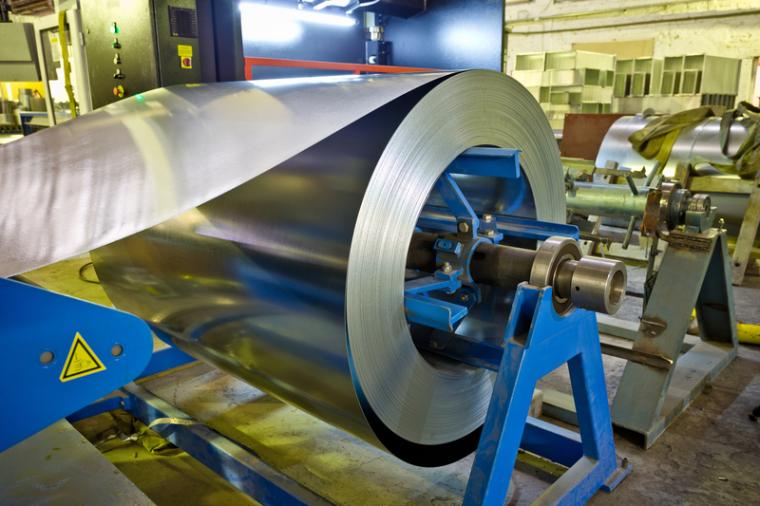
For traditional manufacturing projects, the timing of siting a new facility is a fairly rapid process, normally occurring approximately one year from project identification to final decision. The forces driving the decision primarily are born from actions to meet rising demand, expanding into new markets or to reduce overall distribution costs. For these rapidly moving projects, companies tend to limit their search to identify areas whose attributes include a close proximity to raw material suppliers, an existing building or pad-ready site, and an adequate labor market that can be utilized to the corporation’s advantage.
With advanced manufacturing organizations, the essence of their operating model is to capitalize on the explosive growth curve of new technology, creating disruptive change. This change could be for existing companies in their particular industry, or in some cases, creating entirely new industries. Their technological breakthroughs have taken many forms. Innovation can stem from areas such as the fabrication of new materials, for instance composites and ceramics, additive manufacturing via 3D printing, robotics, micro-manufacturing and clean room production. These are only a few of the descriptors for what many people now define as “advanced manufacturing.”
There are both similarities and differences between traditional and advanced manufacturing. They are similar in areas such as the use of transportation modes (road, rail, water or air) to move raw materials and finished product. They both utilize a functional organizational structure combining both production direct and support personnel to make up their workforce. Ultimately, they all have overarching goals of safety, quality and productivity to increase profitability.
For advanced manufacturers, and from a site selection perspective, the two attributes that are fundamentally different are that they are highly engineered operations born out of extensive R&D and, since a first of its kind of facility has to be built and proven, their implementation timeline can be significantly longer. These two fundamental differences have distinct implications on how these projects should be approached from an economic development perspective—the first requires simple, short-term integration into an existing region’s supply chain, while the advanced manufacturing project requires creation of an overall environment designed to allow the local existing supply chain to optimize itself.
A particular company’s supply chain is a fulfillment process of receiving raw materials into the facility, processing those materials by adding value and finally shipping finished product to the customer. However, once you combine all of the manufacturers in a particular region, the aggregation of those supply chains (and the organizations that primarily support those companies) is the manufacturing cluster. In addition to the physical companies, there are dynamics that can take many forms, via programs and activities that are created to support growth for the overall manufacturing environment. For advanced manufacturers, coupled with existing companies, this dynamic, living environment can be characterized as the region’s “meta-chain.”
In other words, for any given region, traditional manufacturers’ supply chains are co-existing while concurrently cooperating and competing with each other. Advanced manufacturers, due to their nature of explosive technological growth, will add complexity, therefore requiring advanced supply chain initiatives in areas that can be perceived with more distinct differences than a traditional manufacturing plant. It’s the “everything else” outside of the four walls of the facility and their suppliers’ facilities that needs to be enhanced.
From a timing perspective, economic development initiatives at the project level can help improve a company’s supply chain within the specific timeframe from project announcement to full production (roughly two to five years), whereas meta-chain initiatives may take significantly longer to implement, therefore transcending political administrations at both the regional and state levels.
