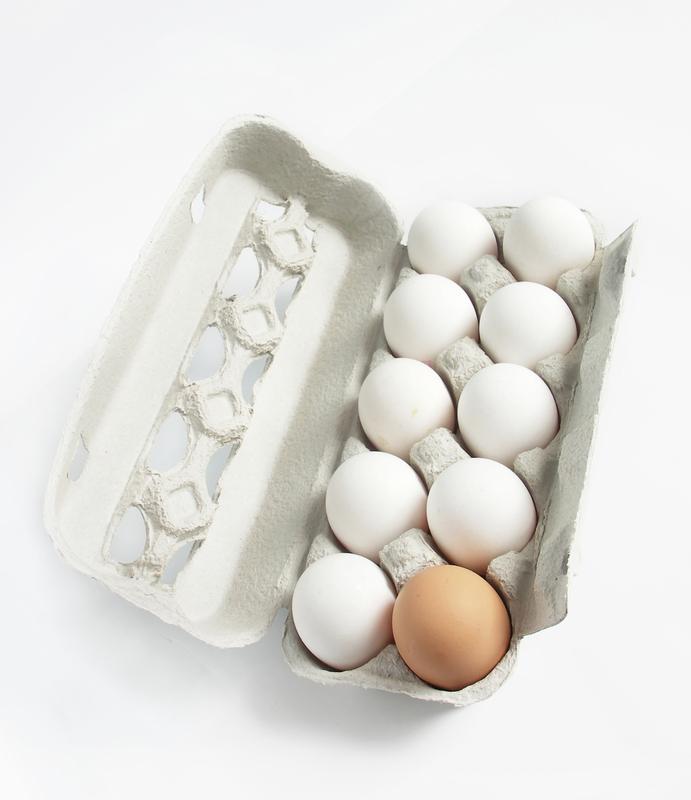
Kroger is opening a 50,000-sq.-ft. facility in Louisville that will collaborate with a high-tech customer fulfillment center (CFC) hub in Monroe, Ohio, to fulfill online orders of fresh food. The DFC model, introduced in partnership with U.K.-based online grocer Ocado in May 2018, combines vertical integration, machine learning, and robotics with affordable and fast delivery service for fresh food, reports Chain Store Age. The new Louisville facility is expected to become operational later this year and will employ up to 161 full-time workers.
"We're proud to expand the Kroger fulfillment network to Louisville," said Gabriel Arreaga, Kroger's senior VP and chief supply chain officer. "The new service is an innovative addition to the expanding digital shopping experience available to Kroger customers. The network's delivery spoke facility will provide unmatched customer service and improve access to fresh food in areas eager for the variety and value offered by Kroger direct to their homes."
Kroger says its CFC facilities leverage proprietary technology solutions focused on artificial intelligence (AI) and advanced robotics and automation to create more seamless and efficient fulfillment, picking and delivery capabilities for enhanced digital commerce capabilities across the U.S. Through the delivery network, the company now serves customers in Florida, as an example, without traditional brick-and-mortar stores.
CFC also represents one of the models engineered for the grocer’s flexible, vertically integrated Kroger Delivery network, which also includes smaller automated facilities and spoke locations, such as the new Louisville facility. In CFCs, more than 1,000 robots traverse giant 3D grids, orchestrated by proprietary air-traffic control systems in the unlicensed spectrum. The grid, known as The Hive, contains totes with products and ready-to-deliver customer orders.
As customers' orders near their delivery times, the robots retrieve products from The Hive, which are presented at stations for items to be sorted for delivery via an algorithmic sorting process. For example, fragile items are placed on top, bags are evenly weighted, and each order is optimized to fit into the fewest number of bags, reducing plastic use.
Once completed, orders are loaded into a temperature-controlled Kroger delivery van, which can store up to 20 orders. Machine learning algorithms dynamically optimize delivery routes, considering factors like road conditions and optimal fuel efficiency.
Kroger unveiled the Monroe fulfillment center in April 2021, its first, followed by others in Groveland, Fla. and Forest Park, Ga. (Atlanta). Earlier in January 2022, Kroger opened a smaller automated center in Indianapolis, which is also connected to the Monroe facility. The fulfillment network plans additional sites in California, Dallas, Forest Park, Ga. (Atlanta), Frederick, Md., Phoenix, Pleasant Prairie, Wis., Romulus, Mich. (Detroit), as well as South Florida and the Northeast.
“Kroger Delivery underpins the permanent shift in grocery consumer behavior and elevates our position as one of America's leading e-commerce companies," said Kroger Chairman and CEO Rodney McMullen.