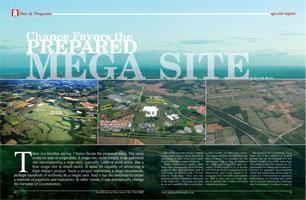
There is a familiar saying: Chance favors the prepared mind. The same could be said of mega sites. A mega site, most simply, is an industrial site encompassing a large area, typically 1,000 or more acres. But a true mega site is much more. It must be capable of attracting a high-impact project. Such a project represents a large investment, perhaps hundreds of millions, by a single user. And it has the potential to create a network of suppliers and customers. In other words, it can dramatically change the fortunes of a community.
But which mega sites manage to attract a high-impact project? Much depends on preparation. In other words, high-impact projects favor the prepared mega site.
When communities market their mega sites, and describe them as being prepared, they often use terms such as “job ready” or “shovel ready.” Or they refer to “ready sites.” These sites may possess an array of attributes important to the single user. (The single user may be an auto assembly plant, a steel plant, a chip foundry, or other large operation.) Some attributes are inherent in the site’s location. For example, the site may happen to be in close proximity to the single user’s suppliers and customers. It may happen to be in an area with well-developed transportation infrastructure. And it may happen to be in an area with favorable demographics. That is, there may be a large supply of qualified labor within convenient commuting distance.
But location isn’t everything. For a mega site to be competitive, it must promise that any development on it will proceed quickly. As a result, many mega sites undergo elaborate preparation. Infrastructure for transportation and utilities may be upgraded. Environmental studies and engineering surveys may be conducted. Commitments to guarantee quick transfer of ownership and control may be secured. And incentive packages may be structured.
All this activity, all this due diligence, is expensive and time consuming. And it requires a fair degree of coordination and in-depth knowledge of local procedures and regulations. In some cases, site preparation is an ad hoc process. For example, the owner or a piece of property may consider it a special circumstance or one-off project. Or interested parties may happen to have good internal processes, however informal.
The preparation of mega sites, however, may be more systematic, more formalized. In fact, there is a trend toward the certification of mega sites. The certification of sites is hardly new. Smaller sites, for instance, are often certified. Nevertheless, the certification of mega sites is fairly new.
THE TVA CERTIFICATION PROGRAM
In March 2004, the Tennessee Valley Authority (TVA) launched a program to identify and certify mega sites. This program was designed to address the needs of potential automotive manufacturing or assembly plants.
TVA elected to use the expertise of a site selection consultant to establish certification criteria and develop a process to evaluate mega sites across the Tennessee Valley. TVA issued a request for information to more than 200 consultants and negotiated with the top13 consultants capable of providing site evaluation services. Ultimately, McCallum Sweeney Consulting (MSC) of Greenville, South Carolina, was chosen to serve as the consultant on the mega site certification project.
County, city and regional economic development organizations within TVA’s service territory submit potential industrial sites for consideration. To date, eight mega sites have been certified by the TVA and MSC. And two of these eight sites have been sold. The first TVA/MSC-certified mega site to be sold was the Golden Triangle Megasite in Columbus, Mississippi. (It was purchased by SeverCorr, a steel manufacturer, in October 2005.) And the second to be sold was the PUL Alliance-Wellspring Project in Tupelo, Mississippi. (It was purchased by Toyota in February 2007.) The six TVA/MSC-certified mega sites that remain are listed in Table 1, along with a selection of other mega sites.
OTHER INITIATIVES
Although the TVA/MSC program has drawn attention to a select few mega sites, it isn’t difficult to find others. And some of these additional mega sites have also been certified. However, it should be noted that there is no national standards body.
Some mega sites have been reviewed or certified by consultants, such as KPMG. And some utilities besides the TVA utilities have economic development divisions that identify and market mega sites. For example, Duke Energy has publicized the L&C Megasite in South Carolina. (For more information, see www.considerthecarolinas.com.)
Some mega sites have been certified, or will soon be certified, by state agencies. For example, Oklahoma and Ohio have launched certification programs. To date, most of the certified properties are smaller sites. However, guidelines appropriate for large sites have been defined.
The Oklahoma Department of Commerce, in partnership with PSO and OG&E, launched Site Ready, Oklahoma’s site certification program for new investment and retention of expanding industry in the State of Oklahoma. According to the Oklahoma Department of Commerce, the purpose of Site Ready is to proactively serve the needs of businesses by developing an inventory of sites that are certified for immediate investment and development.