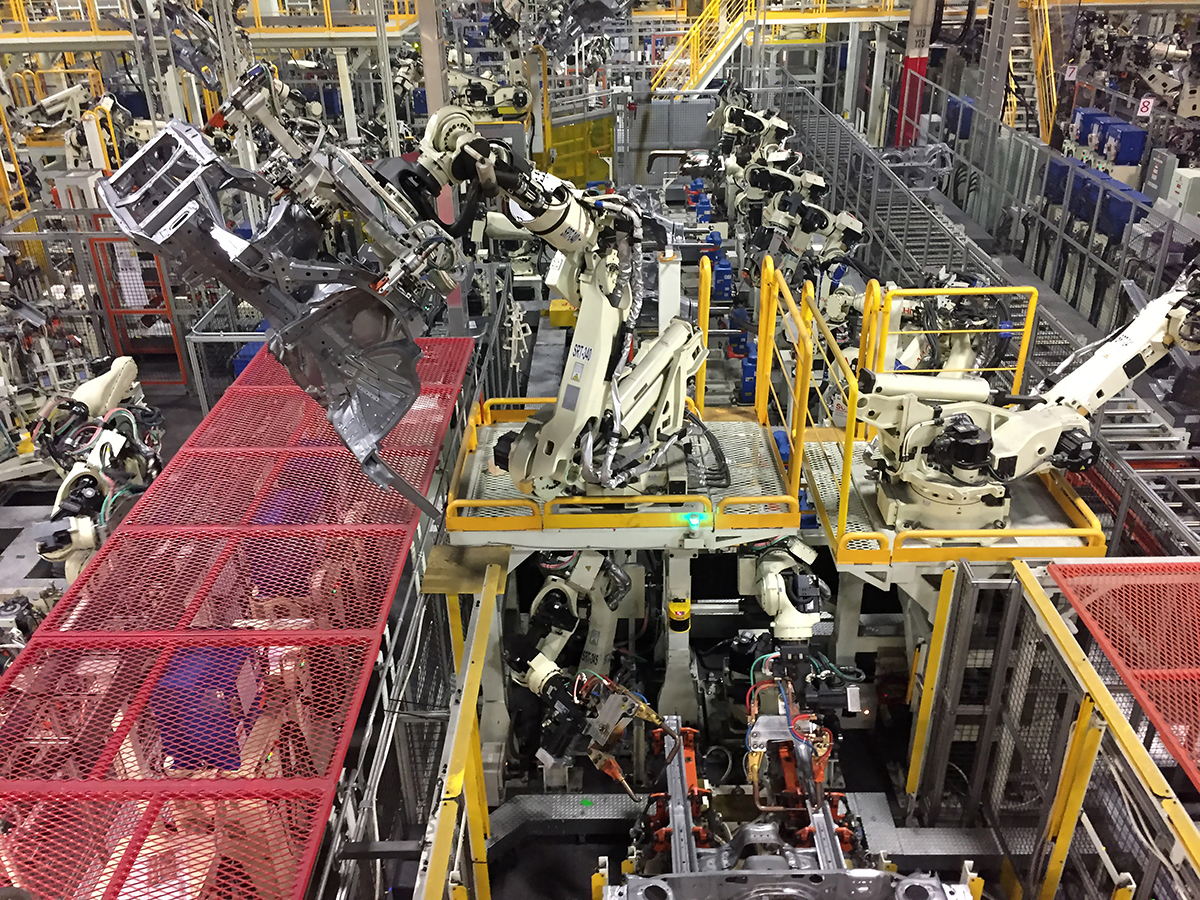
Quantitative Cost Analysis and Qualitative Considerations
A traditional manufacturing siting decision is primarily a function of a quantitative analysis of start-up and ongoing operational costs. The cost analysis performed is not for all costs, but for significant variables that will fluctuate by site. These costs primarily include labor (including payroll taxes and benefits), real estate costs, utilities and communications costs plus local property, sales, state income and franchise taxes. Depending on the significance, a transportation cost analysis per site may be performed and included in the overall model.
Normally these analyses are estimated over a 20-year period. This analysis allows the team to identify the impact of overall costs while incentives are being utilized, and also for some period of time when those incentives expire. Once these nominal costs are calculated, they are then discounted via a net present value calculation using a discount rate that is at or near the project’s weighted average cost of capital (WACC).
While the result of this quantitative analysis indicates the “winner” from a cost perspective, it is only prudent for the project team for advanced manufacturing projects to provide some level of qualitative analysis for potential changes (some foreseen and some unforeseen) that can and may occur over the lifetime of the project. Qualitative considerations are given for items such as quality of life, political stability, local economic health and educational system performance, among others.
The only constant in life is change, and over a 20-year lifetime of a project, the overall manufacturing environment will also change. It can be for better or for worse, or only have nominal significance. It is up to the project team to analyze those factors and include that in a risk analysis to see how that will impact the final decision.
An advanced manufacturing siting decision does not have to have a singular focus on finding the location with the lowest cost. But it can be to find a location that may be close to the lowest cost location, while having an overall environment that will allow the company to grow and prosper over time.
