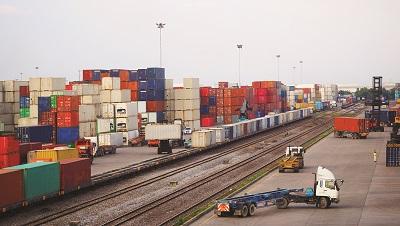
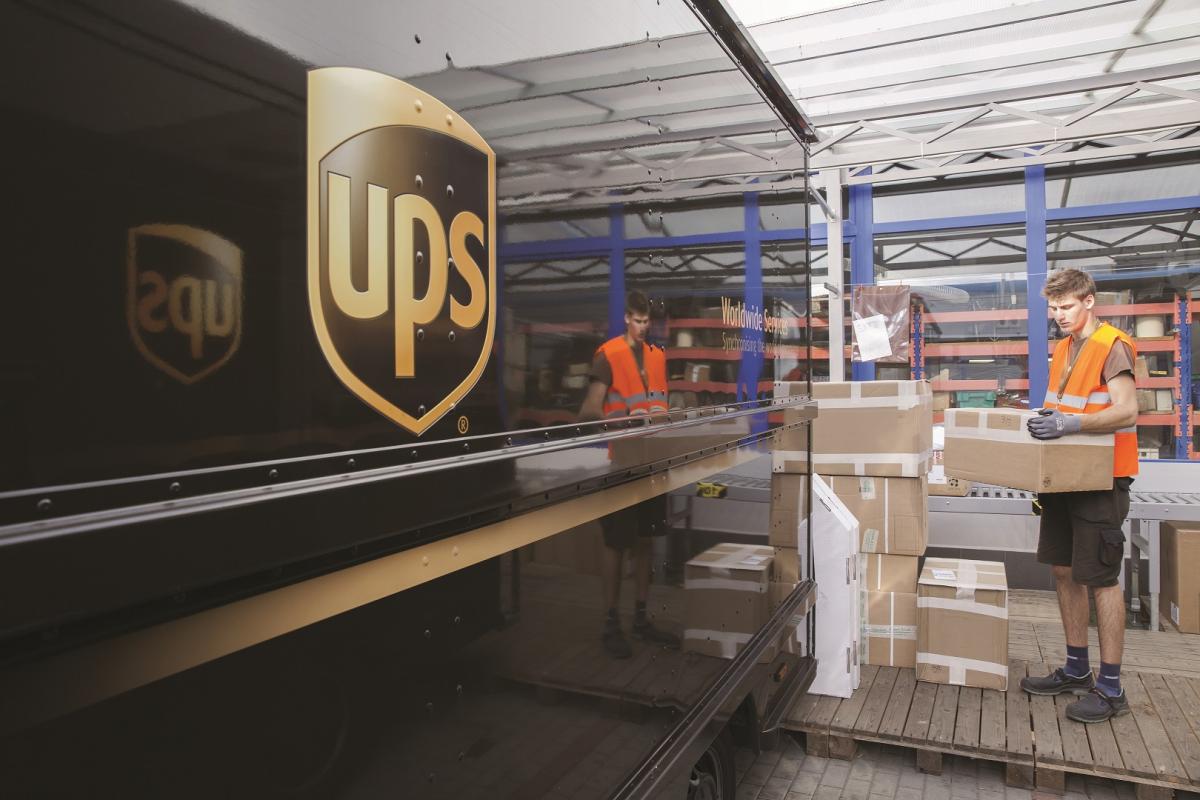
Borrowing from the golfing world, JLL reviewed numerous regional distribution markets across the U.S. and ranked the Top 18 (think 18 “holes”). We focused the study on identifying the “front nine” and “back nine” markets. The “front nine” is important to understand and critical to supply chain execution as it consists of those core industrial markets that dominate from a distribution and site selection perspective.
As transportation costs continue to rise, sustainability goals take on more importance, and as shipping times tend more toward next-day delivery, the trend will be for more facilities, closer to the consumer. This makes the next tier of distribution markets, or the “back nine,” even more attractive from a logistics and operating cost perspective.
To compile the ratings, the JLL Industrial Research team, working closely with on-the-ground professionals across the U.S., identified and applied 32 specific metrics to weight and rank industrial distribution market performance from a supply chain and logistics perspective. The metrics were based primarily on important site selection influencers such as population and demographics, labor availability, wage rates and other costs, energy costs, transportation and multi-modal infrastructure, industrial real estate leasing market and investment variables, as well as local tax and economic incentive opportunities, among others.
Markets were clustered to mirror a natural site selection decision process. Here are the findings:
The “Front Nine”
-
New Jersey/New York Metro Area
-
The home of some of the most densely populated centroid(s) in the country, the New York and New Jersey Metro Area is also the largest seaport on the east coast — an immensely important driver of industrial space.
