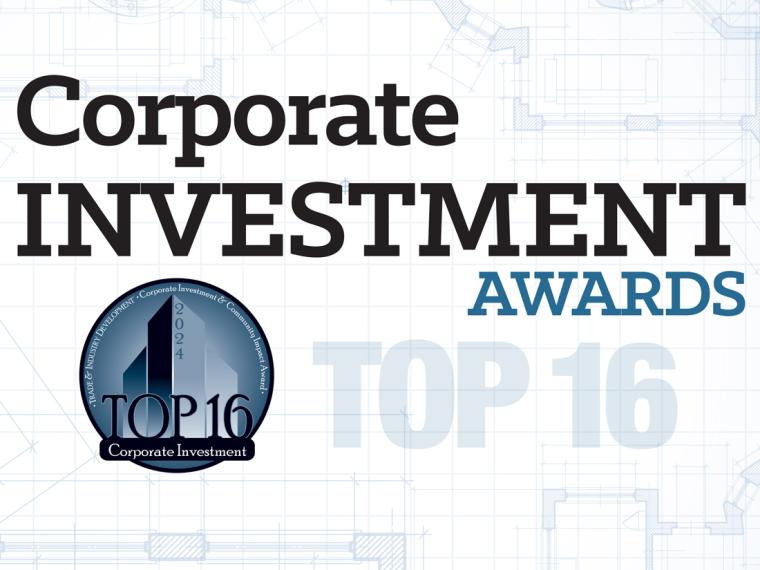
The automotive industry has been a strength for the U.S. economy for more than a century. This year, automotive manufacturing is a particularly strong theme of Trade & Industry Development’s 2024 CiCi Awards for the Corporate Investment category.
Manufacturing companies making both traditional automobiles and auto parts as well as those creating alternative vehicles and fuels chose sites across the U.S. for large capital investment projects, both new and expansions of existing facilities. Trade & Industry Development put out a call for regions to highlight the largest investment projects they won in the calendar year 2023. We chose 16 of those projects as winners of our 2024 CiCi Awards for the Corporate Investment category.
Collectively, these 16 projects bring more than $32.6 billion in private corporate investment. The benefits go well beyond the capital involved, however; these projects are creating or retaining a total of 30,702 jobs.
None of these projects, of course, would have been possible without the hard work of community leaders, local and state economic developers, along with the visionaries at the companies themselves.
Trade & Industry Development offers congratulations to all the winning projects, and we look forward to watching them unfold.
Toyota
Randolph County, North Carolina
North Carolina has had a partnership with Toyota for many years, but the relationship continues to expand. In 2023, the Japanese automaker announced plans to invest an additional $8 billion in its electric battery manufacturing site in Randolph County, North Carolina, a move that will lead to the new hiring of approximately 3,000 employees. Toyota’s total investment in the Randolph County site will now total $13.9 billion and more than 5,000 jobs, making it the largest economic development announcement in North Carolina’s history.
Toyota announced the first phases of the Liberty project in 2021 with $1.29 billion in investment and 1,750 new jobs. As the market shift to electric vehicles has accelerated, Toyota has increased its investment in North Carolina. According to Toyota, this expansion will increase capacity for electric vehicle battery production and add new capacity to also produce batteries for plug-in hybrid vehicles. The project will add eight production lines to the two lines previously announced.
Toyota’s arrival in North Carolina will be facilitated, in part, by a transformative Job Development Investment Grant (JDIG). The project is estimated to grow the state’s economy by at least $9.5 billion over 20 years. Like all grants from the JDIG program, state payments occur following performance verification each year by the departments of Commerce and Revenue that the company has met its incremental job creation and investment targets.
The project further highlights North Carolina’s readiness to support such a large project and its leadership in the clean energy economy. The expansion is expected to attract co-located businesses to support it, such as companies operating in the EV supply chain. The Economic Development Partnership of North Carolina (EDPNC) was joined by the North Carolina General Assembly, Greensboro Chamber of Commerce, Piedmont Triad Partnership, North Carolina Railroad Company and Greensboro-Randolph Megasite Foundation to attract the project.
“Today’s announcement is yet another validation of North Carolina’s national recognition as a hub for innovation, and a top location for electric vehicle manufacturers and suppliers,” said Christopher Chung, CEO at EDPNC. “Japanese investment has a significant impact in our state, with more than 28,000 North Carolinians going to work for Japanese companies every day. We value and appreciate the ongoing partnership our state has with Japan and the economic impact this partnership will continue to have.”
General Motors
Saint Joseph County, Indiana
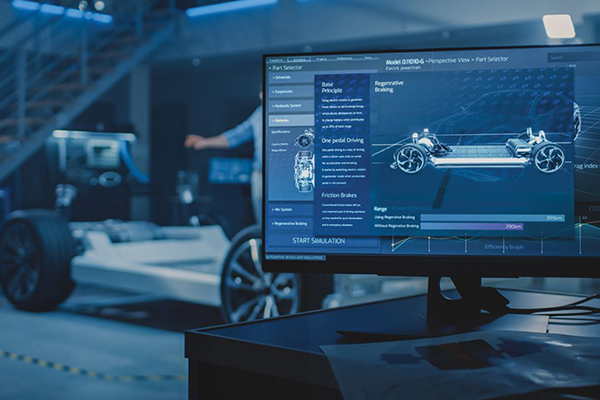
GM has a considerable presence in Indiana with five facilities across the state that employ more than 5,700 Hoosiers. Now, a new project will add to that total. In April of 2023, GM and Korea-based Samsung SDI jointly announced plans to build a new plant just east of New Carlisle at Larrison Boulevard and Indiana 2 to supply GM’s growing EV production needs. GM plans to install more than one million units of annual EV capacity in North America in 2025 and accelerate from there. The project will see an investment of $4.4 billion in the region, with the creation of approximately 1,750 jobs.
