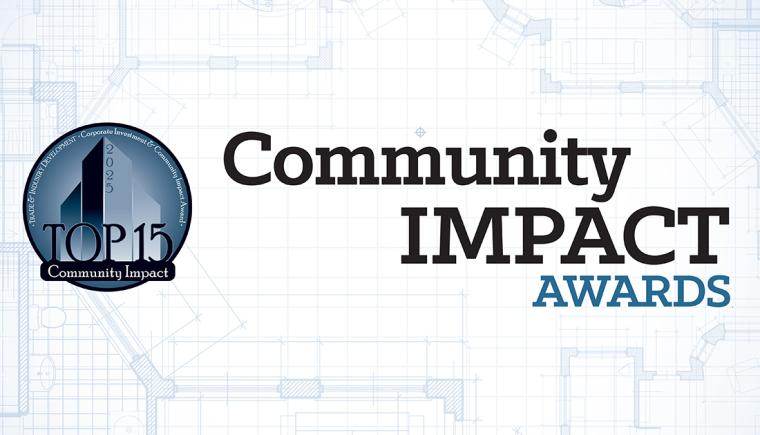
While our Corporate Investment CiCi Awards rank projects by raw capital numbers, the Community Impact side of the awards allows us to highlight more than just monetary value. These are projects that create much-needed jobs in economically distressed areas, or those that retain jobs when another company closes down. They may be projects that reshore manufacturing to the U.S., or those that encourage clean energy. Readers will notice that the capital investment numbers on these projects are smaller, but because they are the right project in the right place at the right time, they have an enormous positive impact on the communities in which they are located.
For the 19th annual CiCi Awards for Community Impact, Trade & Industry Development is recognizing 15 projects announced in 2024 that demonstrate how site selection can make a large difference in a community, providing jobs and opportunities.
The collective capital investment of our 15 winning projects totals nearly $3.7 billion, and these initiatives will create and/or retain more than 17,700 direct jobs. While these numbers may seem small compared to the projects on the Corporate Investment side, the projects are helping to stabilize communities in need of employment, infrastructure improvement, education opportunities and economic independence.
The following are some of the inspirational stories behind our 2025 CiCi Community Impact winners. None of these projects, of course, would have been possible without the hard work of community leaders, local and state economic developers, along with the visionaries at the companies themselves. Congratulations to the winners.
Dow Chemical Company
Midland, Midland County, Michigan
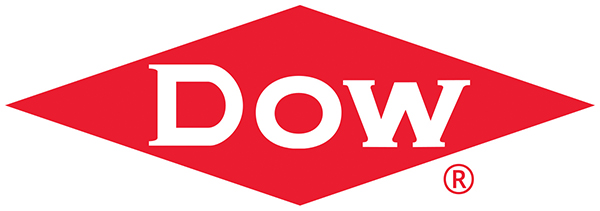
In July of 2024, Dow Chemical Company announced plans to modernize its Michigan Operations Industrial Park in Midland and its Auburn Operations facilities in Williams Charter Township. The modernization project, which involves a $785 million capital investment in the Michigan Operations Industrial Park, will secure the region as a hub for advanced manufacturing and sustainable technology development. The renovations and upgrades will retain 5,000 full-time positions in the community with competitive benefit packages.
The project attracted a number of financial incentives, including a $120 million Critical Industry Program performance-based grant. In addition, it was awarded an estimated $454,450 through a 15-year 100 percent State Essential Services Assessment Exemption, which reduces or waives taxes for manufacturers investing in Michigan, and a 10-year extension with additional parcels for the designated Renaissance Zone, a special area where businesses and residents can enjoy a virtually tax-free zone.
Michigan proved to be the ideal location for this significant investment because of its supportive business climate, skilled workforce and a competitive closing fund in its economic development toolbox. The Michigan Economic Development Corporation worked with the Midland Business Alliance, Bay Future, the City of Midland and Williams Township to craft a solution that supplemented Michigan’s strengths as a site.
The work on the Michigan Operations Industrial Park will begin this year, and the site will remain in full operation through to the project’s completion in 2032. The project will modernize the water and sewer systems to remain up to the task of supporting world-class manufacturing operations. These upgrades will incentivize existing tenants to reinvest and attract new customers to the facility and the greater area.
On a community scale, the successful execution of this project wards off the potential for a $36.7 billion reduction in community-wide personal income that could be lost over the next 20 years were Dow to prioritize investments outside of Michigan. The company has a long-standing history of supporting local K-12 schools, high school co-ops, college internships and numerous community initiatives.
“Continued investments and commitment by an innovative company like Dow will continue to pay high dividends for the people of Williams Township, Bay County and the State of Michigan. Investment by state-of-the-art companies like Dow will help bolster our economic future and growth for years to come,” said Jim Reaume, president and CEO of Bay Future, Inc.
Toyota Motor Manufacturing, Indiana, Inc.
