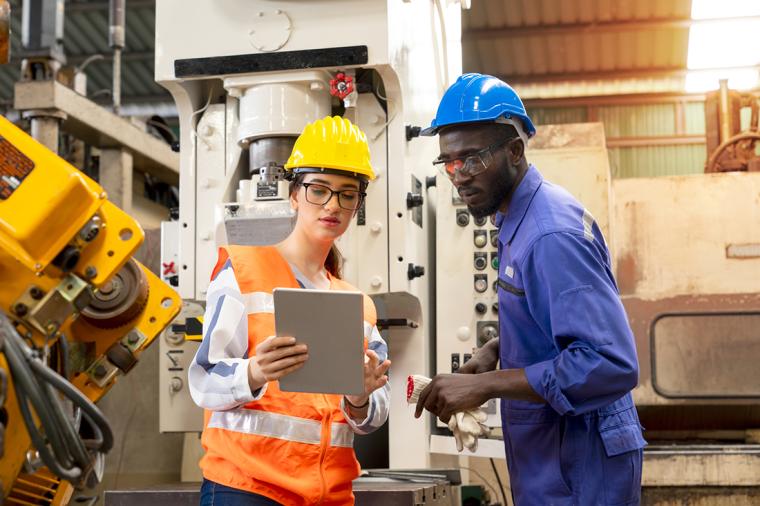
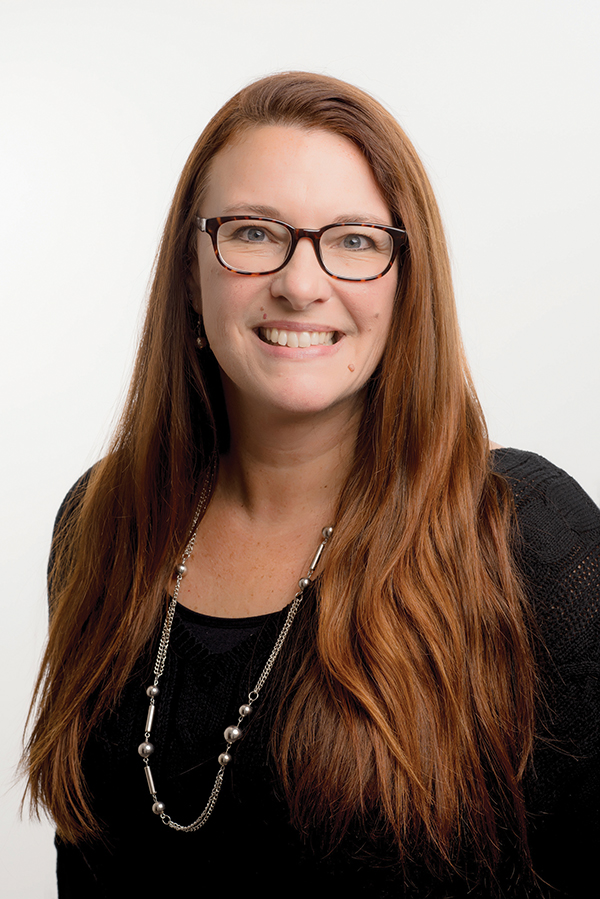
More workers than ever before are seeking employment that allows them to work from home, or that provide an increased level of schedule flexibility. However, with the ongoing labor shortage plaguing manufacturing today, how are employers supposed to address workersí needs, wants and preferences, while still ensuring they can meet their own goals and maximize their bottom lines?
Many manufacturers have already implemented flexible work schedules within their own organizations, and the results are promising. Whether it’s increased job satisfaction, rising employee productivity or increased interest on the part of potential job candidates, manufacturers are leveraging flexibility to attract younger employees to court new opportunities and get ahead (and stay ahead) of their competition.
With all that being said, let’s review what flexibility could (and should) look like in manufacturing today. Here are some arrangements organizations may want to consider, some of which the Association for Equipment Manufacturers (AEM) has implemented over the years:
A compressed workweek. This involves employees working longer shifts over fewer days, such as working four 10-hour days instead of five eight-hour days. AEM opted to offer a summer-only compressed workweek schedule in 2023 as a benefit approved on a case-by-case basis.
Job sharing. This involves two employees sharing one full-time job, allowing them to split the workload and work part-time hours.
Part-time work. Employees work fewer hours than in a full-time position, which can be especially useful for employees who have caregiving responsibilities or other obligations outside of work.
Adjusting or flexing start and end times for shifts. This helps employees who need to work around school and daycare schedules or have other family needs.
Cross-training employees and creating multi-functional teams. This can also help to support flexibility. By training employees to perform multiple tasks, manufacturers can quickly respond to changes in demand by shifting workers between different tasks and processes as needed.
There is no one “best way” to create flexibility for employees. However, one thing to not do is simply make assumptions. Engage employees to understand what flexibility means to them. Implementing flexible work schedules in manufacturing requires careful planning and coordination to ensure production schedules are being met and all employees can perform their roles and meet their responsibilities. However, with both a proper approach and clear communication, creating flexible work schedules can result in:
Improved job satisfaction. When employees possess more control over their work schedules, they are often more satisfied with their jobs. This can lead to improved morale, reduced turnover and increased loyalty.
Increased productivity. Flexible work arrangements can help to reduce employee stress and fatigue, leading to increased productivity and better performance.
Enhanced recruitment and retention. Flexible work arrangements can be an attractive benefit for potential job candidates, making it easier for manufacturers to recruit and retain top talent.
Improved employee health. Flexibility can reduce employee stress and promote a better work-life balance.
Cost savings. Flexible arrangements can help manufacturers to reduce costs associated with absenteeism, turnover and overtime pay.
Manufacturing is a fast-paced industry with demanding workloads and strict deadlines. However, traditional work arrangements with fixed schedules and strict attendance policies may not be suitable for all employees. A flexible work environment can provide significant benefits to both employees and manufacturers, improving job satisfaction, productivity and, ultimately, the bottom line. As industries continue to evolve and grow over time, organizations must consider all options as they look to attract and retain top talent. T&ID