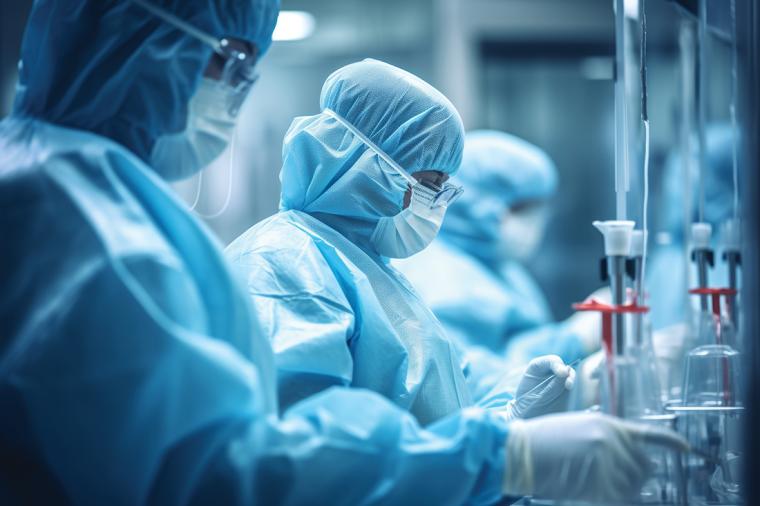
Global healthcare markets are continuing to grow. In 2022, the global market size was estimated to be approximately $8.5 trillion USD and projected to grow by almost 50 percent to a level of $12.5 trillion USD in 2025. This growth is, like in the past decade, driven by aging populations in developed markets around the globe, a growth in chronic diseases and the development of new therapies and technologies.
Despite this continued growth of the industry as a whole, top management of medical companies (medical devices, pharma, biopharma) have a more complex job than ever before. The current global environment in which they operate their companies and serve their customers and patients has become more uncertain. Geopolitical developments play a role; the regulatory framework context changes in many areas; healthcare systems are under cost pressure and still companies are expected to continue to grow.
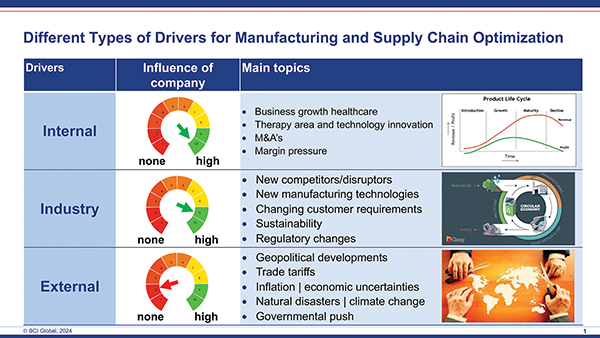
Manufacturing and supply chain leaders in these medical manufacturing companies are expected to optimize and manage their manufacturing footprints in such a way that growth of capacity, where relevant, is guaranteed. However, besides just expanding capacities, they are also expected to do this under the prerequisites of keeping landed costs under control, improving flexibility and overall service levels and to improve the resilience of their footprint.
BCI Global identified three key building blocks for medical companies to optimize their global footprints, leading to a higher level of manufacturing footprint resilience:
1. Risk identification and anticipation
2. Decentralization of the manufacturing footprint
3. Business driven localization of manufacturing
Risk Identification and Anticipation
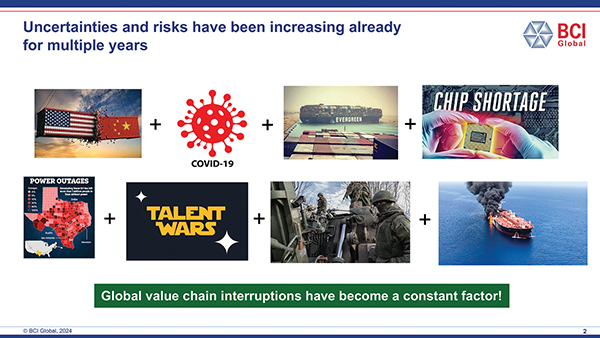
The medical industry historically is highly innovative from a product development perspective. However, from a manufacturing and supply chain perspective, the industry can be regarded as traditional/conservative. As companies were competing on the output of their R&D efforts, and not so much on the way of manufacturing and distributing their products, and as supply chain costs were only a small part of the total costs of a product, there was no pressure to be innovative in the end-to-end supply chain.