-
While real estate costs are higher nearer to the Northern New Jersey and New York population nexus – the region also provides diversity in site selection options as well as labor availability and costs that are not extreme, although a few related metrics like unionization rates tend to slightly offset an overall strong labor score in our model.
-
Southern California
-
Jeramey Lende / Shutterstock.com -
Distribution real estate costs can be high (and available options few) in the infill markets, but between the distribution submarkets of Los Angeles and the Class A ‘big-box’ opportunity of Inland Empire, the region provides significant strategic balance, the ability for efficient throughput of cargo and access to much of the rest of the country.
-
Central and Eastern Pennsylvania
-
This vast geographic area offers distribution access to a broad swath of the U.S. populace, in many different directions via several modes of transit. The fact that it has the reach to other large cities, as well as the transportation infrastructure, good civilian labor force metrics, reasonable cost of living scores – and very important, cost-effective basis for logistics real estate, for a market of its size – helps propel this market into the upper echelon of the “front nine.”
-
Relative to the New York/New Jersey market in our survey, the region provides more ‘large-block’ development opportunities and a lower average land basis, as well as a beneficial business operating environment.
-
Chicagoland & Milwaukee
-
Chicago is an ‘easy par’ market when considering a Midwestern location or core investment opportunity. Combined with its drive-time proximity to much of the nation’s greater consumer base, Chicago ranks right up with its peers as a ‘necessary’ supply chain market, with the second-highest real estate metrics in our model.
-
Milwaukee is an interesting satellite market for Chicago, and while labor costs are a little higher than its larger companion, it is a tight market with few Class A space options available.
-
Dallas/Fort Worth Metroplex
-
Significant, lower-cost labor force, as well as a growing attractiveness for business and headquarters operations, the region is a hub of Class I rail lines and intermodal operations that connect it with other major and regional markets around the country, in addition to an interstate network and major air cargo capabilities.
-
While vacancy is up recently as the development market heated up relative to its 10-year average, the region is home to a number of Class A space options at lease rates that provide cost savings compared to other major U.S. markets.
-
Atlanta
-
With a strong environment for doing business and a substantial yet growing population center, Atlanta is the major anchor market of the Southeast U.S. Logistics real estate remains affordable, and prime space leasing options are more abundant relative to other major markets.
-
Atlanta has connections to the seaport market in Savannah, as well as several intermodal waypoints from major rail lines, keeping its infrastructure score in our rankings from falling too far relative to some other major supply chain locations.
-
The Mideast (Indianapolis, Columbus & Cincinnati)
-
All of the Mideast markets are within trucking reach to touch much of the country in one day’s drive-time. Like many of our Mideast cities, infrastructure and connectivity, cost of living, favorable labor rates and relatively inexpensive real estate and development options benefit the market.
-
Not without its own cargo airport capabilities (hence the news about Amazon quietly using the market to initiate flight operations), the market can tap into Louisville’s UPS all-points international air cargo hub.
-
The Mid-Atlantic
© FedEx 2016
-
While possibly not an obvious selection into the “front nine” for people not already in the market, the DC/Baltimore metropolitan area has one of the best population and demographics ratings in our study.
-
The Richmond and Hampton Roads area does not have the local populace to stand out alone in our model, but it is able to reach other Mid-Atlantic markets within a relatively easy drive-time. Similarly, has a good network of interstate connections, Class I rail and Norfolk is the home of a major U.S. seaport.
-
Southeast Texas
-
In the last of our “front nine” markets, Houston is a large population draw and a major port market for energy-related, commodities and breakbulk product.
-
Population growth in the next five years and median hourly wages make it a market area to watch in the future.
The “Back Nine”
-
Honky Tonk Triangle (Louisville, Memphis, Nashville)
-
While it doesn’t have the same population numbers as the “front nine” markets, Memphis is the home of FedEx’s global ‘SuperHub’ and five Class I rail lines (second only to Chicago) – transportation infrastructure which positions it well as a vital logistics node. It also has the labor force that has made it an e-commerce juggernaut.
-
The area gets a boost with its logistics-centric markets and proximity to more of the Midwest, Great Lakes and central markets like St. Louis in an approximate half-day or day’s truck time. Not to mention, Louisville it is the home for UPS.
-
The Carolinas
-
How do the Carolinas make it so high on the leaderboard? Connectivity, transshipment and labor costs. The region may not be a population powerhouse like some of the other major markets, but the area scores high for cost of living and for both transportation and production location quotients (relative to the national average).
-
At the same time, it has the interstate network, rail capacity, seaport connections and proximity along the eastern seaboard to touch other major population markets. Likewise, forecasted per capita growth in Charlotte and Greensboro/Winston-Salem over the next few years is on pace with many of our “front nine” markets.