Princeton, Gibson County, Indiana
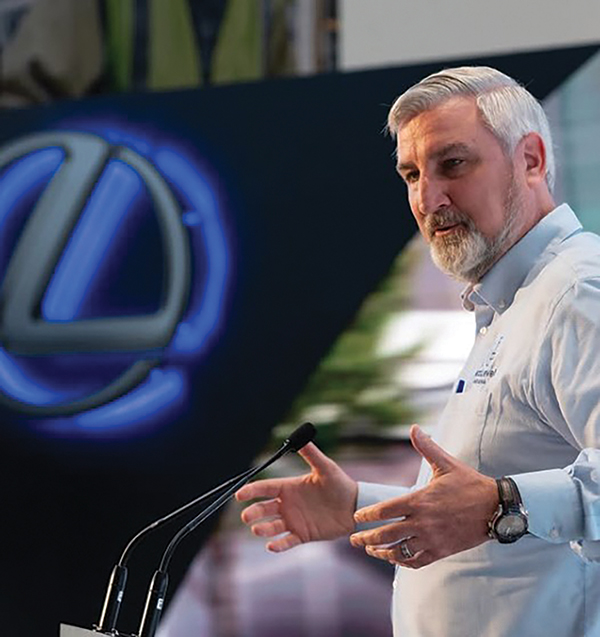
In April of 2024, Toyota Motor Manufacturing, Indiana Inc. announced that it plans to assemble an all-new battery electric vehicle (BEV) plant in Indiana, investing $1.4 billion at its Princeton facility and bolstering the state’s leadership in the future of mobility.
The company’s investment will provide new plant infrastructure, including a new battery pack assembly line at the facility, to support production of the all-new battery electric SUV at Toyota Indiana. To support its growth, Toyota plans to create up to 340 new jobs by the end of 2025. The company already employs more than 7,500 associates in southwest Indiana to support production of the Toyota Sienna, Highlander, Grand Highlander and the Lexus TX.
Toyota broke ground on its Princeton plant in 1996 and has since been a leader in Indiana’s automotive industry while creating new jobs and training opportunities for workers. In addition, the company has played a significant role in advancing quality of place and quality of life in the southwest Indiana region.
Through READI, Toyota is supporting transformative projects, including the new Toyota Indiana YMCA in Princeton and The District housing complex in Princeton, to provide access to health and wellness, community support and housing for all residents while helping employers like Toyota and its suppliers attract even more talent to the region.
The Indiana Economic Development Corporation (IEDC) committed an investment in Toyota of up to $5 million in incentive-based tax credits and up to $1 million in conditional structured performance payments based on the company’s plans to invest $632 million. These incentives are performance-based, meaning the company is eligible to claim state benefits once investments are made.
“Indiana and Toyota share a nearly 30-year partnership that has cultivated job stability and economic opportunity in Princeton and the surrounding southwest Indiana region for decades,” said former Indiana Governor Eric Holcomb. “Toyota’s investment in the state began with an $800 million commitment and has grown to over $8 billion. Indiana proudly looks forward to continuing to being at the center of the future of mobility.”
Delta Electronics
Plano, Collin County, Texas
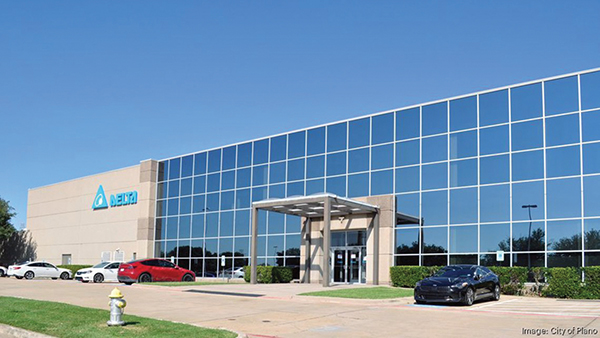
In December of 2024, Delta Electronics, Inc., a Taiwan-based power management company and a provider of Internet of Things (IoT)-based smart green solutions, disclosed plans to expand its campus in Plano, Texas after a competitive bid that evaluated various sites. The company reports nearly $13 billion in annual revenues and a robust workforce of over 18,000 employees across operations worldwide, including an existing 435,000 square foot advanced R&D and manufacturing facility in Plano focused on developing smart energy-saving solutions for AI and cloud data centers, telecom networks, EV charging and other technologies.
With the new $452 million project, Delta Electronics plans to expand its existing facility to 1.5 million square feet in two construction phases. After evaluating various sites across multiple states, Delta Electronics ultimately decided that Plano would be the ideal location, choosing to make its relationship with the City of Plano a lasting one. Between the existing facility and planned expansion, Delta Electronics will employ over 1,500 Texans in the North Texas region.
The project marks the largest manufacturing project in Plano’s history and is expected to encourage the continuation of outstanding city services to residents and businesses alike. Bolstering an estimated 5,000 hotel stays annually, the impact of out-of-state visitors to the local economy is expected to increase.
To attract the project, the City of Plano and Plano Economic Development offered the company tax rebates for 15 years on Real Property and Business Personal Property taxes (city’s collection only). This resulted in a total cash grant of $5,873,000 ($1,973,000 in permit/fee rebates, $3,900,000 in job grants).
As sustainability is of critical importance to the company, Delta’s new campus is expected to transform the area in an eco-conscious way and create a major employment center, bringing a mix of vibrancy and furthering opportunities for retail and dine-in options for the region.
“We understand how critical it can be to choose a location for a company’s operation, especially one of this size, and feel proud that Delta Electronics agrees that Plano offers the resources and partnership to build a lasting relationship,” said Plano Mayor John Muns.
