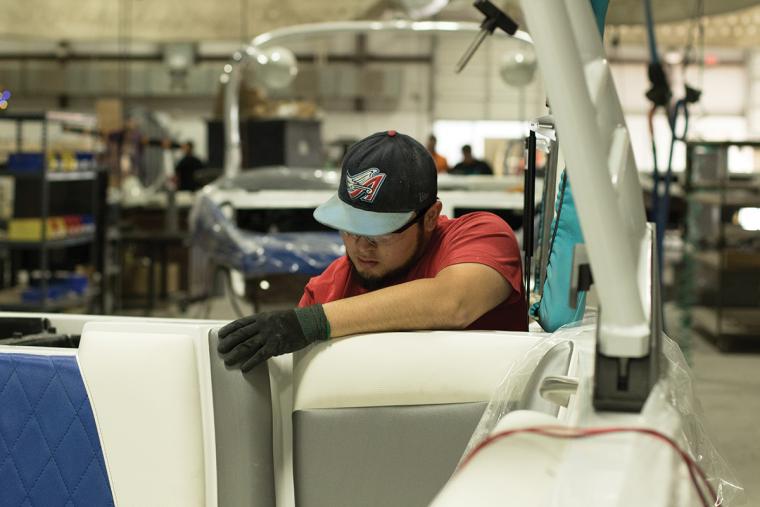
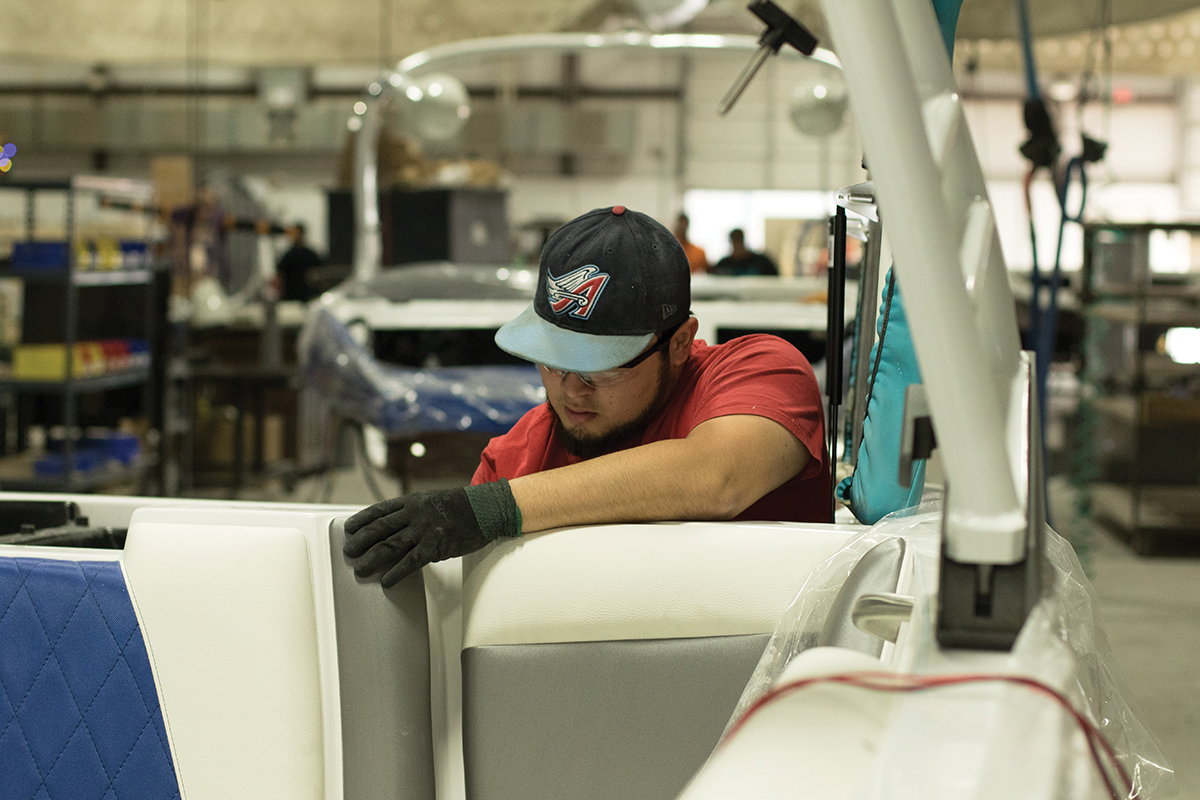
Training a workforce skilled in advanced manufacturing
Abilene, Texas
Approximately 150 west of Dallas/Fort Worth, Abilene, Texas, is focusing on attracting jobs brought back by reshoring and a focus of “made in America.” Local economic developers are focusing on building a highly skilled workforce for the advanced manufacturing jobs flowing into the region.
