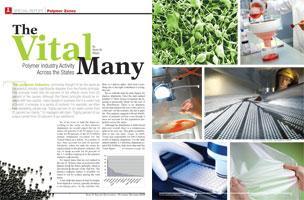
The polymer industry, commonly thought to be the same as the plastics industry, significantly deviates from the Pareto principle. This principle holds that 80 percent of the effects come from 20 percent of the causes. Although the Pareto principle should be invoked with due caution, many people in business find it a useful rule of thumb. It emerges in a variety of contexts. For example, we often hear marketing people say, “Eighty percent of our sales comes from 20 percent our clients.” Or managers will claim, “Eighty percent of our output comes from 20 percent of our workforce.”
So, if we were to rank the states according to the value of their plastics shipments, we would expect the top 10 states (20 percent of all 50 states) to account for 80 percent of the $379 billion annual shipments recorded for the United States as a whole. As a matter of fact, they account for just 60 percent. Similarly, when we rank the states by employment in the plastics industry, the top 10 states account for 60 percent of the 1.1 million employed in the plastics industry nationwide.
For many states that are not ranked in the top 10, it must come as good news that plastics flouts the Pareto principle, which is also known as the law of the vital few. The plastics industry makes it possible for states to vie for a place among the vital many.
A bar chart that arrays its bars by height, from highest to lowest, typically produces a swooping curve. At the extreme left, there is a narrow spike. And most everything else to the right contributes to a long, thin tail.
Not so with the state-by-state figures for plastics shipments. Once the state ranked number 11 (New Jersey) is reached, the tapering is practically linear for the rest of the distribution. There is no dramatic swoop that reduces the rest of the curve to a thin tail. On the contrary, the tail is quite fat. This analysis suggests a broad distribution of polymer activity even though it does not account for the population disparities across the states.
Although the distribution is fairly broad and even overall, there is a conspicuous spike at its very top. This spike is attributable to just one state: Texas. In 2006, Texas was responsible for $49.5 billion worth of plastics shipments. For the state ranked number 2, California, shipments totaled $26.8 billion, little more than half the Texas figure.
Structure of the Plastics Industry
This apparent anomaly has a simple explanation – and it checks with what we know about the structure of the plastics industry. In general, this industry has two parts: the part that produces resins or raw plastics from feedstocks such as natural gas, and the part that processes raw plastics into finished products. Texas, it turns out, is active in both parts of the industry. And it is especially prominent in the production of resins.
Few locations are well suited to the production of raw plastics. Suitable locations are limited to places with extensive refining facilities and well-developed petrochemical capacity. So it should come as no surprise that these locations tend to be found along the Gulf Coast.
They are especially concentrated in the Houston area. Houston dominates the U.S. production of three major resins: polyethylene (37.1 percent of U.S. capacity), polyvinyl chloride (37.0 percent) and polypropylene (53.4 percent). Half of all Texas plastics workers are employed in the Houston area.
Documentation prepared by the Bay Area Houston Economic Partnership reflects both the concentration and the scale of the area’s plastics industry. For example, the Partnership notes that much of this industry is located within the Bayport Industrial District, which covers 12 square miles (8,500 acres). Many of the plants within the district are the largest producers of specialty resins in the world. Examples of prominent companies include EVAL Americas, INEOS NOVA, Kaneka Texas and TOTAL Petrochemicals.
At the beginning of 2006, 55 percent of the district had been developed, leaving approximately 3,800 acres available for new plants and expansion projects. To encourage further development, local authorities offer tax abatements, emissions reduction incentive grants and workforce training grants. The area also boasts unique infrastructure – facilities for industrial wastewater treatment, extensive rail and highway access, and a port that is ranked first in the United States in foreign waterborne commerce and second in total tonnage.
However, as mentioned earlier, Texas is something of an outlier. Relatively few states have the refining or petrochemical capabilities to produce raw plastics on a monumental scale. It should be mentioned, however, that Louisiana accounts for $8.9 billion in plastics shipments. This gives it a number 16 ranking in that category, while it ranks 29th in plastics employment. The disparity in these rankings reflects Louisiana’s strong contribution to synthetic resins production. These resins come from a capital- and technology-intensive industry. In such industries, output per employee is typically high.
Emphasis on Processing Raw Plastics
Beyond the Gulf Coast, most states place greater emphasis on processing raw plastics. The companies that process raw plastics tend to be smaller and more varied than the resin manufacturers. Because they manufacture products that are light and bulky, shipping them over any great distance is expensive. Consequently, plastics processors locate near their target markets. In fact, they are often considered a part of whatever industry they serve. Industries served by plastics processors include automotive, construction, food packaging and medical supply.
In Pennsylvania, which ranks sixth among the states in both employment and plastics shipments, much plastics activity is concentrated in the northwest part of the state, in and around the city of Erie. In a study commissioned by Erie authorities, the region’s advantages were compared to those of Newark, New Jersey; Lowell, Massachusetts; Philadelphia, Pennsylvania; Cleveland, Ohio; and Buffalo, New York. At first glance, it may seem a selective grouping – all the cities are in the northeast part of the country. But for a region that emphasizes plastics processing, it is simply fair to focus on nearby competitors. Nearly all processors in a given region compete with each other to serve nearby industries.
