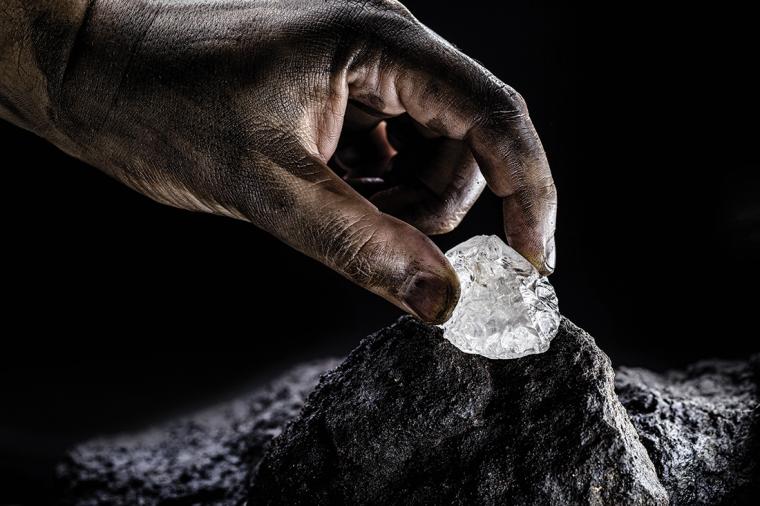
The modern world is on the cusp of an energy transition that will change the way we power our lives. Demand is growing for the commodities that play a critical role in the energy transition and the circular economy, such as lithium and nickel ores, renewable fuels and a new generation of recycled plastics. While there are still many hurdles to cross, itís clear that the race has begun.
Behind the scenes, supporting the energy transition is the supply chain. On one hand, the individual links in the energy transition supply chain must be custom forged to the new commodities’ needs. On the other hand, the underlying structures of these supply chains share common traits with their petroleum-based counterparts. Good supply chain design and management of the new materials, like their predecessors, require an ongoing focus on costs, resiliency and optionality.
Existing supply chains for commodities tend to have a sense of momentum. New supply chains by their very nature are disruptive. They represent a chance to design a system from the ground up, ideally, in a way that accurately anticipates the needs of the many firms and consumers that touch the commodity.
For transportation providers and for economic development officials, leveraging the freight and location assets at their disposal to anticipate shippers’ needs is a great strategy for attracting new business. For shippers and manufacturers who produce or use these new products, exploring the supply chain needs before making site and freight procurement decisions is a critical step that will impact competitiveness.
Supply Chain Challenges for Renewable Fuels
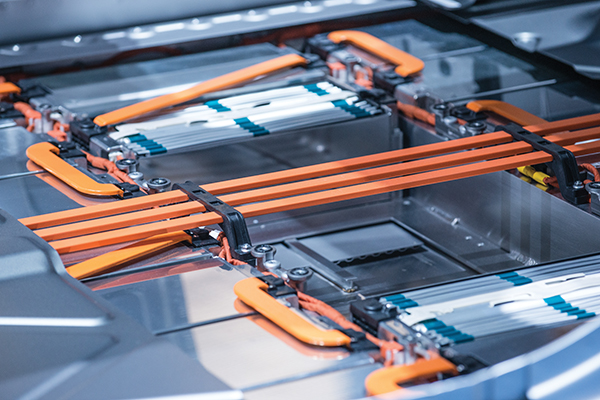
Supply chains for renewable fuels are at various stages of development. Some, such as renewable diesel, have fallen into established patterns. Others, such as green hydrogen and blue/green ammonia, represent more of a blank slate.
The challenge for renewable diesel (RD) and sustainable aviation fuel (SAF) hinges on some key differences around the feedstocks for these renewable fuels versus their petroleum-based predecessors. Typically, a conventional petroleum refinery obtains the lion’s share of its primary feedstock (crude oil) via pipeline, which is an inherently scalable way of moving bulk liquids. But the feedstocks for RD and SAF, such as tallow, vegetable and seed oils, and used cooking oil, are not moved via pipeline. Generally, RD and SAF refiners receive these products by rail.
Many RD refineries are converted from conventional refineries, which typically were not designed to receive feedstocks primarily by rail. On top of that, projecting the railcar fleet requirements, negotiating rates with railroads and establishing the systems to properly manage the rail supply chain are key to RD and SAF refiners’ success.