“At the heart of this new era is a creating highly skilled workforce, that is capable of designing, operating and repairing some of the world’s most advanced equipment,” said Shea Hopkins, director of talent develop at DevelopAbilene - Abilene Industrial Foundation.
DevelopAbilene is focusing on workforce development in several ways. One is the state-based Skills Development Fund, which provides local customized training opportunities for Texas businesses and workers to increase skill levels and wages of the Texas workforce. Its success lies in the collaboration among businesses, public community technical colleges and DevelopAbilene. Another is the Self Sufficiency program, which provides grants to community and technical colleges and community-based organizations to implement customized job training programs in cooperation with employers, to help low-income individuals and those receiving public assistance achieve self-sufficiency and independence.
In Abilene, workforce training starts early. DevelopAbilene also provides funding to Communities in Schools (CIS) program, which provides technical training to high school students so they capable of filling the in-demand jobs of Abilene’s advanced manufacturing industries.
“By creating a distinct pathway, we’re able to show sustainability as well as growth potential in creating a skilled workforce for our community,” said Hopkins.
Tigé Boats is a local business that has benefitted from Abilene’s workforce training programs. It operates a 135,000-square-foot manufacturing facility and headquarters there.
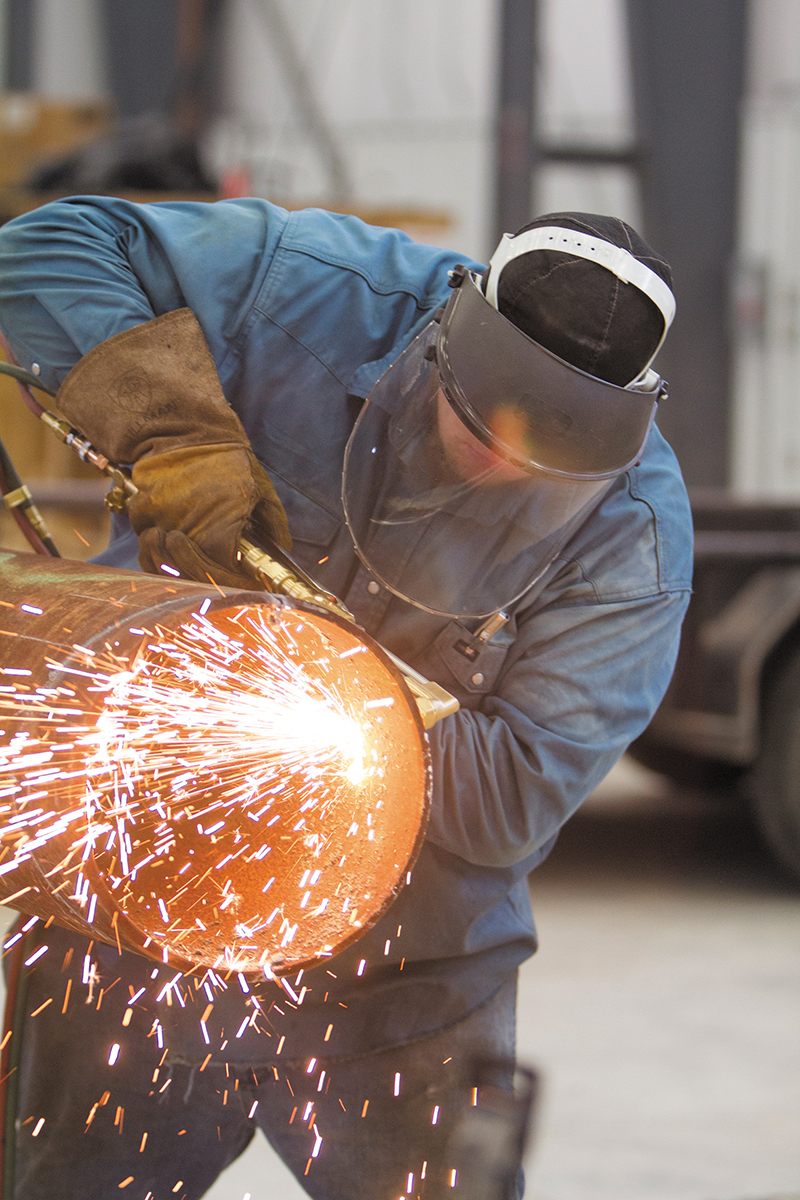
Creating a pipeline of skilled employees to take jobs
Henderson, Texas
