
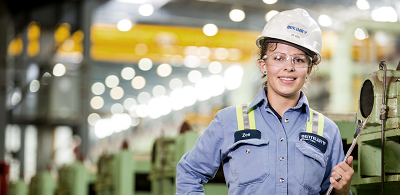
In a U.S. reshoring index published by A.T. Kearney at the end of 2015, the consulting firm concluded that reshoring of manufacturing activities to the U.S. may have been an aberration, peaking in 2011, rather than a sustained trend. A.T. Kearney, however, did recognize a rising tide of foreign direct investment projects that – while not technically reshoring – represent a strong movement by foreign manufacturers into the domestic market.
Foreign direct investment (FDI) companies are drawn by proximity to a huge U.S. consumer market and the stability of the U.S. political and economic climates. And, say A.T. Kearney partners Patrick Van den Bossche and Pramod Gupta, foreign manufacturers are eager to tap into American engineering skills and manufacturing know-how. That interest – coupled with the reality that for every 12 cents of offshore production, there is $1 in U.S. manufacturing output – places a high premium on the continued relevance of U.S. manufacturing.
It’s a future for which Louisiana is well-prepared.
The Workforce Challenge
In the competition for manufacturing investment, job one may be the jobs themselves. Nations, states and regions that position themselves with a well-trained workforce and well-conceived plans for mobilizing workers often advance to the front of the site selection line.
In Louisiana, the workforce differentiator is LED FastStart® OpportunityLouisiana.com. Recognized for its innovation, effectiveness, flexibility and efficiency, LED FastStart, The Economist said,“Probably the most notable statewide workforce-development initiative comes from Louisiana. Its FastStart program, launched in 2008, helps companies recruit and train workers.”
FastStart operates within Louisiana’s economic development agency – LED – and provides comprehensive recruitment, screening, training and orientation services at no cost to eligible companies, including manufacturers that create at least 15 new jobs.
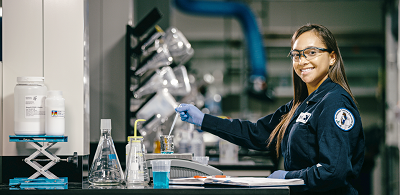
Nonmanufacturers that create at least 50 new jobs benefit from FastStart’s expertise as well. When FastStart helped launch a video game test center in Baton Rouge, Louisiana’s work so impressed EA that the digital entertainment publisher adopted LED FastStart training protocols worldwide. By immersing themselves in client culture and mission objectives for new projects, LED FastStart leaders become an adjunct of the companies’ own human resources department, moving as fast or often faster than the speed of business.
Neither the pace nor the performance are qualities companies expect from government agencies.
“I was blown away with FastStart’s flexibility and their capability to customize,” said Tom Yura Sr., the senior vice president and general manager for BASF’s chemical facilities in Geismar, Louisiana, the company’s largest manufacturing site in North America with nearly 2,000 employees and 22 production units.
Although BASF has operated in Louisiana for six decades, Benteler Steel/Tube entered the state four years ago with news of a $975 million manufacturing investment in a seamless steel tube mill and mini-steel mill. Louisiana and local partners funded a $22 million Center for Advanced Manufacturing and Engineering Technology to train 675 workers for the 1.4 million square-foot plant in Shreveport. Located at nearby Bossier Parish Community College, the center provides comprehensive training on state-of-the-art machinery designed to Benteler specifications.
“FastStart has been very instrumental in helping us to find the right employees and develop training,” said Tim Erway, chief operating officer for the Benteler Steel/Tube site in Shreveport.
A similar advanced training center, funded by the state at SOWELA Technical Community College, will help train 500 new chemical manufacturing workers at Sasol’s $11 billion ethane cracker complex in Lake Charles in Southwest Louisiana. FastStart, through its partnership with the Louisiana Community and Technical College System, has guided development of the advanced training centers, which also will be deployed for training other manufacturers’ employees in each region after their initial training mission is complete.
Harnessing Human Resources
LED FastStart, along with its education and workforce partners, recognizes that long-term strategies must address capacity: “Will Louisiana be able to provide enough skilled manufacturing workers?” is a question already being answered.
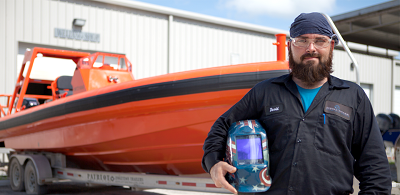
At the secondary level, FastStart provides the C4M curriculum to a growing number of campuses – 50, so far – where students may graduate from high school with a completed, dual-enrollment manufacturing certificate in Louisiana’s Jump Start program.
For expanding manufacturers – including FDI projects like Benteler, Drax Biomass and Sasol – FastStart customizes a unique recruiting, screening and training plan that delivers advanced college graduates and post-graduate professionals, in addition to skilled technicians.
Louisiana recently highlighted its manufacturing initiatives in a custom website, DreamItDoItLa.com, that collaborates with the Manufacturing Institute’s national Dream It. Do It. campaign. Employees in Louisiana’s manufacturing sector are bullish on their profession and proud of the training that helped them land manufacturing careers.
“I’m guaranteed to always be challenged at my job,” said Zoe Rusch, a junior processing engineer for Benteler Steel/Tube. “I’m proud that I’ve helped take a startup mill that didn’t exist a few years ago and made it thrive. Every day, I leave work with the sense that I made a real, concrete improvement – and I’m so proud of that.”
Sasol chemist Jamie Thibodeaux agrees: “More and more women are going into manufacturing. As a young woman, that motivates me to push forward and learn as much as possible. Learning new things and solving new problems every day … had shaped me into a leader that isn’t afraid of failure.”
Louisiana workers value the financial security their industry provides – manufacturers, on average, pay about one-third more than service jobs in the state – but the creative qualities of their jobs also rank high. David Morgan is a mechanic for Jeanerette-based Metal Shark Boats, which manufactures boats for the U.S. Coast Guard, law enforcement agencies and other customers.
“I value when people look up to me for guidance and teaching, so I would like to have my own crew and continue to teach others the knowledge and skills that I’ve learned,” he said.