The new facility, which is scheduled to begin operating in 2026, will house production lines to build nickel-rich prismatic and cylindrical cells and is expected to help significantly increase the accessibility and affordability of EVs. Once complete, the plant will have more than 30 gigawatt hours (GWh) of capacity.
The Indiana Economic Development Corporation worked with GM and Samsung SDI to finalize a performance-based incentive offer to support the joint venture’s investment and job creation plans. St. Joseph County, Indiana Michigan Power and Northern Indiana Public Service Company offered additional incentives. The state offered a variety of incentives to attract the project, including a $135 million Cash Performance Grants, a $3 million Infrastructure Grant, $32 million in Economic Development for a Growing Economy tax credits, a $3.45 million SEF Training Grant and $8.84 million in DWD Workforce In-Kind Services.
“St. Joseph County is deeply appreciative that General Motors and Samsung SDI have selected our community for its EV battery plant,” said Carl Baxmeyer, President of the St. Joseph County Board of Commissioners. “This project represents the largest single investment and job commitment in St. Joseph County in the last 75 years and will impact our region for decades. Our region has a long history of innovation in the automotive industry, and for generations has built vehicles or parts that have been included in vehicles around the world. As the industry evolves, we’re thrilled to once again be at the center of this transformational time for the industry.”
Tesla
Storey County, Nevada
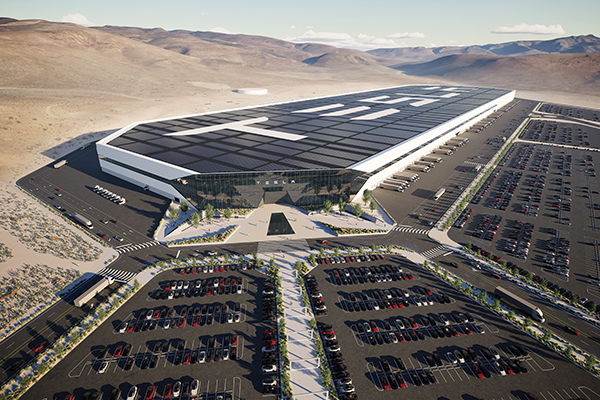
Electric vehicle company Tesla already has an enormous presence in Nevada, going back to 2014, when the company made a commitment to invest $3.5 billion to build a facility capable of producing 35 GWh of battery cells annually — enough to manufacture about 500,000 vehicles per year. This level of battery manufacturing was unprecedented for a single facility at the time, with the expected output being greater than all global battery production in 2013 combined.
Since 2014, Tesla has invested $6.2 billion in Nevada and built a 5.4 million square foot Gigafactory providing 17,000 local construction jobs. Last year, the company announced plans to invest over $3.6 billion more to continue growing Gigafactory Nevada, adding 3,000 new team members and an electric semi-truck and battery manufacturing facility: a 100 GWh 4680 cell factory (with the capacity to produce enough batteries for 1.5 million light duty vehicles annually), as well as the first high-volume Tesla Semi factory. The Tesla Semi is a fully electric combination truck, with 500 miles of range and energy consumption of less than 2 KWh per mile.
To help attract the new project, The Nevada Governor’s Office of Economic Development (GOED) Board approved a $330 million abatement for Tesla. The new facility is expected to contribute to immense economic growth in the state. With a capital investment of $3.6 billion in land, buildings and equipment, the company could generate an estimated $21.8 million in gross average annual property tax revenues, $11.2 million in gross average annual sales taxes, $1.1 million in average annual business license taxes on utilities and $2.1 million in gross average annual modified business taxes over 20 years. All totaled, this will result in an estimated $685 million in net state and local revenues over the next 20 years.
In addition to the 3,000 direct jobs the new project will create, it’s also expected to create an estimated 9,275 construction jobs and 5,858 additional indirect and induced jobs through 2027.
“Since the inception of GOED, the main goal has been to diversify Nevada’s economy,” said Tom Burns, GOED Executive Director. “The Nevada-Tesla partnership cemented a new economic sector in Nevada for the manufacturing of electric vehicle battery packs and drive units, and energy storage products. Tesla’s Gigafactory propelled Nevada’s manufacturing industry, establishing lithium-ion batteries as the state’s eighth largest export both nationally and internationally.”
Starplus Energy LLC
Howard County, Indiana
In October 2023, Stellantis and Samsung SDI (collectively known as Starplus Energy, LLC) announced a significant expansion of Starplus’ EV battery manufacturing operations in Indiana with an additional investment of more than $3.2 billion. The facility will be the joint venture’s second StarPlus Energy gigafactory in Kokomo. To support the growth, the companies plan to create 1,400 new, high-wage jobs in north central Indiana, growing its total planned workforce to 2,800 jobs.
