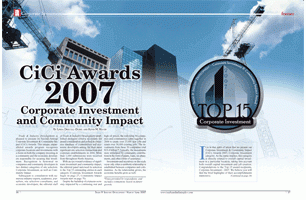
Ford Motor Company — Southeastern Michigan
Facing intense global competition, decreased market share, rising operating costs, and excess U.S. industrial capacity, Ford Motor Company has announced it will drastically change the way it conducts business. Ford is implementing its Way Forward revitalization plan, a strategy to allow it to introduce new products, cut costs, and return the company’s North American operations to profitability.
With facilities throughout North America, Ford is examining where to cut and where to invest and place new product programs. As part of this effort, Ford will make investments totaling $866 million in six Michigan plants. The investments will bring flexible manufacturing and advanced powertrain production to the plants, which include facilities in the cities of Dearborn, Livonia, Wayne, and Woodhaven.
The investments, which represent the first part of a $1 billion commitment announced in August 2006, are supported by a Michigan Economic Development Corporation incentive package of $151 million. In addition, the state and local communities are considering additional property tax abatements.
A University of Michigan economic analysis estimates that increased economic activity created by the investment would save an additional 42,460 indirect Michigan jobs in addition to the up to 13,740 retained directly by the company. The project is expected to generate more than $62 billion in personal income for Michigan workers over the life of the tax credit.
“Our turnaround in North America and our return to profitability is based on strategic investment, not just cost cutting,” said Mark Fields, president, The Americas, Ford Motor Company. “With this investment, we’re expanding our commitment to small cars, producing fuel-efficient powertrains and fortifying our truck leadership.”
“With these investments and a focused and committed workforce, we stand ready to deliver the cars and trucks that people want,” said Joseph Hinrichs, vice president, North America Manufacturing. “We’re solidifying our manufacturing base and positioning ourselves for future growth.”
UPS Worldport II — Louisville, Kentucky
In May 2006, United Postal Service (UPS) announced it would expand its main air hub in Louisville, Kentucky. The air hub, a vast sorting complex called Worldport, already employs about 7,500 of 18,000 UPS workers in Louisville. The expansion, which will create Worldport II, is expected to add about 5,000 jobs. Over 1,200 of these jobs will provide full-time employment.
The expansion represents a more than $1 billion investment in the commonwealth of Kentucky. Nearly 1,100,000 square-feet will be added, while another 334,500 square-foot space will be renovated with new technology and equipment. Additionally, several ramps at the Louisville International Airport will be built or altered, bringing a total increase of just over 3,000,000 square feet.
Encouraging UPS to invest in the expansion was a collaborative effort. It involved both the Kentucky Cabinet for Economic Development and Greater Louisville, Inc., the city’s chamber of commerce. Crucial support was provided by many government officials, including Governor Ernie Fletcher, Louisville Mayor Jerry Abramson, and members of the Kentucky General Assembly.
UPS is expected to receive tax benefits up to $31.6 billion over ten years under the Kentucky Jobs Development Act. UPS also anticipates it will qualify to receive up to $20 million in benefits over the next three years under the Kentucky Enterprise Initiative Act. The program allows approved companies making an investment of $500,000 or more in Kentucky to recoup Kentucky sales and use tax on the cost of construction and equipment.
The presence of UPS has helped attract more than 90 companies to either locate or expand their operations in the state over the past five years, investing more than $1.2 billion and bringing in more than 13,300 new jobs. “We view building our communities to be part of building our business,” said Bob Lekites, UPS’s Louisville-based vice president of airline and international operations. “Past public and private partnerships, as well as collaboration with local universities and minority-owned businesses, have been successful, and we look forward to continuing that with this expansion.”
Kia Motors Corporation — West Point, Georgia
The motto of Kia Motors Corporation — The Power to Surprise — certainly resonates in West Point, Georgia. Ordinarily, the motto is about Kia’s automobiles. But in Georgia, it is also about a huge investment by Kia and state and local authorities. Kia is investing $1.2 billion in a new automotive assembly plant. The new facility will employ an estimated 2,893 people, and stimulate suppliers to employ an additional 2,600.
At the anticipated employment of 2,693 jobs, the total state incentive package is worth $258 million, or $89,550 per job. On behalf of the local community, the state negotiated a local incentive package with the company that provides $130 million in property tax abatements over 15 years. The community and utility providers have also agreed to provide about $21 million in infrastructure improvements (water, sewer, gas, power, etc.) for a total local package of $151 million.