Henderson, located in northeast Texas approximately 90 minutes from Shreveport, Louisiana, is focusing on business retention and attraction through workforce development programs. The Henderson Economic Development Corp (HEDCO) has teamed up with nearby Kilgore College to offer local businesses everything from manufacturing classes like welding to soft skills courses including ones in communication to technology courses.
HEDCO funded a number of welding machines at the Advanced Technology Center, run by Kilgore College. The 6,000-square-foot facility includes classrooms and actual welding and fabrication shop space, as well as two brand new virtual reality welding machine stations. Designed to teach high school students during the day, the center is open to adults in the evening who are looking to advance their skills.
“There are employers in the area that can’t filled skilled workers, so we created programs to put people in jobs,” said Martha Woodruff, director of workforce development at Kilgore College. “Our economic developers are proactive, creating a pipeline of skilled employees to take these local jobs.”
Wooduff said the workforce training is partially funded by a grant from the Governor’s office for displaced workers.
Meridian Brick, a brick manufacturer with a facility in Henderson, is one example of a local business taking advantage of this workforce development.
“We’ve provided communications courses, human resources training, welding and more for Meridian,” said Woodruff. “When we partner with businesses, we start by learning about an organization’s needs and then develop a training plan that addresses those needs.”
Open jobs spur a state to find ways to fill them
State of Michigan
Michigan has a variety of programs aimed at giving students and adults training they need to gain in-demand skills that lead to good jobs.
