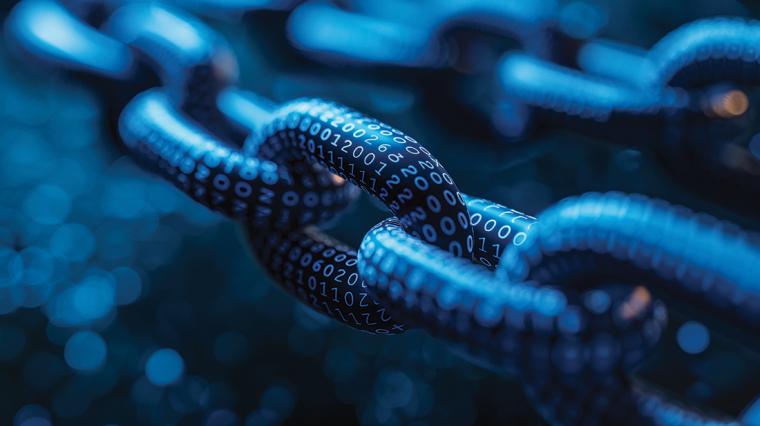
Leading manufacturing companies have long recognized the automotive industryís pivotal role in the supply chain evolution. Data-driven strategic sourcing, supplier performance management, cooperative cost reduction programs and supply chain risk monitoring systems are just a few examples of how auto OEMs have stayed on the cutting edge of procurement and supply chain practices. Automakers have continually reduced lead times, added flexibility and eliminated costly waste throughout the supply chain by communicating real-time production changes and other critical information down through supply tiers via portals. On the supplier quality front, auto companies provide suppliers with instant visibility to even a single defect found at an OEMís plant or in the market, allowing them to identify and address issues before they have a major impact on the OEM or their customers.
Challenges Lead to Innovation
This relentless drive to reinvent has been borne purely out of necessity as automakers have faced a 40-year wave of global competition from Japanese, Korean and now Chinese contenders. With most auto companies buying at least 70 percent of their cost of goods sold (COGS) from suppliers, a constant effort to maintain a cost-effective supply base has been a prerequisite to survival. Those who were slow to innovate have paid the price with losses in competitiveness, market share and profitability.
Beyond the fierce competition, numerous natural disasters, a global pandemic, critical commodity shortages, labor and logistics issues and an unstable geopolitical environment have pushed carmakers to put an equal focus on the stability of their supply chains.
Companies learned the hard way that sourcing the lowest-cost part that does not arrive when you need it is a recipe for disaster. With billions of dollars in assets and thousands of employees tied up in automobile manufacturing facilities, the idling of even a single production line is measured in seconds and has the potential to create extraordinary losses within a single day.
Given the fact that OEM supply chains necessarily span the globe, new sourcing risk models were required to guide procurement decisions in a way that balances part cost and supply risk. Complex monitoring tools also had to be developed to immediately identify the potential impact of everything from relatively obscure disruptive events to major catastrophes around the world.
Data-Driven Strategic Sourcing: Setting New Standards
Even today, automotive industry leaders know that protectionist policies against Chinese manufacturers in certain markets are a temporary deterrent at best, and vulnerabilities in global trade and supplier viability are only growing. Carmakers are scrambling to find the next breakthrough in supply chain efficiency and sustainability to continue competing against the world’s best. They are looking to technologies like artificial intelligence (AI) to forecast demand better, reduce inventory levels across the supply chain, identify potential quality deviations and eliminate low value-added tasks. They also use technologies like blockchain and supply chain financing for security and traceability and to free up valuable capital needed to invest in the future.
Quality Management Innovation: Real-Time Excellence
While a goal of avoiding supply disruptions has risen across the industry as equally important to reducing material costs, leading automakers have prioritized the “cost of quality,” including the impact of defects on OEM production and the potential for devastating recalls. Despite all efforts to eliminate the potential causes for defects, manufacturing processes remain imperfect, leaving detection and quick corrective action as essential measures to minimize losses and maintain a strong reputation for reliability in the market.
Producing a higher portion of their vehicle in their factories, Tesla’s internal supply chain is far more complex than that of many other auto manufacturers. To better manage this complexity, Tesla has created an integrated manufacturing quality system that monitors over 500 process controls during vehicle assembly, using machine vision systems and connected torque tools that feed real-time data to a central quality monitoring system. When any measurement deviates from specifications, the system immediately alerts engineering and quality teams for rapid intervention. This approach integrates quality management directly into the manufacturing process rather than relying solely on end-of-line inspections. OEMs continue to imagine how such a system could span the entire supply chain and provide immediate feedback from every process that impacts the final vehicle’s quality.
The EV Revolution: Reshaping Supply Chains
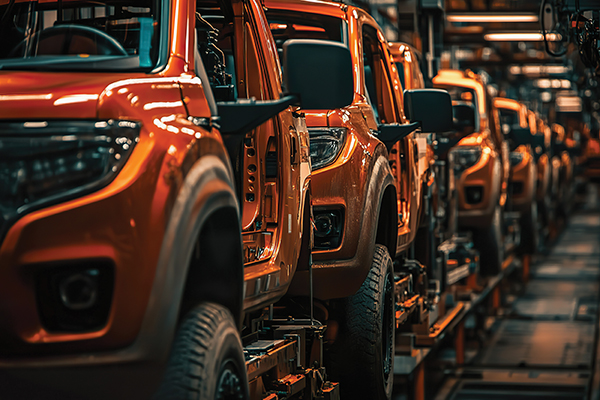
Relentless competitive pressures combined with an increasingly unstable landscape have forced an entirely new way of thinking regarding procurement in the automotive space. At the same time, federal and state regulations forcing automakers to move from traditional internal combustion engines (ICE) to hybrid and electric (EV) powertrains are creating new challenges in the form of changes to the product and processes that have been in place for decades. However, these changes also present an ideal opportunity to implement the next level of innovation internally at the OEM and across the entire supply chain.