Topsoe
Chester, Chesterfield County, Virginia
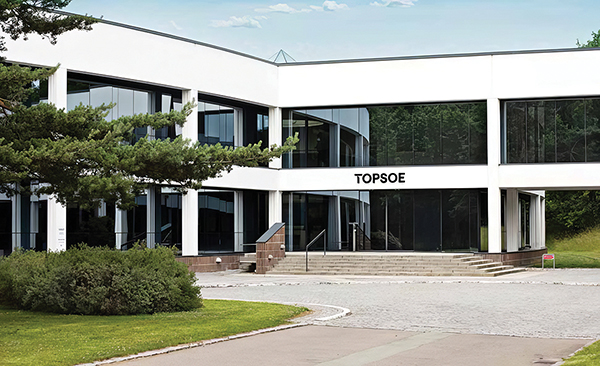
In May of 2024, Topsoe, a Danish manufacturer of carbon emission reduction technologies, announced plans to invest more than $400 million to build a factory at Meadowville Technology Park in Chesterfield County, Virginia. The new facility will manufacture Solid Oxide Electrolyzer Cells (SOEC), which are essential for producing clean hydrogen. Though the company considered several markets for its new 280,000-square-foot electrolyzer factor, it ultimately chose the Greater Richmond area for its support of both clean energy initiatives and international operations.
With the new facility, Topsoe will create 150 new jobs and launch a scholarship program that will recognize five Chesterfield County high school seniors with $10,000 awards annually to foster the next generation of leaders in clean energy. Topsoe’s investment aligns with Greater Richmond and Virginia’s decarbonization efforts and bolsters the region as a hub for clean energy.
The Commonwealth of Virginia awarded Topsoe $6 million from the Commonwealth Opportunity Fund. The Greater Richmond Partnership, Chesterfield Economic Development and the Virginia Economic Development Partnership (VEDP) worked together to secure the project. VEDP’s Talent Accelerator Program will help Topsoe hire and train new employees.
In addition to boosting jobs and capital investment in the region, Topsoe’s work will further sustainability initiatives in Greater Richmond and Virginia. The project is also eligible for benefits from The Port of Virginia Economic and Infrastructure Development Zone Grant Program and Federal tax credits under the U.S. Department of Energy’s Qualifying Advanced Energy Project Credit.
Topsoe’s investment is expected to positively impact the region for many years to come. The company’s $400 million investment will support needed community services throughout Chesterfield County and its 150 newly created jobs will enhance economic mobility for many residents and their families. The project is also expected to create 437 indirect employment opportunities, a total labor income of $34.9 million, a value add of $70 million and nearly $200 million in output or business sales.
“Topsoe’s $400 million investment in a clean energy facility is unlike anything the region’s seen from an international firm,” said Jennifer Wakefield, President and CEO of the Greater Richmond Partnership. “Coupled with 150 new jobs and STEM scholarships, Topsoe is poised to become a partner for social good in the Richmond Region and beyond.”
Hemlock Semiconductor
Hemlock, Saginaw County, Michigan
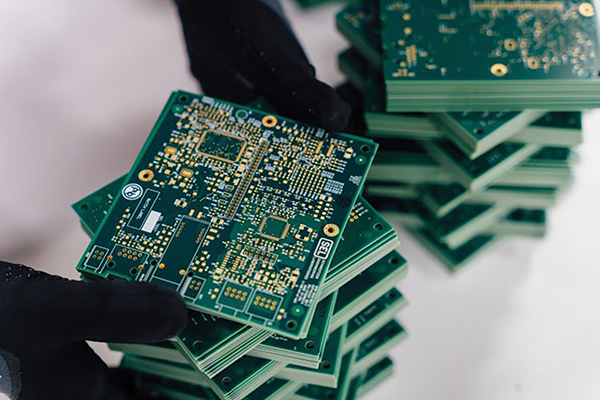
In October 2024, Michigan-based manufacturer Hemlock Semiconductor (HSC) announced plans to build a new facility supporting 180 permanent, advanced manufacturing jobs. The proposed direct funding to the project was made under the Biden-Harris administration’s bipartisan CHIPS and Science Act, which is focused on bringing vital supply chains and good-paying, cutting-edge jobs home to the U.S.
In addition to the $325 million proposed direct funding from the CHIPS and Science Act, the project has attracted $40 million from the Make It in Michigan Competitiveness Fund, which was specifically designed to bring in federal funds from the CHIPS Act and the Inflation Reduction Act.
HSC has been a cornerstone of the Saginaw community for years, and winning federal funds for its expansion in Michigan further builds on its foundation for long-term growth. According to the state, the landmark deal demonstrates how years of careful groundwork enabled Team Michigan to move quickly when a once-in-a-generation opportunity emerged, thanks to the work of its legislature, state departments and local development organizations.
In addition to federal and state funding, the project is attracting a $27 million performance-based grant to significantly expand sanitary sewer capacity at the Thomas Township site through the Strategic Site Readiness Program, $10 million in legislative appropriations for Saginaw Township to support the project and a $650,000 grant to the Saginaw Road Commission from the Michigan Department of Transportation’s Transportation Economic Development Fund, which supports immediate highway needs related to development projects. HSC-majority owner Corning Inc. has already committed $900 million to build a solar components facility nearby that will use HSC as a core supplier.
The funding will not only support HSC’s growth, but also build a thriving domestic supply chain, helping to attract additional companies and their engineers, researchers and suppliers to support the region’s growing semiconductor and tech industries. The company is already a partner in developing educational programs and working with scholarship recipients alongside institutions including Kettering University, Michigan State University, Lansing Community College and Delta College. HSC has joined the MI Tri-Share program, which shares the cost of childcare with employees and the State of Michigan. HSC is also a vocal supporter of the state’s MI Healthy Climate Plan, which aims to create jobs while protecting the environment.
