace
• AAM seeks to integrate unmanned aerial systems and
sustainable aircraft (e.g., electric vertical takeoff/landing)
7. Technological advancements such as:
• Innovations in materials, propulsion systems and avionics
• Manufacturing automation, especially digital transformation (from a model-based enterprise to digital twins to additive manufacturing).
Despite a convergence of growth dynamics, the aerospace industry does face headwinds. The most prominent challenges are detailed in the following section.
1. Supply chain complexity/risk:
• Raw material shortages
• Reliance on several key raw materials (such as critical minerals) in countries with adverse geo/political policies
• A complex, globalized ecosystem of customers, OEMs, multiple tiers of suppliers and numerous maintenance, repair and overhaul providers
• This complexity makes implementing diversity and transparency across the supply chain complicated but nonetheless imperative.
• Remedies include digitization, maintaining strategic sources of raw material reserves, bulk buying of long lead time items, developing alternate sources of supply, friendshoring, and — where pertinent — cross-border sourcing or nearshoring.
2. Sustainability and emissions reductions requiring innovation in materials, fuel and manufacturing.
3. Geopolitical risk, which can negatively impact sourcing, manufacturing and demand (e.g., reduced sales to antagonist countries)
4. A protracted talent shortage based on demographic trends and deficiencies of both technical and foundational skills
5. Workforce issues, both recruiting and retention, that will become a significant pain point for aerospace companies.
Following are some strategies that aerospace companies could be implementing to tackle workforce challenges:
• Increased compensation, both wages and pay-for-performance
• Benefits, which often need to be adjusted to reflect local labor market dynamics
• Personal Time Off (PTO) policy that recognizes work/life balance
• To the extent possible, flexibility in working hours
• Digitizing the onboarding process
• Demonstrating career pathways
• Adding pre-apprenticeships to apprenticeship programs
• Increasing paid internships
• Working closely with workforce and economic development groups
• Partnering with technical schools and colleges
• Promoting the company’s mission, values and brand in local labor markets
The labor shortage is not universal. Some locations face a far greater deficit than others. It is therefore critical to identify locations that have a favorable set of labor market conditions for a new manufacturing or R&D operation.
Global Footprint
Among the countries with the largest aerospace industries are the United States, which is the leader, followed by France, Germany, the United Kingdom, Canada, Italy, China, Spain, Singapore, Brazil, Israel and Ireland. Japan is also well represented, particularly in R&D and space communication. Countries with smaller but growing aerospace industry presences include Portugal, Malaysia, Morocco and Mexico.
WDGC is seeing an increased level of Foreign Direct Investment (FDI) within the aerospace sector. FDI to the U.S. is driven by market size/growth, stability, “Made in America” preference, supply chain diversification and federal incentives such as the Infrastructure and Inflation Reduction Acts. This trend is expected to continue. Leading countries that will comprise the source of FDI will be those with a sizeable aerospace industries including the UK, Germany, Canada and Spain.
Nearshoring is another trend that has taken hold. Both U.S. aerospace companies and those seeking to expand in North America often consider Mexico as an alternative. Mexico does have an established base of aerospace operations. Among the pluses of locating in Mexico are:
1. Established aerospace ecosystem
2. Proximity to the U.S.
3. Tariff-free exporting to the U.S.
4. Comparatively low labor costs
However, there are challenges to locating in Mexico. These include:
1. Finding and building relationships with suppliers
2. Navigating a complex regulatory environment including labor regulations
3. Longer delivery time to customers compared to U.S. operations
4. Rising labor costs
5. Emerging labor shortages, especially among skilled and semi-skilled workers
6. In certain locations, electric power reliability can be an issue
7. Electric power costs are higher than in much of the U.S.
8. Absence of a “Made in America” label
On balance, WDGC does see Mexico as a viable option for selected aerospace operations. At the top of the list would be manufacturing plants where direct labor constitutes an above-average proportion of the cost of goods sold.
Choosing the Best Location
Strategic Framework. Once executive management determines that a new facility will be required, underlying strategic dynamics need to be articulated. These parameters will establish the analytical framework for identifying and choosing a location that will maximize the success potential of the new operation. Among the strategy-related considerations that might influence location selection are:
1. Competitive landscape for the business
2. Composition and rate of growth
3. Geographic focus for the new entity (e.g., all the U.S., a portion of the U.S., Mexico, Europe or Asia)
4. Existing footprint capacity (physical and HR)
5. Whether existing sites will be included in the analysis
6. Due to constraints at existing locations, identifying whether there will there be any relocation of manufacturing capacity
7. Identification of factors that will provide a competitive advantage
8. The importance of proximity to companies in the current supply chain
9. Identifying whether new suppliers will be required, especially if the project involves reshoring
10. The location of new suppliers
11. The operational date of the new facility
12. The identification of three overarching/paramount location selection considerations
The next step is to assemble the internal project team. Thereafter, the team leader and perhaps the day-to-day manager, need to reach out to external service providers. Once brought on board, a multi-phase analytical process is typically followed.
Phase One: Requirements/Criteria
The first order of business is to delineate the initial and future operating requirements of new operations. Given systemic labor shortages, it is especially important to quantify projected headcount by both position and requisite experience. HR assumptions play a significant role in selecting a location that will readily support staffing requirements. For example, a greater proportion of new hires requiring direct experience will tend to gravitate the project toward established hubs for the industry. However, these areas might display more heated labor market competition and higher costs.
Another dynamic that should be accorded heightened attention is the mandate for “green energy.” This issue is, of course, important for most companies, however, given both electric power supply shortages and transmission congestion, many locations will need to walk back green goals at least over the mid-term. These conditions could impact the company’s ability to attain green energy goals.
