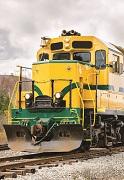
When it comes to moving goods around the country, trucks handle the vast majority of that transportation burden. This is true in the U.S. as well as in Asia or Europe. Trucks are the primary go-to shipping method for most companies. The question for corporate shippers today is…. “What if trucks are unavailable?” This might sound extreme, but is a real concern.
Outside of a truck, what other option does a company have to move goods? Air freight? No, too costly for most. Barge? No, not practical within the continental U.S. The only viable alternative to truck is rail, or intermodal — a combination of both rail and truck.
Intermodal has been the fastest -growing transportation mode for the past nine years running. Ten years ago, few companies thought of rail (or intermodal) as a practical way of moving their goods. Today, that mindset is changing. Growth has been substantial: U.S. rail intermodal volume was 3.1 million containers and trailers in 1980 and 12.8 million units in 2013. This represents a CAGR of 9.5 percent over the past 33 years.
So what has changed? Why the big fuss about rail? Here’s the rundown:
1. Freight costs are on the rise. No question about it. This creates a need for corporate supply chain professionals to look for cheaper, alternative modes of transportation.
a. Railroads are, on average, four times more fuel efficient than trucks.
b. Unlike truck trailers, containers can be “double-stacked.” This two-in-one approach lowers costs and also enhances productivity — containers can easily be transferred to and from ships and trucks.
2. Trucking capacity will likely tighten. The trucking industry is being impacted by a variety of issues that will continue to drive costs up and create tighter capacity, including federal regulations such as ‘hours of service’ that limit the number of hours a driver can be on the road, higher operating costs driven by insurance rates, fuel prices and increasing driver wages. To compound matters, a driver shortfall appears to be on the horizon as many are nearing retirement and the next-gen is pursuing other careers. A greater reliance on rail intermodal means truck driver shortages are less of a problem.
4. Risk mitigation is a notable priority. Given recent natural disasters such as the tsunami in Japan and flooding in Thailand, corporate boards are asking about risk management and there is too much risk to having all your transportation ‘eggs in one basket.’
Based on these facts, it appears rail and intermodal transportation will continue to grow in importance as a way to offset the operational challenges noted previously.
This ‘what is old is new’ phenomenon will be due to the closely coordinated efforts of the trucking companies themselves, shippers, the railroads and industrial real estate developers and their corporate occupier clients as they focus attention and investment capital on inland ports. It’s all about the ongoing battle to drive costs out of the supply chain while at the same time delivering goods more quickly. Having a robust and flexible infrastructure is crucial. Just as the nation’s busiest cargo seaports are investing billions to enhance their operational efficiencies, the continent’s leading rail operators are as well: Rail lines are the barbells linking international cargo gateways to our domestic population centers.
The Evolving World of Intermodal and ‘Inland Ports’
JLL has identified almost 200 intermodal facilities in North America that are controlled by the Class I railroads including the Burlington Northern Santa Fe (BNSF), CSX, Kansas City Southern (KCS), Norfolk Southern (NS), Union Pacific (UP), Canadian National (CN) and Canadian Pacific (CP) as shown in Exhibit 1.
Some of the facilities date from the earliest days of the railroads and are now located within the urban heart of original railroad cities that today are some of the country’s largest metro areas, including Atlanta, Chicago, Kansas City, Los Angeles and Memphis. The roads and other infrastructure systems serving these facilities long ago reached capacity. The real estate that was built 20 or more years ago to serve the companies that utilized these facilities has become functionally obsolete and no longer meets the needs of high throughput operations — much less hyper-kinetic e-commerce operations. But new development is playing catch-up.
The Renaissance
The first fully integrated modern inland port/intermodal facility where the railroad and real estate developer worked together as partners was Alliance Texas which was started in 1993 and encompasses over 17,000 acres. The development features a BNSF intermodal facility as well as an airport geared to air cargo customers.
The next fully integrated project would come nine years later in Chicago by the BNSF at the Logistics Park Chicago encompassing a 435-acre intermodal facility along with an almost 2,000-acre industrial business park.
These developments have successfully brought together all of the players in the supply chain: railroads, real estate developers, trucking and transportation companies, 3PLs (third-party logistics) and corporate users. Even more impressive is the fact that together these two parks have precipitated the construction of over 40 million square feet of distribution, warehousing and manufacturing space. Put into perspective: This is on par with the size of the entire industrial real estate markets of some cities.
From 2000 through Q1 2014, 30 intermodal/inland port facilities have either opened or have been announced with more rumored to be in process. The pace and breadth of development of inland ports/intermodal facilities is even more impressive when considering that 19 of the 30 have occurred since 2008 and were ironically planned and/or developed during the depths of the Great Recession.
