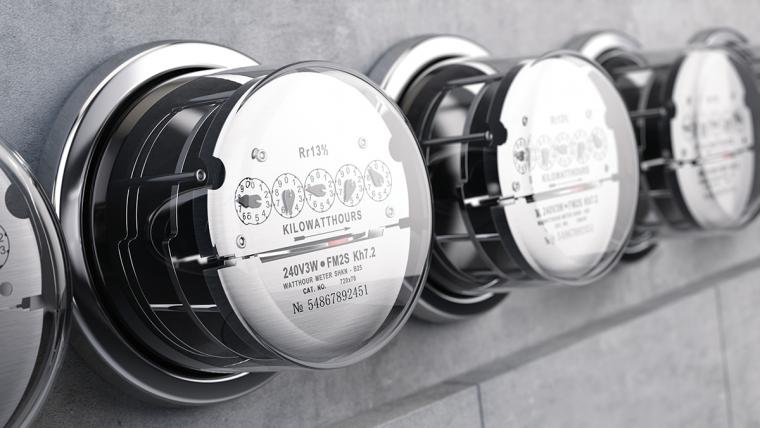
Evaluating and selecting a site on which to locate a new manufacturing facility is a complex process; there are many key considerations. Accessibility of the geographical location is an important factor, regarding airports, highway systems and navigable ports for transportation of raw materials and finished product. The available labor force is another key factor as it represents the lifeblood of the facility’s production and figures prominently in the overall success of the operation in terms of productivity and community development.
A third key consideration when evaluating and selecting a site is the availability and quality of basic utilities. Because utilities can represent between 20-30 percent of overall annual (recurring) operating costs (depending on industry), it is vital to assess them keenly, as their lasting impact can be significant. Not only are there several types of utilities to evaluate, but there are also costs tied to each utility that come with two-fold considerations: initial startup costs and annual recurring costs. Finally, it is important to evaluate the company’s future projections for growth when determining the best location.
This article focuses on evaluating utilities during the site selection process and how discovery of both startup and ongoing utility costs can figure prominently into determining the true attractiveness and potential of the site.
Utilities Defined
Basic utilities necessary for use in manufacturing traditionally include water, wastewater/sewer, electricity, process fuels such as natural gas and telecommunications. To improve the environment, preserve natural resources and lower their carbon footprint, some manufacturers may explore the use of alternative energy sources, services and practices. These include solar energy, co-generation or Combined Heat and Power (CHP), fuel oil, well water and on-site wastewater treatment. For this article, however, the traditional definition of utilities will be used.
Water is vital to manufacturers. Twenty-two percent of the world’s water supply is used for industry1, and every manufactured product uses water as part of the production process. Generally, most manufacturers rely on municipal water systems to provide all water needs for processing and potable uses. If that is the case, a critical evaluation must take place prior to site selection to assess the water utility’s suitability. Using the criteria of needs, availability, capacity, quality and cost, a manufacturer can decide whether the site and community can support its water needs now and will increase with future growth, as well as whether associated costs are acceptable.
An assessment of municipal water suitability should start with a study of the facility’s potential usage regarding gallons per day/month, peak demand times, processing versus domestic usage and special water requirements. Then, water availability can be assessed regarding surface water and ground water and the size of the water main to ensure proper flow to the site. Capacity should next be examined, including a measurement of the community’s average excess capacity that’s typically available for use. Water quality should be assessed with a formal analysis to specifically determine the chemical content of a potential community’s water; the analysis should identify not only the presence of, but also the density of organisms and dissolved minerals that could potentially interfere with industrial processes.
Finally, when all other criteria are evaluated for suitability, an assessment of potential water costs involved with using the municipal system should be done. Since water usage costs can be affected by several factors in the community, and can vary widely regionally and from location to nearby location, it is wise to do one’s due diligence in discovering specifics. Water costs can take the form of one-time fees and ongoing service charges: one-time fees may be for initial connection to the water line, as well as impact fees for usage; ongoing water service charges are commonly based on thousands of gallons of water used, either on a monthly or quarterly basis.
Other factors related to water costs are age and condition of the water system (along with current and planned expansions to the system), growth rate of the community and its past ability to expand the system to address that growth, the history/volatility of past service charge increases and the community’s projections for future increases.
Wastewater (or effluent) service charges consider the amount and composition of the wastewater discharged by the industrial facility into the community’s sewer system. A thorough site selection process should initially consider whether a gravity-feed or pump station system will be required to handle the facility’s effluents, as well as the total system capacity, average daily usage, peak daily usage and excess capacity, all measured in million gallons per day (MGD), effecting overall wastewater costs.
In addition, communities vary widely regarding whether or not they accept untreated effluent, as well as how much and what type of untreated effluent they allow into their treatment plant. Additional costs or surcharges are often imposed by a community based on effluents discharged by a company and the type of treatment those effluents require. These costs are typically based on the measured value of Biochemical Oxygen Demand (BOD), which is the amount of dissolved oxygen required during the treatment process to biologically decompose any organic matter in the wastewater, as well as the measured value of Total Suspended Solids (TSS), which is the total amount of materials in the wastewater.
