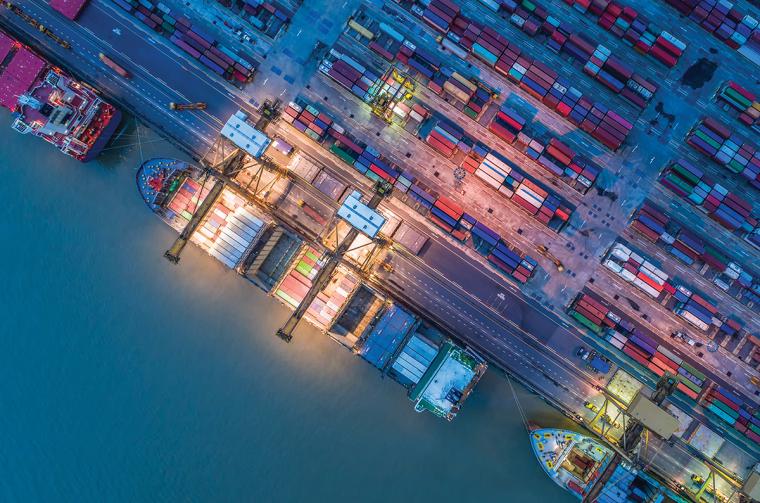
For most of our world history, societies have lived in a very regional world. What was produced in a region was consumed in that region. Sure, there are many examples of great traders and explorers, such as Marco Polo and Ferdinand Magellan, who sailed the world discovering and trading commodities, but it was not until the 1970s, with the advent of containerization and international shipping, that global trade started to evolve rapidly. The creation of the World Wide Web, as well as new technologies that it sparked, were the major catalysts of global supply chain management as we know it today.
We now live in a truly global world economy. Companies make and ship products all over the world and must manage very complex supply chain networks of plants and distribution centers to serve their customers in the most efficient and effective ways.
Globalization has created its share of opportunities and challenges for manufacturers. It has pressured U.S. manufacturing companies to innovate, get lean and become smarter and faster at what they do to compete with countries that operate with lower costs. Since U.S. manufacturers are not always able to compete from a pure labor-wage-rate standpoint, especially for lower-tech, labor-intensive goods, often their only option is to be more innovative. New product development, lean practices, productivity improvements and new technologies have all come into play.
The quest for competitive advantage and growth led companies to low-cost manufacturing countries. Coupled with the rapid evolution of the Web and supply chain technologies, this enabled truly global supply chain strategies — “make it anywhere and ship it anywhere” — as long as it was the most efficient and effective solution.
The intensification of globalization, which gave rise to the manufacturing sector in developing countries like China, India, Mexico, Brazil and Vietnam, is now being reexamined. Manufacturers that were caught up in the outsourcing/offshoring craze are reconsidering this method for a variety of reasons.
In light of that, the following examines the “Big 3” changes impacting global supply chains today.
Reason #1: Cultural and political winds are shifting
Like it or not, understand it or not, the votes are in: there is clearly a trend toward protectionism. The proof is in the bread pudding (Brexit) and the apple pie (Trump). The political winds are blowing, and it has been made clear that voters want their government to look after its own welfare and interests first. This sentiment extends to border protections, global trade agreements and immigration policies.
Big companies, for one, are taking note. Walmart, for example, committed to source more products from the United States than from offshore, meaning an additional $250 billion in products either made, assembled or grown in the United States.*
Other consumer trends support a move toward a more regionalized economy, such as the renewed focus on fresher foods (farm-to-table) and locally produced products to support local economies. The increase in sustainability and environmental friendliness also supports a more regionalized supply chain, which typically results in less carbon emissions.
So what does this trend mean for supply chains? Companies that have historically been more focused on importing or sourcing product from thousands of miles away will be negatively affected. This will provide more incentive for companies to consider establishing a manufacturing presence within the country they are serving.
Reason #2: Cost curves have changed
Companies are in business to make money and will always pay close attention to total delivered cost, which includes the cost to source materials and components, the cost to make (direct labor and overhead) and the freight cost to ship.
Typically, the largest cost drivers influencing manufacturing or sourcing decisions are freight costs and labor rates. It was the big differential in labor costs between the United States and China — and Asia as a whole — that created the wave of outsourced manufacturing to begin with.
