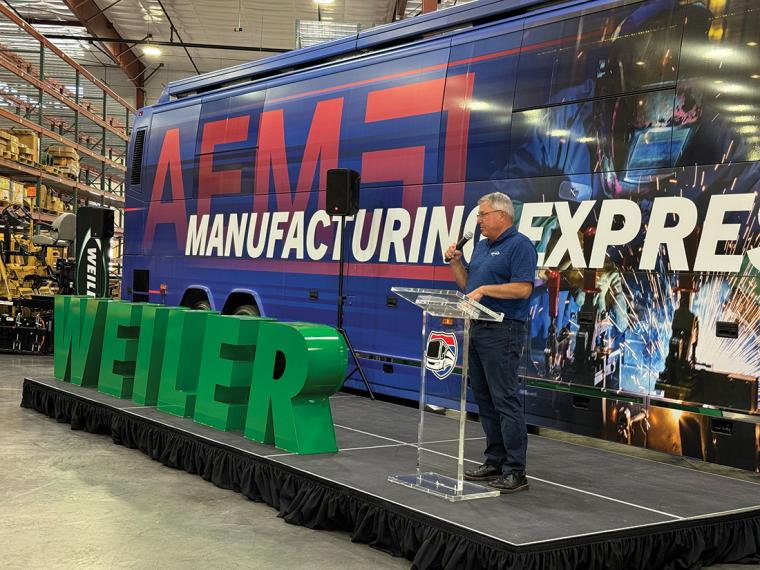
How do you best tell the stories of advanced manufacturing organizations and the best practices they follow to adapt to the new economy? If youíre the Association of Equipment Manufacturers (AEM), you visit the nationís manufacturers.
The AEM’s Manufacturing Express officially kicked off its 10,000-mile cross-country bus tour in Iowa on July 1, 2024, with stops at Weiler in Knoxville in Iowa, Vermeer Corporation in Pella, Iowa and Ring-O-Matic in Pella before making an appearance in the Urbandale, Iowa Fourth of July Parade and a tailgate at an Iowa Cubs game with Two Rivers Marketing and Spindustry.
The AEM Manufacturing Express, which drew manufacturing workers as well as companies, is the most ambitious member engagement initiative in the association’s 130-year history, designed to tell the stories of the men and women who make the equipment that builds, powers and feeds the world.
“Behind every piece of equipment is a story, and we are excited to tell the stories of the 2.3 million men and women of our industry,” AEM President Megan Tanel told the crowd of more than 700 people who had gathered for the launch at Weiler.
Since the first week of July, the AEM’s interactive mobile tour has traveled thousands of miles and made dozens of stops across 14 of 20 states on the route to highlight all the ways in which equipment manufacturing contributes to society today, and how these companies are addressing gaps in the manufacturing workforce.
The numbers help paint a picture of the industry’s impact: 11 percent of manufacturing jobs are supported by equipment manufacturing, which represents 2.3 million workers, and contributes $316 billion to the U.S. gross domestic product annually. From creating family-sustaining jobs and driving innovation to supporting the movement of people and goods and helping to power vital public services and utilities, there is much to celebrate, recognize and admire about the industry.
Numbers Tell Only Part of the Story
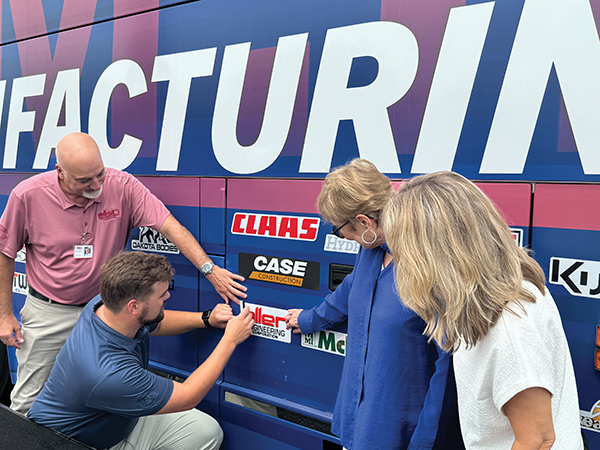
An August stop at Allen Engineering, a concrete equipment manufacturer in Paragould, Arkansas, allowed the team members on the Manufacturing Express to learn about second chance hiring. Allen Engineering Corporation was founded in 1964 by the late Dewayne Allen and Mary Ann Allen, and it continues to rely on a foundational principle: family.