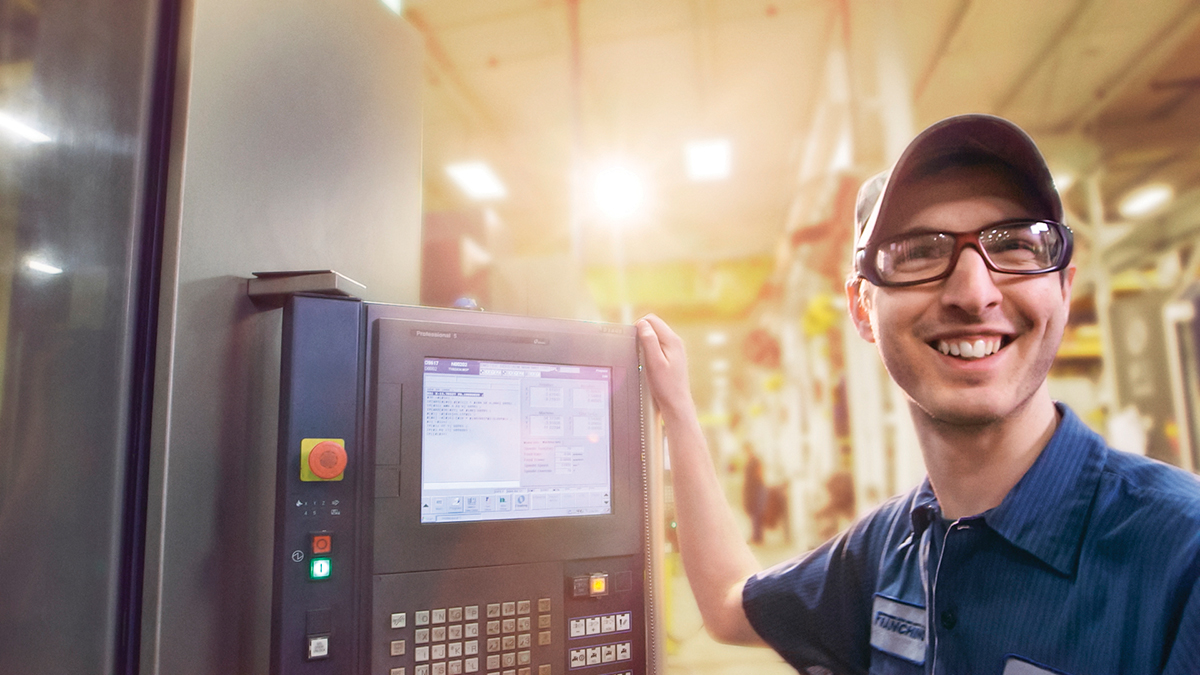
To help both businesses find suitable employees and its residents find jobs, the state’s economic developer is working to help people of all ages enhance their jobs skills.
“We’re working with employers and educators through the Michigan Career Pathways Alliance to help students become aware early on of what opportunities are out there, and what training they need to get those jobs,” said Murray. “We’re also partnering with the state Education Department to help schools get the resources they need to strengthen career technical education classes and improve access to counselors.”
In addition, the state’s Skilled Trades Training Fund helps employers develop the talent they need to fill thousands of available jobs, or give current employees new skills to retain jobs. Since its inception four years ago, the state has invested more than $30.3 million in the program in the first three years, assisting 855 businesses and creating nearly 12,000 jobs.
“The Skilled Trades Training Fund helps companies create new jobs and retrain existing employees,” said Murray. “That allows businesses to grow in their existing locations rather than move elsewhere in search of employees with in-demand skills.”
The state has also expanded its apprenticeships programs to nontraditional fields and to under-served populations with the help of a federal grant, which helps people gain skills without accumulating significant college debt. In 2017, there are 14,850 active and registered apprenticeships in the state, up from 11,802 in 2015.
One success story is the healthcare industry in the Grand Rapids area, which is quickly becoming a healthcare leader in the state. Working in conjunction with economic development board West Michigan Works!, organizations such as Mercy Health, Cherry Health, Mary Free Bed Rehabilitation Hospital and Spectrum Health have partnered with Grand Rapids, Montcalm and Muskegon community colleges to create the state’s first accredited apprenticeship program for medical assistants. The program has a 95 percent placement rate for the roughly 300 students who have participated.
Growing a skilled workforce through education and attraction
Greater Louisville, Kentucky
Faced with slower population growth than competitive cities, Louisville, Kentucky has a multi-pronged approach to developing a robust workforce.
The first is a focus on workforce training programs implemented by Kentuckiana Works, the region’s workforce development board. In the past year, Kentuckiana Works raised more than $2.3 million in new funding for workforce development efforts and helped over 2,100 people get jobs through job training, scholarships and workforce readiness preparation.
This includes the Code Louisville program, which helps people develop coding skills as a direct link to employment. The local school systems have begun to play a more significant role in preparing students for the workplace with various work-ready initiatives supported by private sector employers.
Louisville’s Mayor, Greg Fischer, has also gotten in the act. His office runs a SummerWorks program, offering young adults a real-world work experience in the private sector.