The qualitative analysis can occur at any time. For some projects, it can serve as the initial filter to qualify sites for consideration. This is especially true for advanced manufacturing projects where the technology is so new the supply chain will have to be developed concurrently with project start-up. For others, it occurs once short-listed sites are stratified via cost, and the cost differences between the top three sites are very close, such as a few percentage points (as compared to total costs) over the 20-year timeframe. For most projects, however, the qualitative analysis constantly occurs as positive and negative attributes of a region are identified during due diligence.
Characteristics of a Healthy Meta-Chain for Advanced Manufacturers
For all site selection projects, the four primary considerations in choosing a site are:
1) The availability of sites and buildings,
2) Workforce quality and availability,
3) Ongoing costs (including tax and incentive implications), and
4) The overall quality of life and risk characteristics of the region.
For an advanced manufacturing project, the overall considerations also include these four areas. But what is different is the emphasis on certain areas within these primary considerations.
Here are a few areas that economic development agencies should consider when positioning their region for advanced manufacturers.
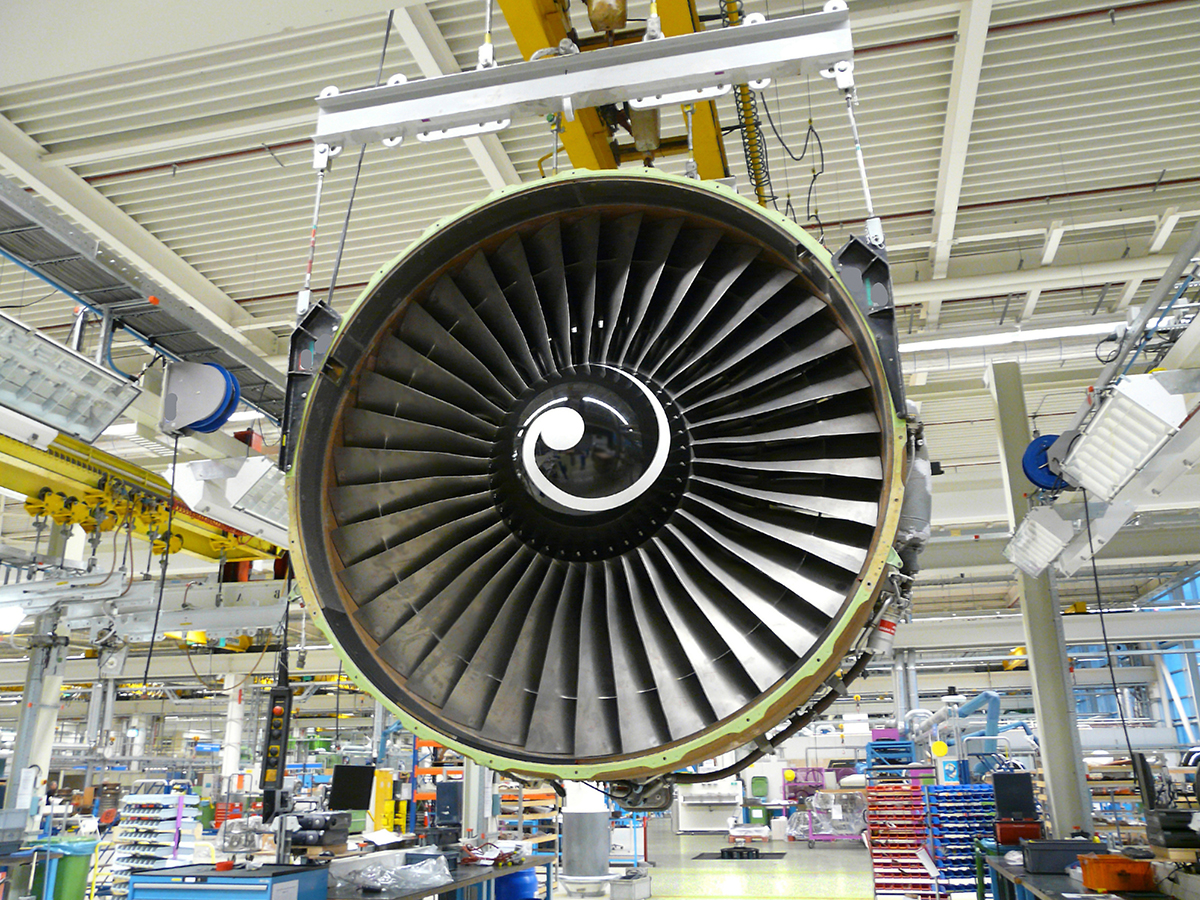
• Sites and Buildings
In recent years, there has been significant effort to certify sites, but not buildings, for economic development purposes. This effort is effective in shortening the timeline for plant start-up. However, a building designed for advanced manufacturing normally requires construction to higher standards than is seen for spec buildings. Keep in mind, too, that recently vacated buildings normally are not cost-effective renovation candidates for advanced manufacturing needs.