Ultimately, the deal is all about jobs, which are especially welcome in an area hard-hit by the decline of the textile industry. At the Kia plant, the average salary is expected to be $50,000, with benefits – a big boost to the local economy, where average per capita income is $17,626. A Georgia Tech study estimates the economic impact to the state of Georgia at approximately $4 billion per year.
In “the most complex deal we’ve ever done as a state,” according to Georgia Department of Economic Development deputy commissioner Chris Clark, the time elapsed from Kia’s first phone call expressing interest to a signed contract was 11 weeks.
Ordinarily, automobiles are assembled according to “just in time” principles. To keep inventories low, assemblers rely on nearby suppliers to produce components as needed. This approach, which assures the timely assembly of many components, was expressed in the deal itself. For example, just one aspect of the deal — securing the 3,300 acres of land Kia wanted — was accomplished in less than two months, even though the state’s team had to negotiate purchase options with more than 30 property owners.
Advanced Micro Devices — Malta, New York
The State of New York has secured yet another element in its emerging nanoelectronics cluster. Nanotechnology, the highly controlled manipulation of matter at the atomic scale, is widely touted as the future of industry, and even of nations. And the first, most lucrative, nanotechnology applications are happening in electronics.
Public authorities around the world are vying to cultivate nanoelectronics communities. Even in an era of tightening budgets for research and development, the federal government continues to increase its support of the nanosciences. It is in this context that New York is striving to build its own nanoelectronics infrastructure. Such an infrastructure would emulate the example set in Texas, where an early investment in Sematech positioned the state as a center for semiconductor research.
Early wins included Sematech itself, which invested $403 million in a research center in upstate New York. In addition, an IBM-led consortium of high-tech companies will spend $1.9 billion on nanoelectronics manufacturing and development in East Fishkill, New York. Other companies in the consortium include Sony, Toshiba, Samsung, Infineon, Advanced Micro Devices (AMD),and Charter.
New York’s latest success is in attracting additional investment from AMD. In June 2006, AMD and New York officials announced a multi-billion dollar deal that will enable AMD to build and operate the most advanced semiconductor manufacturing facility in the world at the Luther Forest Technology Park in Malta, Saratoga County.
Under the terms of the agreement, AMDwill be able to construct a new fabrication plant (fab) designed to produce 300-mm wafers using 32-nanometer process technology. Expenditures at the facility are projected to total more than $2 billion during the first five years of operation, bringing the project total investment to $5.2 billion.
The project is expected to create 1,200 new high-tech jobs, 1,209 indirect jobs, and 1,791 induced jobs. Construction activity will also create an estimated 6,000 jobs.
AMD had also considered a site in Dresden Germany, where AMD already has a fab. But AMD ultimately responded to New York’s proven commitment to the semiconductor industry, a financial incentive package, and an educated workforce that could serve the semiconductor industry.
General Motors— Ypsilanti and Warren, Michigan
In April 2006, Michigan Governor Jennifer M. Granholm announced an incentive package approved by the Michigan Economic Development Corporation (MEDC) to encourage General Motors to invest up to $282 million in its Warren Transmission operation and up to $125 million in its Ypsilanti Transmission operation.
“We will work with General Motors to encourage them to take advantage of the great opportunity this grants provides to the company and the community,” Granholm said. “GM’s continued commitment to investing in Michigan and its workforce demonstrates that we will not concede new automotive investment and jobs to any other state or nation.”
The MEDC approved a Single Business Tax credit valued at more than $34.6 million over 20 years in an effort to win the company’s investment in the Ypsilanti facility. Ypsilanti Township has approved a 12-year tax abatement valued at $6.9 million to support the project.
The MEDC also supports a tax abatement valued at more than $4.9 million for the Warren Transmission facility. The city of Warren is also considering a 12-year local tax abatement that could be valued at more than $19.8 million to secure the project, which is expected to retain 300 jobs.
A University of Michigan economic analysis estimates that increased economic activity created by the investment in the Ypsilanti facility would save an additional 11,490 indirect Michigan jobs in addition to the up to 2,000 retained directly by the company. The project is expected to generate more than $16 billion in personal income for Michigan workers over the life of the tax credit.