The expansion will grow the joint venture’s total investment to more than $6.3 billion. The second next-generation EV manufacturing facility will be built adjacent to the first gigafactory in Kokomo first announced in May 2022, which is currently under construction and targeted to launch in the first quarter of 2025 with an annual production of 33 gigawatt hours (GWh). This second battery manufacturing facility will start production in early 2027 and aims to have an initial annual production of 34 GWh, significantly increasing U.S. capacity and accelerating Stellantis’ transition to EVs.
The investment represents the sixth battery facility to support Stellantis’ electrification plan outlined in its Dare Forward 2030 initiative, the company’s long-term electrification strategy to invest $35 billion through 2025 in electrification and software globally. Stellantis plans to reach a 100 percent passenger car battery electric vehicle (BEV) sales mix in Europe and 50 percent passenger car and light-duty truck BEV sales mix in the U.S. by 2030. To achieve these targets, the company is securing approximately 400 GWh of battery capacity. Stellantis is on track to become a carbon net zero corporation by 2038, all scopes included, with single-digit percentage compensation of remaining emissions.
The Indiana Economic Development Corporation (IEDC) Board of Directors has committed to an investment in StarPlus Energy of up to $37.5 million in the form of conditional tax credits and up to $2 million in conditional training grants based on the project’s investment and job creation plans. The IEDC also committed an investment of up to $22 million in conditional redevelopment tax credits and up to $115 million in conditional structured performance payments. These incentives are performance-based, meaning the company is eligible to claim state benefits once investments are made and employees are hired and trained.
“Indiana’s economy is on a roll,” said Indiana Governor Eric Holcomb. “[The] commitment from Stellantis and Samsung SDI will double the capital investment, the new jobs created and the impact this joint venture will have on Kokomo and the State of Indiana for decades to come. This decision puts Hoosiers squarely at the center of innovating and developing the future of mobility, catalyzing Indiana’s leadership position in tomorrow’s global economy.”
Scout Motors
Richland County, South Carolina
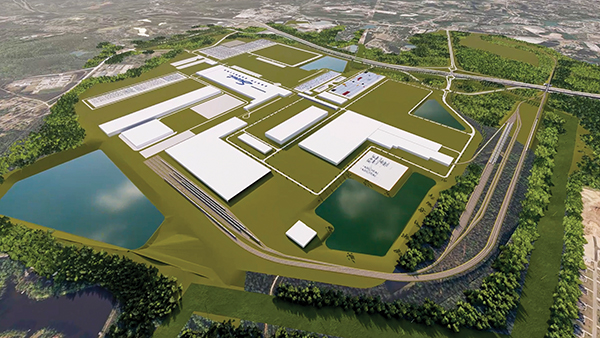
In March of 2023, the South Carolina Department of Commerce announced that Scout Motors Inc. plans to establish its first manufacturing plant in Blythewood, near Columbia, South Carolina. At the Richland County site, the company will build all-electric, next-generation trucks and rugged SUVs harkening back to the iconic Scout vehicles produced from 1960 to 1980. The company’s $2 billion investment has the potential to create 4,000 or more permanent jobs.
The Blythewood Industrial Site off Interstate 77 spans approximately 1,600 acres, with the plant itself occupying 1,100 acres. Vehicle production is targeted to begin by the end of 2026.
Tysons, Virginia-based Scout Motors is an independent U.S. company backed by Volkswagen Group with an experienced Board of Directors, including Dr. Gernot Doellner, Head of Group Strategy at Volkswagen AG, and Peter Bosch, Member of the Bentley Motors Board for Manufacturing. Scout is currently evaluating the potential for outside investment.
The company’s trucks and SUVs will be built on a newly designed all-electric platform. With internal engineering focused on attributes including ground clearance, approach angles, robust axles, payload capacity, all-electric range and new digital features, Scout products will honor its heritage while injecting fresh American ingenuity to create a new era of iconic all-purpose vehicles, said the company.
The South Carolina General Assembly has appropriated $1.29 million in addition to the project’s capital investment, and the company was also approved for job development credits.
“Richland County has spent years laying the groundwork for today’s historic announcement, and we are thrilled that Scout shares our view that this area is the ideal location for a world-class company to plant its flag,” said Richland County Economic Development Office Director Jeff Ruble. “With our supportive business development network, vibrant workforce, culture of innovation and connectivity to key strategic hubs, Richland County has created a strong economic foundation that Scout would be able to build upon in the years to come.”
Gotion Inc.