“We hire for attitude, not aptitude,” said President and CEO Jay Allen. “When you are a family-owned business, you have to focus a lot on how you instill commitment among the rest of the people who make up your team — your family. I’m really proud of the way we have built this culture.”
Allen Engineering highlighted the fact that it had offered an employment opportunity to a recovering addict and former felon who had made a concerted effort to turn his life around. Often, candidates with criminal and addiction histories are screened out during the hiring process, but Allen told a story of the company’s decision to take a chance. The young man turned into a hard-working employee and remained on track, leading to Allen Engineering becoming increasingly involved in various local addiction recovery programs.
“If you take the formerly addicted and incarcerated out of the work pool, that’s a significant chunk of the population,” explained Allen. “They’re usually willing to work in the trades and do blue-collar work, and we wanted to tap into that demographic, of course in a way that wouldn’t put our company or other employees at risk.”
The backbone of the program involves a fairly extensive drug screening process. Testing occurs before hiring and randomly throughout the year. Employees (including top management) never know when they will be tested. Word got out quickly that Allen Engineering was a second-chance employer, and at one time the company employed more than 20 recovering addicts.
Finding the Creativity to Attract and Retain Skilled Talent
Allen Engineering, which recently celebrated its 60th anniversary, has evolved and changed from a ready-mix and aggregate producer to designing, manufacturing, distributing and marketing concrete and related equipment that is sold across the world. As a smaller business, the company is aware that it must provide innovative solutions to customers, and uniquely support employees to attract and retain the talent it needs.
Some companies that engage in second chance hiring of individuals with criminal records or addiction histories experience benefits in the form of increased loyalty by workers who received the second chance that started a positive ripple in their lives. The opportunities they receive and the support that is provided to keep them sober allows for many to regain custody of their children and reunite with loved ones and gives them a stable base on which they can build the rest of their lives.
“As a smaller company, we realize that we have to work a little bit harder than everybody else to be able to stay independent, family-owned and American-made,” said Allen. “And I think we’ve found some tactics that allow us to retain good talent and keep making quality products.”
Small and Large Manufacturers Are Evolving the Skillsets for Advanced Manufacturing
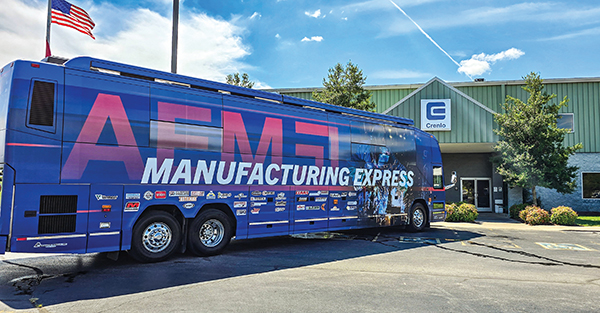
AGCO in Duluth, Georgia is doing big things: both figuratively and literally (in the case of its nine-ton Fendt 700 Vario tractor). Across a worldwide portfolio of 25 brands, including Fendt, Massey Ferguson, Valtra, Challenger and Cumberland, AGCO manufactures tractors, combines, hay tools, foragers, tillers, sprayers, engines and generators — in other words, the advanced equipment the world’s farmers rely on for modern agriculture applications.