“We are considering the Ypsilanti and Warren Transmission Operations because the facilities have continuously demonstrated their ability to stay competitive and provide high-quality products,” GM Manufacturing Manager Ken Dosenbach said. “GM appreciates the long-term business relationship that has developed over many years with the state of Michigan, the township of Ypsilanti and the city of Warren, and we look forward to building on those relationships in the coming years.”
General Motors Corporation — Toledo, Ohio
Good news seems scarce in the U.S. automobile industry. The headlines amount to a litany of losses, layoffs, and plant closures. And General Motors (GM), the biggest of the big three, may soon lose its status as the world’s largest automaker. But GM remains a determined competitor, as evidenced by its decision in February 2006 to expand its transmission plant in Toledo, Ohio.
The expansion will house manufacturing of GM’s new generation of Powertrain equipment, a new six-speed, rear-wheel drive automatic transmission. GM expects the new transmissions, which provide better performance and fuel economy, to replace its older four-speed transmissions by 2011.
GM will make a total fixed asset investment at the site of 413.2 million, including $70 million for a 400,000 square foot building addition, $30.6 million in building renovation, and $412.6 million for machinery and equipment. As a result of the project and the state assistance provided, GM will retain 2,000 existing full-time jobs with an average hourly wage of $28.49.
According to local press accounts, local and state officials provided an incentive package valued at $75 million over 15 years. The largest component from the state consisted of a 75 percent Job Retention Tax Credit for seven years, valued at up to $23 million. Other state components included a Roadwork Development grant, an Economic Development Contingency Fund grant, an Ohio Training Tax Credit, and a low-interest loan from Ohio State Infrastructure Bank Program funds. The City of Toledo will provide a 100 percent, 15-year Enterprise Zone tax incentive on property purchases and infrastructure improvements associated with the project.
The Powertrain project in Toledo is part of GM’s plans to streamline its operations and guarantee its future liquidity. “The introduction of these new six-speeds marks an exciting new chapter in this plant’s90-year history of producing efficient, reliable, smooth-shifting automatic transmissions,” said John Buttermore, GM Powertrain vice president of manufacturing.
ProLogis — Wilmington, Illinois
Turning swords into plowshares is no easy matter, as Illinois and Will County officials learned when they tried to attract investment to Joliet Arsenal. For decades, the 3,000 acres making up the Joliet Arsenal had been used by the federal government as an ammunition plant. But in 1993, it had been declared excess Army property. The Will County area found itself facing the same opportunities and challenges faced by hundreds of communities nationwide that have endured base closures.
State and local officials sought to replace and enhance the economic benefits once generated by the federal installation. The plan was to stimulate diversified projects and land uses, creating new job opportunities. The Joliet Arsenal Development Authority was created, and an Enterprise Zone within the property was defined. For companies willing to invest in the area covered by the Enterprise Zone, various incentives were made available.
In September 2006, Illinois Governor Rod Blagojevich announced that the extension of an Enterprise Zone had secured an investment commitment from ProLogis, a global provider of distribution facilities and services. ProLogis plans to build as much as 10 million square feet of industrial space on a 770-acre area within the park. This project will accommodate regional and super-regional distribution centers, for a total expected investment of up to $300 million. This is estimated to create as many as 3,000 jobs.
ProLogis will qualify for an array of benefits. There is a 6.25 percent state sales tax exemption permitted on building materials. Also, there is an incentive called the Enterprise Zone Jobs Tax Credit. It allows a $500 credit on Illinois income taxes for each job created in the zone. Another tax incentive is the Enterprise Zone Investment Tax Credit. It applies to qualified investments in machinery, equipment, and buildings. Finally, the Illinois Department of Transportation is working on an initial $2 million agreement with the Joliet Arsenal Development Authority and ProLogis for road improvements at the site.
RBS Greenwich Capital — Stamford, Connecticut
In June 2006, Royal Bank of Scotland (RBS) broke ground for a new facility in Stamford, Connecticut. The new facility will expand RBS’s presence in Connecticut, housing the firm’s RBS Greenwich Capital office as well as its Manhattan corporate banking operation. By the time construction is completed in late 2008 or early 2009, the facility will contain 500,000 square feet, including a 95,000 square-foot trading floor. The trading floor will accommodate 1,400 traders, making it the second largest in the world.