With the shift from ICE powertrains, which have traditionally held a high level of OEM in-house value-added (typically in-house casting, forging, machining, engine and transmission assembly) to an EV powertrain which is often highly dependent on suppliers’ content (batteries, electric motors, inverters, DC-DC converters, onboard chargers), the importance of selecting the right business partners and developing the most efficient supply chain is becoming even more critical than in the past.
Large supplier companies that possess leading EV component and system technologies and have the financial prowess to invest in production facilities while continuing to fund the development of the following and next-generation technology are in a much stronger position than traditional suppliers of mature ICE technology. These major EV suppliers have choices regarding where to expend their development and industrialization resources. At the same time, these supplier resources are vital to new startup EV companies and the traditional players trying to compete in a growing EV market while maintaining their current ICE and hybrid vehicle operations. The bottom line is that suppliers of key EV technologies have become, in essence, equal partners to OEMs.
It Begins with a Mindset Change
In the early 90s, a mentor said, “Vendors sell hotdogs. We work with suppliers.” Although he had not yet imagined the term “partner,” the message was consistent. A typical short-term, transactional relationship with a “vendor” is not how a company should want to conduct itself with a supplier of parts essential to producing a high-quality vehicle. It makes good business sense as well. By treating suppliers fairly in the context of a long-term, mutually beneficial relationship, companies can induce these suppliers to go the extra mile, beyond contractual obligations, to make both partners successful.
If you’re starting to get uncomfortable with the kind of soft side stuff that some believe has no place in the rough and tough business world, consider the change that the automotive companies are facing. With certain key suppliers providing a significant portion of the vehicle powertrain technology and a large amount of the development resources and investment dollars, traditional buyer-seller relationships in which suppliers submit a quote on a design that an automaker has conceived are archaic and ineffective in today’s environment.
OEMs can no longer begin the sourcing process as a new vehicle is being developed, nor can they simply focus on one particular model. Automakers are “partnering” with key suppliers well before vehicle development cycles to develop materials, components and systems that can be used across platforms from small sedans to large trucks and SUVs to optimize precious development resources and realize maximum economies of scale.
General Motors’ battery development strategy demonstrates its evolving approach to EV supply chain innovation. GM is working to accelerate battery technology advancement through its new battery cell development center while strengthening partnerships with suppliers. Battery plants are being created with strategic partners without the need to predict GM’s customers’ future model mix preferences precisely. Whether buyers trend toward sedans, trucks or SUVs in the future, each plant’s output can be configured to fulfill the demand. This strategy provides a natural hedge against inevitable changes in consumer preferences while creating economies of scale and reducing development time, cost and risk.
A Deeper Analysis
At the same time that major Tier-1 EV suppliers are increasing in stature, OEMs are moving strategically downstream, partnering with companies deep into battery supply chains to secure much-needed materials and move them efficiently to battery plants and other processors. Critical materials and components at Tier-2, 3 and 4 levels are being secured directly by OEMs to ensure they have adequate volumes of scarce materials and the best available technologies to improve battery and, ultimately, EV performance.
This year, Honda announced a major initiative in Canada that clearly shows this concept at work. Interestingly, Honda did not simply announce a new “battery plant” or an “EV assembly plant.” Instead, the press release outlined “plans to build a comprehensive EV value chain in Canada… including investment by joint venture partners, to strengthen its EV supply system and capability… from the procurement of raw materials…” This is a vivid departure from traditional automotive procurement strategies as Honda is thinking beyond their own walls and even the walls of their Tier-1 suppliers. They are partnering with strategically selected suppliers like Asahi Kasei (battery separators), POSCO (cathode materials) and GS Yuasa (battery technology) to build a total supply chain infrastructure that will ensure a continuous supply of the types of materials and technologies Honda will need to compete in the EV market of the future.
In a similar move, Volkswagen’s vertical integration strategy for battery supply chains reached a new milestone through PowerCo, its dedicated battery company. Beyond direct investment in battery production and material sourcing, PowerCo’s licensing agreement with QuantumScape for solid-state battery technology manufacturing rights demonstrates how OEMs evolve from traditional buyer-supplier relationships to deep technological partnerships. This collaboration, combining Volkswagen’s manufacturing expertise with QuantumScape’s next-generation battery technology, exemplifies the automotive industry’s shift toward integrated technology development and production optimization.
We also see Ford and SK Innovations teaming up to establish their “Blue Oval City” concept in Kentucky and other locations, creating electrification “hubs” with significant portions of the EV supply chain being co-located within close proximity. Once completed, this hub approach will significantly reduce lead times, inventory levels and logistics costs while further shortening the quality feedback loop with suppliers.
The Road Ahead
Although the automotive example may be severe, many industries face similar challenges, from solid competition, supply chain disruptions, resource scarcity and rapidly changing technologies. The good news is that companies from all industries can find elements of the automotive journey that support their efforts to fend off competition and become among the best.
The first step is to deeply understand the innovative supply chain practices currently used in the automotive industry and to match them up with their own industries’ specific challenges. The varied details of each industry’s situation should not deter the application of some of the fundamental principles that have been tried and proven in a highly competitive arena.
Automotive supply chains will continue to evolve with further advancements in electrification, autonomous vehicles, ridesharing, fuel cell powertrains and beyond. Leading companies in this space will no doubt continue to innovate their supply chain strategies and practices to ensure they remain competitive on a global basis.
Wherever an industry or company are on this journey, understanding the latest automotive procurement and supply chain practices and considering how they may be applied in their environment can help companies create a sustainable competitive
advantage. T&ID