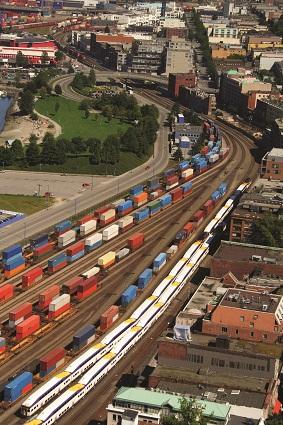
The logistics and distribution business sector is alive with robust activity, which is expected to continue into 2013 and beyond for a variety of reasons, one of which relates to trends within supply chain management (SCM).
Supply chain management, in the most simplistic definition, is the art in management of providing the right product at the right time to the right place at the right cost to the customer. Just about every product that reaches an end user represents the cumulative effort of multiple organizations. These organizations are referred to as the supply chain.
Supply chain management plays a critical role in our society as SCM knowledge and capabilities can be used to support medical missions, conduct disaster-relief operations and handle other types of emergencies. SCM has also assumed a more important role as consumers have raised their expectations for having access to a wide array of products. From a business perspective, SCM is essential to company success, particularly as it relates to customer satisfaction, the reduction of operating costs and improvement of a company’s financial position.
The origins of SCM date back to the 20th Century with the development of the assembly line, a time referred to as SCM’s “Creation Era.” Although the concept has been around for a long time, the term was actually first used around 1982 by Keith Oliver, an executive with strategy and technology consulting firm Booz, Allen and Hamilton.
Following the “Creation Era” came the “Integration Era,” which included the development of Enterprise Resource Planning (ERP), allowing for “value-added” service and cost savings through integration. Improvements continued and expanded, as did geographic boundaries leading to the “Globalization Era.” This era is characterized by the attention given to global systems of supplier networks and relationships in addition to expansion of supply chains beyond national boundaries and into other continents.
Fast forward to the “Specialization Era” during which industries began to focus more on core competencies, causing many companies to abandon vertical integration within their own organizations and sell off non-core operations. Distribution functions were outsourced to include extended supply chains, which required companies to become much more strategic about managing operations outside of their own four walls.
As outsourcing of distribution functions became more prevalent, a growing trend emerged with the provision of SCM as a service. Momentum mounted in this service sector during the 1980s with the inception of transportation brokerages, warehouse management and non-asset-based carriers. Today this service sector has expanded even further to include supply planning, collaboration, execution and performance management.
What can be anticipated in the future? More service with an extreme emphasis on cost savings opportunities and customer relationships. The most recent term coined is “SCM 2.0,” which is used to describe changes within the supply chain industry and the evolution of processes, methods and tools that manage it in this emerging “era.”
Given the evolution of supply chain management and the knowledge that continuing improvements will be made to drive results, global and domestic companies are re-evaluating what they look for in real estate site location decisions driven by supply chain strategies.
From the global perspective, traditional supply chain strategies have included cost reduction approaches, risk minimization and geographic balance. While these factors remain as top priorities, other influencing factors are being more strongly considered, such as escalating transportation costs and a desire to locate in closer proximity to the customer.
Operating in closer proximity to the customer has led to the growing trend of “nearshoring” or locating facilities in lower-cost countries closer to home. For companies in the United States this could mean Mexico, Costa Rica and Brazil as compared to more distant locations such as China, India or Vietnam. In addition to being in closer proximity to their customer base, “nearshoring” may offer U.S. businesses further advantages such as lower travel, labor, raw material and real estate costs.
Site location decisions within the United States vary depending upon the industry sector. All decisions have crossover in terms of base criteria, but individual factors are ranked in a different order of priority.
As an example, manufacturing firms may not be as reliant on local demand for goods and therefore might have more flexibility with respect to geography of their location decisions. Their location decisions depend more on local factors such as the quality and availability of workforces, access to innovative technologies and labor costs whereas the logistics and distribution site selection decisions are highly focused on:
1) Availability of real estate
2) Labor costs/availability
3) Inbound/outbound transportation infrastructure strength
4) Tax policy
5) Electricity costs/reliability and;
6) Economic development incentives.
Availability of real estate obviously influences location decisions, particularly as vacancy rates are decreasing and empty warehouse space fills up. Current vacancy rates in many markets are back in the single digits and capacities have improved substantially.
Outsourcing to third-party logistics (3PL) providers, as noted earlier, is a continuing trend. According to Modern Magazine, the top 20 3PL operators increased in total square footage from 514 million square feet to 543 square feet from 2010 to 2011, representing a 5.6 percent increase in occupied square footage and a corresponding decrease in the availability of existing quality warehouse facilities.
The scarcity of available real estate will require companies to allow for longer lead times in the site selection process if construction of a new facility is necessary due to a lack of available warehouse product.
Labor costs and availability are critical in every sector when it comes to the site selection and decision-making process because likely no factor matters more to a business than the quality and availability of its labor.
