The U.S. Foreign-Trade Zones program continues to serve U.S.-based manufacturing operations by making a positive contribution to their operating margins. FTZ procedures do this by enabling a number of U.S.-based companies to significantly reduce their Customs duty costs on imported components and materials – even though their finished products are destined for the domestic market. In recent years many manufacturers have discovered that, under the U.S. FTZ model, their finished products do not have to be re-exported for the company’s bottom line to be positively affected by Zone procedures.
Unlike other “Free Trade Zone” models offered by countries whose main attraction to manufacturers is low labor cost, the U.S. Foreign-Trade Zones program offers the ability on a case-by-case basis to lower the effective duty rate on imported components in situations in which the manufactured product has a lower Customs duty rate than one or more of its imported components.
For example, prior to implementation of the Uruguay Round tariff reductions, which commenced in 1995, domestic manufacturers of capacitors (a key component of many electronic devices) enjoyed a 10 percent rate of tariff protection versus capacitors produced overseas. Etched capacitor foil – a key component – could be imported at duty rate of 5.3 percent. The U.S. tariff structure of the day was biased in favor of manufacturing capacitors in the United States because the duty rate on the imported component (foil) was lower than the duty rate that would apply to the import of the manufactured product (capacitors). However, the Information Technology Agreement – which was implemented as part of the Uruguay Round regime – has made a dramatic change the tariff structure under which the U.S.-based capacitor manufacturer now operates. Under today’s U.S. tariff structure, foreign capacitors may be imported into the United States at a “free” rate of duty, while imported etched capacitor foil remains dutiable at a rate of 5.3 percent. The relative duty rates between capacitors and capacitor foil have become “inverted.”
For the U.S.-based manufacturer of capacitors there are only two solutions for resolving this inverted tariff rate relationship: Move the manufacturing operation offshore; or, obtain U.S. Foreign-Trade Zone status. For the capacitor manufacturer operating under Zone procedures, imported etched capacitor foil may be brought into its Foreign-Trade Zone facility without paying Customs duty. The foil may then used in the manufacture of capacitors. The capacitors may then leave the FTZ production facility and be entered into the U.S. commerce at the same tariff rate that would apply to them as if they had been manufactured overseas – that is, “Free.” This tariff rationalization feature of the U.S. Foreign-Trade Zones program enables the U.S.-based capacitor manufacturer to maintain the cost-of-production structure it needs in order to compete with its overseas counterparts, which, in some cases, may even be its own multinational sister plants. The key difference between U.S. Foreign-Trade Zone benefits and those offered by so-called “Free Trade Zones” in many other countries is that, in the case of the U.S.-based capacitor manufacturer, its effective duty rate on imported components is reduced to zero even if all of its production is for the domestic market.
In today’s global manufacturing environment, production allocation decisions within a given company’s family of production facilities can often pit a U.S-based production facility against its foreign sister plants in competition for production share. Needless to say, the plant’s day-to-day operating margin can be influential in determining its level of production, and, in some cases, its ability to keep its doors open. When the staff economists of U.S. Foreign-Trade Zones Board evaluate applications by companies who want relief from the “inverted” tariff rate relationships between their imported components and their manufactured products, they review the net economic impact that Zone procedures would produce. In an overwhelming number of cases, the loss of Customs revenue that would otherwise be paid to the government by the manufacturer is more than offset by the economic and revenue benefits of attracting or retaining the manufacturing activity itself. An added economic bonus in many cases is that what would otherwise be an import of a finished manufactured product is displaced by a good manufactured in the United States using American labor and both foreign and domestic parts and materials.
According to Andrew McGilvray, executive secretary of the Foreign-Trade Zones Board, U.S. Department of Commerce, “Over the years, the Foreign-Trade Zones Board has approved the use of FTZ procedures in a number of industries. These include automotive and auto parts manufacturing, chemical and pharmaceutical production, shipbuilding, oil refining, aerospace, and electronics manufacturing.” He adds, “Of course, the Board must evaluate each application on economic and policy grounds. Most applications received in recent years have met the standard for approval, and the overall number of U.S.-based companies and industries with FTZ Board authority has continued to increase.”
Demonstrating that relief from inverted tariffs will result in more U.S.-based activity is essential to obtaining the benefit. The history of the U.S. Foreign-Trade Zones program has shown that some industries – such as pharmaceutical and aerospace manufacturing – have had an easier route than other industries. For example, both the oil refining industry and the lift truck industry required changes in the industry itself before the precedent for relief from inverted tariffs was established. In other industries – for example, shipbuilding – relief from inverted tariffs has been granted on certain commodities (such as propulsion equipment), but not on others (steel mill products). Thus, the U.S. Foreign-Trade Zones program can operate in a very surgical fashion to enhance and retain U.S.-based production.
This surgically precise evaluation and granting of the benefit of relief from inverted tariffs can sometimes have a dramatic affect on local economies and the men and women who comprise their workforce. Between 2002 and 2004 more than 1,000 jobs in the upholstered furniture industry were outsourced to China. The Community Development Foundation of Lee County, headquartered in Tupelo, conducted a study of the situation and found that inverted duty rate relationships were giving foreign-based upholstery covering operations an advantage over vertically integrated furniture manufacturing operations located in the United States.
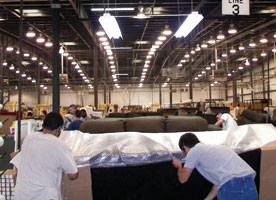
David Rumbarger, president and CEO of the Community Development Foundation says, “We needed a way to change the economics of vertically integrated furniture production, or we were going to lose another 1,000 full-time jobs in Lee County alone. Our total population is a little over 80,000, so we could not afford to lose another thousand jobs to China.” The solution came in the form of Foreign-Trade Zone manufacturing authority, including relief from inverted tariffs for specific commodities not manufactured in the United States. Rumbarger adds, “We deliberately limited the scope of the products that relief from inverted tariffs would apply to. We did this for two reasons. First, we didn’t want the furniture companies’ benefit to come at the expense of their American suppliers. Second, we didn’t want anyone to have any sort of valid claim that that was what we were trying to do. The FTZ Board’s examination of our applications was plenty thorough, but the Board came to the right decision and saved 1,000 American jobs. Even though the scope of relief from inverted tariffs for the furniture companies is pretty narrow, it’s important enough for them to remain vertically integrated and maintain a full complement of skilled positions. It’s also nice that a number of their American suppliers understand that FTZ status has helped to preserve some of their domestic customer base.”
Relief from inverted tariffs enables U.S.-based manufacturers to produce their goods and sell them in the American marketplace, and maintain the operating margins that are essential to their survival. This is especially important when one considers that every manufactured product that is produced in the United States – even when a number of foreign parts or materials are used in its production – represents the displacement of a foreign-made finished product.
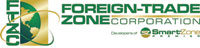
Copyright © 2010 by Greg Jones
Used by Permission