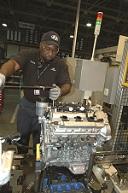
Reshoring is defined as the bringing back to the U.S. of the manufacture of products that had been lost to offshore sources, also sometimes called “onshoring,” “insourcing” and “backshoring.” It is based on the logic of localization: to produce near the consumer. Localization makes good business sense in general, but especially for the U.S., which is still the biggest consumer market.
Making more of our own products for our own market has many benefits. Replacing imports should be an obvious niche for U.S. companies seeking growth, with the potential to reduce offshore costs, improve image and quality, and leave a lighter green footprint. U.S. manufacturing is expected to expand in size and popularity and with it the supply chain will also become stronger, adding greater attractiveness to U.S. production. The growing consumer preference and demand for “Made in USA” products adds additional incentive.
While reshoring often makes sense on a total cost basis alone, replacing products that were previously imported also provides the fastest means to reduce the national trade deficit, which will further empower a strong local consumer market. The 1.6 job multiplier effect offers additional incentive for EDOs to focus on reshoring and industrial expansion.
In recent years, global shifts in wages, energy prices and supply chain costs prompted companies to more carefully assess their total costs, curbing or reversing offshore sourcing. While the offshore movement was driven primarily by cheap price and labor abroad, reshoring is driven by total cost of ownership (TCO) analysis. TCO accounts for all landed costs, plus all hidden costs, which when added up often amount to 20 percent or more. These costs accrued from offshoring are not accounted for in simplistic cost models, but they are hard costs and are what are driving companies to reshore.
The Reshoring Initiative offers the Total Cost of Ownership Estimator™, a free tool to help companies easily determine their TCO for specific products. The Estimator uses 36 factors to calculate 27 costs, which it accumulates into a single Total Cost for a product sourced from one particular production source. This process can be repeated for each source, allowing the user to objectively compare the TCO for the same product from multiple sources, whether local or offshore, and whether in-house or outsourced.
The expansion of the reshoring trend has resulted in bringing U.S. net annual manufacturing job losses to zero. See Figure 2, which gives a good overview of the trends in reshoring and offshoring.
Stopping the decades-long bleeding is a big achievement, but it is only the tip of the iceberg in terms of what reshoring can do for our companies and our country. If the current trend of increased TCO use is paired with other favorable factors, the potential for reshored jobs is estimated at up to six million, as demonstrated in Figure 3.
TCO is an essential component for OEMs to make an accurate sourcing decision and also can be used both to convince customers to buy from onshore companies versus offshore competitors and to attract FDI.
The Reshoring Initiative recommends that all OEMs, contract manufacturers and development organizations focus on using a development plan based on localization.
A Focused Reshoring Program
Begin by identifying products and components that are currently imported to the region from offshore and seek to replace them with local production. How?
1. You can use the Datamyne database to identify all ocean-freighted imports by all regional companies, generally OEMs.
2. Decide which imports are, in aggregate, in large volume and could be economically produced in the region: in-house or by suppliers (generally SMEs). For example:
a. Emphasize those products for which the region has the required suppliers or skilled labor, even if not in excess.
b. Exclude such things as produce that cannot be grown locally, items that are intrinsically too labor-intense, minerals that cannot be found locally, etc.
3. Ask the importers to consider producing or sourcing locally what they now import. When importers respond that they do not produce or source locally because labor rates and thus prices are much lower (typically 30 percent) offshore, or mention taxes, regulations, etc., help them use a more comprehensive metric: TCO.
a. Invite involved importers to the Reshoring Initiative’s free Total Cost of Ownership (TCO) Estimator to reevaluate offshoring versus reshoring. The Initiative also trains the EDO’s field staff what to discuss with the importer and trains a few EDO staff to be the local experts.
b. Help the importers see that there is often no or only a small TCO difference with local production or sourcing, even though there is a large price difference.
c. If the importer has lost the knowledge required to produce the products, assemble a team to help it redevelop that knowledge.
d. For work that the importer decides to outsource, bring importers and suppliers together in a Purchasing Fair to start the shift of work from offshore. The Reshoring Initiative’s user data suggest that about 25 percent of offshored work would come back if TCO was consistently used.
e. Identify any remaining TCO gaps versus offshore. To close remaining small gaps, utilize a team, as needed:
1) Automation: e.g., machine tool and automation distributors and producers
2) Workforce technology skills training: technology providers and distributors, trade associations, community colleges
3) Lean and other process improvements: MEP (Manufacturing Extension Partnership), AME (Association for Manufacturing Excellence), etc.