Kankakee County, Illinois
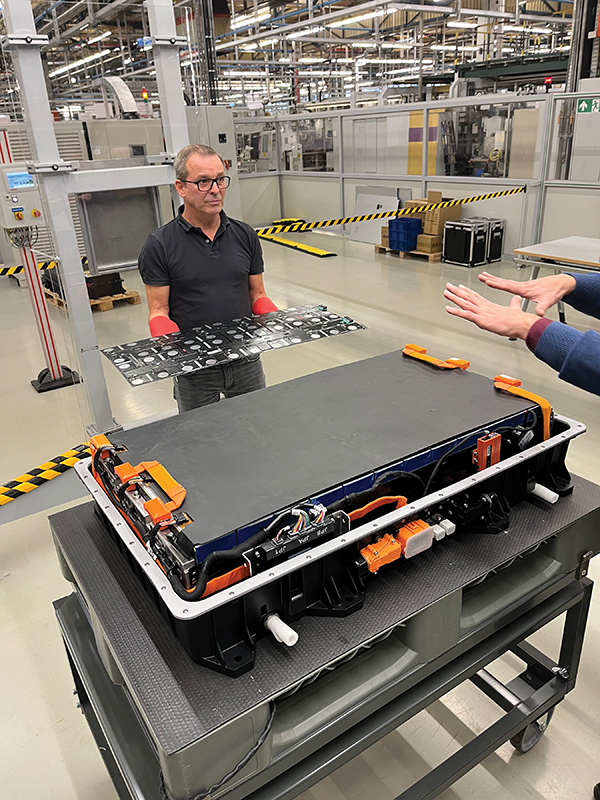
Gotion Inc., a subsidiary of Gotion Hi-Tech headquartered in Hefei, China, is a manufacturer of energy storage systems and EV batteries. The parent company has facilities all over the world, including Germany, Japan, Singapore and China. Since 2014, Gotion Inc. has been headquartered in Fremont, California, and operates an R&D facility in Ohio. The company is also in the process of building a raw materials plant in Michigan.
In September of 2023, Gotion announced its choice of a site in Manteno, Illinois for a $2 billion investment in a lithium-ion battery manufacturing plant that will employ approximately 2,600 individuals.
During the site selection process in late 2022, Gotion came across the nearly vacant and underutilized former Kmart warehouse in Manteno after exhausting several other site searches. Kmart closed the Manteno site in 2019 and only a small portion of the building was being used for warehousing by the owner. Upon seeing the warehouse, Gotion’s broker initiated meetings with the Economic Alliance of Kankakee County, the Village of Manteno, police and fire personnel, the Kankakee County workforce organization, the local community college and the pertinent utilities including ComEd, Nicor Gas and AQUA Illinois.
The plant, situated on 153 acres, encompasses more than 1.5 million square feet of manufacturing space. Gotion is now in the process of construction work on the interior of the building, with work on equipment and manufacturing lines expected to be completed in the first quarter of this year. The first energy storage system battery packs and EV batteries will roll off the line in less than a year, said the company. The batteries produced at Gotion’s Manteno site will be used by Rivian (located in Normal, Illinois) and Lion Electric (located in Joliet, Illinois). Hourly pay is expected to exceed 120 percent of local rates in heavy industry jobs, amounting to over $55,000 per year.
Gotion’s total incentive package from the State of Illinois is valued at $536 million. This includes reimbursement from REV Illinois, the State of Illinois’ Reimagining Energy and Vehicles tax incentive. Through REV, Gotion is eligible to receive tax benefits totaling $213 million over 30 years. The REV agreement specifies a minimum company investment of $1.9 billion and the creation of 2,600 full-time jobs that are paid at least 120 percent of the average wage of similar jobs in Kankakee County.
As part of Illinois’ commitment to build out comprehensive EV hubs and support Illinois’ workforce, the state will also fund a new manufacturing training academy, as well as award an additional grant to workforce providers to expand training and prepare regional employees for the new jobs.
Gotion will also be the first recipient of Invest in Illinois funding in the amount of $125 million in capital funding. At the local level, Gotion was offered a 30-year tax cap on property taxes. This agreement, approved by nine taxing districts in the jurisdiction, freezes the company’s property tax once it reaches $2 million. The current property taxes on the site are at just over $900,000. This deal more than doubles the taxes paid to the local taxing districts.
“We are excited to have this company consider Kankakee County and bring these opportunities to our residents,” said Village of Manteno Mayor Timothy Nugent. “These will be good paying jobs and an anticipated tax revenue double what the site currently produces.”
ENTEK Lithium Separators LLC
Vigo County, Indiana
ENTEK, the only U.S.-owned and U.S.-based producer of “wet-process” lithium-ion battery separator materials, announced plans in March 2023 to establish operations in Indiana, investing $1.5 billion in a new Terre Haute production facility. The project, which marks the company’s largest investment to date, is expected to create up to 642 new, high-wage jobs by the end of 2027 and support the growing EV industry in Indiana and across the United States.
ENTEK, a global company headquartered in Lebanon, Oregon, will establish operations on a 350-acre greenfield site in the Vigo County Industrial Park II in Terre Haute. The company plans to initially construct four buildings covering 1.4 million square feet, with equipment built at current ENTEK manufacturing facilities in Oregon and Nevada and specialty biaxial stretching equipment supplied by Brueckner Group USA, to manufacture battery separators for lithium-ion battery manufacturers across the U.S.
The campus, which will be fueled in part by a $200 million grant from the U.S. Department of Energy (DOE) as part of the recent Bipartisan Infrastructure Law, will enable ENTEK to scale its U.S. production to be capable of supplying approximately 1.4 to 1.6 million EVs annually by 2027. The new giga-scale lithium-ion battery separator operations will leverage ENTEK’s sustainable, state-of-the-art solvent extraction and recovery systems and processing techniques, and the company will use available renewable energy with a focus on a reduced carbon footprint. The company plans to break ground on the campus as soon as engineering and permitting is completed and launch its Indiana operations between 2025 and 2027.
The project is the first phase of ENTEK’s planned expansion to produce about 1.4 billion square meters of ceramic coated lithium separators across its operations. Phase 2 of the project will add up to an additional 1.8 billion square meters of battery separator produced annually for a total of 3.2 billion square meters, which will provide enough separators for about 3.5 million electric vehicles.