-
Florida
-
Labor costs, unionization rates and blue collar workforce availability all score very high in our model. Florida is also now the second-most populous state on the East Coast, only behind New York, has a number of well-operated ports, and good and developing intermodal connectivity.
-
Serving the growing population in Florida is a must and has created growth in the industrial markets serving the state. The supply chain challenge is that Florida is a huge consumption market, but little is manufactured there. Utilizing Florida as a regional distribution center is operationally difficult.
-
Minneapolis
-
Minneapolis may be a surprise player in our rankings. The city benefits from a good cost of living, an affluent core of residents and density of Fortune 500 companies, while having a population that is similar in size to many of the metropolitan areas further down in the “back nine” rankings.
-
While it may also lack some of the same supply chain infrastructure, Minneapolis serves its Upper Midwest regional economy well with good scores on its blue collar civilian labor force, but realizes higher relative costs both from a wage and real estate pricing perspective.
-
The Heartland Markets (Kansas City, St. Louis)
-
Rail connectivity helped put Kansas City higher on our list. While it may not have the drive-time population or labor analytics of other markets, it still proves to be the ‘link’ of cross-border rail activity to Mexico and with interchanges with Canada.
-
St. Louis obtains very good, balanced scores in our study that track well along many of our indicator averages. It has strong access to concentric rings of the Midwest consumer base and an industrial real estate market that provides availability and access to affordable tracts of buildable land and rental rates that sit close to the U.S. median.
-
Northern California & Reno
-
The Northern California cluster, including Reno, encompasses a huge layer of the Western U.S. population center, but is also spread out over a vast geographic area. Given the Port of Oakland and the interstate network connecting many of the Northern California markets with other major metro areas, the regional cluster scores well in our rankings for transportation infrastructure.
-
Oakland has a large local base of residents and consumers, similar to a few of the markets in our “front nine,” but also a higher-than-average cost of living, warehouse wage rates and other labor market indicators. With vacancy tight in Oakland and very few new development options available, the Central Valley has emerged as a nexus for new big-box construction. The Sacramento, North Bay and Reno markets offer a little more site selection flexibility.
-
The Desert Markets (Las Vegas, Phoenix)
© 2016 United Parcel Service of America, Inc.
-
Phoenix is an important local and regional market with a population slightly below some of the bigger swingers earlier in our index.
-
Both Phoenix and Las Vegas have good labor availability and pricing metrics. With the ability to build big box distribution facilities, the Desert markets are certainly important players.
-
The Mountain Region
-
Denver and Salt Lake City score well in our index from an industrial real estate perspective, with good rents, available land and business environments.
-
Population-wise, they are both comparable to the Mideast and Carolina markets, but they are challenged by the longer-range drive-time accessibility to other markets to serve as effective super-regional hubs.
-
The Pacific Northwest
-
Similar to the Mountain region in our study, the Pacific Northwest is an important piece of a supply chain “four corners” strategy. With a strong container port network between Seattle and Tacoma, and important rail connections, the region can service the population centers in and around that region.
-
While population growth is booming in the Pacific Northwest, Seattle and Portland are relatively isolated from other major population centers and have a higher cost of living and warehouse labor costs.
Conclusions
Increases in freight costs, trucking capacity concerns, labor availability, more competitive customer service requirements, global complexities, risk mitigation – these operational concerns are keeping corporate supply chain professionals up at night.
When it comes to distribution network strategy, companies must ultimately make site selection decisions that pin their strategy down to the ground. It is clear that the benefits of integrating supply chain strategy and real estate execution are significant and will add value to any process.
Related Agencies
- New Jersey Commerce, Economic Growth, and Tourism Commission
- Georgia Department of Economic Development
- Texas Economic Development Corporation
- Pennsylvania Department of Community & Economic Development
- WEDC - Wisconsin Economic Development Corporation
- Indiana Economic Development Corporation
- JobsOhio
- Kentucky Cabinet for Economic Development
- South Carolina Department of Commerce
- Tennessee Department of Economic & Community Development
- Enterprise Florida
- Missouri Partnership
- Arizona Commerce Authority
- Utah Governor's Office of Economic Development
- Washington State Department of Commerce
- Los Angeles County Economic Development Corporation
- Upstate California Economic Development Council
- Dallas Office of Economic Development
- Savannah Economic Development Authority
- Columbus Chamber
- REDI Cincinnati
- Indy Partnership
- Greater Louisville
- Louisville Economic Development Alliance
- Paducah & Louisville Railway
- Charlotte Regional Business Alliance
- Greater Winston-Salem Inc
- Greater MSAP - Minneapolis Saint Paul Economic Development Partnership
- St. Louis Regional Chamber
- Greater Seattle Partners
- Sacramento Municipal Utility District (SMUD)
- Greater Phoenix Economic Council
- Seattle Southside Business
- Greater Seattle Partners