This has changed. First of all, manufacturing and supply chain costs are for many companies now much more important and secondly, much more is expected: the manufacturing and supply chain footprint must also facilitate resilience and flexibility. Resilience starts with awareness: creating visibility on which risks the company actually runs in the global manufacturing footprint.
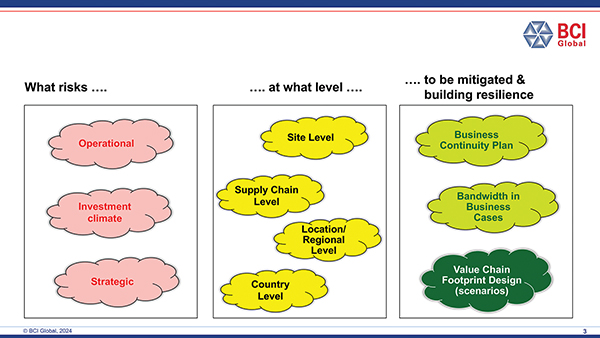
Many companies are now running initiatives to create this visibility by applying a methodological, fact-based approach to identify risks at different levels in their footprints and determine their potential impacts and also potential mitigation strategies.
BCI Global’s IRAM framework (Integral Risk Assessment Method) is an example of such a methodological framework which can be applied in different industry verticals, including medical technology, pharma and biopharma.
The framework consists of eight categories of risks related to the value chain footprint of a company:
• Geopolitical risks, e.g., the impact of geopolitical uncertainties, potential armed conflicts, upcoming or intensifying trade barriers
• Economic and financial risks, e.g., the volatility of inflation, economic development and healthcare spend policies
• Transparency risks, e.g., corruption and bureaucracy
• Natural disaster risks, e.g., earthquakes, wildfires, tornados and water shortages
• Personal security risks, e.g., crime, terrorism
• Energy security risks, e.g., lack of energy supply, grid capacity, vulnerability of the grid systems
• Labor market risks, e.g., low unemployment, high competition in the labor pool
• Supply chain and carbon risks, e.g., risks related to “having too many eggs in one basket” as well as, for example, carbon measures related to the import and export of specific materials (such as CBAM in the EU)
The eight categories can be operationalized into 50 detailed risk factors:
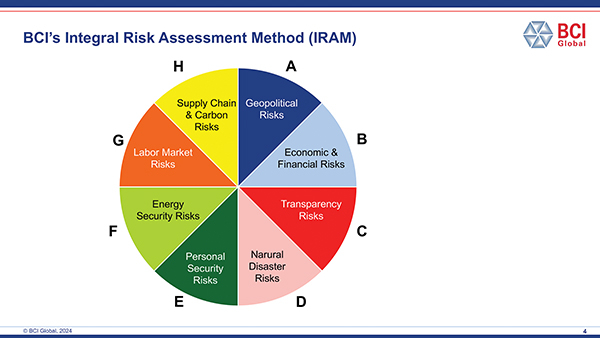
A Case Study on Risk Assessment
In a recent project involving a medical company, BCI Global applied this framework by identifying risks across the eight categories. The company has a manufacturing footprint with 10 manufacturing sites across the United States, Europe and Asia. The focus of this company’s manufacturing strategy had historically focused on 1) guaranteeing that manufacturing capacity could facilitate ongoing business growth globally and 2) keeping the cost-per-unit under control so the company’s products remained cost competitive, also in the tightening reimbursement schemes in the major markets.
Now the company’s top management, driven by the observed level of uncertainty around the globe as well as by the impact of some of the risk-related events happening in past years, tasked its manufacturing leadership with the challenge to determine the company’s main risks in the manufacturing footprint and to develop a strategy regarding how to mitigate these risks.
This was the first time this company really took an integral approach to risk related to the what, how and where of manufacturing.
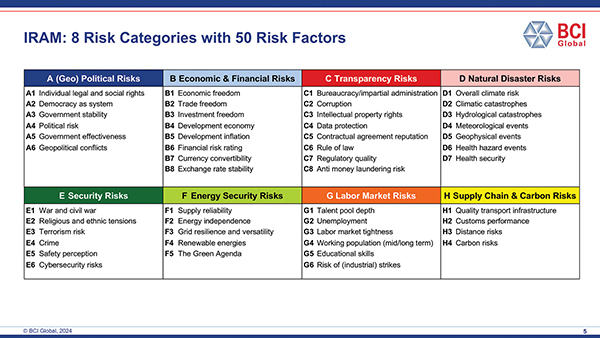
The first step of the analysis, identifying and quantifying risks at the level of the 50 detailed risk factors in the table above, led to fact-based insights such as:
• The company had a significant share of its manufacturing capacity located in relatively high-risk locations (e.g., China, earthquake zone in the U.S., flooding risk areas in Europe).