State-level incentives from the IEDC totaled approximately $13.5 million, and included cash performance grants, job training grants, innovation vouchers and a manufacturing readiness grant. In addition, local authorities provided land grants and property tax abatements that totaled $150 million.
“It has been an incredible honor to work with Larry Keith, Kim Medford and the ENTEK team on this extraordinary opportunity for our community,” said Steve Witt, President of the Terre Haute Economic Development Corporation. “At the local level, we will do our utmost to help make ENTEK’s fabulous new project a success.”
Plant Agricultural Systems
Potter and Lubbock Counties, Texas
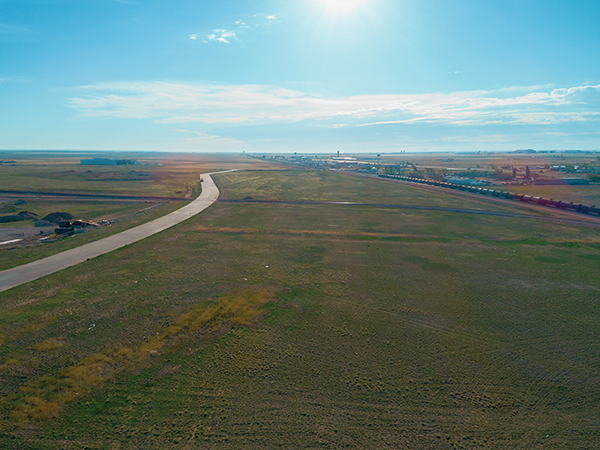
Supporting the availability of fresh produce worldwide is increasingly a matter of technology. Plant Agricultural Systems, a Florida-based infrastructure service provider that delivers both the physical and digital infrastructure necessary to support localized fresh produce demand, has a goal of dynamically enabling society’s transition to more sustainable methods of food production, distribution and consumption. To further this goal, the company is expanding in West Texas, a region chosen because of its importance in supplying much of the nation’s food.
PLANT-AS will expand with two plants, one in Lubbock and another in Amarillo. The company will develop over 1,100 acres of advanced Controlled Environment Agriculture (CEA) production in West Texas as a part of its phase one domestic operations roll out. The total investment of $1.18 billion is comprised of a $670 million investment in Lubbock and a $510 million investment in Amarillo. It will create approximately 1,600 new jobs (700 in Amarillo and 900 in Lubbock).
The Amarillo City Council approved a Location Incentives Agreement totaling $3.75 million for PLANT-AS in March of 2023. Three months later, at the end of June 2023, the AEDC announced a Public Private Partnership with the company. PLANT-AS’ Amarillo project includes the development of nine million square feet of advanced CEA production facilities on 400 acres at the Centerpoint East site. Fresh produce, including leafy greens and vine crops such as tomatoes, will be produced using state-of-the-art hydroponic technology. Incentives in the Lubbock area will include $6.9 million in land value as well as infrastructure improvements.
The modernization of the region’s strong agriculture industry with new technology exhibits strong parallels to the monumental partnership between Lubbock and Amarillo in bringing ground-breaking technology to the region. Likewise, as the technology sector continues to develop in the region, the advanced production facilities of PLANT-AS serve as modern data centers where production technicians will be supported by artificial intelligence to process crop-cycle data.
“We are excited about the decision by PLANT-AS to locate in Amarillo and Lubbock,” said Kevin Carter, President and CEO of Amarillo Economic Development Corporation. “The West Texas region plays a significant role in providing food for the nation, and I believe it was extremely important for our communities to work together on this project. Congratulations to Lubbock and Amarillo on what I see as a huge win for our area.”
QTS Data Centers
York County, South Carolina
As the digital economy expands, so too must the critical data centers that support the digital realm. In September 2023, QTS Data Centers, a provider of colocation data center infrastructure and related services, announced plans to establish operations in York County, South Carolina. The $1 billion investment is the company’s first South Carolina facility and will help establish a technology hub in York County. The number of jobs the project will create has yet to be determined.
The QTS campus, located near Hands Mill Highway and Campbell Road in unincorporated York County, will use carbon-free power when feasible and leverage water-saving technology for cooling. QTS’s $1 billion investment in the data center campus represents a substantial boost to the state’s economy, creating jobs, attracting other businesses and bolstering infrastructure development. Though the state is unable to predict specific job numbers, the project is expected to generate hundreds of new, high-paying jobs in construction, engineering, IT and other sectors, expanding employment opportunities in the region.
Increased employment and business activity will generate tax revenue for the state and local governments, enabling them to invest in public services, education and infrastructure. The new data center will support the growing reliance on cloud computing, data storage and internet connectivity, attracting tech companies and businesses requiring robust data solutions.
QTS has the potential to partner with educational institutions to develop a skilled workforce for the growing data center industry, creating new training and learning opportunities for South Carolinians. QTS has a history of supporting local communities through philanthropic initiatives and partnerships, which could extend to York County and surrounding areas. Increased tax revenue from the project is expected to benefit public schools in York County, improving educational resources and opportunities for local students.
The Coordinating Council for Economic Development awarded a $200,000 set-aside grant to York County to assist with the costs of site preparation.
“QTS Data Centers’ $1 billion investment in York County reflects our community’s commitment to a brighter future,” said York County Council Chairwoman Christi Cox. “Their presence here will significantly boost public school funding and broaden our tax base. We extend thanks to our local utility partners for their invaluable support in making this vision a reality.”