The project represents an investment of $400 million. It is expected to retain 700 existing jobs and create 1,150 new jobs in Connecticut in the next five years. The project’s other benefits include nearly $196 million in net new state tax revenue and $44 million in net new local revenue generated over a ten-year period. The project will also indirectly create employment opportunities in the state for 2,488 workers. Annual real disposable income is estimated to increase by $71.8 million directly and $101.2 million indirectly.
“Our state, and Fairfield County in particular, is a hub for some of the world’s leading financial institutions,” said Connecticut Governor M. Jodi Rell. “To have a company of RBS’s prominence … further demonstrates that we are making the right investments in our industries, workers, and education, and transportation systems.”
Direct government incentives to make help make the project a reality came primarily from two sources. The Connecticut Department of Economic and Community Development (DECD)pledged up to $100 million in Urban and Industrial Sites Reinvestment Tax Credits to support the project. In addition, the Connecticut Development Authority is providing a $9 million sales and use tax exemption on construction materials over three years.
In addition to benefiting from these incentives, and finding a site that meets its expansion needs, RBS has found a location that satisfies the transportation needs of its commuting employers. RBS Greenwich Capital also saw the benefit of retaining its highly skilled workforce in Connecticut.
Samsung Electronics —Austin, Texas
Building a new semiconductor foundry, or fabrication plant, is a huge, risky undertaking. These plants, which produce the integrated circuits that are at the heart of many electrical and electronic devices, require expensive equipment, are subject to wide swings in customer demand, and may become obsolete if chip-making technology requires the creation of entirely new plants. However, chip makers can be encouraged to invest in new fabrication plants, or fabs, if public authorities offer to share the risk. Typically, local communities offer competitive packages of financial and infrastructure incentives.
When Samsung Electronics indicated it intended to build a new 300-mm fab, chief rivals to have Samsung invest in their communities included New York and Texas. According to press accounts, the New York offer was larger, but Samsung ultimately decided to build its new plant in Austin, next to its existing 200-mm fab. Once complete, the 300-mmfab will be the size of nine football fields, which will make it the largest fab in the U.S. This new facility will be capable of producing the latest in flash or DRAM memory chips using design technology in the 50-nm range.
Initially, Samsung will invest $220 million in its Austin operations, which already represent an investment of $1.9 billion. Eventually, costs may run as high as $4 billion. According to Samsung, the new investment will bring greater cost competitiveness to its Austin operations. In addition, Samsung indicates it will be able to enhance customer support for the increasing local demand for memory chips.
It is estimated that the new plant will create 900 jobs. The payroll could exceed $50 million. To secure these benefits for Austin, Texas officials presented an array of incentives that totaled $233 million.
“We are thrilled that Samsung chose Austin,” said Tim Crowley, Chair of the Greater Austin Chamber and President of the Community Banking Group for Frost Bank. “Samsung has been a major economic influence in our region and clearly will continue to be one as we grow and prosper together.”
Gulfstream Aerospace — Savannah, Georgia
Gulfstream Aerospace, a wholly owned subsidiary of General Dynamics, has announced plans for a $300 million, seven-year expansion of its manufacturing and service facilities in Savannah, Georgia. As a result of the expansion, employment at the facility is expected to grow by some 1,100 jobs, a 25 percent increase from the current employment level of 4,300 employees.
“In the past four years we’ve seen strong, steady growth in our industry,” Gulfstream President Bryan Moss said. “From 2004 to 2005, we experienced a 12 percent increase in aircraft production at our Savannah facility and we have every reason to believe that growth will continue. This expansion is necessary to meet the industry’s projected increase in demand for new business-jet aircraft and the maintenance that will follow.
“While Gulfstream may be an international company, our roots are deeply embedded in Georgia and Savannah ,” Moss continued. “We appreciate the assistance and cooperation we have received from the Georgia Department of Economic Development, the Savannah Economic Development Authority, Chatham County and the City of Savannah in supporting our site expansion.”
To ensure a growing pool of potential employees to fill the more than 1,000 jobs created by this expansion plan, Gulfstream will participate in new job training programs. In addition to the State of Georgia’s Quick Start program, Gulfstream will work with Savannah Technical College on programs specially tailored for Gulfstream’s employment needs.
