
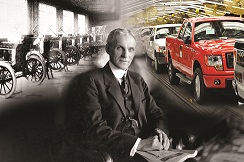
On December 1, 1913, Henry Ford started operating the first manufacturing assembly line. It was a concept that changed worldwide manufacturing operations by making volume manufacturing feasible and cost competitiveness attainable for the general public. That’s the way everybody looked at manufacturing until shortly after World War II. America dominated the world in manufacturing output, but gradually started to fall behind other nations on manufacturing technology. Then, in 1951 the Univac computer joined the world of manufacturing. Enter the term advanced manufacturing versus traditional manufacturing.
Why is Regaining America’s Competitive Edge in Manufacturing so Important?
In 2013, The National Association of Manufacturers (NAM) reported:
-
Manufacturing contributed $1.87 trillion to the economy. This represented 11.9 percent of the total nation’s GDP.
-
For every $1.00 in manufacturing, another $1.48 was added to the economy.
-
Manufacturing supports 17.2 million jobs in the United States, or about nine percent of the workforce. In addition, for every 100 jobs created in manufacturing, another 60 are created in service sectors.
-
The average manufacturer worker earns about $17,000 more per year than the national average. As a result, the U.S. has the highest worker productivity in the world.
-
Manufacturing accounts for two-thirds of all private-sector R&D in the U.S.
-
Taken alone, U. S. manufacturing would be the tenth-largest economy in the world.
-
Manufacturing employs 75 percent of all scientists and engineers.
Every city and state in America has “advanced manufacturing” as an economic development target in their overall development plan. However, if you ask those involved in the economic development planning what exactly comprises the boundaries of “advanced manufacturing” in their plan, you are as likely to get as many answers as you have people.
In the mid-1960s, manufacturing was still separated into two categories “advanced” and “traditional.” That is, traditional manufacturing was hard product industries such as automotive, steel and industrial machinery and the like, while “advanced manufacturing” would best be described as manufacturing process technologies. These industries included computer technologies, high-performance computing, high-precision technologies, information technologies, biotechnology, medical device manufacturing, advanced robotics and other intelligent production systems, automation, control systems to monitor processes, sustainable and green technologies, new industrial platform technologies, custom manufacturing, management methodologies and scalability in manufacturing. Detroit was traditional manufacturing; Silicon Valley was advanced manufacturing.
On June 24, 2011, President Obama spoke at Carnegie Mellon University and launched the Advanced Manufacturing Partnership (AMP). This private-sector-led national effort is a key component of Washington’s plan to revitalize American manufacturing. This partnership involves government, at both federal and state levels, industry and academia to identify the most pressing challenges and transformative opportunities to improve technologies, processes and products across multiple manufacturing industries. The AMP report presented to the President on capturing competitive advantage in advanced manufacturing addresses needs in three broad categories:
-
Enabling innovation in all manufacturing industries
-
Securing the talent pipeline
-
Improving the business climate.
Enabling Innovation in all Manufacturing Industries
The most common definition of advanced manufacturing involves the use of technology to improve products and/or processes, with the relevant technology being described as advanced, innovative or cutting edge.1 The White House defined advanced manufacturing as “manufacturing that entails rapid transfer of science and technology into manufacturing products and processes.” Most discussants agree that an appropriate advanced manufacturing definition should be dynamic in nature and treated as more of a benchmark. That is, there is a constant iteration of improving manufacturing frontiers. Therefore, what is classified as “frontier” is constantly changing. As C. B. Adams put it in a St. Louis Commerce Magazine2 article, “Advanced manufacturing is like a chameleon. It changes in response to needs of whichever company has incorporated it into its manufacturing process.”
Industries that were long considered traditional manufacturers such as the auto industry have embraced advanced manufacturing. “Advanced manufacturing, as we define it at Johnson Controls, is not just the actual manufacturing of products on the shop floor. Rather, it is a series of steps, beginning with advanced development, which we call ‘ideation,’ all the way through to production,” said Bob Henderson, plant manager for Johnson Controls, a St. Louis manufacturer of assembly parts for Chrysler and Dodge products.
The focus of advanced manufacturing is not on product lines, as was the case with traditional manufacturing, but on the processes by which products are built. Advanced manufacturing is the methodology behind the current revolution in manufacturing affairs that is redistributing comparative advantage worldwide. This is no less revolutionary then Mr. Ford’s chain-driven assembly line. Manufacturing has fundamentally changed with the arrival of global competition. This is evidenced by those enterprises capable of distributing value chain production worldwide and reducing costs by exploiting automation and information integration. The U.S. cannot and should not attempt to compete on a labor cost basis. Our comparative advantage resides in technological and process innovations that boost productivity and make advanced manufacturing possible.
The key to the resurgence of the American manufacturing sector lies in achieving a competitive advantage through higher levels of productivity and improved customer service. Whether termed just-in-time, advanced manufacturing, lean thinking or manufacturing flexibility, the elimination of waste from the value chain and a drive to push the limits of technology are the dominant ideas in state-of-the-art manufacturing. Advanced manufacturing consists of the “hard” improvements made in manufacturing machinery and technology and the “soft” improvements of waste reduction and resource management, collectively referred to as sustainability. This blending of technical innovation and process control will lead to an increase in productivity that will allow American manufacturers to compete successfully worldwide.