“Lowering the cost of clean energy for industrial users and delivering carbon-neutral fuels by 2050 will help create a more competitive business environment in Michigan and support HSC’s continued growth and success as the nation’s leading manufacturer of ultra-low carbon polysilicon for the semiconductor and solar energy industries,” said Steven Holty, HSC Sustainability Leader and co-chair of the Energy Intensive Industries Workgroup for the Council on Climate Solutions.
Walmart
Robinson, McLennan County, Texas
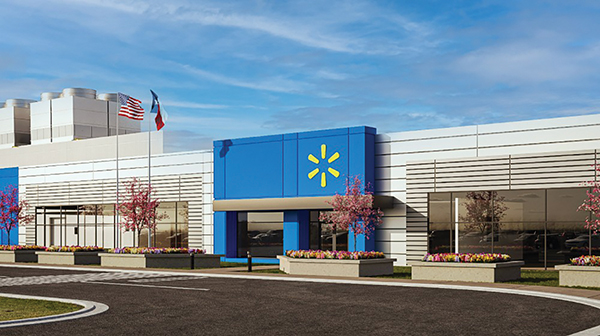
In March of 2024, Walmart announced it will expand its presence in Texas with a new milk processing facility in Robinson. The project is expected to generate nearly 400 new jobs and $350 million in capital investment. Walmart’s investment in Robinson will not only grow the Texas economy as a whole but will also support the local economy.
The company’s new milk processing facility in Robinson will exist as a hub to serve more than 750 Walmart stores and Sam’s Clubs in states across the U.S. including Texas, Oklahoma, Louisiana and parts of Arkansas and Mississippi. The facility will process and bottle a variety of milk options for Walmart’s Great Value and Sam’s Club’s Member’s Mark brands. With milk supplied directly from Texas dairy farms, this farm-to-processing approach is expected to streamline the company’s operations while also bolstering local and regional food and beverage supply chains in Texas. The new facility is slated to open in 2026 and will be the company’s third milk processing facility in the U.S.
The city provided the project with infrastructure and property tax incentives through 380 agreements. In addition to creating jobs, the new project will put the Robinson area on the map for industrial and manufacturing activities. It is also the first large project in the Robinson Business Park and will serve as a catalyst for the development of the remainder of the business park.
“This monumental investment is the first of its kind in both size and value for the area, signaling a transformative era for Robinson,” said Bert Echterling, former Mayor of Robinson. “This project serves as an example for other similar towns across the county and the state that it’s possible to compete for (and win) high-impact projects, transforming the community for generations to come.”
AAON, Inc.
Memphis, Shelby County, Tennessee
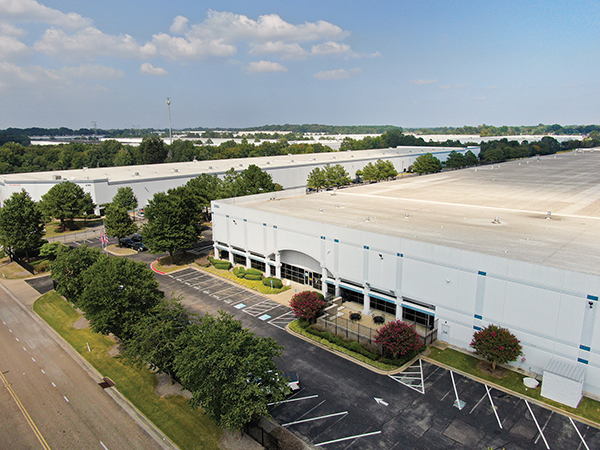
In November 2024, Tulsa-based HVAC manufacturer AAON, Inc. announced plans to expand its presence to Tennessee. For the $238 million expansion, the company chose the former American Snuff facility in Memphis, a move that is expected to create 830 new jobs. The project is now one of the top three largest economic development wins in Shelby County in the last decade based off net new jobs. Additionally, AAON’s decision to locate in Memphis and Shelby County represents the number one largest manufacturing project to locate in the community in the same time frame. Both statistics underscore that this project marks a transformational opportunity for the region.
The new 787,000-square-foot Memphis facility will produce advanced thermal management equipment under the BASX brand, including air-cooled systems, computer room air handlers (CRAHs), direct evaporative coolers and liquid cooling distribution units. These systems will be critical in supporting multibillion-dollar data centers and AI-driven facilities being developed across the country, including xAI in Memphis.
AAON’s new production facility will generate substantial economic activity in Shelby County and breathe new life into a historic building in Memphis. The project will also provide a variety of employment opportunities to families across the region, allowing them to live and work within the same community.
To attract the project, Tennessee Valley Authority offered a performance training grant, TNECD awarded AAON an economic development grant through the department’s FastTrack funding and the City of Memphis awarded a 15-year PILOT program grant.
“Building a robust recruitment pipeline requires strong relationships with both industry leaders and our economic development partners,” said Memphis Mayor Paul Young. “Welcoming AAON to Memphis represents a significant step toward making our market even more competitive on a national level. With AAON’s commitment, we are enhancing our local economy and elevating Memphis as a destination for high-quality jobs and sustainable industry growth.”
Type One Energy Group, Inc.
