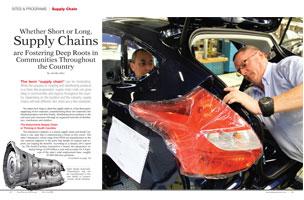
The term "supply chain" can be misleading. While the process of creating and distributing products is a chain-like progression, supply chain roots can grow deep in communities and regions throughout the country. Depending on the location and the industry, supply chains will look different. But, there are a few constants.
No matter how long or short the supply chain is, it has three parts: supplying of raw materials, manufacturing these raw materials into finished products and then finally, distributing these products to the end users and consumers through an organized network of distributors, warehouses and retailers.
The Automotive Supply Chain is Thriving in South Carolina
The automotive industry is a classic supply chain and South Carolina is one state that is experiencing a boom in this sector. The state's businesses, which range from OEM car manufacturers to the raw material suppliers to the ports that handle its imports and exports, are reaping the benefits. According to a January 2011 report by The South Carolina Automotive Council, the automotive industry brings in $29 billion a year and accounts for 5.4 percent of the state's total employment base, roughly 85,000 full-time positions.
![]() |
Eight Speed Automatic Transmission that will be manufactured in the new facility in Laurens County, South Carolina |
The automotive industry took hold in the state when tire-maker Michelin established its first U.S. production facility in South Carolina in 1973. It got another boost when BMW opened its first non-German manufacturing facility in Greer in 1993. The momentum continues today.
Last July, ZF Transmission, a German company, announced that they were building a nearly one million square foot facility in Laurens County near Greenville, which will be a $350M investment and create about 900 jobs.
Marvin Moss, executive director of the Laurens County Development Corp., said, "The state of South Carolina has been working on the automotive cluster for a number of years. Not only will the new ZF facility add a number of new jobs, but for every employee that ZF hires, it will contribute an additional three-to-four jobs in the state."
The plant will make fuel-efficient eight- and nine-speed automatic transmissions for Chrysler's passenger cars and light trucks.
According to Bryan Johnson, marketing and communications manager for ZF Group's North American operations, "We looked at 70 site locations and chose the area because of the total infrastructure - not just roads but supply base around there. Building a transmission is very detailed and you need a skilled workforce and knowledgeable suppliers." He added that proximity to customers, major transportation hubs, a competitive business environment and training through the state's ReadySC program were also factors.
ZF has another facility 15 miles away in Duncan, South Carolina, that supplies axle systems for BMW's Greer plant. In a 200-mile radius of those facilities, the company has another five locations, giving credence to the fact that automotive supply chain is indeed a cluster.
Dorchester County is another area in South Carolina benefitting from the automotive supply chain. Robert Bosch LLC, another leading automotive supplier, has been the county since 1974, producing equipment such as fuel injectors, anti-lock brake systems and electronic stability control systems. It recently announced that it will expand its operations there, investing about $125 million and adding approximately 300 jobs to the 1,500 it currently provides.
Jon Baggett, director of Dorchester County Economic Development, said that Bosch chose to stay in the area because of reliable infrastructure, a proven facility and a strong workforce.
Another automotive supplier success story in Dorchester County is Showa Denko Carbon, which provides granular graphite to the automotive industry, along with graphite electrodes to the steel industry. Located in the area for 24 years, it also recently announced a $200 million expansion that will add 100 new jobs.
"Because our business has been successful and we see growing demand for high quality graphite electrodes, we have decided to expand here, which will be good for our customers and the community," said Robert C. Whitten, president and CEO.
The automotive supply chain is bolstered by Clemson University's International Center for Automotive Research (CU-ICAR), an advanced-technology center where academia, industry and government organizations work together to expand the automotive industry's knowledge base.
![]() |
Safelite Autoglass opened up a new facility in Braselton, Georgia, in August 2010 |
Automotive Supply Chain in Southeast Extends Deep to Georgia
The Southeast's supply chain isn't limited to South Carolina. Jackson County, Georgia, is another place that's attracting automotive suppliers. One addition to the automotive industry there is Safelite Autoglass, a leading supplier of automotive safety glass, which just opened up a facility in Braselton in August 2010.
Shane Short, president and CEO of the Jackson County Area Chamber of Commerce, cited the area's centralized location in the South as a big draw, being situated on I-85 and only an hour from Atlanta.