New intermodal facilities have the potential to bring with them the development of an estimated 172.3 million square feet of distribution, warehouse and other related logistics facilities specifically targeted to take advantage of their proximity to the rail and intermodal facilities. At an assumed construction cost of $50 per square foot for buildings alone, this represents an investment potential of $8.6 billion. Add in the costs for installation of business park infrastructure such as roadways, utilities and extension of rail lines and that number likely swells well beyond $10 billion.
Exhibit 2 identifies the new projects and the associated developable real estate. It is important to note that in most cases the railroads are not the ones constructing the real estate facilities associated with their intermodal/inland port facilities. Rather, it is a private real estate development group that has typically partnered with the railroad and other supply chain partners to plan and coordinate development strategies for the overall success of the project.
While the newer developments are spread across the country, there is a definite concentration of the newer developments taking place in the East, Southeast and Midwest. Highlights of some of the larger and more interesting projects are described below.
New/Planned Inland Port/Intermodal Projects
-
AZ – The Inland Port Arizona is a 1,637-acre project that will be served by the UP and targeting supply chain partners that need a cost-effective alternative to Los Angeles. The developers are still in the planning stages but the assemblage has the potential to accommodate over 15 million square feet of real estate.
-
FL – CSX opened its new Winter Haven Intermodal in April 2014. An estimated 8 million square feet can be developed in the areas adjacent to it.
-
IL – Two newer facilities in the Chicago area (both being adjacent to one another) join the existing and highly successful BNSF Logistics Park Chicago (LPC) that opened in 2002.
-
RidgePort Logistics Center is a 1,500-acre development that has the potential to construct almost 15 million square feet of space. Most interestingly, this park will feature refrigerated express rail service for produce and other perishables grown in Central California and railed to Chicago. Processed foods, grains and other perishables grown and produced in the Midwest will fill the back-haul to California. Transport of food via rail is the newest product to receive interest from those in the supply chain looking to take advantage of the economies that rail has to offer.
-
Joliet Intermodal Center (JIT) by the Union Pacific is immediately north of BNSF’s LPC and opened in 2011. It has the potential to construct 20 million square feet of space with over 3 million square feet already built since its opening.
-
-
KS – The BNSF Intermodal and Logistics Park KC opened in late 2013 and sits on the operator’s transcontinental line between Chicago and the Ports of Los Angeles and Long Beach. The Edgerton, Kansas, facility opened with annual capacity for 500,000 container lifts, which will be tripled upon build-out. The 1.5 million-lift capacity will attract 100 million square feet of new industrial development within a 350-mile radius of the inland port; 60 million of that will be constructed within the Kansas City area.
-
NC – The NS has partnered with the City of Charlotte, Charlotte Airport Authority and other municipal authorities to open one of the more innovative facilities from a land use perspective. The Charlotte Regional Intermodal Facility opened December 2013 with the intermodal rail yard portion interspersed with the runways of the Charlotte International Airport. Over 15 million square feet of space could be developed in conjunction with the intermodal facility and airport.
-
SC – Positioned between Charlotte and Atlanta, the NS-operated South Carolina Inland Port extends the Port of Charleston’s reach 212 miles inland. Operations began in October 2013 and several companies are using the terminal, including BMW, which is moving its South Carolina export operations into a 413,000 square-foot facility at the 220-acre inland port. BMW is using double-stack trains to transport about 70 percent of the 1,100 cars it makes daily at its Greer plant to the Charleston port. From there, the vehicles are shipped to 130 markets worldwide.
-
TN – Memphis, a long time railroad city, has been the recent focus of several railroads and their real estate partners.
-
The CN has recently expanded and enhanced its Memphis intermodal facility with plans for the adjoining 800-acre CN Memphis RidgePort Logistics Center capable of accommodating 6.0 million square feet of space.
-
The NS opened its Memphis-Rossville intermodal facility in 2012. Real estate developers control adjoining land that could translate into the construction of 15 million square feet.
-
-
TX – The Dallas area is home to the first holistically planned intermodal/inland port facility, AllianceTexas. With the advent of the much-talked-about reshoring of manufacturing operations to the U.S. and Mexico, it is anticipated that Dallas and Houston will be vital links in bringing those goods to the rest of the U.S. Two new developments in the state include:
-
KCS’ CenterPoint Intermodal Center in Houston, a 689-acre development capable of accommodating 7.5 million square feet.
-
UP’s Dalport, a 353-acre development in Dallas with a potential for approximately five million square feet of development.
-
Conclusion
Rail transportation has been around for 150 years now, but it has evolved from a mode of transportation limited to passengers and a limited number of companies with certain types of lower-value commodity products into a real part of the supply chain management equation for all companies.
Although supply chain management can be quite complex, the increasing interest and focus on rail and intermodal as well as related inland port projects is quite simple. When comparing rail/intermodal to trucking, the benefits include:
-
Lower-cost option
-
Only viable alternative to truck
-
More sustainable/less carbon emissions.
As companies continue to seek lower-cost solutions, mitigate risk and become more sustainable, the growth of rail and intermodal transportation as well as related inland port projects should be no real surprise!