4) Economic development assistance/incentives: EDOs.
f. Recruit other U.S. companies or FDI to fill large regional supply gaps.
g. Using the TCO software, forecast when additional work will be reshorable based on forecast increases in foreign labor costs. Follow-up accordingly.
h. Develop tools to help the importers decide to reshore:
1) Lists of regional or state companies that have successfully reshored
2) Lists of suppliers to which importers have shifted sourcing
3) TCO/ Reshoring Initiative
4) Lists of resources to help reduce total cost at importer or supplier
5) U.S. Department of Commerce’s online ACE tool
6) Free publicity, if wanted.
These steps will foster great benefits. Work that comes back from offshore rather than from neighboring states creates much more of a win/win situation for everyone. Minimal incentives are required, since the work comes back in the self-interest of the involved companies. Local ecosystems are strengthened around OEMs to make them more successful and more firmly linked to the region. This environment also feeds the skilled workforce program described in this article.
Skilled Workforce
Having the skilled workforce is a major factor in the continued success of reshoring efforts. Companies need to be aware of what the issues are, what is being done, and how they can help. Here are some of the Reshoring Initiative’s suggestions.
The bottleneck to expanding the skilled workforce is recruitment: students are hesitant to follow STEM fields, especially in manufacturing. The following programs are crafted to overcome at minimal cost negative perception issues in recruitment:
1. The perception of ongoing manufacturing decline: We need to change the belief that there is no future in manufacturing and that all the work will go offshore. This can be done by:
a. Promoting the success of reshoring to improve the attractiveness of manufacturing careers
b. Recruiting NAM (National Association of Manufacturing) and local groups like NTMA, PMA, PMPA, EDOs, MEPs, AME and the community colleges to gather local reshoring cases
c. Publishing in local media such as the regional “Reshoring Cases of the Month” and submit nationally. Reshoring Initiative has an online case reporting capability.
Reshoring needs recruiting, and recruiting needs reshoring to be visibly succeeding. These steps motivate students to select, guidance counselors to recommend and schools to provide skills training.
2. Perception of low prestige and income: Change the image of “vocations/trades” training as lower status than a four-year university degree and of a university degree as the only route to middle-income careers. As manufacturing skilled workers take on more mental and less physical responsibilities, the “professional” terminology is increasingly appropriate.
a. Terminate the use of the terms “vocation” and “trades.”
b. Refer to the skilled occupations as professions and the workers as professionals as is done in Germany and Switzerland.
c. Requires the cooperation of K-12 educational system, community colleges, media, employers, EDOs, etc.
d. Benefit: Increases attractiveness of skills training and careers.
3. Document that training pays: Here is evidence that you can make a difference. The Reshoring Initiative presented to the Department of Labor to include in BLS data the incomes of workers who have passed apprenticeships or have a strong portfolio of credentials. Based on its discussion, BLS has added at the bottom of a key page that shows the relationship between income and degree level a note regarding apprenticeships and training, and changed the heading from “Education Pays” to more neutral text. They have started a survey to collect the data. By making available to guidance counselors and school administrators data showing that there are “other ways to win,” we will attract higher-caliber recruits. This effort has a high impact with almost no cost.
The more manufacturing is reshored, the stronger are the forces that attract it. Bringing production back to the U.S. has the potential to lower a business’s total cost, improve its ability to innovate and produce a high-quality product. It also will advance infrastructure, investment in a skilled workforce, competitiveness and the U.S. economy as a whole. A strong economy means a healthy consumer market that will ensure the continued demand for local (thus high-quality, low-environmental-impact) goods.
The economic recession heightened consumers’ awareness and desire to buy “Made in USA” products. The Reshoring Initiative provides the tools for manufacturers to determine which cases are viable options for reshoring. TCO offers the most accurate analysis and often reveals the U.S. to be the most sensible sourcing location.
Reshoring Resources
-
Calculate TCO with the Total Cost of Ownership Estimator™ – Free online tool at the Reshoring Initiative to help evaluate sourcing alternatives and to make a case when selling against offshore competitors.
-
See on YouTube the newly released in-depth webinar Applying Reshoring and Total Cost in PA with Harry Moser, presented by NEPIRC.
-
New Reshoring Library -The updated version of the Reshoring Initiatives’ Reshoring Library contains 1000+ linked articles on reshoring. Data from articles can now be publicly accessed through the Advanced Search function. Businesses can use it to find other companies in their region/industry and target them in their sales efforts.