“There is no better way to make a difference in the life of a young person than to hire them and put them to work. They will learn real world lessons they will remember all their lives, while building Louisville’s talent pipeline to the future,” said Mayor Fischer.
“These programs are important to serving the pipeline of workforce for various industries. Without strong work ready programs, companies lose confidence in our ability to provide workers today and tomorrow,” said Deana Epperly Karem, vice president of regional economic growth at Advance Greater Louisville.
In addition to training workers, Advance Greater Louis is focusing on attracting new talent to the region. Its LiveinLou talent initiative recruits people from all over the country but specifically in populations that are 200 to 500 miles away. While it launched with a focus on recruiting 25-54 year olds with degrees, the program quickly learned that the community’s need for non-degreed people is just as important, according to Karem.
“Companies seeking a new location for their expansion are talking about workforce and talent more today than ever,” said Karem. “Our programs help us provide confidence to clients that there is a workforce available, but also a program that betters the pipeline as the company itself grows.”
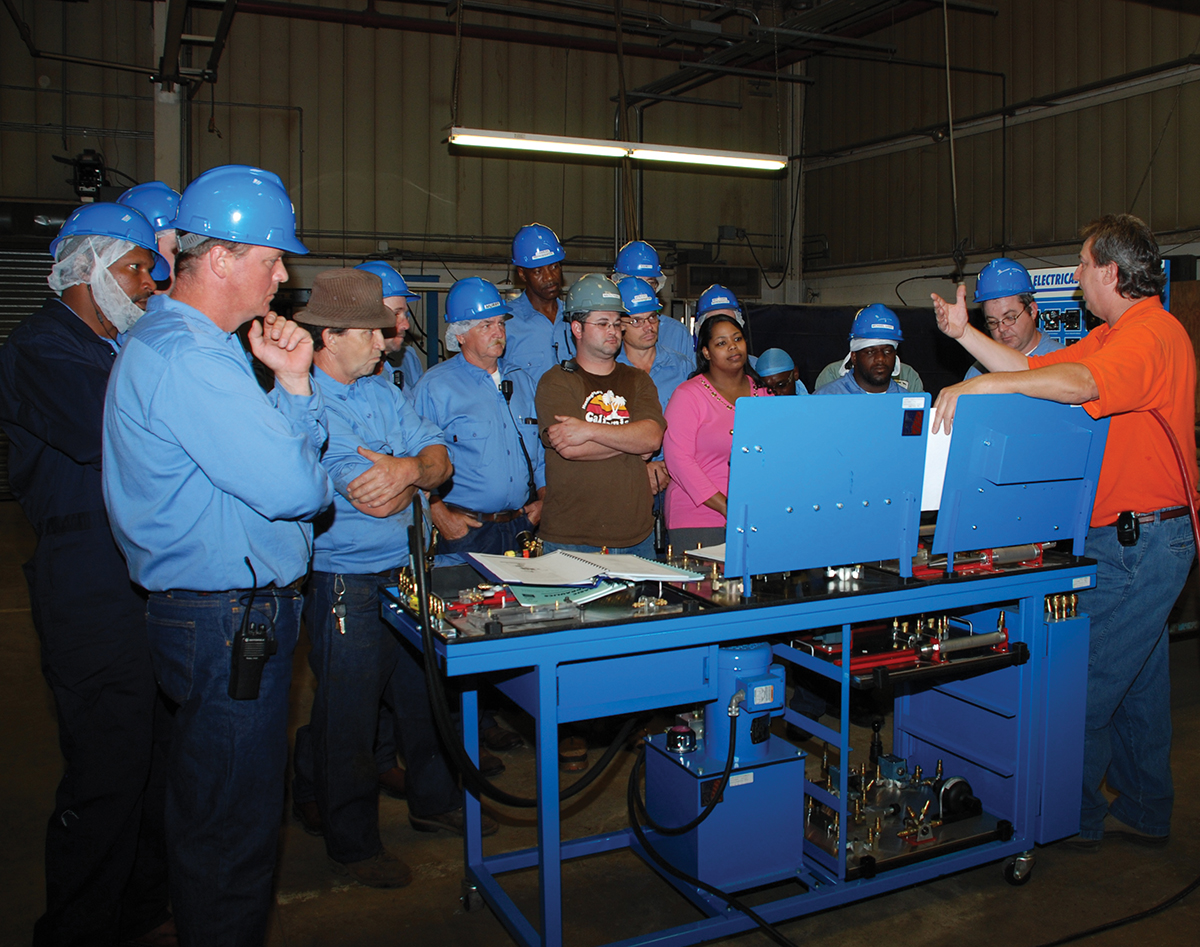
East Arkansas Delta
In eastern Arkansas along the Mississippi River, the push to bring better and higher-paying jobs the region is going strong. Local economic developers like the Crossroad Coalition and the Arkansas Delta Training and Education Consortium (ADTEC), which is comprised of five Arkansas community colleges, are using their collective resources to address current and future training needs of business and industry. They are especially focused on attracting new jobs and businesses brought back to the U.S. through reshoring efforts.