Graphic Packaging International, LLC
McLennan County, Texas
In February of 2023, Atlanta-based Graphic Packaging International announced plans to spend $1 billion in a three-year window on a high-tech paperboard recycling mill in Waco, marking a record investment for economic development for the area. The site will be a 640,000-square-foot facility in Texas Central Park. The mill will turn corrugated box cardboard into thinner paperboard packaging for cereal boxes and other consumer products.
Production is expected to begin in 2026.
The Waco mill, which is being designed to facilitate the recycling of 100 percent of the paperboard side rolls and waste produced by the company, will improve the company’s overall environmental impact. It will allow a variety of recyclable materials to be effectively cleaned and separated, enhancing the circular economy benefits of recycled paperboard and leading to a potential decrease in overall greenhouse gas emissions. The mill will incorporate smart technologies, such as using a gas turbine to generate electricity and produce steam for paperboard drying, improving the overall efficiency and reliability.
The project, which was brought to the region with efforts by the City of Waco, McLennan County, Waco Industrial Foundation and the Greater Waco Chamber Economic Development, marks a major milestone as Waco’s first billion-dollar investment in the community. It will bring 230 new jobs with an average annual salary of $65,000 which is almost $10,000 more than McLennan county’s 2022 average yearly wage, according to the Texas Quarterly Census of Employment and Wages.
“I am thrilled that Waco will have its first billion-dollar investment in the community,” said Waco Mayor Dillon Meek. “I’m thankful for the Graphic Packaging leadership team, who saw first-hand how our community comes together for the greater good, including workforce development and long-range infrastructure plans. Our community’s commitment to collaboration between local government, businesses, and education greatly benefits large and small businesses. Thank you to all the parties who diligently worked to achieve this important milestone. Welcome to Waco, Graphic Packaging.”
Canadian Solar US Cell Manufacturing Corp.
Clark County, Indiana
When it came time to choose a site for its second solar photovoltaic (PC) cell production facility in the United States, Canadian Solar looked to Indiana. In October of last year, the company announced plans for a new facility in Jeffersonville. The new plant is expected to create approximately 1,200 new jobs over the next several years.
Canadian Solar, a provider of solar power products, services and system solutions, will invest a projected $800 million to construct and equip a state-of-the-art PV cell manufacturing plant at the River Ridge Commerce Center. The new plant will produce an annual output of 5GW – equivalent to approximately 20,000 high-power solar panels per day – and ship the finished cells to the company’s new module assembly facility in Texas, announced earlier this year. Production is expected to begin by the end of 2025.
Canadian Solar plans to begin hiring for new positions in mid-2024 and will ramp up hiring in early 2025 to fully staff the Jeffersonville plant. This facility joins the company’s global manufacturing facilities in Canada, China, Brazil, Vietnam and Thailand.
Based on the company’s job creation plans, the Indiana Economic Development Corporation committed an investment in Canadian Solar of up to $9.7 million in the form of conditional tax credits and up to $400,000 in conditional training grants. The IEDC also committed an investment of up to $2 million in conditional redevelopment tax credits based on the company’s investment plans and up to $200,000 in Manufacturing Readiness Grants. These incentives are performance-based, meaning the company is eligible to claim state benefits once investments are made and employees are hired and trained. The City of Jeffersonville and the River Ridge Development Authority offered additional incentives.
“The City of Jeffersonville is pleased that Canadian Solar has chosen River Ridge Commerce Center as home for their newest critical production facility in the United States,” said Jeffersonville Mayor Mike Moore. “Not only are they making a large financial investment into our community, but they will also become one of the largest single-site employers in the Greater Louisville region. When in full production, their total employment base will include over 150 engineers at this facility. We are thrilled to see a global industry leader join our community and provide a product with enormous potential.”
Koura
Iberville Parish, Louisiana
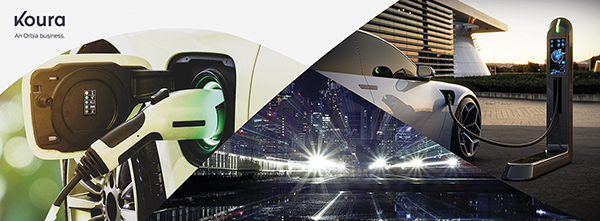
In October, Orbia’s Fluorinated Solutions’ subsidiary Koura announced two expansion projects at the company’s Iberville Parish, Louisiana facility that will support the nation’s lithium-ion battery production supply chain, enabling domestic production of 1.7 million electric vehicles annually.
The first proposed project is the construction of a $400 million manufacturing facility that will produce LiPF6, a component that allows for the flow of electricity through lithium-ion batteries. This facility will be the first of its kind in the U.S. and Koura estimates it will produce 10,000 metric tons of LiPF6 per year.
The company also proposed an additional $400 million investment to build a second new production plant that will manufacture 40,000 metric tons of a primary building block in polyvinylidene fluoride (PVDF) manufacturing which serves as a critical binding agent for lithium-ion battery production.
Koura expects to create 100 direct new jobs across the two projects with an average annual salary of $80,000, while retaining 80 current positions. It also anticipates the creation of more than 2,000 construction jobs at peak construction of both facilities. Louisiana Economic Development estimates the projects would result in a combined 283 indirect new jobs for a total of 383 new jobs in the Capital Region.
