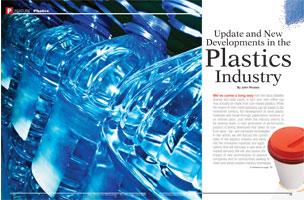
We’ve come a long way from the black Bakelite phones and radio cases. In fact, your new coffee cup may actually be made from corn-based plastics. While the origins of man-made polymers can be traced to the nineteenth century, the development of novel plastic materials and break-through applications continue at an intense pace. Just when the industry seems to be slowing down, a next generation of performance plastics is being developed that takes its cue from nano-, bio- and composite technologies. In this article, we will discuss the current state of the plastics industry and delve into the innovative materials and applications that will stimulate a new level of market demand. We will also assess the impact of new technologies on plastics companies and on communities seeking to retain and attract plastics industry businesses.
Current State of the Plastics Industry
The world’s annual consumption of plastics is in excess of 550 billion pounds, up from over 350 billion pounds in 2000. Longer term anticipated growth reflects new product development driving additional demand and the growing level of consumerism in India, China and other emerging economies. Within the United States, there are approximately 100 billion pounds of polymer resin produced each year with some softening in demand during the recent recession.
Plastics are known for their material properties of moldability, favorable weight to strength ratios, corrosion and water resistance, and other characteristics. It is a ubiquitous material with major applications as a packaging material; as components in transportation equipment, machinery, medical devices, appliances and electronics equipment; as a construction material; as an adhesive and coating substance; as medical supplies; and countless other applications.
The plastics industry cluster includes resin manufacturing and compounding, production machinery and metal fabrication of molds and fixtures, the actual manufacturing of plastic products and parts, and the distribution of resins and shapes. Employment within this cluster is in excess of 850,000, and it is one of the top North American manufacturing segments. States with the highest employment in the production of plastic resin are Texas followed by Ohio, Michigan and Illinois. Those with the highest employment in the manufacturing of plastic-related products include California, Illinois, Indiana, Michigan, Ohio, Pennsylvania and Texas.
Plastics have traditionally been classified in one of three categories: thermoplastics, thermosets and elastomers. Thermoplastics are the most common type and have a relatively soft consistency with the ability to be remelted and therefore recycled. They include polyethylene, polypropylene, nylon and polystyrene that are made into packaging, rope, foam insulation and many other products. Thermoset plastics are hard in consistency, cannot be remelted, and include epoxy-based materials, phenolics, polyurethanes and melamines. Elastomers have a primary characteristic of being flexible and include materials such as neoprene and silicones.
Plastics are also classified as being either commodities, engineered plastics or specialty plastics. Commodities have high volume consumption rates with limited performance characteristics, global production sources and intense competition. Engineered plastics have high performance capabilities and require significant attention to composition and production quality control to achieve optimum results. This inherently makes them less prolific and of higher value. Specialty plastics have limited runs with more niche applications.
As expected, when products and materials become a commodity there is a natural shift to highly productive manufacturing methods as well as a migration to lower cost destinations. This is particularly true for products that are relatively easy to ship due to lower weight and smaller size, have longer production runs, and require minimal modifications to meet multiple customer specifications. Products that are highly engineered or otherwise customized, have short production runs, or have exceptional weight or size characteristics, tend to retain their production close to their local markets.
Emerging Plastic Materials and Their Applications
Plastics are typically comprised of a base resin that is compounded with fillers, plasticizers, color-enhancing pigments and other additives that are proportioned to some well-defined formula to achieve specific results. There are thousands of resin/additive combinations that are utilized to make different products and the ultimate performance of a given plastic material is derived from both the chemistry of the base resin and its interaction with the types and proportions of additives that are utilized.
The search for new performance characteristics for plastics is relentless along with the emerging interest in those that are biodegradable, have a high recycle potential or are made from renewable/non-petroleum materials. There is also a convergence of plastics with nanotechnology and composite technology that has given rise to some very promising high performance materials. The age of plastics is about to take on some radically new directions as will be discussed below.
Radio Frequency (RF) Embedded Plastics
The RF system is essentially a signal generator embedded in a plastic medium that can take on different shapes and be utilized for highway toll tags, amusement park wrist bands, building security system badges, clothing inventory tags, library book management, cargo container seals and tracking systems, hospital patient tracking, childcare tracking – the list is endless and growing rapidly. The production of specific long-run applications will quickly become a commodity but the development of new applications will continue to be a knowledge-based activity. There may be some high security or high value, small production run applications that will not migrate to the lowest cost production destination.
Nanocomposites
The application of nanotechnology to plastics is the opportunity to affect the performance of a particular resin and a profile of additives at the molecular level. This type of precise engineering has produced materials with properties such as greatly enhanced heat, dent and scratch resistance. There can also be an increase in dimensional stability, electrical conductivity, stiffness, flame retardancy – any number of favorable characteristics. Being able to control the material performance at such a fundamental level and input a nearly infinite variety of substances as additives, gives the engineer and product designer substantially more latitude in product design and performance.