According to AVP of manufacturing and distribution, Rich Glover, Safelite has an internal supply chain, manufacturing about 30 percent of its own products. To facilitate a three-day lead time, the company uses JIT (just-in-time) inventory operations and forecasting optimizer software. Not only does it manage 8000 SKUs and 87 locations, the company find its business driven by factors including weather, oil prices and even the school calendar.
"The more miles driven, the more windshields are broken. Our peak season is the summer when kids are out of school. And, weather conditions like hurricanes and tornadoes, which break windshields, impact our business. On the negative side, high gas prices mean that people drive less," said Glover.
Automotive Supply also Big Business in Moberly, Missouri
Belying a population of 14,000, Moberly, located in the central part of Missouri, has a thriving automotive supply chain. It began in the 1930s with a single company, Orscheln, that's still a Moberly mainstay today.
![]() |
Orscheln Products started the automotive supply chain in Moberly, Missouri, in the 1930s |
According to Corey Mehaffy, president of the four-county Moberly Area Economic Development Corporation, Moberly has a number of Tier 1 and Tier 2 automotive suppliers and a long history of manufacturing for the automotive industry. In addition to Orscheln, he named Dura Automotive, an Orscheln spinoff that makes brake parts as well as Mack Hils, a company that manufactures antique truck beds and supplies to automotive OEMs and the military. Others include Wilson Trailers, that makes flatbed trailers for semis, along with Performance Tools, a tool and die shop that supplies Orscheln and Dura Automotive.
Orscheln Products develops and supplies driver-control products such as parking brakes and fluid level indicators for the heavy truck, aviation, military, agricultural and recreation vehicle industries - for virtually all vehicles except for passenger cars and light trucks. Headquartered in Moberly, the company has locations in Europe, India and China, along with a network of more than 100 distributors worldwide.
President Bob Orscheln said that the company is vertically structured from a supply chain perspective, manufacturing about 80 percent of its products.
"We're low volume, but we have more than 10,000 active parts and about 800 customers, including Caterpillar and Volvo. While companies that supply cars might have orders of 500,000, if we get an order for 60,000 units in a year, that's a lot. In fact, some of our customers only order 50 units."
Because of this low volume, he finds it advantageous for the company to manufacture its own products and domestically source the rest. "We don't find any advantage to having an electronic board made in China and shipped back to us," he added.
Performance Tool is another Moberly company that is helping shorten the supply chain there.
"Orscheln could have their molds built anywhere, but by using a local company like us, they rely on the fact that we will respond very quickly. If they have an issue, we can even be over there in a few minutes, since we're only a mile away," said owner Greg Carney.
![]() |
Ethanol is part of Nebraska's agricultural supply chain. |
The state of Nebraska has built the ethanol industry literally from the ground up.
"Agriculture here has a well-developed supply chain," said Dennis Hall, economic development manager at Nebraska Public Power District, the state's largest utility and an economic development agency.
"We're the number two producer of ethanol in the U.S. We have abundant corn and cattle to eat the byproduct of ethanol manufacturing. It's a very efficient chain," added economist Ken Lemke, PhD, there.
Chief Ethanol Fuels, in Hastings, Nebraska, has been producing ethanol for 26 years. It now produces 72 million gallons per year.
Duane Kristenson, vice president and general manager, said that the location is ideal from a supply chain perspective, with an ample supply of corn from nearby farms and a strong rail system to ship the fuel out of state, typically to the West and Southwest. Though corn is plentiful in Nebraska and his company's inbound supply chain is short, worldwide issues are a concern.
"This year, corn prices have gone up because of factors like the drought in Russia and higher demand in China. When you talk grain, you're talking worldwide conditions."
Former Air Force Base in Roswell, New Mexico, Leads to Growth of Aerospace Support Industry
In Roswell, New Mexico, local officials turned what could have been a negative, the shuttered Walker Air Force Base, into the Roswell International Air Center - a thriving aerospace support sector. The location is ideal for companies interested in pilot training as well as those that maintain, refurbish, paint or disassemble planes.
![]() |
A&P program at Eastern New Mexico University in Roswell supports the aerospace industry there. |
"With our location, including long, wide runways, uncrowded airspace, a tower-controlled airport and weather that's warm year around, we're an idea location for these companies," said Bob Donnell, executive director of the Roswell-Chaves County Economic Development Corporation.
"The industry has really taken off and we now have eight aerospace companies," said Danny Armijo, regional director for New Mexico Manufacturing Extension Partnership.
One is Great Southwest Aviation located on site at the air center providing services such as fixed base operator (FBO) flight training and hanger storage.