The Greater Knoxville Region and Clinton,
Anderson County, Tennessee
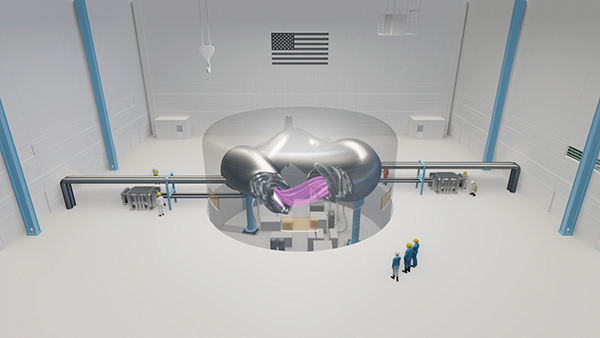
In 2023, Tennessee Governor Bill Lee introduced the $50 million Nuclear Energy Fund through Executive Order 101 as part of a strategy to recruit sustainable energy companies and reduce the state’s dependence on foreign energy sources. The fund, approved by the Tennessee General Assembly in the 2023-2024 budget, marked a proactive yet natural approach for Tennessee to strengthen its nuclear energy ecosystem by offering financial incentives to nuclear power-related businesses relocating or expanding in Tennessee. The fund also incentivizes nuclear programs at Tennessee’s higher education institutions.
In February 2024, less than a year after the fund’s creation, Tennessee landed its first major nuclear-related company: Type One Energy. The project represents a combined investment of $223.5 million to establish Type One’s headquarters in the Greater Knoxville region and expand its fusion R&D operations to Anderson County. The company is creating 330 new jobs across the two locations, and these jobs will span various roles in fusion research and development and headquarters-related jobs. Both opportunities will offer what the department considers to be highly skilled positions, offering well above the county median.
Upon completion, the company will house its stellarator fusion prototype machine, Infinity One, at TVA’s Bull Run Fossil Plant in Clinton. This aligns with Tennessee’s commitment to energy independence and positions the state as a leader in clean energy innovation.
As the first recipient of funding from Tennessee’s Nuclear Energy Fund, Type One Energy’s relocation has the potential to attract additional investments and companies in the nuclear sector, advancing the state’s position in this industry and increasing local economic development.
Type One Energy received a $4.5 million grant from Tennessee’s Nuclear Energy Fund. These grant dollars are awarded through TNECD. In terms of federal incentives, the company received a Tennessee Valley Performance Grant. Anderson County also proposed a 12-year 50 percent tax abatement that is subject to approval.
“With assets like Oak Ridge National Lab, Tennessee is the quintessential location for companies like Type One Energy to grow and succeed,” said TNECD Commissioner Stuart C. McWhorter. “This project will not only strengthen Tennessee’s R&D footprint but also further develop our nuclear sector, which wouldn’t be possible without the forethought of Governor Bill Lee and our Tennessee General Assembly to create the Nuclear Energy Fund.”
Laepple Automotive
Detroit, Wayne County, Michigan
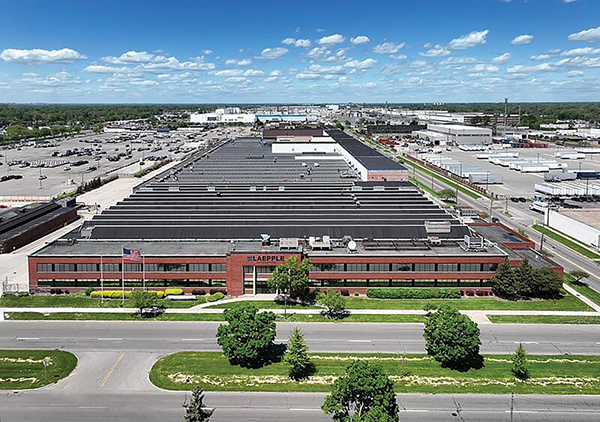
In September of 2024, Laepple Automotive, the U.S. entity of German auto parts manufacturer LÄPPLE AUTOMOTIVE, debuted plans to establish its new U.S. headquarters and main operations in the City of Detroit. The project is expected to create up to 173 new jobs and $93.4 million in capital investment in Detroit, solidifying the company’s presence in the state while adding to Michigan’s robust automotive industry. The company was attracted to Michigan’s legacy in the automotive industry as well as its existing ecosystem of mobility companies as potential partners.
The project, according to the state, is built on a successful partnership in the making. An unrelated entity, METD Detroit, Inc., will purchase the long-vacant, 428,000-square-foot Mount Elliot Tool and Die facility that Laepple Automotive will call home. As a result of Laepple Automotive’s rental agreement, METD Detroit can commit to significantly rehabilitating the facility, with improvements and modifications to the structure itself and the installation of state-of-the-art automotive manufacturing equipment.
The historic manufacturing site has already served the industry for over 80 years, and its location in Detroit gives Laepple Automotive a strong position for future growth: the company is already building new OEM partnerships in the auto industry. The new building owner, METD Detroit, Inc., will also occupy a portion of the building, creating additional jobs.
The site is located in a Geographically Disadvantaged Area, with an unemployment rate higher than the state’s overall rate. To help attract the project, the state and city offered the company a $3.5 million Michigan Business Development Program performance-based grant, a five-year 100 percent SESA Exemption with an estimated value of up to $653,760, a $474,687 Detroit at Work training and talent recruitment proposal, an estimated $22,000 from the Detroit Regional Partnership through promotional videos and other in-kind support.