When defining operating needs for an aerospace location selection, it’s important to consider headcount, site/building and utility requirements, and proximity to suppliers and customers. Once baseline information is assembled, the geographic search region must be defined. This area might include a multi-state territory or the entire U.S.
Now the team needs to define and assign weights to location criteria. It is helpful to delineate broad categories (e.g., utilities) and assign specific factors (e.g., electric power) to each category. Furthermore, consider dividing criteria into cost (e.g., labor) and qualitative (e.g., labor supply) sections. A scorecard template can be utilized to populate and weight location criteria.
Phase Two: Location Screening
Objective. The principal objective in this phase is to reduce the initial field of location candidates to a manageable number. A two-stage exercise is typically followed.
Stage One is a winnowing process whereby areas are eliminated or accepted by applying statistical thresholds (e.g., population size). This stage encompasses desktop research that generates a long list (often six to 10) of qualified locations.
Stage Two embraces a confidential Request for Information (RFI) issued to the lead economic development organization. RFI results are combined with desktop research to rank/score long-listed locations which culminates in a shortlist (usually two to four) of finalist locations.
Stage One: Desktop Research. The process for most projects involves applying statistical criteria in a multi-round analysis. In each round, a statistical threshold is established. Areas failing to meet the threshold are rejected while those passing the test are carried forward to the next round. Stage One is metric-driven. Illustrative location screening criteria for a prototypical aerospace parts/components project are illustrated below. Note that criteria weights and thresholds would be somewhat different for other industry segments such as aircraft assembly or MRO.
1. Demographic characteristics (e.g., population size/growth, educational attainment, labor force)
2. Industry employment most applicable to aerospace
3. Occupational employment most applicable to aerospace
4. Presence of four- and two-year colleges with aerospace-related programs
5. Indirect labor cost indicators such as household income, cost of living and housing costs
6. Median wages by occupation
7. Air service
8. Transportation resources
9. Tax rates/practices
10. Natural disaster risk
11. State business climate ranking
Stage Two (RFI). Before the issuance of a confidential Request for Information (RFI) to the leading economic development organization in each area, the first step is to search for available buildings and/or sites that meet fundamental criteria. Longlisted areas deficient in available sites and/or buildings should be dropped from further consideration. The remaining areas will now be further assessed based upon the RFI, which is intended to generate intel that is generally not available via desktop research. Emblematic intel gleaned from an RFI is outlined below.
1. Roster of major employers, e.g., aerospace-related, advanced manufacturing, R&D centers/innovation hubs
2. New and expanding employers
3. Downsizing industrial employers
4. Highlights of pertinent education/training programs
5. Aerospace and manufacturing career awareness (especially for high school and middle school students)
6. Profiles of suitable sites/buildings already identified
7. Electric power supply, reliability, cost
8. Green energy availability
9. Planned improvements to infrastructure (e.g., electric power, other utilities, transportation)
10. Property and sales tax exemptions
11. Potential incentive programs, benefits and eligibility
Shortlist Selection
Desktop research and RFI results are amalgamated, and each long-listed area is then ranked/scored. The team then earmarks several locations for Phase Three empirical research. Frequently, two to four locations are awarded shortlist status.
Phase Three: Location Evaluation
The Thrust. Phase three embodies firsthand research in finalist or shortlisted areas to contrast each area and reach team concurrence on the best long-term location. The latter includes a metro area or county, a sub-labor market and a specific building and/or site. The major focal points of the empirical research, which includes both virtual and field-based evaluation, involve the labor market, site/building and infrastructure.
When engaging in firsthand location evaluation, results from the following tasks will enable the team to determine the viability of targeted locations:
1. Interviews with comparable employers on recent/current operating experiences, and labor market conditions (e.g., competitive demand, labor availability/quality, market competitive compensation and benefits, turnover and keys to achieving preferred employer status)
2. Interviews with other pertinent constituents
• Staffing agency
• Workforce development board
• Education/training officials
• Utility representatives
• Regulatory approval/compliance
• Transportation
3. Site/building tours/discussions
4. Review of detailed site/utility characteristics
5. Dialogue with local and state economic development agencies, including:
• Area fit for the project in question
• Rate and composition of growth by industry
• Funded and planned infrastructure improvements
• Getting into business assistance
• Permit expediting/coordination
• Penultimate incentives offer
Summarize field evaluation findings for each location criterion using a scorecard ranking. The team manager should then prepare a summary presentation of Phase Three, including the scorecard and other supporting data/graphical displays. After review, team members should convene to discuss the results and reach a consensus on the preferred location and best alternative. Additionally, a task completion plan for the next phase, involving real estate acquisition and negotiations for incentives, should be developed.
Conclusion
The aerospace industry has entered a period of healthy growth in both the commercial and military sectors.
However, headwinds such as geo-political risk, complex supply chains, reliance on few suppliers for critical materials, government regulation and a talent shortage could imperil growth. Companies are addressing these challenges with innovative strategies. The industry is expected to witness strong expansion in the U.S., an uptick in foreign direct investment, and more friendshoring and nearshoring (including Mexico).
Choosing a new aerospace facility location should follow a structured process to identify the most viable long-term solution. Of utmost importance are proximity to suppliers (existing and new), proximity to customers, talent pool breadth/depth, fully serviced industrial sites or available buildings, electric power infrastructure and business operating costs. Incentives, while desirable, should be viewed in the context of enhancing a compelling location for the manufacturing plant. T&ID