A secondary objective of Site Ready is to prepare Oklahoma communities to accommodate new business prospect inquiries. By going through the application process, communities will have the opportunity to learn what the relevant needs for various projects are and how to strategically plan to address those needs.
Oklahoma’s Site Ready program has devised guidelines for eight project types. There are guidelines for aerospace parks, heavy industrial parks, light industrial parks, warehouse/distribution parks, business services parks, research and development parks, rural business/commerce parks, and (last but not least) mega parks.
The guidelines were created with the help of an independent, third-party consultant. They include generic site profiles, project profiles, and project “musts and wants.”
In Ohio, certification standards have been devised for mega manufacturing site improvement projects. These standards encompass site size and configuration, utility minimums (water, sewer, electric, gas, and telecommunications), transportation access (highway, rail, and air), and zoning issues.
TYPICAL STANDARDS
Because several entities are promulgating standards, some differences are bound to arise. Nonetheless, there is a fair degree of commonality. Typically, standards are most alike in the physical requirements for a site. These include overall size and the number of contiguous, developable acres. They also encompass proximity to transportation resources, access to utilities, and favorable demographics (access to a trainable workforce). More complex issues involving administrative details may show a little more variance. For example, if environmental issues are uncovered during a Phase I review, a Phase II audit may be required. In addition, recommended remediation may need to be completed. In any event, the more comprehensive the requirements—and the greater the degree to which the requirements are satisfied—the greater the assurance the site will accommodate rapid development and an early construction date.
A typical breakdown is as follows:
Site must be a minimum of 1,000 acres with 700-800 contiguous, developable acres.
Site must be accessible, with zoning, right-of-way, and easement issues clarified.
Site must be available for sale, with clear title demonstrated. (In addition, ownership of contiguous parcels must be determined and options must be secured.)
Site must be located outside the 500-year flood plain.
Site should be located within an attainment area. (If not, tradable air emission credits must be available.)
Site must be served by rail. (Preference for Class I railroad and two-rail carrier choices.)
Site must be within 3–5 miles, via truck route, of an interstate, or on a limited access, four-lane divided highway. (Interstate frontage preferred.)
Site must have a Phase I environmental audit. (And Phase II actions should be clarified.)
Site must have adequate access to utilities. If there is any deficiency, plans (including schedules and costs) should be in place.
Site must have geotechnical and soil assessments completed. And wetlands and protected species should be identified. If any mitigation is required, plans should be clarified.)
Site must have plans for expedited permitting in place.
Site must be located within a 25–30 miles of at least 50,000 people
Additional preparations could include the securing of long-term options, the completion of utility and infrastructure upgrades, and the completion of a construction pad.
FURTHER TRENDS
The trend toward more demanding, more formalized certification standards for mega sites was originally a response to a more fundamental trend—the migration of auto assembly operations to the southeastern United States. It appears both of these trends are likely to continue.
Just two weeks after Toyota announced it had settled on the PUL Alliance-Wellspring Project’s mega site, state legislators in Tennessee met to discuss why a Tennessee mega site contender hadn’t been chosen. The legislators decided that Tennessee communities needed to enhance their ability to pool the resources necessary to develop a mega site. The legislators are making plans to create regional mega site authorities.
There is also speculation that the migration of auto assembly operations may lead to a “filling in” between the Midwest (where domestic manufacturers dominate) and the Southeast (where foreign-owned manufacturing operations, or “transplants,” dominate). In one presentation, by a Federal Reserve analyst, it was interesting to see that the “finalist” sites considered by Toyota were in an east-west band stretching across the northern reaches of the south.
It is also possible that location trends for auto assemblers may instigate location trends for auto suppliers. For those suppliers capable of supplying both domestic and transplant manufacturers, intermediate locations may be preferred. (In general, suppliers prefer to be located within a day’s drive of an assembler. Otherwise, maintaining “just in time” schedules could be difficult.) Accordingly, locations that may not offer mega sites may be affected by the mega site trend. For example, in hilly West Virginia, there are few large, flat sites, but there are many suppliers. These suppliers include Nippon Thermostat, Diamond Electric, NGK Spark Plugs, Allevard Springs, Capre West, and K.S. and A.K. of West Virginia. Suppliers in West Virginia and other intermediate locations are positioned to serve assemblers based in mega sites in both the North and the South.