An additional challenge for RD is the fact that demand is concentrated in California, where there are additional incentives. While there is a significant amount of production located close to the consumption points on the West Coast, PLG Consulting’s market analysis confirms that the leading production area is the Gulf Coast. There isn’t currently a path to get refined fuels from the U.S. Gulf to California by pipeline. Again, rail has been tapped to fill the void, but this doubles down on the need for rail infrastructure, rail freight negotiation, railcars and supply chain management resources.
Green hydrogen is a fuel that is still in its early development without much of an established supply chain pattern yet. It is produced when an electrolyzer powered by renewable electricity separates water into its component elements, hydrogen and oxygen. As a gas, hydrogen can be used for remote or backup electricity generation. As a liquid, it can be used as a transportation fuel. About 70 percent of the cost of green hydrogen is tied to the production of renewable electricity. So, it will be produced in places that can efficiently produce wind, solar or hydroelectric power.
Handling hydrogen poses serious challenges, especially over long distances and when it needs to be stored for long periods. Hydrogen storage infrastructure is required at production and distribution/customer sites, and this infrastructure is still in its infancy. Truck transportation of hydrogen is hazardous and expensive.
Over long distances, it often makes sense to liquefy hydrogen, which requires cooling it to −423 degrees Fahrenheit (-252.7 degrees Celsius) and keeping it in an insulated tank. Liquified hydrogen allows for shipping in greater density, but also introduces “boil-off,” with the likelihood that some of the product will be lost to evaporation.
Green hydrogen is potentially green the whole way through, but expensive compared to petroleum alternatives. Technology breakthroughs and government incentives will improve its cost competitiveness over time.
A potential alternative is green or blue ammonia, which is a way to store and ship the hydrogen molecule within another common industrial chemical. Green ammonia is produced when nitrogen is added to green hydrogen. Blue ammonia employs carbon capture and sequestration to improve its sustainability. These renewable fuels are also generating buzz, but they come with significant supply chain and refueling challenges as well. Although there are existing supply chains for conventional ammonia, it is a toxic inhalation hazard that must be handled with extreme care.
Keeping the Supply Chain Fully Charged for Battery Materials
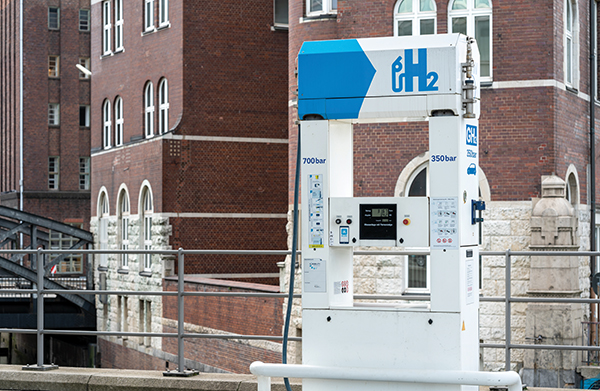
The movement of metals and minerals used in electric battery production is poised for significant growth, driven by the increasing demand for sustainable energy solutions. Aside from the normal supply chain trials and tribulations, the larger challenge for manufacturers is sourcing the quantity of energy transition minerals (ETMs) needed to support a clean energy future.
The International Energy Agency estimates it will require six times more mineral inputs than the quantity moved today to reach global net-zero targets by 2050. There are potential chokepoints in both the mining of raw energy transition minerals and in processing them into the forms used in batteries.
Elon Musk famously exhorted entrepreneurs to enter the lithium refining business. “It is basically like minting money right now,” Musk said during a Tesla earnings call in mid-2022. The price of lithium has since dropped, as commodity prices are prone to fluctuate; nevertheless, Tesla continues to vertically integrate into lithium processing at a site near Corpus Christi, Texas.
One can easily imagine a future in which having access to lithium mining and/or refining has as much geopolitical significance as being a low-cost oil producer. Four countries (Australia, Chile, China and Argentina) produced 94 percent of the world’s lithium in 2022 according to U.S. Geological Survey. China’s share of raw lithium production is about 15 percent, according to the U.S. government data. But it dominates lithium refining with 60 percent refined in China, according to Barron’s.
The U.S. is investing to close the gap. The bipartisan Infrastructure Law included $3 billion in funding for battery manufacturing and battery recycling grants to “ensure that the United States has a viable domestic manufacturing and recycling capability to support a North American battery supply chain.”
Canada also has significant deposits of spodumene, a coarse rock that contains lithium. There are more than a dozen projects to develop mines and produce concentrated product there.