The facility will offer in-house training programs for Laepple Automotive’s employees. This dedicated area will begin as a training ground for the company, with plans to extend training and certification to others in the industry.
“Laepple Automotive is recognized internationally for their advances in forming sheet metal and car body assembly,” said Maureen Donohue Krauss, CEO and president of the Detroit Regional Partnership. “They’ve helped bring life back to older industrial facilities in Germany, which we were recently able to tour, and we’re excited for them to do the same at the former Mt. Elliott facility in Detroit. We were happy to partner with the MEDC and DEGC to successfully make the case for Michigan and the Detroit Region as the best place for Laepple to establish a new presence and grow in North America.”
Home Market Foods
South Windsor, Hartford County, Connecticut
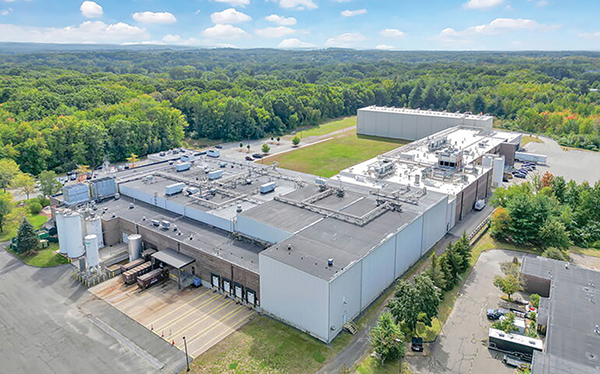
Home Market Foods, a Boston-based provider of premium food products for over 50 years, was recently looking to expand into a new facility to increase its meatball production line. The company’s needs were specific and immediate. Connecticut economic development agency AdvanceCT was able to point Home Market Foods toward a facility in South Windsor, outside of the state capital Hartford, that had formerly been occupied by Carla’s Pasta, a subsidiary of Tribe 9 Foods, which had made specialty pastas up until the company began bankruptcy proceedings in 2023. The 148,000-square-foot facility was slated to be sold and most likely shuttered, with all of its approximately 140 employees set for termination.
Representatives from Home Market Foods toured the facility and found that it was perfectly suited to the organization’s needs. As the plant was already an FDA-approved site, Home Market Foods would be able to begin production nearly immediately without the need for regulatory approval processes. The company purchased the site and committed more than $70 million to its transformation and expansion. Additionally, Home Market Foods committed to hiring back nearly all of the former Carla’s Pasta workers for the new plant, preventing the economic blow the closure threatened to bring to the town.
While saving 140 jobs, Home Market Foods also committed to creating 70 new jobs to fill out its production lines. Home Market Foods was attracted to the region’s wide availability of skilled labor, Connecticut’s business climate, proximity to distribution channels and support from the state and town of South Windsor.
“There is no shortage of location options for companies like Home Market Foods to consider, so I am delighted that they chose Connecticut and chose to bring their business to our state,” said Connecticut Governor Ned Lamont. “I would like to acknowledge the many organizations that helped present Connecticut’s value proposition to Home Market Foods during this process; Connecticut’s DECD, AdvanceCT, Mayor Audrey Delnicki of South Windsor, Eversource and MetroHartford Alliance. Team Connecticut was in full effect on this project, and we are thrilled with the outcome.”
Quaker Windows and Doors
Eldon, Miller County, Missouri
In May of 2024, manufacturing company Quaker Windows and Doors announced plans to expand its Eldon, Missouri manufacturing facility, investing more than $30 million and creating 220 new jobs. The company’s expansion will add a vertical paint line and increased capabilities for insulating glass production while helping meet demand for its commercial, residential and luxury windows and doors. With the expansion, Quaker will increase its manufacturing capacity, adding 300,000 square feet to its existing 450,000-square-foot campus.
The original phase for the company’s Eldon facility was completed in 2020. The location has now received three additions in four years, bringing its total space to nearly 800,000 square feet. The latest expansion includes the installation of a state-of-the-art vertical paint line to increase powder paint capabilities. Quaker is also expanding its insulating glass production and adding tempering capabilities to better meet the needs of its customer base.
Quaker’s expansion continues to generate new employment opportunities in central Missouri. The company is one of the leading employers in the Eldon area and has brought positive effects to the community. To attract the project, the Missouri Works Program offered the company up to $2,525,761 in tax withholdings and sales exemption for machinery, equipment and energy.
“We’re thrilled to see Quaker continuing to grow and create even more opportunities in Eldon,” said Michelle Hataway, Director of the Department of Economic Development. “As a longstanding community partner and quality employer, Quaker’s success in central Missouri is helping Missourians prosper. Our team is grateful to support this leading manufacturer alongside our partners as it embarks on the next chapter of its inspiring story.”
ES Foundry
Greenwood, Greenwood County, South Carolina
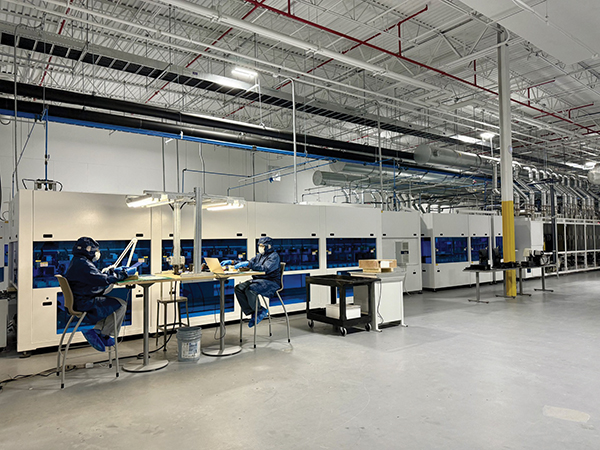
In August 2024, ES Foundry, an American company engaging in the onshoring of crystalline solar cell production, announced plans to open a manufacturing facility in Greenwood, South Carolina. The company converted more than 400,000 square feet into a state-of-the-art facility in less than eight months, holding its grand opening event in January of 2025. Hiring began in August 2024 and is expected to top 500 employees by July 2025.