Materials that are being applied to nanocomposites include nanoclays, carbon nanotubes, nanotalcs, other minerals and related materials. At this level, the fundamental characteristics of the resin can have a unique interplay with the properties of each additive. This opens up the field of material science to a whole new approach but also brings a much higher level of complexity. This will drive the need for a wide array of software modeling, prototyping and testing to enable a more controlled and rapidly deployed material development process.
Some of the immediate applications for nanocomposites include automotive and aerospace components; military hardware; electronics; medical devices; timed release of biocides and dyes; barrier layers within food packaging; semiconductor/polymer device for improved photovoltaic solar cells; foam applications for seat cushions, disposable diapers; packaging materials – the list seem endless. Nanocomposites will be a key player in the on-going materials revolution that will produce many new product applications.
Smart Polymers
This includes a series of polymers that respond in shape and displacement to changes in the environmental, such as temperature, amount of light, presence of water or pH. In many cases it is a non-linear response such that the shape change can be significant based on a minimal stimulus. When the stimulus is removed, the material can resort back to its original shape. There are a host of applications for these materials in surgical and other medical situations, remote actuated valves and switches at the micro and macro level for industrial and medical use, and many other opportunities. The smart polymer adds another dimension to the designer’s toolbox – remote change in distance based on specific, predictable conditions.
Bioplastics
Although plastics-related products have brought a substantial value to society over the past one hundred years, there have been several issues that needed to be addressed, including, the persistence of plastics in the environment after they are discarded and the consumption of petroleum – a non-renewable resource – as a feedstock for plastics. Applied research and new product development has been aggressively pursuing solutions to these problems and new options are beginning to surface. An emerging product is polylactic acid (PLA) polymers that are derived from converting starches and sugars from corn and sugarcane into resin pellets.
NatureWorks LLC, an independent company wholly owned by Cargill, has developed plant-based polymer resins that can be converted into fibers for clothing, films in packaging, and a variety of molded products. Toray Plastics, a global plastics company with headquarters in Japan, has helped to develop a plant fiber-reinforced PLA plastic that has improved heat resistance, rigidity and moldability by compounding the base resin with certain plant fibers. The result is a higher performance product that has the potential for wide applications including component parts in telecommunications and electronics equipment, automotive and aerospace, energy and other markets. When companies of this stature take an aggressive interest in bioplastics, new developments in technology and applications will move forward rapidly.
There are other bioplastics opportunities that are currently on the market. Companies have developed soy-based resins that are being used as composite counter tops; adhesives in plywood; polyurethane foam for automotive seats and foam insulation; and rigid structures for sections of large drainage pipes that are strong but easy to handle and assemble. Over time, plant-based polymers will make significant substitutes and improvements to petroleum-based plastics.
The Impact of New Technologies on Plastics Companies
The rapid changes in new material technology may obsolete existing products by offering enhanced performance or reduced cost. In addition, the evolving ability of off-shore sources to provide lower cost alternatives to more sophisticated parts and equipment fabrication will continuously cut into domestic production. It is important to stay abreast of new product and process developments and be positioned to make strategic changes and investments. Larger companies may need to enhance their R&D function and gain access to additional R&D resources such as a university with a polymer program or other technology partner.
The Role of Location in the Plastics Industry
Location does play a role for plastics companies and differs over the life cycle of a particular product. In the early phases of product development, there is a need to locate near, or at least have direct access to, R&D. This may be co-location of a company’s R&D function with a university’s polymer program or with a technology partner. The location will have a reasonable access to transportation and business services along with a favorable quality of life and options for spousal employment. Exact location requirements will vary by company and product mix.
As the company expands, having access to the enabling resources for growth (sites and buildings, labor skills, training and education, interstate and rail access, utilities and reasonable cost) become the key factors. As the product matures, the issue of cost and the resultant operating margins become the critical factors as the product becomes a commodity and global competition intensifies.
Community Considerations
Communities that seek to retain and attract plastics companies need to offer an integrated package of resources that include certified sites at a high level of readiness, interstate and rail (depending on size of company) access along with a qualified labor force backed by top training programs. Utilities need to be in place and offered at a reasonable rate. Access to both product and process R&D will be critical to companies seeking to adapt to new opportunities and having a reasonable plastics industry presence is a factor. There is both a science and an art to matching the right community with the needs of a specific company.
There will be swings in demand as a reflection of the economy but plastics are not going to disappear. The pending trends show some very promising breakthroughs in plastics technology and the life cycle stages of any type of material or product will continue to shorten. From a longer term perspective, as the old movie line goes: “There is a future in plastics.”