Be sure to conduct a thorough discovery of maximum allowable limits for effluents (measured in mg/l), as well as any surcharges for exceeding limits in terms of BOD, TSS and other effluents. An estimated, itemized monthly bill based on wastewater usage and effluent production costs is necessary when evaluating a site for industrial development; this should include all applicable one-time connection and community impact fees. Any applicable state and local taxes should also be assessed.
Electric power can figure prominently into a manufacturing facility’s costs. Electricity needs can vary widely depending on industry, but are generally evaluated in terms of kilowatt hour (kWh) and maximum demand (kW) as units of measure. Electric power requirements can be assessed based on the type and amount of electrical equipment to be used in the facility. Daily electricity needs to run the equipment, key equipment’s sensitivity to power fluctuations, time of use and amount of use per day and the potential overall maximum demand for electricity are all factors that affect costs.
The need for process fuels, usually in the form of natural gas, should be considered. Consumption of natural gas for heating and production processing is calculated in therms (the unit of heat equivalent to 100,000 Btu or 1.055 × 108 joules) or MCF (denoting a thousand cubic feet of natural gas). The natural gas needs of the facility, in terms of line size, delivery pressure in psi, time of use, hours of use and non-interruption issues should be assessed in detail as they can figure prominently into costs of not only natural gas service, but also reliable delivery of other process fuels such as fuel oils.
Finally, costs of providing telecommunications to the potential site should be assessed. This assessment should include a thorough review of both routine and special requirements of the facility regarding Internet usage, data services, phone lines and fiber optic capability.
Startup/One-Time Costs
Potential costs for each utility should be thoroughly discovered during the field investigation phase. Again, the costs are two-pronged, including startup or one-time costs to get the facility up and running and ongoing costs incurred monthly to keep the facility in continuous production.
Initially, key providers for water, wastewater, electricity, process fuel and telecommunications services should be identified. Working with them, determine if the utilities currently being delivered to the site are adequate for the facility’s startup needs. If they are not, determine how the infrastructure will be augmented or updated and if the costs to do so will be paid by the organization, the utility or a combination of the two. Augments and updates can include extending utility lines to the site, increasing line sizes and increasing delivery pressure.
Specific utilities may require initial improvements. In the case of electricity, a dual feed of service from an existing or alternative substation may be required or capacity may need added to an existing substation. In the case of water, especially in areas that face chronic water shortages, it is not uncommon to find that the community will mitigate impact on their water supply from industrial usage by collecting significant one-time, high-impact fees, the proceeds of which can be reinvested in the community. Initial wastewater costs may also include one-time impact fees. For both water and wastewater, the development of company-owned-and-run operations like on-site well drilling or pre-treatment plants may need to be explored as options; these costs will figure into initial expenses, but can save money on ongoing costs longer term.
For all utilities, the field investigation phase can be completed by requesting detailed estimated monthly bills from each utility. These documents will serve as a baseline on which to measure ongoing utility costs for the facility.
The Role of Deregulation
It is important to note that when considering regional differences in utility costs, deregulation comes into play. Some states in the U.S. are deregulated for electric power and natural gas, some are not. When assessing these costs within a deregulated state, it may be found that providers — because they act as distributors in these states — are less likely to absorb any one-time costs required to prepare a site to meet a company’s needs through line extension. Therefore, it is wise to do one’s due diligence in deregulated states when navigating the most advantageous deal up front.
Estimating and Verifying Ongoing Costs
Once initial startup costs have been discovered for each utility and estimated monthly bills have been secured, the field investigation phase is complete and one can move to the verification phase of the site selection process. This phase helps uncover the intricacies of ongoing, long-term costs represented by monthly charges from each utility. At this point, the company can request a commitment letter from each utility provider. These letters should include confirmation of the specifics discovered during the evaluation process, including the community’s ability to meet usage requirements; confirmation of line sizes and locations on the site; and confirmation of total system capacities including average daily usage, average peak usage and excess capacity. It is also important that the commitment letter include projections regarding potential cost increases to ensure the site and its utilities remain adequate as the manufacturing business grows.
Startup Cost Relief
In many instances, a company may have the opportunity to gain some relief from startup costs through incentive programs negotiated through community, state and regional development organizations. Communities eager to attract manufacturers may be willing to assist with startup costs by helping to negotiate with utilities or by providing grants for connection and impact fees. This should be explored in detail as part of the field investigation.
There is no doubt that the detailed discovery of utility costs is a major factor in the search for a new facility location. Routine and special issues with startup costs, estimates of monthly recurring costs in the long-term and the potential for relief from some of those costs in the form of incentives are all factors to explore. When all the facts are uncovered and surprises are eliminated, the company can then move forward in selecting a site that will serve its needs in both the short-term and as the company grows. T&ID
1http://www.unwater.org/downloads/Water_facts_and_trends.pdf