"You have all the benefits of a larger airport like the Sunport and Dallas/Ft. Worth, without the congestion," said president and CEO Larry Jessen.
Another company drawn to the area is Dean Baldwin Painting, which repaints planes for a number of major companies including United, American Eagle, Boeing, UPS and DHL.
Jim Burress, general manager at Dean Baldwin Painting, discussed the impact the company has on the area. "Our payroll runs through the community up to 12 times," he said.
Also supporting this industry is the area's college, Eastern New Mexico-Roswell (ENMU), which offers an Airframe and Powerplant (A&P) training program, the industry term for mechanics.
"The past two-and-a-half years, the air industry in Roswell -- and all over the U.S. -- has exploded in terms of employment, because of an aging workforce," said ENMU president John R. Madden. "Our grads refer to their license as a ‘license to steal' because they can go anywhere and do just about anything with their A&P certification."
![]() |
J.H. Kelly - working on a nacelle in Longview, Washington |
Marriage of Heavy Industry, Deep Water Ports and a Business-friendly Environment Spurs Growth in Washington
In Longview, Washington, located in the southern-most part of the state, creative solutions abound for its entrenched manufacturing and industrial supply chain. In fact, the Port of Longview, a deep water port, worked to retain a large customer, the Indian wind turbine manufacturer, Suzlon. In the process, it matched Suzlon with local industrial mechanical general contractor J. H. Kelly, so J.H. Kelly could perform maintenance and aftermarket OEM work. Not only did the Port of Longview keep Suzlon's business, it helped J.H. Kelly flourish in a new market.
"Our work with Suzlon ballooned into more businesses both locally and out of state. And, it led to work with other wind manufacturers. We now do work with Mitsubishi and Gamesa, a wind OEM out of Spain. We're pleased with the port's communication and cooperation to meet their customers' needs and provide opportunities for companies like us," said vice president Rob Harris.
Ken O'Hollaren, executive director at the port, said that the port plays an important role in the area's manufacturing supply chain by creating jobs in manufacturing and international trade.
"We develop the infrastructure to support these jobs at our marine terminals and industrial property, creating a positive economic ripple that strengthens the local community," he said.
Bob Gregory, Longview city manager, agrees. He said, "Our area understands skilled labor, manufacturing and embraces industrial manufacturing. People who've built here will tell you that because of factors like easy permitting and excellent job training, it was easy to get up and running."
Biomedical Manufacturing Grows in Georgia
![]() |
The BioBusiness Center at University of Georgia in Athens helps spur growth in the area's biomedical industry. |
"We are what you'd consider an OEM and in the supply chain - it's just that our business is manufacturing purified human and animal proteins," said Jinx Patel, research director at Athens Research and Technology.
Athens Research and Technology's supply chain is long. It ships its highly specialized proteins to biomedical research facilities, hospitals and pharmaceutical companies all over the world.
The company is just one example of the biomedical field in Athens, Georgia, that began because of University of Georgia's strong biomedical research program there. The university's BioBusiness Center is helping fledgling biomedical companies grow.
"We're helping them understand what the potential supply chain will be as well as market opportunities," said BioBusiness Center director Margaret Wagner-Dahl. "Plus, we're trying to build critical mass and credibility in the industry, so there'll be enough talent, workforce capacity and investment capital to sustain it."
Matt Forshee, president and CEO of the Athens-Clarke Co. Economic Development Foundation, agreed with Patel. "We think of life sciences as only being pharmaceutical products, but there's a strong supply chain component and it's going on here."
Distribution-based Supply Chains are Thriving Throughout the Country
The distribution part of the supply chain is strong in areas of the country that are centrally located and feature excellent modes of transportation, whether it's by road, rail or water.
![]() |
Best Buy's distribution center in Ardmore, Oklahoma |
"They're here because of the proximity to their markets," said Brien Thorstenberg, vice president of development at Ardmore Development Authority. "We're exactly 97 miles to both Dallas and Oklahoma City on I-35. There's easy access to much of the Southwest and Great Plains."
Best Buy, with eight distribution centers throughout the country, uses strategic locations and savvy programs, such as flow through, to shorten the supply chain. Using flow through, Best Buy takes incoming products and ships them out of a distribution center the same day they come in, rather than putting them in a warehouse.
"We're also working with vendors to ship directly to stores and bypass distribution centers, whenever possible," said Brian Mast, director of operations at Best Buy. "This works well for items like air conditioners that are in high demand when there's a heat wave."
