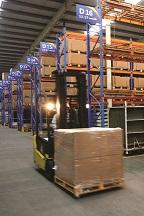
It should not come as a surprise that the logistics and supply chain management industry, because efficiency and eliminating waste is at its core, is one that not only tends to adopt and integrate sustainable concepts and practices more readily, but also one that often leads the way in developing new and more sustainable ways of doing business. Whereas many industries and businesses are highly invested in preserving their traditional ways of doing things, logistics providers are driven to always be operating more efficiently and providing better, faster and cheaper service. Accomplishing more, whether that means fulfilling orders, bundling shipments, processing returns or supplying materials to manufacturers, while at the same time expending fewer resources, is at the heart of any logistics provider’s purpose.
That is not to say that logistics providers are quick to accept any new product or process that touts itself as sustainable or green. Any process improvement must be verified by measurable gains. As will be shown below, many companies are doing just that when it comes to sustainability goals and the practices being implemented to reach those goals.
Ultimately, much of this focus on efficiency comes down to one primary factor, energy. Energy, in turn, translates to cost. The key byproducts of efficiency are 1) reduced costs and 2) reduced emissions and environmental effects associated with decreased energy consumption. Although reduction of emissions is not always the explicit or primary impetus behind driving down energy consumption, increasingly it is a factor being taken into account by suppliers and customers as their end users are becoming more mindful of where goods come from and how they were handled. Also, companies are beginning to realize the importance of sustainability over the long run at the expense of some short-run costs. And more so than maybe any other business, logistics providers and supply chain managers are looking to drive out waste and its cost.
Some of the largest participants in the industry are taking this to heart. Armstrong & Associates Global Top 25 3PL provider and supply chain management leader GENCO confirms this perspective in its online publication, “Supply Chain Perspectives” stating;
“Can green logistics practices protect the environment and drive more profit? The answer is an emphatic ‘yes.’
Surprisingly, the tools needed to achieve a more sustainable supply chain are the same as those used to drive operational efficiency. GENCO drives quality and continuous improvement through its Lean operating culture.
Lean is essentially a crusade against waste and inefficiency — too many steps, too much time, too much manual work. Well, what is green logistics other than a crusade against waste of another kind, such as unnecessary freight runs, excess packaging and inefficient lighting?
GENCO applies Lean principles in its work with customers on green logistics initiatives. The results have proven very positive not just for the environment, but for our customers’ bottom lines.”
Merriam Webster defines sustainable as an adjective meaning, “able to be used without being completely used up or destroyed: involving methods that do not completely use up or destroy natural resources: able to last or continue for a long time.” The EPA states the principle this way, “Sustainability creates and maintains the conditions under which humans and nature can exist in productive harmony, that permit fulfilling the social, economic and other requirements of present and future generations.”
This broad concept manifests itself in many different ways when applied specifically to the realm of logistics and supply chain management. Sustainable practices can be found in many aspects and activities within the industry. Some have long been practices of the industry solely for the sake of waste reduction and efficiency gains, as is the nature of the business, while others are increasingly being implemented explicitly with environmental impact and resource conservation in mind.
Modern Materials Handling recently surveyed a variety of industry experts to find out how the traditional warehouse and distribution center environment can and is being transformed by sustainable strategies that benefit the business, the customer and the planet. While there was a broad range of responses, a number of popular trends emerged from the conversation. Some focused on the physical aspects of the facilities themselves while others entailed changes in the way the businesses operate.
The primary factor on the list was simple, location. The greatest source of energy use associated with many logistics facilities is not the building itself but from the associated transportation services. Location can have a drastic impact on the transportation demands, fuel costs and resulting CO2 emissions among other environmental impacts. In times when fuel was cheap and the perception of climate change was not of the relative importance it is today, there may not have been such a critical eye placed on facility location and how it interacts with the transportation network. Today, many companies are performing detailed network modeling to determine the optimal location for logistics facilities with an eye to sustainability. For facilities concentrated on sourcing and production, the focus might mean being closer to inbound ports or sources of material inputs. For those focused on warehousing and order fulfillment, proximity to customers is the priority. The latest models now take into account the overall carbon footprint of a company’s supply chain, factoring in both distance between locations and the mix of transportation modes.
When it comes to the design of the actual building, lighting is identified as one of the most high-impact features with respect to sustainability. Lighting can account for as much as one third of the energy use in a distribution center. In increasing order of impact on energy consumption, the three most popular lighting sources being adopted by facilities managers looking to meet sustainability benchmarks are energy-efficient fluorescent fixtures, light emitting diode (LED) fixtures and natural light. Fluorescent and LED fixtures can reduce energy consumption from lighting as much as 80 percent and beyond that when supplemented with natural light or used in combination with occupancy sensors to ensure lights are on only as required.