Koura’s St. Gabriel facility has been in operation since 1991 and currently produces R-134a, a refrigerant. These new facilities will support the company as it aims to expand domestic manufacturing of EV and electrical grid batteries and shift production of their materials and components to the U.S.
The company expects construction of both new facilities to begin in 2025 2025, with operations beginning in 2026.
“Koura’s proposal for building two new operating units at the company’s St. Gabriel facility located in Iberville Parish will certainly enhance the economy in Iberville Parish and the State of Louisiana for both job creation and capital investment,” said Iberville Parish President J. Mitchell Ourso Jr.
Meta
Dakota County, Minnesota
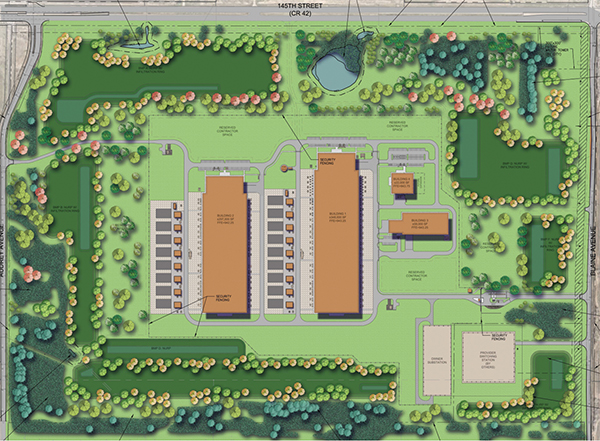
In early September, Meta Platforms Inc. – the parent company of Facebook — announced plans to build a $700 million data center in Rosemount, Minnesota. The project will be one of the largest construction projects in Minnesota’s recent history. Meta’s chosen site is 280 acres of UMore Park property along County Road 42 next to Dakota County Technical College. Ultimately, the facility will be powered with renewable energy. In October, state utility regulators approved electricity contracts for the $700 million project, which will create 50 full-time jobs and approximately 1,000 short-term construction jobs.
To date, Meta has 17 data centers operating or under construction in the U.S. Data centers contain thousands of computer servers that store and process reams of information. They usually run around the clock and use enormous amounts of power, making them prime customers for electric utilities.
According to Xcel Energy, several Minnesota entities are working on the Meta project, including Dakota County, Greater MSP and the Minnesota Department of Employment and Economic Development. The city of Rosemount already voted to rezone the land from agriculture to business park use, paving the way for the sale.
Rosemount Mayor Jeff Weisensel said the project as outlined would be “significant” for the city, as the land goes on the tax rolls, “key to the city’s future.”
“We’re looking forward to a firm that appreciates ... the emerging technology and innovation that we’re trying to attract,” said Weisensel.
Toyota Motor Manufacturing, Kentucky (TMMK)
Scott County, Kentucky
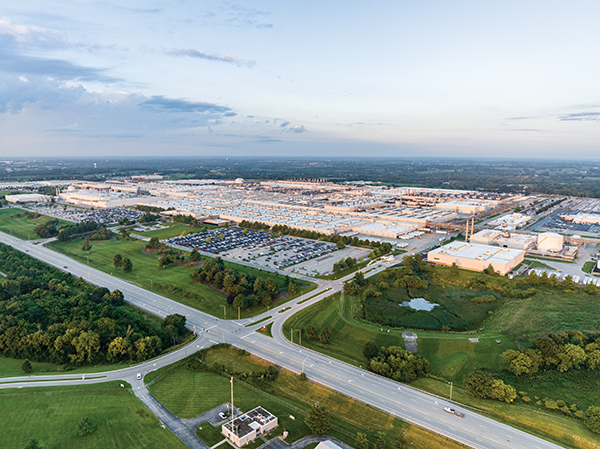
In May of 2023, The Commonwealth of Kentucky announced that Toyota has committed to retaining 700 full-time Kentucky jobs and establishing the company’s first U.S.-assembled battery electric vehicle (BEV) at Toyota Motor Manufacturing, Kentucky (TMMK) in Georgetown. The project is part of a $591 million commitment for future projects at the Scott County facility.
TMMK is Toyota’s largest manufacturing facility in the world and the project will lead the company’s vehicle carbon reduction efforts. TMMK also plays a central role in foreign-direct investment from Japanese-owned companies in Kentucky. Currently, nearly 200 Japanese-owned manufacturing, service and technology-related facilities are located throughout the Commonwealth, employing more than 45,000 people full time.
Toyota leadership confirmed plans to assemble an all-new, three-row SUV BEV at TMMK as the operation leads the company’s vehicle carbon reduction efforts. Through its ongoing incentive agreement with the state, the company has committed to the retention of nearly 9,000 employees at the Georgetown operation.
This project follows an October 2021 announcement of a $461 million investment to upgrade the Georgetown facility and prepare the site for future vehicle electrification. That announcement included the transition of 1,400 indirect employees to direct Toyota roles.
To encourage investment and job retention in the community, the Kentucky Economic Development Finance Authority (KEDFA) in May 2023 approved a supplemental project to an existing Kentucky Jobs Retention Act (KJRA) program agreement with the company. The performance-based agreement can provide up to $240 million in cumulative tax incentives based on the company’s total cumulative investment of nearly $2.8 billion across the original and supplemental KJRA projects with an annual job target requirement of up to 8,950 over the term of the agreement.