The consulting firm Alix Partners reported that, in 2005, Chinese-produced parts arrived at U.S. destination ports an average of 22 percent cheaper than comparable products produced domestically. By the end of 2008, the average price gap had dropped to 5.5 percent. Today, according to Boston Consulting Group, the gap has shrunk to approximately one percent.
The rising cost of Chinese labor is a big reason for that gap closing, with average manufacturing wages in China rising 15 to 20 percent annually.† However, an equally important factor is transportation. The higher the cost of transportation, the more significant the freight penalty to ship over greater distances. Freight costs are increasingly offsetting, even eclipsing, savings from cheaper labor.
As transportation costs continue to rise, sustainability goals gain in importance, and as speed-to-market becomes more important, the trend will be to produce products as close to the final consumer as possible.
The fast-growing e-commerce sector, and its heavy demands for labor, has made labor analytics one of the most important aspects of industrial site selection today. Dedicated e-commerce or direct-to-consumer fulfillment centers can require anywhere from three to 10 times the amount of labor for the same footprint of a more traditional distribution center and it can be even more during peak seasons. Pick and pack operations simply require more people than a traditional pallet-in-pallet-out operation.
With unemployment rates at all-time lows and demand for labor intensifying with e-commerce growth, labor has become one of the most critical and sensitive influencers of site selection.
When the holiday season is in full swing, you hear folks being critical of the fact that the Christmas advertising season seems to get started earlier and earlier each year. Like it or not, the Christmas logistics season now starts in September. Amazon, Walmart, UPS, Target, Macy’s, etc. all start ramping up their hiring of distribution labor (think elves in brown suits) and will hire hundreds of thousands of people to support logistics operations during the busy holiday shopping and shipping season.
The growth of e-commerce has had a significant influence on industrial real estate driving rents up, vacancy rates at all-time lows and demand for labor and seasonal labor at all-time highs.
Reason #3: Rapid advances in technology
The world today is in the midst of an Industrial Revolution. Advances in technology are completely changing the world and disrupting (for the better) the way supply chains are managed… and we haven’t seen anything yet.
If you grew up in the 1960s and 1970s, you undoubtedly watched the space-age cartoon comedy, “The Jetsons”. The Jetson family was doing some really cutting edge and crazy things in those days. Among other things, they had driverless vehicles, 3D food printing machines, wireless phones, flying cars and robots. A little crazy, right?
According to a 2017 MHI report developed in collaboration with Deloitte Consulting,‡ robotics and automation were ranked as the most likely technologies to disrupt the supply chain world. Other technologies in the top five included (No. 2) predictive analytics, (No. 3) the Internet of Things (IoT), (No. 4) driverless vehicles and drones and (No. 5) sensors and automatic identification.
Rapid advances in technology will continue to drive innovations in supply chain and distribution with a direct focus on labor productivity improvements, allowing companies to do more with less. Tight labor markets will become less of a constraint to more automated companies, and robotics and other new technologies will disrupt operating practices as we know them, creating opportunities to seek competitive advantage.
We are just on the advent of new breakthroughs in artificial intelligence (AI) and nano technology that will have a huge impact on the world of supply chain as we know it in the not too distant future. Get ready.
Key Takeaways
Shifting views in cultural and political thinking, changes in operating cost curves and rapidly evolving technologies are all catalysts of change in the global supply chain. Increasing freight costs, intensified competition for labor, increasing customer service requirements, global complexities, risk mitigation and cultural sensitivities all play into supply chain thinking and keep corporate supply chain executives up at night.
Regardless of the speed and direction the political winds are blowing, companies will continue to seek ways to make money and serve customers in the most efficient and effective ways possible.
When it comes to supply chain network strategy — how many manufacturing and distribution facilities a company should optimally have and where they should be located — companies must ultimately make decisions that pin their operational strategy to the ground. Having the right facilities in the right locations is critical to making the supply chain work.
This connection between operational strategy and real estate execution has not been easy for many companies to get right. In fact, according to research done by JLL and Deloitte, the findings speak for themselves. Some quotes from those studies follow:
“61% of companies struggle to bridge the gap between strategy and implementation.”
“Many companies simply lack the capabilities to deliver on the strategy.”
— Monitor Deloitte 2016 study (“Strategic Capabilities: Bridging Strategy and Impact”).
It is no wonder then, that the benefits of integrating supply chain strategy and real estate execution are significant and will add value to any process. Having a cross-function team of supply chain experts and real estate execution professionals working closely together is the right answer. Makes sense, don’t you think? T&ID