Recycling may not be a new concept, but increasingly logistics providers are finding more creative ways to recycle, reuse and repurpose resources both in construction and operations. When it comes to facilities, it is difficult to be more sustainable than reusing or repurposing an existing building. With the market in many areas heavy with distressed or vacant properties, more companies are seeing the financial and environmental value in redevelopment rather than new construction. Many municipalities are also increasingly interested in finding ways to help companies be creative in redeveloping vacant and contaminated properties and are willing to provide financial support and other incentives to assist.
Operationally speaking, recycling has largely been incorporated into industry practices. In fact, in 2012, recovery of one of the most commonly used packaging materials, corrugated paper, reached an all-time high rate of 91percent, with most of that being recycled. With just 54 percent being recycled in 1993, corrugated and other paper-based packaging materials have led the way in setting the standard for packaging recovery and reuse.
The next frontier in sustainable packaging is in the growing use of returnable plastic containers (RPCs). RPCs are particularly well-suited alternatives for internal captive pools or standardized shared pools. They are especially gaining popularity in the packaging and transportation of fresh foods. A recent study by IFCO Systems, a global leader in RPCs for fresh products, found that RPCs generate 82 percent less solid waste, consume 92 percent less water and require 49 percent lower energy demand compared to display-ready corrugated packaging when shipping the same amount of a given mix of produce commodities. Franklin Associates, a consulting company focusing on product life cycle analysis, supports the findings of the study, noting that it “shows that the environmental benefits of IFCO RPCs are primarily due to the benefits of container reuse. While corrugated containers incorporate recovered fiber and are recycled at high rates, they must be manufactured and recycled for each produce shipment made in a single-trip container.”
While there are many ways to incorporate sustainability into warehousing and distribution facilities and throughout the supply chain, many industry managers and executives would echo that the first thing a business should do when defining its sustainability initiatives is consider what its goals are. Is the pursuit of sustainability solely for the purpose of reducing costs and increasing operational efficiency or is it to implement practices that are consistent with the values of the company and its customers?
The quest to drive out waste in search of improving the bottom line is a powerful driver that pushes logistics providers toward ever more efficient and increasingly sustainable practices, but other factors play a role in moving supply chains toward greater sustainability as well. Many companies are instituting sustainability initiatives and are expecting, and in some cases requiring, that participants farther and farther along their supply chain participate and meet certain standards and have similar sustainability goals. In its “2012 Supply Chain Report,” the Carbon Disclosure Project declared, “suppliers that do not measure, quantify and manage their greenhouse gas emissions will soon see their business move to competitors that can provide better information and clearer evidence of change.”
Automaker Subaru’s initiative to build all of its vehicles in zero landfill plants is an example of a business initiative that has far-reaching effects down the supply chain. To accomplish this goal, Subaru had to persuade shippers and suppliers to take back packaging materials and other items removed from parts during the assembly process and find ways to reuse them. Because everything that comes into the Subaru plant must be reused, recycled or converted to energy, suppliers are forced to come up with sustainable packaging solutions to keep that source of business. For example, Styrofoam inserts the company uses for protecting engine parts are able to be used for five trips from Japan and back before they have to be recycled. According to a report from USA Today, the company claims that effort alone has resulted in savings of $1.3 million a year.
Location also plays a significant role in Subaru’s supply chain and logistics sustainability strategy. Having suppliers nearby has many benefits that impact sustainability and the bottom line. At the company’s Lafayette, Indiana, assembly plant, seats are shipped from a company in Frankfort, Indiana, about a half hour drive away and dashboards come from Greencastle, Indiana, about an hour’s drive from the plant. Being strategic about these locations results in fuel cost savings, expedited delivery times and reduced CO2 emissions from transportation. The close proximity of those suppliers also helped Subaru make its case for having them take back waste and packing material for reuse.
While change, particularly when it comes to incorporating sustainable practices, can be slow and sometimes difficult for companies to implement fully into their supply chains, for those in the logistics and distribution industry those changes may not seem quite as drastic. If sustainability has not been a focus of a company’s business strategy to date, especially if it is in the logistics industry, it should be a goal worth considering as customers and suppliers are increasingly using sustainability as a point of delineation. If not already, businesses can expect activities such as quantifying and tracking carbon emissions and incorporating reusable packing materials and containers to become more and more pervasive across the industry. If these changes are not driven by internal forces, public demand for increasing transparency and disclosure of sustainable practices, especially efforts to reduce CO2 emissions, is likely to continue to push businesses in that direction for the foreseeable future. Being prepared to work with customers and partners to implement these initiatives and having the resources in place to meet these increasingly common demands will be crucial to remaining competitive. In an industry driven by waste reduction and improved efficiency, businesses can rest assured the concept of sustainability is not a fad, but is here to stay.