As part of the expansion, Gulfstream will upgrade site infrastructure, including improvements to the railway delivery and water drainage systems. Gulfstream, the Georgia Department of Transportation, Chatham County, and the City of Savannah will work together to improve traffic access routes to Gulfstream’s facilities.
Edward Jones — St. Louis County, Missouri
To financial firm Edward Jones, the logic was irrefragable. First, baby boomers, aging and in need of retirement planning, posed an unprecedented growth opportunity. Second, for Edward Jones to seize this opportunity, the firm would have to expand its far-flung network of investment representatives, who typically occupy one-person offices. Third, to support the additional representatives, Edward Jones would need to enlarge its central offices.
For the most part, Edward Jones keeps its support staff in three campuses in St. Louis County. And as of October 2006, it is clear Edward Jones will continue to do so, even though the staff will quickly grow. Edward Jones announced it planned to redevelop its campuses in St. Louis County while adding at least 500 jobs in the next five years. By 2016, the number of new jobs created is expected to total at least 1,000.
Key components of the Edward Jones expansion plan include:
• improvements to area roadways, including replacement of the I-270/Dorsett Road interchange to improve safety and increase its ability to handle traffic
• three new office buildings and corresponding parking garages at North Campus by the end of 2011, resulting in 650,000 square feet of new office space; some of the new buildings will replace smaller buildings dating back to the 1960s
• a new 250,000-square-foot office building and corresponding parking garage adjacent to the firm’s headquarters location Manchester/Ballas Road, called “South Campus” by the firm. Edward Jones will seek approval from the City of Des Peres for this expansion.
Edward Jones anticipates investing up to $260 million in new construction in the next five years and donating land for road improvements. To encourage this investment, incentives were provided by federal, state, and local institutions. Funding for the interchange alone reached $30 million. Other incentives encompassed jobs programs, real property tax abatements, and a sales tax abatement linked to purchases of construction materials.
Subaru of Indiana Automotive (SIA)/Toyota — Lafayette, Indiana
In March 2006, Toyota confirmed that it would begin manufacturing automobiles in Lafayette, Indiana. The vehicles will be produced at the Subaru of Indiana Automotive (SIA) plant, where Subaru vehicles have been rolling off the assembly line for over 16 years.
Both SIA and Toyota issued production forecasts for 2007. Subaru expects to produce about 125,000 vehicles. Toyota plans to add about 100,000 to this number. About $230 million will be invested to install Toyota’s Camry manufacturing processes in an existing SIA line.
Over 2,000 are already employed at the site. Another 1,000 jobs will be created to accommodate Toyota’s operations. “This is just what our local and state economy needs. What a shot in the arm,” said Gary Henriott, chairman of the board of the Lafayette –West Lafayette Economic Development Corporation (LWL-EDC). Henriott also indicated that for every job created at SIA, at least another four or five jobs would be created elsewhere in the community or state.
“The potential economic payback is enormous, affecting every sector of our economy from jobs to housing to retail, service and our quality of life,” said Cinda Kelly, executive director of the LWL-EDC, which assembled the incentive package and worked closely with the automotive companies. “These are the jobs we want. This is an investment we want. And we put our heads together to make the best local offer possible.”
To attract the investment, city, county and state officials assembled an incentive package totaling approximately $23.5 million. The package included tax breaks, workforce training funds, and an infrastructure grant. The governor and the Indiana Economic Development Corporation, along with state representatives, even came together to support the project by passing the Indiana Single Sales Factor legislation. This legislation was important to Toyota because it recognized that most corporations do business in many states. The legislation, which includes the Indiana Single Sales Factor provision, promises future benefits to many of Toyota’s tiered suppliers, which have investments in Indiana and outside the state.
Quad/Graphics — Sussex, Hartford, and Lomira, Wisconsin
In an account of its humble beginnings — 11 employees, a rented press, and a borrowed binder housed in a 20,000-square-foot building — Quad/Graphics credits its rise to prominence to a long-held belief: If you build plants, work will come. A similar belief may have inspired the State of Wisconsin, which has extended job creation incentives to Quad/Graphics. Wisconsin could state this belief as follows: If you build a business-friendly climate, the plants will expand.