The efforts are working. In May, 2017, Shandong Ruyi Technology Group of China announced that the company will invest $410 million in the former Sanyo Manufacturing Corp. facility in Forrest City, Arkansas. When operational in mid-2018, the facility will process more than 200,000 tons of Arkansas cotton annually into yarn for textile use and bring up to 800 jobs to the Mid-South.
“That project is an example of how putting the right pieces in place over time can lead to a major success,” said Chris Heigle, Crossroads Coalition chairman of the board and researcher at East Arkansas Community College.
The region has a combined labor force of over 100,000 with strong industry footholds in manufacturing, retail, healthcare and agriculture. Arkansas Delta is engaged in the ACT Work Ready Communities initiative, and is looking forward to all participating counties being designated as “Work Ready” within the year, according to Heigle.
One example of the region’s workforce development programs include Arkansas Northeastern College’s Workforce Orientation & Retraining Keys (WORK) program. Run by ANC’s workforce training division called The Solutions Group, this program provides training and mentors to help guide people into life-long employment.
Big River Steel, which opened a new $1.3 billion steel mill and recycling facility in Osceola, Arkansas, in March, 2017, has tapped into the WORK program for workforce training.
“Providing accessible educational and training opportunities is our mission, and we are proud to offer workforce training to our local companies and new companies coming to the area such as Big River Steel. The Solutions Group has garnered national recognition for its innovation and flexibility, and we are glad to offer that experience and knowledge to the economic development of this region,” said Dr. James Shemwell, president of Arkansas Northeastern College.
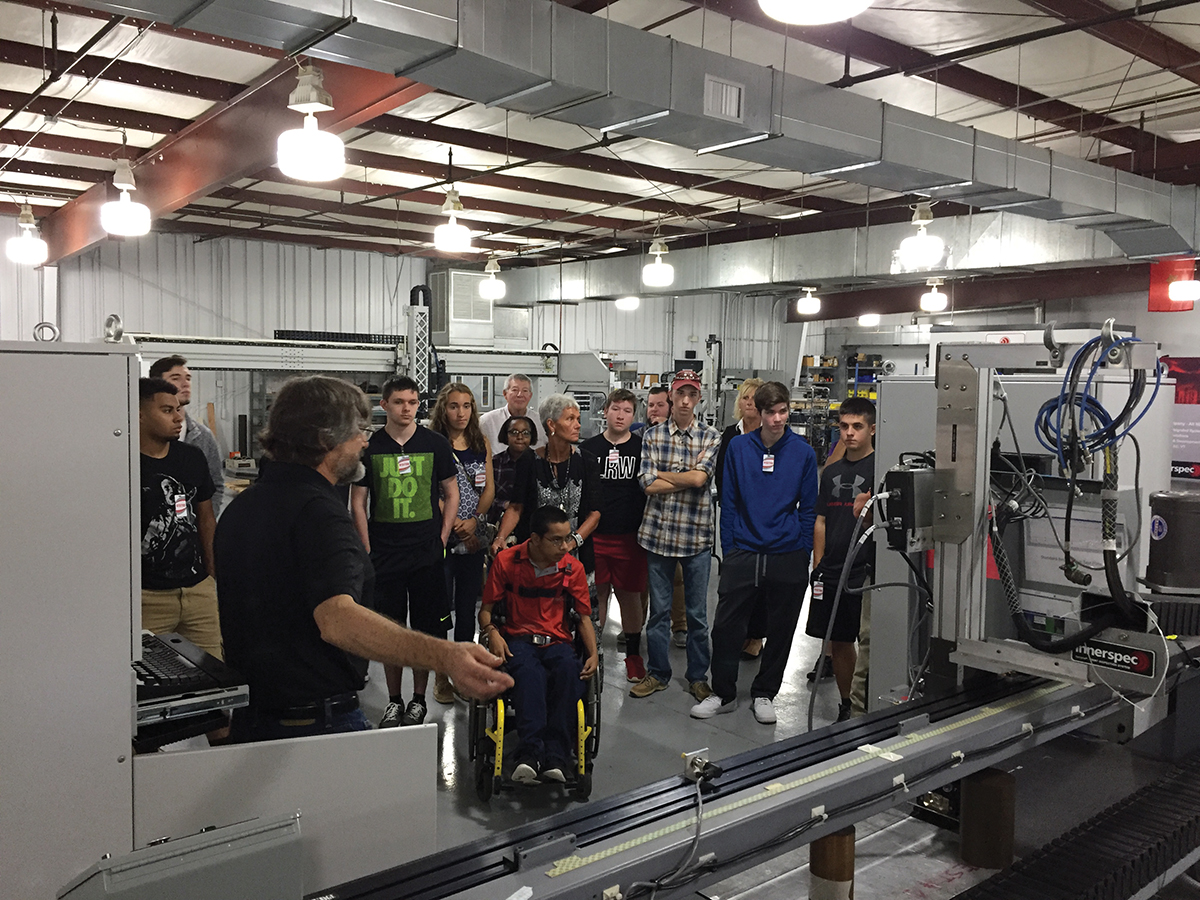
Bedford County, Virginia
Strategically located in west-central Virginia between the Lynchburg and Roanoke metro areas, Bedford County has access to a large workforce. The region is also putting its efforts into creating a talent pipeline for its industries that depend on a highly skilled and ready workforce.