ES Foundry is the first new industry to move into the campus formally occupied by Fujifilm, which downsized operations in 2022, eliminating 400 jobs. Once fully operational, the facility will have a shipment capacity of 3 GW by the third quarter of 2025, making ES Foundry the largest producer of crystalline silicon photovoltaic (PV) solar cells in the U.S.
By bringing production back to the U.S., the company is reducing reliance on foreign supply chains and ensuring a more stable, secure source of critical solar components. The new facility will use bifacial Passivated Emitter and Rear Contact (PERC) solar cell technology, a proven and cost-effective solution that enhances energy efficiency and long-term durability. Unlike emerging solar technologies that face scalability and reliability challenges, PERC cells offer a stable and market-ready alternative.
ES Foundry’s arrival in Greenwood County represents a major step forward for the local economy, bringing new jobs and revitalizing a key industrial site. As the first new industry to establish operations at the former Fujifilm campus, ES Foundry is transforming an existing facility into a state-of-the-art solar manufacturing hub. The company is on track to employ 500 area residents by June 2025, the most jobs ever created by a company in its first year in Greenwood.
The ribbon-cutting event was especially meaningful as it came just days after the closure of Ascend Performance Materials, which resulted in the loss of more than 200 jobs in the community. Many of the newly hired ES Foundry employees previously worked at Ascend, finding new opportunities in a growing and sustainable industry that is shaping the future of renewable energy.
“A better script couldn’t be written to soften the impact of a manufacturer closing than to retain much of the highly skilled workforce at a new industry just a mile down the road,” said James Bateman, Greenwood County Economic Development Director. “With the end of an era caused by global market shifts in nylon fiber production comes new beginnings in the rapidly expanding domestic clean energy sector.”
Republic Airways/LIFT Academy
Tuskegee, Macon County, Alabama
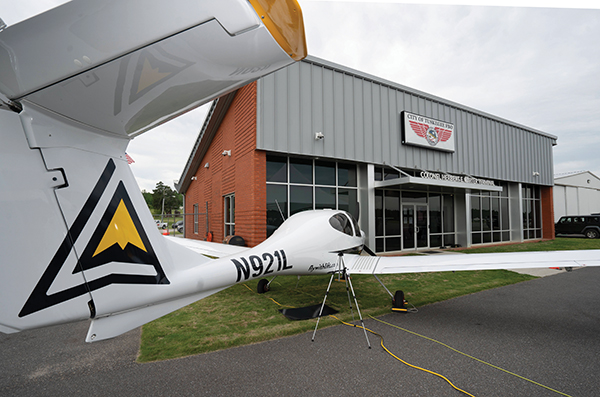
As part of a project announced in March 2024, Republic Airways and its Leadership in Flight Training (LIFT) Academy announced plans to develop an advanced flight training program in Macon County that will prepare the next generation of aspiring pilots on the airfield where the famed Tuskegee Airman learned to fly. LIFT will partner with Tuskegee University and the City of Tuskegee to base the training center at storied Moton Field. The partnership was developed to recruit and educate future African American pilots with first-rate classroom and flight instruction.
As part of the project, LIFT will create 35 full-time aviation-related jobs in Tuskegee over a three-year period, with an average annual salary of nearly $75,000. In addition, 57 certified flight instructors will be involved in the program at Moton Field. The project calls for a capital investment of $27 million for aircraft. In addition, the State of Alabama is providing $6.2 million in job creation and investment credits under the Alabama Jobs Act over a period of 10 years.
Tuskegee University’s new academic program will offer a bachelor’s degree in aviation science (pilot track) with a general education core and aviation-science related courses in aerodynamics, aircraft structures, aircraft propulsion and more. A second component of the program is flight training during which students will be able to take the appropriate FAA certification for private and commercial pilot certificates.
LIFT’s aviation academy in Tuskegee is bringing more than just jobs — it’s tying into the legacy of the city’s historic Moton Field and expanding it to create new career pathways for students at Tuskegee University. The LIFT project is also expected to diversify recent gains in the manufacturing and retail sectors of Tuskegee’s economy and add demand for housing and services that will lift the quality of life for all the county’s citizens.
“A new generation of Tuskegee airmen and women will have the training they will need to serve our country through the military or as commercial pilots,” said Dr. Charlotte P. Morris, president of Tuskegee University. “The new partnership with LIFT and Republic will build leaders and legacies.”