• The company thought it had significantly mitigated risks already by making use of contract manufacturers. However, the analysis made clear that this was only for a small share of capacity and still at high-risk locations.
• It became clear that the company’s “blockbuster” product was produced at a single location with, due to strict licensing regulations, no real backup at one of the other nine sites around the globe with the assumption that it would be easy to shift production over to another site.
• Several risks were identified related to some of the older sites with old production technology: only limited support/backup available in case the old production technology failed, with a significant risk of supply disruption to the market.
Based on these findings, the company made several new decisions, including:
• Engaging in capacity expansions at newer sites in lower risk locations, accepting a slightly higher cost per unit;
• Initiating a program to develop close partnerships with two selected CMOs and increase capacities outsourced to them (including implementing a dual capacity strategy for blockbuster products); and
• Initiating a global program to harmonize processes, standards and licenses (where relevant) across the 10 global sites.
Decentralization of the Manufacturing Footprint
Many medical manufacturing companies had a historical manufacturing strategy of centralized production in focused global manufacturing plants. The advantages of such a strategy included economies of scale, intellectual property (IP) protection, low complexity of the end-to-end supply chain and integration of research and development, engineering, new production introduction and commercial-scale manufacturing.
In the current world that includes all the uncertainties addressed earlier in this article, companies across different industry verticals have begun to decentralize their manufacturing footprint in order to reduce risks and become more resilient.
A recent BCI Global survey (in cooperation with SC Media) of 150 manufacturing leaders in companies in Europe and the U.S. confirmed that this decentralization is really occurring:
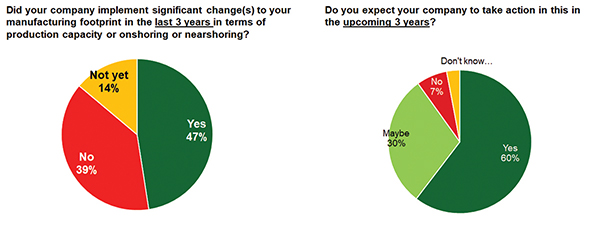
Forty-seven percent of the 150 companies stated they had already started decentralization in the past three years. An even more striking 60 percent indicated they expect to take this kind of direction in the next three years.
Healthcare manufacturers were the dominant segment in the pool of survey respondents, so among the companies stating they already did and/or were expecting to take action in terms of decentralization of manufacturing were a significant number of medical technology, pharma and biopharma manufacturers.
There are several examples of medical manufacturing companies taking a more decentralized approach towards manufacturing than the industry did in the past. These include:
• Cell and gene therapy/ATMP manufacturers typically start in one location, often in North America, and then quickly spread their capacity toward other continents, especially Europe. This is not only about risk management. In the case of closed-loop supply chains in the cell and gene space, proximity to the patient base/treatment centers plays an import role as well (speed of supply and treatment, reduction of supply chain interruptions and costs).
• Pharmaceutical manufacturers regionalizing production of active ingredients becoming less dependent on Asia as the main sourcing region (China/India). This strategy is also supported by government policies aiming to achieve a higher level of healthcare and industrial autonomy.
• Medical device manufacturers decentralizing production by deciding to put the next expansion not at a current location in the company’s historical home base (for example, the U.S.) but rather in a growing market (such as Malaysia for the Asian market) or a second established market (for example, Europe).
Business-Driven Localization of Manufacturing
Medical manufacturers are looking at specific markets around the globe to establish local-for-local manufacturing there. This is mainly driven by business (and/or risk) factors. The current major example is China. Other examples include Brazil, Japan and, to some extent, India.
Chinese authorities are clearly aiming to have a significant share of production of medical products for the Chinese market to be made in China in the coming years. So, where we saw earlier in this article that companies are moving (partly) away from China manufacturing, specific medical companies are moving in the opposite direction: locating new or expanding existing production capacities in China to take advantage of better market access and better positioning in the value-based procurement system in China.
A major challenge for Western medical manufacturers is to determine the best strategy for manufacturing in China or any of the other countries where localization may help to drive the business. Does this mean setting up a fully new, wholly owned manufacturing site including a supplier base, or can this be done together with a partner, for example, in a joint venture set up? Would doing only final assembly or fill/finish activities qualify as local production?
These are the questions many companies are currently wrestling with to develop the business case for localized manufacturing. T&ID