Through $300 million worth of investments in three of its Wisconsin plants, Quad/Graphics has reinforced its position as the nation’s most technologically advanced printer of magazines, catalogs, direct mail, and other commercial products. The company, which employs approximately 6,500 people from its Sussex, Hartford, and Lomira, Wisconsin locations, recently completed the installation of seven new presses, two high-density storage systems capable of storing tens of thousands of pallets of work in process, and a high-volume trim wastepaper collection system. The Wisconsin Department of Commerce is providing up to $3 million in tax credits for creating up to 750 new jobs connected with the investment.
“All these investments increase our competitiveness and increase our need for highly skilled individuals,” said Joel Quadracci, Quad/Graphics president and CEO. “To its credit, the State of Wisconsin recognizes the value employers like Quad bring to the state’s economy by offering job-creation incentives.”
Quad/Graphics is the largest privately held commercial printer in the Western Hemisphere. Founded in 1971 with a single location in Pewaukee, Wisconsin, it now has nine print-production facilities nationwide as well as a network of prepress, graphic design, photography and sales locations. With sales of $1.9 billion, Quad/Graphics employs approximately 6,500 people in Wisconsin and 12,000 people worldwide. Quad/Graphics was named one of Fortune’s “100 Best Companies to Work For,” 2006.
Swedwood North America — Danville, Virginia
In October 2006, Swedwood North America, a subsidiary of IKEA, announced it had decided to build its first U.S. manufacturing operation. Swedwood will locate the operation in Cane Creek Centre, an industrial park jointly developed by Pittsylvania County and the City of Danville. At this site the company expects to employ up to 740 people. They will help produce furniture for IKEA home furnishing stores in North America.
The Swedwood manufacturing facility represents a $281 million investment. The facility will be completed in phases, with Phase 1 to be completed by the end of 2007. At the end of this phase, the facility will cover 810,000 square feet and employ 270 people.
Local officials stressed the importance of matching Swedwood’s “fast-track” development schedule with a proactive approach. The county and city prepared the property in Cane Creek Centre for immediate occupancy. “The close proximity to many IKEA stores and distribution centers, coupled with good regional infrastructure and available land, make Danville ideal for this facility,” said Bengt Danielsson, North American president of Swedwood.
“All members of our Virginia team went to bat to win this project,” said Jeffrey M. Anderson, executive director of the Virginia Economic Development Partnership (VEDP). The VEDP worked with the City of Danville and Pittsylvania County to secure the project. These localities were also assisted by a $3 million grant from the Governor’s Opportunity Fund. The grant was approved by Governor Timothy M. Kaine, who also helped provide a $1 million grant from the Virginia Investment Partnership program.
Another member of the Virginia team was the Virginia Tobacco Indemnification and Community Revitalization Commission. It approved $2.3 million in Tobacco Region Opportunity Funds. Several other institutions indicate that the project may qualify for additional funds. For example, funds may be received from the Virginia Department of Housing and Community Development, which administers the Virginia Enterprise Zone Program. Additional incentives focus on rail and economic access grants, as well as training assistance.
Fidelity Investments — Research Triangle Park, North Carolina
With 200,000 people employed in the financial sector, North Carolina is one of the nation’s foremost states in banking. (In fact, it is second only to New York in this sector.) And North Carolina is set to become even more prominent in finance now that Fidelity Investments is building a new facility in Research Triangle Park.
The new facility represents an investment of $100 million. It is expected to bring 2,000 jobs to Wake County. Because Fidelity has about 1,000 employees based in North Carolina, the new facility will effectively triple Fidelity’s workforce in the state.
The company has been awarded a $2 million grant from the state’s One North Carolina Fund, as well as a Job Development Investment Grant (JDIG), which extends over a 12-year period. For each year the company meets required performance targets, the state will provide a grant equivalent to 75 percent of the state personal income withholding taxes derived from the creation of new jobs. If the organization creates all of the jobs called for under the agreement and sustains them for 12 years, Fidelity Investments could receive a maximum benefit of $54.6 million.
Fidelity is also eligible for sales tax refunds of up to $3.88 million and a Community College Training Grant of $4.6 million. Local incentives, which are being provided by Wake County, amount to $4.2 million from Wake County. Altogether, the Fidelity incentives may eventually exceed $69 million.
“Today’s announcement offers proof that our innovative incentives programs combined with our skilled workforce and number-one-ranked business climate provide the right mix for companies looking to locate and expand in the state,” Governor Mike Easley said. “We will continue to make the necessary investments in education, infrastructure and workforce development to support North Carolina’s financial industry.”