Greenville Manufacturing Kentucky
Greenville, Muhlenberg County, Kentucky
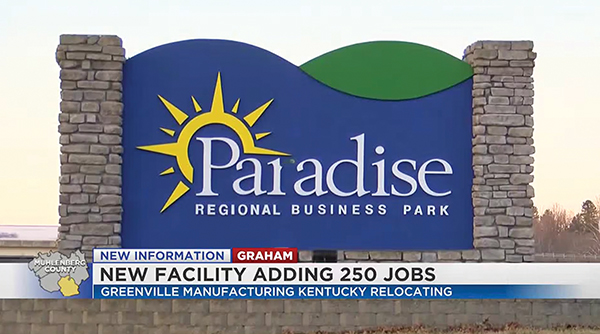
Greenville Manufacturing Kentucky, a maker of equipment for the agriculture, forest products and biomass sectors, announced in December of 2024 that it would be relocating to a new facility in Muhlenberg County, creating 250 new jobs for the community and investing $16.2 million in capital. The project will be the first established at the new Paradise Regional Industrial Park and include new equipment and increased operational space to meet growing consumer demand and company growth. While the company currently operates in a facility in Greenville, the new location will allow for continued growth in sales, outreach into new industries and more in-house manufacturing and less outsourcing.
To encourage investment and job growth in the community, the Kentucky Economic Development Finance Authority (KEDFA) has approved a 15-year incentive agreement with the company under the Kentucky Business Investment program. The performance-based agreement can provide up to $7 million in tax incentives based on the company’s investment of $16.2 million and annual targets of creation and maintenance of 250 Kentucky-resident, full-time jobs across 15 years and payment of an average hourly wage of $26.07, including benefits.
By continuing to invest in a community with high unemployment numbers, Greenville Manufacturing Kentucky is helping boost the economy in the region with a new source of high-paying manufacturing jobs. As the first to locate in a newly formed industrial park, local leaders expect the expansion to draw attention from other interested companies in the region. The project represents a major success for the Kentucky Product Development Initiative, the state’s site development initiative, as the Paradise Regional Industrial Park site was approved for $745,000 in state support in 2023.
“This new facility was earned by the loyal, dedicated employees in Kentucky and the support of the community,” said Dane Floyd, CEO of Floyd Holdings. “Our companies have experienced incredible growth, and we had to decide where to grow next. Starting almost from day one in Greenville, the outreach and support of local leaders really reinforced what a great community we had been welcomed into. With great employees, forward-thinking local leaders, great training facilities and state support all the way to Governor Beshear’s office, Kentucky made my decision an easy one.”
Crucial MRO
Murphysboro, Jackson County, Illinois
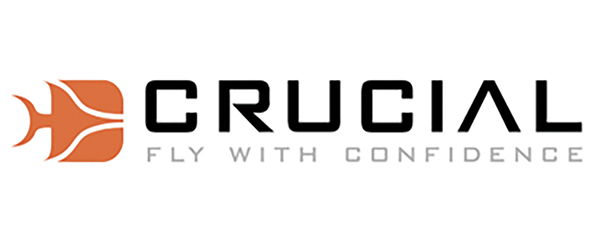
It began with a suggestion voiced from an aviation trade show booth. Southern Illinois Airport’s manager Gary Shafer commented, “You look like you need a new hangar.” Crucial MRO’s Marc and Stacy Burton were the passersby and laughed as Marc replied, “Believe it or not, we were just talking about that!”
That one comment, combined with Southern Illinois’ central location, low cost of living and on-site workforce pipeline through Southern Illinois University Carbondale’s nationally recognized aviation program, led to the Burton’s initial commitment to share hangar space with an existing tenant. Within a short time, the company quickly grew to two of their own hangars as they began centralizing the company’s U.S. operations to this once small regional airport now turned aviation and transportation hub.
Located in Jackson County’s small town of Murphysboro, Illinois (population 7,093), Southern Illinois Airport is now home to Crucial MRO’s rapidly expanding company focused on commercial aviation maintenance, repair and overhaul (MRO) services. The expansion announced in 2024 includes a parts and components shop essential to service and maintenance operations.
Conversations with Murphysboro Mayor Will Stephens resulted in the identification of an existing building (the Curwood Building) within close proximity to existing operations. The revitalization of the building will play an industrial role in the city’s upward growth trajectory. Crucial’s new facility, Crucial Aero Ranch, will have a profound and transformative effect on the City of Murphysboro and the broader Southern Illinois region through job creation and continued expansion of a company that discovered Southern Illinois through a timely trade show interaction and has now made the region home. According to an IMPLAN model from the University of Illinois Extension’s Illinois State Census Data Center, the impact of 45 jobs in the Aviation Support Services industry on the economy of Jackson County equates to more than $4.5 million dollars in annual labor income, nearly $4.4 million in additional value added and more than $7.4 million in annual output.
The City of Murphysboro advanced $200,000 in TIF funding to help facilitate the transfer of the property from the previous owner to Crucial. Additional incentives are available via Jackson County Enterprise zone.
“Beyond the economic benefits, the collaborative spirit and determination to see this project through highlight Southern Illinois’ dedication to attracting companies and supporting their growth, and Crucial’s expansion is a perfect example,” said SI Now Executive Director Deb Barnett. “A win for one is a win for all of Southern Illinois and this win is big for the City of Murphysboro.” T&ID
Related Agencies
- Texas Economic Development Corporation
- Missouri Department of Economic Development
- Greater Indianapolis Foreign Trade Zone/INzone
- AdvanceCT
- Intersect Illinois
- Michigan Economic Development Corporation
- Midland Business Alliance
- Tennessee Department of Economic & Community Development
- Missouri Department of Economic Development
- Greenwood County Economic Developoment
- Alabama Department of Commerce
- Muhlenberg Economic Growth Alliance
- Jacksonville Regional Economic Development Corporation