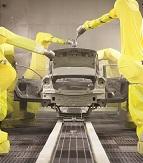
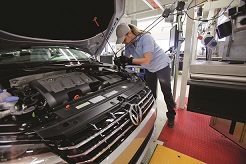
-
Sales of personal vehicles for 2014 are expected to be 16.5 million units, up nearly 60 percent since the dismal 10.5 million in 2009.[1]
-
Employment in the motor vehicle manufacturing sector grew at an annual rate of 4.7 percent, more than four times the lackluster 1.1 percent for U.S. manufacturing as a whole.[2] This is especially favorable given the puny job generation rate that has characterized the nation’s recovery from the Great Recession.
-
Over $30 billion in new capital investment has been announced. Volkswagen, for example, announced plans to invest $7 billion in North America during the next five years, much of which will probably be for a new assembly plant.
-
Other metrics are improving, such as quality of U.S.-made automobiles. Toyota will produce the Lexus ES350 at its Georgetown, Kentucky, plant, the first time the company’s showcase brand has been manufactured outside of Japan.
-
New technologies are being commercially implemented. The stars finally seem aligned for widespread use of electric engines. For example, Nissan’s Leaf has received strong consumer acceptance in the U.S. with about 45,000 units sold. Electric car maker Tesla Motors became profitable in 2013.
But what are the implications for new assembly plants in the U.S.?
How Things are Different
October, 2013, saw production in U.S. assembly plants of nearly 1.6 million vehicles, the largest monthly output since 1999.[3]This statistic raises a broader question: how has the auto industry changed over these past 15 or so years, particularly in its manufacturing strategy?
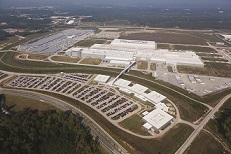
One of the most striking differences is the reduction in the number of assembly plants and staff. The number of U.S. workers employed in motor vehicle manufacturing facilities has gone down by about 100,000, from around 235,000 in the late 1990s to about 137,000. The number of major U.S. assembly plants has dropped from 65 to 43. These refer to Code 3361 in the North American Industry Classification System, which includes cars, trucks, busses and special-purpose vehicles such as fire engines. The 33611 subsector, comprised of cars, vans and light trucks typically purchased by consumers has gone from 204,000 employees/52 large U.S. plants to 109,000 employees/36 large plants.
On the one hand, the number of U.S. facilities and employees are unlikely to return to 1990s levels for a long time. On the other, productivity and its contribution to the industry’s health and sustainability have soared.
-
Automakers have made large equipment investments including robotics and automation that allow for more output per worker and plant. Perhaps recent downsizings allowed for some plant rationalization such as closing less-efficient facilities, although this is not clear.
-
They have extracted more performance from existing facilities by adding shifts and other more intensive use of established capacity.
-
Assembly plants make greater use of vendors. Suppliers now contribute over half the value of completed automobiles and in some cases over two-thirds.
-
Eliminating brands such as Plymouth and Saturn considered lower end or less popular may have been part of corporate strategies to produce more high-value, larger-volume, higher-profit units resulting in favorable impacts on financial performance.
Geography
Since the late 1990s, the number of states with large automotive assembly plants has declined, the geographic area of auto assembly has become more focused and concentrated and the centroid of car production has moved south.
In 1998, 26 states were home to one or more large motor vehicle manufacturing establishments (1,000-plus employees); geographically they were fairly disparate, from New Jersey to California. Toward the end of the economic downturn, only 16 states had such plants. (The number is rising again with use of some closed plants by non-legacy companies.) On the positive side, Mississippi, which had no assembly plants in the 1990s, now has Nissan and Toyota. Alabama in 1998 had only one, Mercedes; it has since recruited Hyundai to Montgomery and Honda to Lincoln.
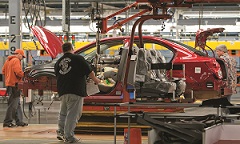
One generalization is that more modern plants in southern states have replaced older, less-productive facilities in northerly locations that had problems related to efficiency, quality and work ethic. There is truth to this, but it is an incomplete explanation for all geographic shifts. Traditional U.S. car companies, the states and communities in which they are located, their workforces and labor organizations and others in the industrial heartland went through a near-death experience and have learned from it. Major efforts have been made to revive the auto industry’s original geographic base and make it more competitive, with some commendable successes. Recent U.S. Commerce Department data show that the state adding the most motor vehicle manufacturing jobs was Michigan.
Another key influence on assembly plant location is logistics, especially inbound. Assembly plants must have rapid, efficient delivery from the supply chain network since suppliers provide so much of the value of finished vehicles and components, and they must be delivered on a just-in-time basis. Over half the nation’s auto parts plants and over 80 percent of the large ones that probably provide the biggest, most sophisticated components, are in the dozen states in the I-55/65/75 corridor. Hence the concentration of assembly plants in that area is no surprise.