Mast also said that Best Buy chooses the location of its distribution centers based on access to major highways, proximity to transportation hubs, a strong workforce and an active, aggressive economic development agency.
The Northeastern Strategic Alliance, a nine-county region in northeast South Carolina, tells a similar story.
![]() |
Best Buy's distribution center in Ardmore, Oklahoma |
"There's no better point of entry to the east coast than in our area. We're close to the Ports of Charleston, Savannah, Wilmington and Georgetown. Companies can have everything shipped by road or rail and then sent on to distribution centers along the east coast," said Jeff McKay, executive director there.
QVC is one company taking advantage of the location, with a customer fulfillment center in Florence, South Carolina.
"QVC located here to position itself ideally for the future," said Robby Roberson, general manager at QVC's Florence customer fulfillment center.
"We're halfway between Miami and New York City," he continued. "This is important because at QVC, we don't produce anything. We buy from suppliers, move products into our supply chain and then distribute. QVC does a better job than most at getting products in time and shipping it before payment is due."
Supply Chain Issues are Changing the Way Companies Do Business
The earthquake and tsunami in Japan has had a devastating effect on the auto industry, due to disruptions in production of key suppliers there. It's causing companies in many industries to reconsider their reliance on just-in-time.
"People are very aware of supply chain effect. Every time there's a problem, it ripples to Tier 1 and OEMs," said Mohammed A. Omar, PhD. assistant professor of mechanical engineering at CU-ICAR.
![]() |
ZF Group: Axles being manufactured for BMW's JIT inventory system in Duncan, South Carolina |
Omar explained that reliance on JIT means that supplies in the supply chain network will arrive at the required time in the required quantities. Companies try to keep a very small buffer to stay lean and save money. With JIT, companies typically rely on two suppliers so one supplier can't drive cost and quality, as well as have a backup supplier in case of situations like this. But, because of patents and specialized technology in Japan, in some instances, there was only one supplier and not a redundant supply.
"Everyone is rethinking this style of supply chain because of events in Japan," he said.
Toyota Motor Corp, the world's largest automaker, told U.S. dealers that production disruptions triggered by the earthquake and tsunami may reduce vehicle supplies into the 3rd quarter of 2011.
"The potential exists that supply of new vehicles could be significantly impacted this summer," said Bob Carter, group vice president of U.S. sales.
Another issue that is facing some manufacturers is the increasing scarcity of raw materials.
Complex Chemical in Tallulah, Louisiana, produces functional fluids, such as motor oil and brake fluids, for auto maintenance. It does custom manufacturing for companies such as BP Castrol and Lubrizol, because those companies find it financially advantageous to outsource manufacturing rather than open up their own manufacturing plants, according to Complex Chemical president and owner Jerry Melton.
However, Melton said his business has found it increasing difficult time ensuring he has an adequate supply of raw materials which are typically derived from petrochemicals.
"It probably occupies 50 percent of my time, and I'm not the only one. It's not exclusive to this area," Melton said. "It's easier for me to make products and ship them out than it is to get the raw materials. We're outstripping our supplies in the world. There's going to have to be a shaking up about our attitudes."
On the production side, the company faced a catastrophe similar to what many Japanese suppliers recently faced when a category 4 hurricane virtually wiped out its facility and operations. The business survived - its customers maintained adequate inventory -- because of Complex Chemical's backup plan, where it partners with its competitors to serve as each other's backup production facilities.
"I've found that some of my best customers are my competitors," Melton added. "We're included their contingency plans and vice versa. They stepped in and made products for us while we were getting back in operation."
Supply Chains: An Area of Growth
Aside from the impact faced by challenges from issues such as like rising fuel and commodity prices and unforeseen disasters, supply chain companies share few generalities. Their supply chain programs differ by industry, region and company, because each business adapts to best serve its particular niche. One thing they all share, however, is that no matter where they are located, these businesses are thriving and have grown deep roots in their communities.
Related Agencies
- Laurens County Development Corporation
- Dorchester County Economic Development, SC
- Jackson County Area Chamber of Commerce
- Moberly Area Economic Development Corporation
- Nebraska Public Power District, Economic Development Department
- Roswell Economic Development
- Longview Economic Development
- Athens-Clarke County Economic Development Department
- Ardmore Development Authority
- North Eastern Strategic Alliance
- Northeast Louisiana Economic Alliance