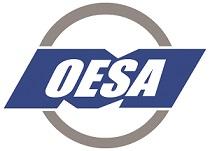
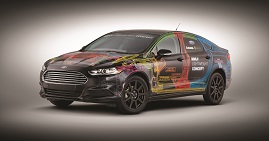
Automotive suppliers supported the production of 17 million units of light-duty vehicle production in North America in 2014 and will meet the expected production of 17.3 million units in 2015. Further out, the leading automotive forecasters are predicting an average of 17.7 million units of production in 2016 and 18.2 million units in 2017. Capital investment in plant and equipment will be required in the supplier sector to flex-up and support 1.2 million units of additional production over the next three years. Additional human capital also will be needed. In fact, 70 percent of OESA members report they are hiring production employees. Still, as mentioned previously, suppliers are being cautious about adding fixed costs to their breakeven points. OESA members estimate their breakeven point to be 13.5 million units, an increase of 42 percent from the depths of the 2008-2009 recession. However, North American production has doubled in the same time period.
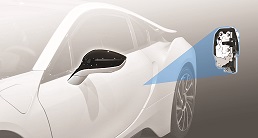
This points to the need to build supplier capacity in very strategic ways, looking closely at supplier locations that optimize inbound and outbound logistics, access to the right human resource talent pools, proximity to customer and supplier engineering and design staffs and utility costs – typically the top four criteria mentioned by OESA members – along with all the other business climate conditions that go into a site location decision. All said, the number one priority of the supply base is the support of their customer: the large system integrators are focused on the vehicle manufacturers and the subtier-suppliers focus on their customers down through the supplier value chain. There are two main trends driving supplier strategies in the support of their customers. The first is the gravitation of assembly production toward Mexico and the second is the introduction of new technologies into the finished vehicle.
Regarding Mexico, a number of European and Asian vehicle manufacturers have announced at least 1.3 million units of new assembly capacity coming online between 2014 and 2020. The consulting firm IHS Automotive has analyzed the epicenter of North American automotive production, and on a production-weighted basis, this growth of vehicle assembly in Central Mexico will move the epicenter of the industry from the border of Missouri and Arkansas today to the Northwest corner of Arkansas by 2021. In turn, the suppliers are analyzing if they need to build additional capacity in Central Mexico or if they can ship from existing locations. In addition, the suppliers are receiving inquiries from vehicle manufacturers to build capacity in supplier parks around new and existing assembly plants throughout the entire North American continent. One thing is certain; the supply base does not want to enter into situations where new capacity will be “stranded.” That is, stranded because it is located in a way to serve a single customer that might drop off or out of its customer mix. Or perhaps it is stranded because it is locked into a single component, material or process that becomes obsolete due to a disruptive technology or market force. Creating options and degrees of freedom to respond to a very dynamic market is core to every supplier’s product and manufacturing strategy.
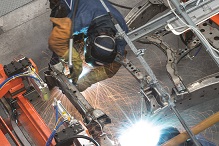
The second major force driving the supplier investment is new product innovation. From consumer-driven and safety-related innovations related to active cruise control that keeps a constant distance between vehicles to lane departure technology that can warn the driver or steer the car back into safety, electronic, driver-assistance technologies are proliferating within the vehicle. This is opening up the door to a whole new set of automotive suppliers entering the industry (particularly those providing cameras, controls and software) to traditional suppliers growing whole new business units (specifically the first tier suppliers that are integrating all of these new technologies into powertrain, steering and other systems). Vehicle manufacturers and suppliers are opening R&D centers and skunk work operations in the Silicon Valley, California, region to tap into the design and engineering talent required to develop and bring these new technologies to market. New testing facilities are opening up to accommodate the development of autonomous vehicle and road infrastructure requirements.
In conclusion, the North American automotive industry and the supplier sector is very healthy. However, there is no room for error. The industry is expecting prefect product launches, significant increases in incremental volumes, rapid response and correction of any recall situations and the successful introduction of new product technology and manufacturing processes. The next five years will bring more change than the past 15 years. And it will be positive change – dramatically different than the change imposed on the industry in 2008 and 2009.The industry will remain disciplined. The industry’s focus on return on invested capital and cash flow will assure this discipline. And that focus on return on invested capital will also drive the industry toward new opportunities from new assembly capacity to supplier-driven product and manufacturing product innovation.