Like many mining materials, ETMs rely on bulk movements in ships and railcars for the upstream portions of their journey. As they move downstream through the refining process and become more valuable finished and semi-finished products, trucking becomes a more attractive mode since it is quick, flexible and secure.
Lithium and nickel products require transportation infrastructure and rail fleet. Most rail carriers will not supply railcars, thus the design of the infrastructure needs to consider fleet size and the possible need for railcar storage. Before market players move forward, it is important to work with experienced transportation professionals to achieve the best results.
There is also a significant challenge in the co-products created in processing raw ETMs. Processing lithium ores creates large amounts of co-products that must be stored until they can be shipped to another user. It is estimated that co-products can account for about 70 percent of the ETMs and reagents used to process them.
No Easy Solutions to Plastic Waste Issues
No discussion of sustainability would be complete without a discussion about plastics. Significant breakthroughs in advanced recycling are broadening the spectrum of which plastics can be recycled and improving their performance nearly to the level of virgin plastics. Nevertheless, significant supply chain challenges remain to ensure that recycled feedstocks materialize and can be shipped efficiently.
Every year, more than 300 million tons of plastic waste are generated globally. Approximately 36 percent of all plastics are used in packaging, including single-use plastic products for food and beverage containers, and most of that ends up in landfills, according to the United Nations Environmental Program. Only nine percent of plastic waste is recycled worldwide and only four percent in the U.S., according to estimates by the Organization for Economic Co-Operation and Development (OECD).
The production of plastics made from recycled materials is growing; in fact, it has more than quadrupled in the last two decades according to the OECD, but it still represents only about six percent of total production.
Consumer packaged goods companies are making pledges to use more recycled content. For example, Coca-Cola pledged its packaging worldwide will use at least 50 percent recycled material by 2030. Unilever pledged to cut its virgin plastic use in half by 2025.
Advanced recycling brings plastic waste back to its molecular building blocks. One method of advanced recycling, pyrolysis, involves subjecting plastic to extreme heat without exposure to oxygen. The plastics break down into pyrolysis oil, which can be used as a plastic resin feedstock. Advanced recycling is more energy-intensive than mechanical recycling, but it allows materials that would otherwise be sent to a landfill to be reused. Advanced recycling facilities in North America will need hundreds of thousands of tons of suitable waste products. They must be properly sorted, cleaned and baled.
Since there is an overall shortage of materials that reach the recycling stream, longer supply chains are required from the population centers to mechanical and advanced recyclers. That increases costs and transit times.
Plastic maker LyondellBasell estimates that there will be demand for 15 million tons per year of recycled resins by 2030, but supply is projected for 10 million tons.
A circular economy requires a circular supply chain, but let’s face it, we don’t excel at reverse logistics. What would a more efficient reverse logistics supply chain look like?
I have been living for the last year in Germany, where consumers put all their plastic and metal packaging waste in the “yellow sack” and take it to a deposit point strategically placed around town (mine is about three blocks away). Paper, glass and biodegradable food wastes go in separate waste streams, sorted by the consumer.
It can be difficult to keep these multiple waste streams organized. I have four bins in my kitchen. I don’t think most U.S. consumers are ready for this regimen, but it’s hard to argue with the results. Over 60 percent of municipal waste generated in Germany since 2005 has been recycled, according to the German Environment Agency.
Boosting U.S. recycling requires a complete change in consumer attitudes, values and behavior that won’t come easily. What is already shifting is a growing feedstock demand for mechanical and advanced recyclers. Getting recyclables into their hands cheaply and efficiently represents a significant market opportunity.
Supply Chain Management in the Circular Economy
As the energy transition develops, new supply chains are emerging to support increased demand for the commodities that will power our lives more sustainably. The process of matching these supply chains to the needs of the shipper in terms of costs, speed to market, safety, preservation of product quality and inventory management are key to ensuring success.
For transportation and logistics providers, there is a significant opportunity to penetrate these new markets as a first mover by tailoring services to meet shippers’ needs. For economic development officials, there is a significant opportunity related to building supply chains that radiate from their cities and states. For shippers, there is a significant opportunity to leverage the supply chain to gain an advantage over the competition and to better serve customers.
Whether you approach the supply chain from the perspective of a freight carrier or shipper, good supply chain management is never a “set it and forget it” task. It requires constant monitoring, negotiation, procurement and continuous improvement to ensure best-in-class performance. It is that constant feedback loop of designing, maintaining and improving supply chains that will be a central task needed to create the circular economy. T&ID