The Erie study characterized a typical project – a manufacturer devoted to molding plastic parts for the automotive, medical or consumer products markets. The hypothetical operation occupied a building with 60,000 square feet situated on six level acres in a fully improved industrial park served by rail. Investment totaled about $11 million and covered essentials such as the land and building, machinery and equipment, and inventory. Energy use averaged 300,000 KwH/month. Sales for the first year were estimated at $8 million. Finally, the number of employees totaled 80.
For such an operation, the overriding location criterion was cost. By far the leading cost factor was labor. It accounted for up to 60 percent of the project’s total operating costs. By comparison, power costs were relatively insignificant, accounting for just 2-5 percent of total operating costs. Other cost factors included taxes, build-to-suit costs and cost of living.
Just because labor costs are a leading consideration does not mean localities or regions vying for corporate investment will choose to compete solely on the basis of low wages. Indeed, many regions recognize the need of workforce quality. In Erie’s hypothetical company, the payroll included five managers/engineers, 10 technical personnel, and 15 skilled workers (mold makers and maintenance mechanics).
Workforce Development
By maintaining workforce development resources, a region can make the case that its labor pool is capable of boosting productivity and raising output per employee. In addition to customized-training programs, the Erie region offers these resources: the Knowledge Park at Penn State, the Plastics Computer-Aided Engineering Center, and the Plastics Technology Center.
Such resources are especially important to plastics processors because the industry in many respects emphasizes the optimization of materials, formulations and processes. Systematic optimization efforts may be beyond the scope of small, individual companies. But technical programs could serve many small companies in a region. And their mission could encompass not just workforce development, but business development. These programs could hasten the application of improved equipment, reveal partnership opportunities and identify niche markets resistant to low-cost foreign competition.
Many regions besides northwestern Pennsylvania maintain such resources. In Mississippi, there is the Mississippi Polymer Institute, which works with the University of Southern Mississippi’s School of Polymers and High Performance Materials to serve the needs of over 200 polymer manufacturers. In Wisconsin, there is the Wisconsin Manufacturing Extension Partnership and a range of academic programs, including the Polymer Engineering Center, the Engineering Polymer Industrial Consortium, and the Wisconsin Technical College System. In West Virginia, there is the Polymer Alliance Zone, a membership organization. Twenty-eight of West Virginia's 134 polymer companies are located in the Zone.
Such institutions serve a community-building function valuable to the industry’s many small processors. In addition, they help slow the general drift away from long-range research to optimization efforts focused on near-term product introduction or modification. And they may play a role in hastening the application of new approaches developed in academic institutions. The future of the plastics industry ultimately depends on incorporating rational approaches based on theoretical advances.
Promising areas of research include the development of new catalysts, the design of polymeric materials on the molecular scale, and the use of biological systems to control synthetic processes and perfect complex structures. Aiding these new developments are tools such as high-speed computing and improved analytical methods. Emerging applications include biodegradable polymers, polymers synthesized from alternative feedstocks, and polymers with novel electrical and optical properties.
Leaders in capitalizing on academic developments include institutions in Massachusetts and Ohio. In Massachusetts, there is the Center for UMass/Industry Research on Polymers, the oldest Industry/University Cooperative Research Center established by the National Science Foundation. In Ohio, a networking group called PolymerOhio promotes the global competitiveness and growth of Ohio’s polymer industry. PolymerOhio’s members include Ohio polymer companies, leading polymer academic institutions, economic development agencies and service providers.
Ohio has a particularly rich array of academic resources: the University of Akron’s College of Polymer Science and Polymer Engineering; Case Western Reserve University’s Department of Macromolecular Science and Engineering; the University of Cincinnati’s Institute for Nanoscale Science and Technology; the University of Dayton’s Polymer, Nanocomposites, Composites Group and Center for Basic and Applied Polymer Research; the Kent State University Liquid Crystal Institute; and Ohio State University’s Center for Advanced Polymer and Composite Engineering.
Last year, PolymerOhio launched its Advanced Polymer Company Attraction (APCA) program. PolymerOhio notes that the APCA program focuses on identifying and stimulating the interest of companies in global industry segments that offer the highest potential to establish new operations in Ohio. These segments include polymer processing, advanced composites, bioderived materials, and flexible displays and electrical optical devices. PolymerOhio regards these segments as opportune economic development targets because they have strong existing and projected growth, and also because they have characteristics that make them unlikely to engage in offshoring as they grow.
Utilizing PolymerOhio’s specialized industry knowledge and corporate relationships, the program will facilitate early identification and optimized development of leads. Ultimately, economic development representatives will finalize negotiations with prospective companies.
Plastics Industry Activity: State Rankings
Plastics Industry Jobs | Plastics Industry Shipments | ||||
State | Number of Jobs | Rank | State | ||
1 | | 99,000 | 1 | | 49.5 |
2 | | 90,000 | | 26.8 | |
3 | | 82,000 | 3 | | 25.9 |
4 | | 78,000 | 4 | | 23.0 |
5 | | 71,000 | 5 | | 22.6 |
6 | | 58,000 | 6 | | 19.4 |
7 | | 58,000 | 7 | 17.4 | |
8 | | 39,800 | 8 | | 16.0 |
9 | | 39,400 | 9 | | 11.7 |
10 | | 39,000 | 10 | | 11.6 |
Note: The data in this table comes from a 2006 survey conducted by the Society of the Plastics Industry (www.plasticsindustry.org). The Society estimates that the total U.S. employment in the plastics industry is 1.1 million, and that the total value of U.S. plastics industry shipments is $379 billion.