The combination of employee wages and benefits generally represents the largest single cost of doing business. This circumstance has become even more pronounced in today’s labor market as non-wage costs become a larger part of a business’ overall costs. These labor expenses are affected by local and state public policy as well as worker demographics in addition to healthcare considerations, and industry and firm performance.
Since produced goods have a high degree of value dependent on each individual worker at each stage in the production line or distribution process, access to a consistently high-quality workforce is critical to a company’s overall success.
Inbound/outbound transportation infrastructure strength will have a great impact on site selection. The movement of goods is central to the production of goods. Without a healthy logistics industry, manufacturing and commodity production will not thrive. Logistics is not only made up of the movement of goods, but also their effective storage and distribution.
Logistics firms have many of the same considerations as manufacturing firms in their location decisions. However, in some respects logistics firms are even more dependent on the existing or planned transportation networks of roads, railroads, waterways and airports.
A 2012 CNBC report on “America’s Top 10 States for Doing Business,” measured by the value of goods shipped by air, land and water; availability of air travel; and quality of roads -- indicated the following states within the Top 10 category of Infrastructure and Transportation:
1. Texas
2. Minnesota
3. Georgia
4. Tennessee
5. Nevada
6. Wisconsin
7. Kansas
8. Utah
9. Arizona
10. Ohio.
While these states ranked in the Top 10 because of their inherent strengths from an infrastructure perspective, these rankings will be comparatively analyzed with the other elements that make up a successful site selection.
Tax policy can be a deal breaker. Few issues garner as much policy interest and debate as do state and local taxes. For firms that can operate virtually anywhere, tax rates matter a great deal in the location decision. Business taxes, individual income taxes, sales, unemployment, insurance and property taxes all play a role in selecting an optimal location.
The financial health of the community and state has become an increasingly important consideration as companies prefer to avoid locating in communities or states that have large deficits or unfunded liabilities since these circumstances could lead to future tax increases or reductions in vital services, both of which could negatively impact businesses or citizens.
Electricity costs and reliability are vital considerations. Warehouses in the U.S. use an average of 7.6 kWh of electricity annually. Therefore, the availability of low-cost and reliable electricity is another top priority in the location analysis of warehouse and distribution centers.
Regions positioned to offer the best electricity rates are not only aggressively selling their advantages, but are also prevailing when electricity costs and reliability rank highly in the decision criteria.
Kentucky fares very well in this category as the state’s utility rates are generally 25 percent less than the national average according to the Kentucky Department of Business Development.
Other states such as Missouri and Illinois are competitive as well, with rates running about 18 percent below the national average according to Ameren Corporation and validated by Edison Electric Institute.
A common circumstance observed in regions where utilities are at their most efficient and economical is that mutually beneficial partnerships have been formed between local government and the utilities.
Economic development incentives continue to be of interest to the logistics distribution sector as they are extraordinarily helpful in offsetting short- and long-term project and operating costs.
Some recent examples of effective incentive tools that states and communities have utilized to attract and retain the logistics/distribution sector include:
• Sales tax recapture agreements: Through a restructure of business operations, a company can source all sales through one location versus multiple locations. As an inducement for the company to change its business operations, an agreement may be structured in which the company and community share in the percentage increase over the original base sales tax collections for an agreed-upon period.
• Personal and/or real property tax reductions: In exchange for creating jobs and making capital investment, the company may receive a partial exemption/abatement/reduction of property tax liability over an agreed-upon time.
• Forgivable loans: In exchange for a certain level of job creation and capital investment, a community may provide an up-front “loan” for building improvements and/or purchase of machinery and equipment. As the job and investment commitments are met, the loan is “forgiven” over some period of time, often in annual increments.
• Tax increment financing: This is an exceptional tool whereby incremental increases in assessed value are captured and utilized for land acquisition, building purchase, facility improvements and/or needed infrastructure to support a project.
• Training assistance: Many federal, state and local programs are available to help companies offset training costs associated with new and incumbent workforces. As a general rule, the primary objective of training assistance programs is to provide transferrable skills that will aid the employee in developing lifelong skills needed in the workplace.
• Tax credits: Credits to offset a variety of business taxes may be offered in support of a business’ commitment to make capital investment and create jobs over a specified period. The reduction of tax liability can be very meaningful to companies as they make investments in growth. Some tax credits may be refundable, meaning that if the value of the credit exceeds the amount of tax liability, the difference is refunded to the company in the form of cash.
Within the logistics and distribution sector there are many changes occurring. Perhaps most impactful are those within the field of supply chain management. One such change not discussed, but equally important given its impact in the industry, is the qualifications employers now require of their supply chain managers. Previously, managers may have had varied backgrounds in a wide variety of fields with a substantial variation in levels of experience. Today, many managers are educated and degreed in the field of supply chain management. This is a primary reason many colleges and universities have developed curriculum specifically geared to effectively train the next generation of workers within this dynamic and critically important industry.