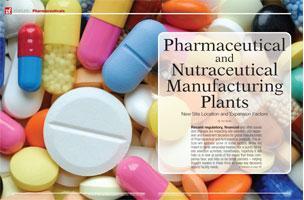
Recent regulatory, financial and other issues and changes are impacting site selection, site expansion and investment decisions for global manufacturers of Pharmaceutical and Nutraceutical products. This article will address some of these factors. While not meant to be an exhaustive treatise, nor a punch list for site selection activities, nonetheless, hopefully it will help us to look at some of the issues that these companies face, and help us be better partners – helping thought leaders in these firms to make key decisions around facility needs.
Some of the major issues Pharmaceutical & Nutraceutical manufacturers are facing today include:
1. A lingering global recession and restrictive capital
2. Stringent new guidelines for regulatory compliance and safety
3. An awareness of a need for “zero tolerance” for microbial contaminants
4. Rising energy costs and increasing desires to implement renewable energy solutions
5. Profit squeeze on products – driving cost saving measures that include increasing upkeep and maintainability of plants for maximum useful life.
With these items in mind, it will be more important than ever to help understand the key business goals and objectives of companies as they explore options for growing their businesses through expansions. It will now be more incumbent than ever to make a careful “go/no-go decision” that will look at one or more of these options:
Adding capacity at new grass-roots sites
Expanding at an existing site or campus
Growing production internally through renovation and re-engineering of the processes and space.
The site selection professional that can be fully cognizant of these factors, and that helps participate in an unbiased fashion will find this to be a win-win solution for both parties in the long run. Over the last year, four out of five clients that this observer has worked with, have put new greenfield projects on hold and are looking to increase profits and market share through one of the other two alternatives.
Let’s explore this further:
Restrictive Capital
Companies that may have down-sized and faced increasing erosion of profits are more conservative than ever when looking at large capital investments, especially when it comes to new plants and distribution facilities. Facing large sunk costs at existing sites, executive management and company boards are looking hard at new Greenfield projects.
Careful analysis that looks at all of the major business drivers will be required, which should at a minimum address:
United States / Global:
Competitive construction costs and reasonable building design requirements
Quality of life that supports recruitment and retention of technical and professional staff
Close proximity to public and private institutions active in bio-medical research with a tradition for business sector R&D partnerships
Industrial support services that meet the needs of pharmaceutical manufacturing
Commercial air service that provides convenient access for corporate staff, customers and others requiring access to/from the facility
Reliable and affordable utility services including electric power and natural gas
Ample supply of high quality water at a reasonable price
Modern and reliable telecommunications infrastructure
Business friendly community that understands and supports the needs of Pharmaceutical, Nutraceutical, and other Life Sciences and related organizations that deal with cGMP environments
Development incentives geared to these sectors including reduced cost financing, workforce recruitment and training, tax credits for R&D, property tax abatement
Availability of highly productive workers with a good work ethic and at affordable wages
Tradition of labor-management cooperation.
Finally, a Master Plan should be developed that has input from all stakeholders and that looks at both on-site expansions vs. new sites.
Computer Modeling and simulation may be used to look at increasing production with existing processes, as well as planned capital investments. These activities may draw out the site selection process from a schedule standpoint, but ultimately it will benefit the organization as they can make valid business decisions based on solid evidence.
Stringent New Guidelines for Regulatory Compliance and Safety
Global companies that operate in the United States are facing more scrutiny by the FDA for compliance with Current Good Manufacturing Practice (cGMP) requirements and validation protocols. Moreover, these organizations are also rapidly moving to comply with both the letter and spirit of European guidelines (EMEA).
One large pharmaceutical company I’ve been working with has had to address this through creating dedicated conference rooms for visiting regulatory agents and with extensive modifications to their facilities to ensure compliance.
For some companies, this may create a focused need for both time and capital to be dedicated to renovation projects and re-engineering to ensure compliance at existing sites. For others it may lead to a decision that a more cost effective solution would be to start with a blank slate at a new site for new products and processes.
Zero Tolerance for Microbial Contamination
Along with regulatory scrutiny, leading companies want to protect their reputation and their “Brand” by ensuring that their products meet the highest standards of safety and quality. Microbial level contamination by bacteria, viruses, metals and other contaminants must be strictly avoided. Most of the manufacturing companies in these industries are addressing these concerns in a variety of ways. Foremost among these methods is to keep potential contaminants out of the plant in the first place.
Some of the methods used to help in this regard include:
New and better designed locker, gowning and scrub rooms
Better segregation within the buildings and between certain types of buildings on the campus between “clean” and “dirty” designations
Design of the overall campus and buildings to severely restrict access to anyone who is not adequately gowned and monitored
Airlocks, corridors and vestibules designed to keep contaminants out of clean manufacturing spaces
Significantly changed designs of newer facilities in ways that many are not accustomed to, for example, eliminating or severely changing the way that deliveries are made, and restricting drivers to carefully controlled areas
Uniform and gowning requirements for workers who were previously not required to wear them
Training and awareness programs.
Renewable Energy
Pharmaceutical & Nutraceutical companies tend to be led and run by innovative and creative people. Also there is a strong global operating stage that they practice their trade upon. It should be no surprise that many of these companies are some of the early adopters of energy conservation and renewable energy policies and actions.
From a site selection and/or expansion perspective this adds some new items to the list of important location factors for many of these companies, a few of which include:
Near green energy sources
In states/municipalities that offer feed-in tariffs
Workforce that appreciates a green culture
Partners including their design and construction teams that understand renewable energy strategies, LEED issues, and that can help them best achieve their goals in this regard
Facilities that minimize impact on their surroundings.
Product Cost Drivers: How these Affect Design, Maintenance and Operation of Plants
Dan DeGrendel, a senior process engineering manager in Columbus, Ohio, who has worked for over 20 years with two of the world’s leading pharmaceutical and Nutraceutical companies, offers the following on the importance of designing in “maintainability” with new plants, and in making long-term commitments to operating and maintaining plants for the highest level of efficiency:
“For most companies, a bad day is if production is down or product was scrapped. As we move forward, for companies that do not have a catastrophic consequence of failure, maintenance will no longer be seen as an operating expense but as an important enabler of the company's mission. Companies that ‘get it’ will thrive in the future; those that do not will continue to experience higher manufacturing costs and will not survive.”
Dan goes on to address reduced profit margins and their impact on these companies, “Historically, pharmaceutical and Nutraceutical companies have benefited from higher product margins. Their primary objective is to meet regulatory requirements. Product cost is a secondary consideration. Moving forward, they need to apply concepts common to other industries in order to lower product costs and remain competitive. This includes applying reliability engineering concepts to increase equipment up-time and reduce operating costs…”
Facing Unique Challenges
In summary, pharmaceutical and Nutraceutical manufacturers face many unique challenges that other industries often don’t even consider, and these issues and challenges are growing ever more complex and costly. These companies will continue to grow, expand and build new plants. To best understand their site needs, it will be helpful to fully understand the issues and challenges that they face.