Manufacturing is a process of applying correct business practices that result in production of the right product, in the right quantity, at the right time. Two new elements, time and distance compression, have been added to traditional business concerns. Time compression has placed a premium on the ability of business to respond quickly and correctly before their competitors dominate new markets. Distance compression has resulted in the whole world becoming potential sources of supply and competition. This is particularly true in the global pressure to reduce wages and achieve a cost advantage. Advancements in transportation and information technology are but two manifestations of this new reality.
Two specific elements must be present in a manufacturing concern before it can be termed “advanced.” The first of these is the use of advanced technology for precision control of the manufacturing process. This creates a uniform and consistent quality product. Technologically advanced machinery is often capable of multiple uses and of being quickly reconfigured for similar products. This flexible response to customer demands allows a manufacturer to respond to a wider range of conditions without making additional capital investments. The second element of advanced manufacturing is the application of advanced processes used throughout the value chain to reduce costs. Management and labor review processes for continuous improvement. Waste and the inefficient use of resources are examined in detail to determine how they can be eliminated. A highly trained and motivated workforce acts as a multiplier for management efforts. This segues us to the second point of the AMP Program.
Securing the Talent Pipeline
Technical skills are essential to the future of advanced manufacturing. According to a survey conducted by the NAM on the future advanced manufacturing workforce requirements, 53 percent of the respondents listed technical skills as the greatest need. Additional skill sets included the ability to work in teams (47 percent), strong computer skills (40 percent), the ability to read and translate diagrams and flow charts (39 percent) and strong supervisory and managerial skills (37 percent). Jobs in the new manufacturing picture require complete understanding and mastery of these varied skill sets. Workers need the production skills to set up, operate, monitor and control the manufacturing process. They need the process design and development skills to continuously improve production processes. They need skills in maintenance, installation and repair to maintain and optimize complex equipment and systems. They need knowledge of the supply chain logistics to plan and monitor the movement and storage of materials and products.
The National Council for Advanced Manufacturing (NACFAM) has enlisted 32 national manufacturing trade associations and professional societies to support "America’s 21st Century Learning System" policy roadmap. Key points include:
-
Validated and rigorous world-class learning standards, assessments and curricula for PK – 16.
-
Applied learning in grades PK – 12.
-
Demonstrated mastery of academic and workplace competencies for high school seniors to get diplomas.
-
Strengthened career counseling for students in grades 7 – 12.
-
Support of lifelong learning and continuous skill enhancement for all Americans through retirement.
As an example, this high level of training is reflected in the way Boeing has developed new technologies and processes for the assembly of the C17, FA18 and F15 programs. The company is developing new technologies that improve the assembly of the aircraft from a systems approach by utilizing automated drilling, reaming, fastening and the application of sealants.
“Speed is not how quickly you can move, but how quickly you can move in the right direction. One of our key focuses is to see how quickly we can solve manufacturing problems in a more efficient and timely way.” Now we’re not just looking at feeds and speeds issues. We are machining for assembly now as opposed to improved metal removal rate. When you think about that, not only are we impacting and changing the technology, but we also impact resources required, because a different skill set is required of our operators,” said Bill Williams, director of manufacturing processes improvement.
“For instance, assembly teams used to consult large, bulky printed work instruction manuals. Now the teams consult web-based instructions that are electronically displayed. To give them the needed skills, team members are trained for competencies on computers and computer systems. We have it such that they know what is required next in each sequence of building the job. Advanced manufacturing means they are higher on the value chain. That is really driving a change in our resource management as related to training and deployment of technology.”
Improving the Business Climate
High taxes, government over-regulation, at both the federal and state level, a stalled Congress that doesn’t seem to be able to rein-in its spending, that’s what most companies see that is creating a lack of confidence, and puts up a barrier to improving the business climate and advancing manufacturing in the U.S.
A report from Booz & Company, a New York-based global management company, and the University of Michigan’s Tauber Institute for Global Operations calls for the private sector and policy makers in government to concentrate on four actions to provide the greatest momentum for manufacturing:
-
Think and grow regionally. The U.S. needs to build a better future with Mexico, shifting less demanding jobs and labor-intensive processes to that country while helping to build a safer consumer economy there and retaining highly skilled work in the U.S.
-
Develop and attract skilled talent. The U.S. needs more robust manufacturing education programs, immigration reform and promoting the attractiveness of manufacturing careers.
-
Foster high-impact clusters. The public and private sectors can build geographical concentrations of suppliers, service providers and academic institutions reinforced by investments in infrastructure.
-
Simplify and streamline the tax and regulatory structure. Closing the gap between the current statutory tax rate and the effective tax rate would be a revenue-neutral way to put U.S. manufacturing on a level global playing field.
There are literally hundreds of government programs, both state and federal, providing assistance for everything from worker training to expansion aid. The U.S. Department of Commerce website provides information on all current federal and state-by-state incentives under the Select USA program. These programs do not include local or negotiated incentives which may increase assistance substantially. It is always recommended that one secure an incentives management team for assistance.
Conclusion
The term “advanced manufacturing” encompasses all of the developments in the manufacturing field over the last 60-plus years including high-tech products and lean, green and flexible manufacturing. No one definition captures everything said about advanced manufacturing. Perhaps one of best definitions is really a non-definition given by Tom White, Missouri Enterprise Business Assistance Center, “Advanced manufacturing, by its very nature defies definition, because it is going to be different for the chemical industry than it is for the metal fabrication industry and any other industry.”
References:
1 Wikipedia, http://en.wikipedia.org/wiki/Advanced_manufacturing
2 St. Louis Commerce Magazine, http://www.stlcommercemagazine.com/archives/october2001/manufacturing.html