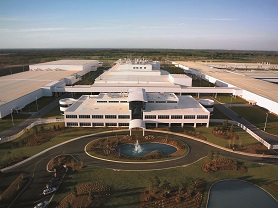
So the greater influence of supplier locations and reduced role of market proximity may have contributed to closing facilities that were primarily regional or branch plants, which served a geographically limited market or were too far outside the vendor network. The Northeast and California have some of the nation’s greatest personal income and purchasing power, but have lost their traditional auto assembly facilities. (The former Fremont, California, NUMMI plant and GM Wilmington, Delaware, plant are each to be re-used by electric car makers Tesla and Fisker.) Even in growing sunbelt states, plants significantly east or west of the supplier corridor were closed, such as Ford’s F-150 plant in Norfolk, Virginia, and GM’s Oklahoma City SUV assembly operation, despite multi-hundred-million-dollar investments in both only a few years before. (There are exceptions such as long-established GM plants in Kansas and Texas and Toyota’s San Antonio plant that began manufacturing pickups in 2006.) In 2017, auto assembly will totally cease in Australia, which at one time had a robust independent domestic automobile manufacturing industry.[6] It says a lot if assembly no longer makes sense in a wealthy, car-dependent nation of 24 million people.
Continental Drift
For decades, auto manufacturers have maintained a highly integrated production scheme among the three major nations of North America. An automotive pact has been in effect between Canada and the U.S. since 1965; NAFTA (North American Free Trade Agreement) in 1994 expanded both scope and geography of free trade. Canadian- and Mexican-assembled vehicles have been well accepted by U.S. buyers. Units of GM’s prestige Cadillac brand are assembled in Coahuila. U.S. police departments were unconcerned that their most popular vehicle, the Ford Crown Victoria, was a “foreign car,” having been assembled in Ontario.
However, Mexico’s recent dramatic increase in auto production raises eyebrows. In 1994, when NAFTA went into effect, Mexico was responsible for six percent of North American auto production; now it does 19 percent and this is likely to rise with recent new plants. Mexico is expected to pass Japan and Canada as the top exporter of cars into the U.S.[7] In February, 2014, for example, Mazda opened its new 230,000 unit/year Salamanca assembly in the central Mexican state of Guanajuato. This will now be its only North American assembly operation, following its departure from the Flat Rock, Michigan, plant that Ford built in the early 1970s and now has taken over again. The Salamanca Plant is notable for several reasons, one being application of sophisticated technology allowing a single set of components (engine, transmission, body systems) to be used in a variety of vehicles. Audi, after looking extensively at the U.S., chose to construct its North American plant in Puebla.

Exports have become a vital part of the U.S. auto industry, totaling over $12 billion in January alone.[8] Failure to nourish and sustain this rapidly growing business can reduce market opportunities and revenue for U.S. firms, harm the U.S. balance of trade and cause other problems. Several carmakers building plants in Mexico are known to have considered the U.S. before making their location decisions.
Forecast for 2014
The crystal ball is cloudy and most carmakers are guarded when discussing plans, but many conditions support the concept of new U.S. assembly plant construction.
Many existing plants are at or close to capacity and are straining to meet demand; dealers of some brands are screaming for more cars to sell.
Upgrades to existing plants have generated productivity improvements and greater output, but the point may have been reached where this is no longer enough. Some companies have put off constructing new plants even though markets appear able to absorb their products; further delay puts them at risk of losing sales and market share. Such attitudes are understandable. Having gone through a historic downturn and the trauma of closing plants and laying off employees, they have been reluctant to construct new ones even as economic conditions improve. They want to be sure they can sustain whatever staff and facilities they have. Hesitancy to build new plants, however, may be about to lose credibility.
There will probably continue to be increases in market demand for personal vehicles in North America. Auto sales have historically tracked general prosperity — buyers need to feel reasonably secure about economic prospects before taking on such major purchases. The job-generation aspect of the current economic recovery has been poor, but shows signs of gradual improvement.
The U.S. represents an attractive location for auto production. It and its partners form one of the biggest and fastest-growing markets in the world while some other countries are less appealing with regard to investment climate, protection of intellectual property and other criteria.
Absence of U.S. free trade agreements with more of its export destination trading partners is a prominent and troubling matter, but is receiving attention. Automotive exports to non-NAFTA countries nearly tripled between 2009 and 2012 and have since grown further, according to the International Trade Administration.[9] However, are such sales sustainable when similar vehicles are available from less-expensive sources? Favorable resolution of this vital trade issue can add more impetus to development of new auto plants in the U.S.
[1] Ward’s Auto and Center for Automotive Research, http://www.cargroup.org/assets/sites/tradeandindustrydev.com/files/forecasts/2014_-_q1_forecast.pdf
[2] U.S. Commerce Department, County Business Patterns data series, http://www.census.gov/econ/cbp/. Unless otherwise stated, statistics are from this source.
[3] Ward’s Auto/CAR, cited above.
[4] https://www.bmwusfactory.com/bmw_articles/bmw-manufacturing-recognized-for-export-success-at-south-carolina-plant-2/