“There is nothing more exciting than to know that Toyota Motor Manufacturing, Kentucky continues to bring new products and technology to our community – the home of the largest Toyota plant in the world,” said Jack Conner, executive director of Scott County United Inc.
Cosma International of America, Inc./
Magna International
Haywood County, Tennessee
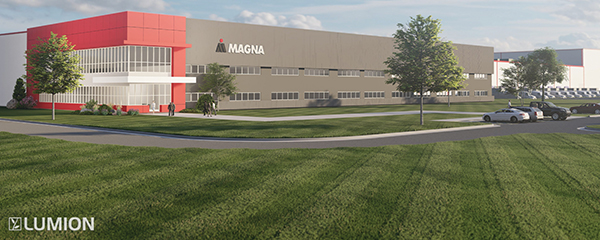
In July, Canadian auto supply company Magna International announced that its Cosma International subsidiary will open three plants in two Tennessee locations in 2025. The company will invest more than $790 million to build the first two supplier facilities at Ford’s BlueOval City supplier park in Stanton, Tennessee, and employ approximately 1,050 people (750 employees at a battery enclosures facility and 300 employees at a new seating plant).
Magna International Inc. is a mobility technology company that offers modular solutions for system and parts as well as full-vehicle assembly. The company sells its products to original equipment manufacturers of cars and light trucks, and operates manufacturing operations, product development, engineering and sales centers across Asian, European and North and South American regions.
In addition to the two West Tennessee locations, Magna will also build a stamping and assembly facility in Lawrenceburg, Tennessee. Combined, Magna will create approximately 1,300 new jobs in Tennessee.
Ford’s on-site supplier park will allow for vertical integration that helps ensure efficient production at BlueOval City, which will be capable of producing 500,000 electric trucks a year at full production. Magna will supply Ford’s BlueOval City with battery enclosures, truck frames and seats for the automaker’s second-generation electric truck. Magna’s two facilities at BlueOval City supplier park include a new 800,000-square-foot frame and battery enclosures facility and a 140,000-square-foot seating facility.
The battery enclosures facility will join one of Magna’s sister plants in Ontario, Canada, which is currently producing battery enclosures for the Ford F-150 Lightning. The seating facility will produce polyurethane foam and assemble and sequence “just-in-time” complete seats.
“We are proud that Magna is leading the way to grow Ford’s BlueOval City supplier park and boosting job creation with its commitment of nearly 1,300 new jobs in Tennessee,” said TNECD Commissioner Stuart C. McWhorter. “The $790 million investment from Magna will further shape the economic landscape of Lawrence and Haywood counties and strengthen the electric vehicle supply chain in Tennessee for years to come. Congratulations to all our partners who worked to bring these three projects to fruition.”
Albemarle Corporation
Chester County, South Carolina
The surging demand today for electric vehicles and other energy storage applications that use lithium-ion batteries has created significant opportunities for U.S. based producers. Albemarle Corporation, specializing in transforming essential resources such as lithium and bromine into critical ingredients for mobility, energy, connectivity and health, last year announced plans to establish South Carolina operations in Chester County. The company plans to invest at least $1.3 billion and create more than 300 new jobs to construct a new “Mega-Flex” lithium hydroxide processing facility.
Situated on nearly 800 acres near Richburg, Albemarle’s new “Mega-Flex” conversion facility will support EV and energy storage markets. The term “Mega-Flex” refers to the facility’s ability to process diverse lithium feedstock, including lithium, from recycled batteries. The new facility is expected to annually produce approximately 50,000 metric tons of battery-grade lithium hydroxide from multiple sources, with the potential to reach up to 100,000 metric tons.
The jobs that will be created by the facility will offer an average annual wage of $93,000, significantly boosting the local economy and providing career opportunities for South Carolinians. Additionally, over 1,500 construction jobs are projected during the building phase. The facility will play a crucial role in the expanding EV supply chain, positioning South Carolina as a hub for clean energy technology and attracting further investments in the sector.
In addition, the increased employment and business activity will generate significant tax revenue for the state and local governments, enabling them to invest in infrastructure, education and other public services. Albemarle has expressed commitment to partnering with local educational institutions to develop a skilled workforce for the lithium industry, creating new training and learning opportunities for South Carolinians.
The Coordinating Council for Economic Development approved job development credits related to the project. The council also awarded a $9 million Rural Infrastructure Fund (RIF) grant to Chester County to assist with the costs of mitigation, site preparation and infrastructure improvements.
“Albemarle is focused on meeting growing customer demand and this investment is part of our global commitment to transforming essential resources into critical ingredients that enable a more resilient world,” said Albemarle Corporation Chief Executive Officer Kent Masters. “We wanted a location with access to nearby rail and port transportation and the availability of skilled workers. We’re excited to have chosen South Carolina and to be closer to our customers as the supply chain is built out in North America.” T&ID
Related Agencies
- Economic Development Partnership of North Carolina
- Nevada Governor’s Office of Economic Development
- Richland County Economic Development
- Economic Alliance of Kankakee County
- Terre Haute Economic Development Corporation
- Lubbock Economic Development Alliance
- South Carolina Department of Commerce
- Waco Economic Development
- Louisiana Economic Development
- Kentucky Cabinet for Economic Development
- Texas Economic Development Corporation