Characteristics of an advanced manufacturing building would be one with clear spans to house a clean room, thick slabs and solid foundations for precision machinery, are thermally robust for temperature maintenance and have significant telecommunications infrastructure to manage the needs of big data.
For economic developers, it’s a good practice to stratify which buildings in your entire portfolio can fit the needs for advanced manufacturers and which ones may not, and the cost of building modifications, if feasible, to bring the buildings to a higher standard.
• Workforce and Education
Advanced manufacturing companies need advanced skills to operate successfully. In order to provide these additional needed skills, the commitment to education should be evident from K-12 to post-graduate support.
Characteristics of an advanced manufacturing workforce educational system would include local and private school aggregate performance against national rankings. Normally this includes the emphasis of STEM programs in several grade schools in the area, in addition to existing regional high schools that are either dedicated to a science and math curriculum and/or have a technical and/or college-bound component in their existing curriculum. For many of the high schools, dual enrollment is important. However, the history and volume of dual enrollees is the key. For cities, this should be measured in thousands, rather than hundreds, of students.
To attract the entire workforce for a project, it is important that the region (normally provided via the state) has a program to recruit, screen and train workers via a dedicated team specifically designed for that purpose. The training includes development of job-specific skills e-manuals in addition to training videos specifically for the needs of the project.
In the U.S. today, there are approximately a half-dozen states that have such a program, and by doing this, those states have created a distinct competitive advantage to attract advanced manufacturing. The presence of, and relative activity of, the local chapters of national professional societies, such as ASCM, SME, ASSP and SHRM, are a great indicator of how well the community believes in continuous education, to provide long-term pipelines for professional positions.
The birthplace of advanced manufacturing companies, in many instances, comes from university research. Areas that can combine university research with incubator support for start-ups that can commercialize the university’s efforts are key. They are effectively able to build the ecosystem for advanced manufacturing from the ground up, therefore creating a distinct advantage for the region.
• Taxes, Laws and Incentives
According to the tax foundation, corporate income taxes are levied in 44 states, with five states whose corporate tax rates are lower than 5 percent. However, 18 states have a single factor apportionment formula, which can greatly reduce the tax burden for products shipped out of state. In addition, there are 33 states that have R&D or advanced manufacturing specific tax credits, and some of those can be monetized and sold in cases where there is no income tax burden for the manufacturer.
Tort reform legislation is designed to limit the liability of manufacturers. Over half of the U.S. have passed some type of legislation designed to limit liabilities for various industries, including manufacturing and medical. For states that have tort reform for manufacturing, choosing to locate in one of those states can limit the company’s future exposure to lawsuits.
Advanced manufacturing companies, due to the higher amount of automation, have the potential of creating an inherently safer work environment than traditional manufacturers. If this is the case, policy makers and industry can work together, expanding the number of job classifications to reflect this situation, to ultimately reduce workmen’s compensation costs.
In addition, local economic development zones can be created to support advanced manufacturers in myriad ways by reducing taxes paid, or re-directing a portion of property taxes paid to support infrastructure development in the particular zone. Several states have also passed
mega-project legislation, giving them the power to design, fund and close a deal without having to initiate a special legislative session.
Regions that can offer a combination of any or all of these areas better position themselves to attract advanced manufacturers. That is, however, assuming that the overall region and state are in sound fiscal health to be able to maintain these offers once committed.
• Quality of Life/Reduction of Risk
People want to work in areas where they enjoy living, and advanced manufacturers are normally drawn to communities that enjoy a higher quality of life. In addition, the decision-makers want to take all actions necessary to reduce their overall risk given the innate complications of siting a new facility.
One of the ways to reduce this risk is via project startup support. The new project will have a designated project manager, and most likely someone that is not from the area. When this is the case, it is important for the region (built into the project offer) to designate an ombudsman to help the project manager communicate through all levels of state and local government. A well-defined project plan utilizes an ombudsman that has manufacturing industry experience and has hopefully performed start-ups.
However, the project will evolve past an ombudsman, and even the ombudsman will need local and state support. In these instances, it is important that the local economic development function is regional in nature. By having this organizational structure in place, the efforts and needs of the region are coordinated not only for a particular project, but also for the workers that may likely be traveling into the area during their work commute, in addition to coordinating initiatives identified above and others based on agreed regional priority.
Advanced Manufacturing Needs Nurturing to Prosper
In order for the advanced manufacturing plant to thrive, it will need an environment that nurtures its growth. The adage that “there is no perfect site” may be true, but the reality is that there can be areas that are constantly moving toward improving their environment.
The road may be long, but by considering the points mentioned above, the path can be built in a manner that every turn points the advanced manufacturer toward a brighter future. T&ID