Its key industries include nuclear energy with employers such as Babcock & Wilcox and AREVA, wireless communication with employers such as Harris Corporation and CommScope and a variety of advanced manufacturing.
“A strong part of what makes our county unique in workforce development is that we created a program eight years ago called Bedford One, ‘Offering New Experiences’ from classroom to career,” said Traci Blido, Bedford County economic development director, who leads the Bedford One program.
The Bedford One program links high school students with local businesses based on their career interests. It is a partnership between the Bedford County Office of Economic Development, Bedford County Public Schools and area businesses. An advisory committee made up of representatives from the county’s business industries, schools, Chamber of Commerce and Economic Development office guides the program.
To date, more than 4,000 students have visited more than 50 businesses and success is measured through surveys that are distributed to the students and businesses immediately following a tour. Survey results show 90 percent of the students feel the tours are informative and reinforce their ideas about their career choices. Also, 92 percent of the students surveyed said they are more likely to work in Bedford County as a result of what they learned on their tour. Since this program was implemented in 2009, the school system also implemented an internship class for senior high students in which they can work for a few hours a week at a business they are matched with to learn and get a deeper experience. The high school internships have increased to nearly 250 a year and apprenticeships and actual full-time jobs have even been offered after graduation in some cases.
“We are getting to the point where businesses are asking to do the tours or internships each year and we’re having a tough time to get them all worked into the schedule,” said Blido. T&ID