AGCO rolled out the red carpet – Massey Ferguson red, to be exact — for the AEM Manufacturing Express’ visit to Duluth, Georgia in late August to celebrate the equipment manufacturing communities across the U.S. that comprise its family of facilities, all from northeast Georgia.
For all its manufacturing might, AGCO is still a young company. Formed in 1990 through a splitting-off of Deutz-Allis’ North American arm, AGCO has quickly grown via a combination of strategic acquisition and bold expansion. AGCO understands that modern agriculture equipment isn’t what it used to be, nor are the skillsets employees must possess if manufacturers want to continue thriving into the future.
“We’re always asking ourselves how we can better develop and equip our employees with the skills needed for their roles today, as well as tomorrow,” said Lori Goldberg, vice president of global talent solutions at AGCO.
The Manufacturing Express Team had a chance to hear about a new workforce development initiative helping answer that question.
AGCO’s CATALYST Rotational Program provides full-time employment to post-graduate students around the globe. Those embarking on their new careers receive more than just a full-time job. CATALYST employees know they will also be embarking on an extended journey of professional development.
“Talent management can’t just be about what an employee can give to your company,” Goldberg said. “It also has to be about what you can give back to the employee. Our CATALYST employees have the education and core skills our company needs on day one. Once they’re here, we want to keep filling up their personal toolkits with other essential skills they need to become seasoned professionals.”
AGCO’S CATALYST program, which launched in January 2023, provides everything from on-the-job technical training and mentoring to networking and leadership development. It’s all geared toward attracting the right talent to the organization, and ultimately setting that talent up for success within an evolving company and industry.
“We realized that if we could connect with talent when they’re just coming out of college and show how we’re actually willing to invest in them, we could differentiate ourselves as an employer,” Goldberg said, adding that differentiation is extremely important today since agricultural equipment manufacturers are also competing with the likes of Apple, Amazon and Google for the same types of employee skills.
Thus far, the CATALYST program is making a huge difference. Goldberg said AGCO has been receiving more applications than it has positions available. Additionally, nearly all CATALYST employees have decided to remain with the company after their CATALYST track has ended. By every measure, CATALYST has been a success.
Advanced Equipment Manufacturing in the Carolinas
The last week of August, the AEM Manufacturing Express traveled to both North and South Carolina to visit Timken Tyger River and Shiloh plants in a multi-state doubleheader visit, before continuing on to Leeboy and BOMAG to finish the week before a long Labor Day weekend. Along the route, AEM continued to tell the story of equipment manufacturing through events, activities and content, as well as speak with one collective voice about the bipartisan pro-manufacturing policies the industry needs.
The dual-visit to Timken’s Tyger River and Shiloh plants — the company’s pillars of its U.S. bearings division, in Union, South Carolina, and Rutherford, North Carolina — was a recognition of the profound impact that the equipment manufacturers have in the Carolinas, and the dedicated employees who are continuing to make that legacy possible.
Timken’s bearings are the foundation of many machines that drive the world, and the company emphasizes the importance of their product in terms of safety.
“Safety is a nonrecoverable metric,” says Marty Hallman, the company’s director of bearing operations in the Americas. “People may not always realize the importance of these components in keeping them safe, but I like to use those moments, like when a plane lands safely, to remind them that this wouldn’t be possible without our products.”
The company prides itself on taking care of its employees and the surrounding community. Timken employs 1,900 workers across nine manufacturing and distribution facilities, and the company is committed to keeping its manufacturing local. Timken places an emphasis on programs aimed at attracting the next generation of manufacturing employees, including high school students, transitioning military veterans and encouraging college students to try their hand at a trade. The company’s dedication to its employees is clear, and it plans to continue building a future in which innovation and community go hand-in-hand.
While the summer of 2024 has come to a close, the Manufacturing Express continues its journey across the United States, sharing the stories of innovation and determination that helps build, feed and power the world. Readers can follow the stories at www.manufacturingexpress.org. T&ID