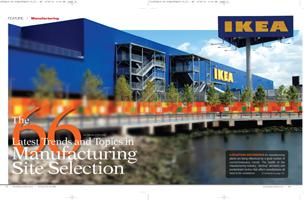
Location decisions for manufacturing plants are being influenced by a great number of current/emerging trends. The health of the manufacturing industry, “shoring” decisions and predominant factors that affect manufactures all need to be considered.
Industry Health
The U.S. manufacturing sector is more robust than it has been in decades. In most industries, U.S. manufacturing is truly globally competitive. This includes OEMs (original equipment manufacturers) and suppliers. Principal reasons for the rebirth of U.S. manufacturing are:
1. Innovation—the U.S. remains the world’s leader
• U.S. number one in patents issued per capita
• U.S. number one in GE’s Innovation Survey
• U.S. among top five in both R&D as a percent of economic output and per capita scientific/engineering talent.
2. Technology investment, which has been increasing around seven percent per annum
• lean manufacturing
• robotics
3. Realignment of supply chains
• regional as opposed to extended
• optimal efficiency
• cost-effective
• lower disruption risk
• more timely customer delivery
• greater flexibility to meet changing customer demand.
4. Cost compression vis-à-vis offshore countries, especially China (total landed cost differential likely to be under 15 percent by 2014).
5. Large, stable, affluent North American market
• industrial
• consumer
6. Customer preference for “buy American.”
7. Rebound in the U.S. economy.
8. U.S. competitiveness as a base for exporting.
9. Quality/productivity of American workers.
10. Incentives for companies to invest and expand manufacturing operations.
U.S. manufacturing began to turn the table at the beginning of this century. Since the last recession, manufacturing has been the most buoyant economic sector. Consider the following:
1. Twenty nine consecutive months of employment growth.
2. Close to 500,000 jobs were created during this time span (December 2009- May 2012).
3. Substantial spinoff employment associated with manufacturing
• 11.9 million direct jobs
• 7.1 million indirect jobs.
4. Over 286,000 manufacturing firms.
5. Huge jump in productivity, almost 30 percent since 2000.
6. Average annual capital expenditures over $160 billion since the last economic downturn.
7. Manufacturing revenue up 20 percent since 2009.
8. Exports rising sharply
• in recent years growing 10-20 percent per annum
• currently stands at $1.15 trillion (74 percent of all U.S. exports).
Manufacturing, like nearly all sectors, has encountered unexpected economic headwinds over the past couple of months. Growth has temporarily stalled. However, as the above statistics indicate, long-term prospects for U.S. manufacturing are bright. It should remain a vital and thriving segment of the U.S. economy well into the future. New/expanded operations should span nearly all industry segments, including both durable and nondurable goods. Among the highest growth industries, measured in value of shipments, are:
1. Capital goods (e.g., primary metals, machinery, fabricated metals, robotics).
2. Medical and scientific instruments.
3. Auto (OEMs and suppliers).
4. Health/beauty products.
5. Computer/electronic goods.
6. Food processing.
7. Specialty chemicals.
8. Plastics.
9. Packaging.
10. Furniture.
Geographic Concentration
As might be expected, the most populous states also have the greatest employment in manufacturing—California leads the way with 1.2 million manufacturing jobs. Rounding out the top 10 are Texas, Ohio, Illinois, Pennsylvania, Michigan, New York, Indiana, North Carolina and Wisconsin.
When measuring manufacturing’s proportion of total jobs, the top states are shown in Exhibit 1, the “Geographic Jobs Concentration” chart (we also show the contribution of manufacturing to state gross domestic product).
This shows clearly that manufacturing remains a critical economic component of the country and many states. Manufacturing has been growing in most states over the last couple of years. Among the more robust states for manufacturing job gain are Michigan, Indiana, Iowa, Oklahoma, North Dakota, South Dakota, Texas, Missouri, Washington, Colorado and Wisconsin. Not surprisingly some of the best-performing states are underpinned by large industries in a growth mode, including transportation equipment, high-technology and energy.
Deployment Strategy
Most companies today adhere to a multi-shore strategy to meet global demand. Three major differences in manufacturing deployment strategy that have occurred over the past 10 years are:
1. Less offshoring solely to reduce cost.
2. More offshoring to penetrate markets, especially in developing countries.
3. Greater reliance on the U.S. as a manufacturing base.
A mini trend has taken hold wherein corporations have reshored at least some production from China (and secondarily from other countries such as Japan and Mexico) to the U.S. Enablers are innovation, technology and productive labor. Nearly all reshoring can be justified on economic grounds. That is, cost differentials have narrowed to the point wherein the offshored capacity carries greater risk than financial reward.
Reshoring is not for everybody. Products characterized by one or more of the following traits, however, are prime reshoring candidates:
1. High value.
2. Transportation sensitive
• delivery time
• cost
3. Low to medium volume (not huge predictable volume).
4. Fluctuating demand.
5. Some customization.
6. Customer mandate for shorter
• lead time
• shipping time
• inventory level
7. Compressed order cycle.
Many industries, ranging from appliances to machinery, display such characteristics. For these industries, factors such as the following can make a compelling case for reshoring:
1. Marginal difference in total landed cost.
2. Risk associated with a long, complex supply chain.
3. Rising offshore costs
• labor
• transportation
• energy
4. Long lead times/cost of capital.
5. Inflexibility to meet changes in demand.
6. Product quality/defects.
7. Intellectual property protection/knockoffs.
8. Lost sales opportunities if not “made in USA.”
9. Leverage/synergy of manufacturing near R&D and sales/marketing.
10. Savings in management time/travel cost.
Companies that have reshored manufacturing work (mostly from China to the U.S.) are displayed in Exhibit 2:
The reshoring trend will likely continue as cost differentials compress, companies balance production in light of supplier and customer locations, and technology/innovation make U.S. manufacturers even more competitive on a global stage.
Another related and important trend is the onshoring of manufacturing that heretofore might have gone to lower-cost countries (see Exhibit 3).
Further reflecting appeal of the U.S. for manufacturing is reverse investment by foreign-owned companies. The firm of WDGC estimates that around 15 percent of new manufacturing plants built in the U.S. are owned by foreign companies. A notable trend has been investment by companies from the developing nations such as Brazil, Russia, India and China (BRIC). Like reshoring, reverse investment has been in diverse industries and geographies (see Exhibit 4).
Of course, the U.S. manufacturing resurgence has also been underpinned by companies expanding or locating new capacity in the U.S. to serve primarily a domestic market and in some cases also exporting overseas. Highlighting the industry and geographic diversity are the companies displayed in Exhibit 5.
Another emerging trend for U.S. companies still offshoring mainly for cost reasons is the Latin America option instead of or along with Asia. This “nearshoring” alternative can be cost-competitive with Asia while also allowing companies to serve both fast-growing South/Central America markets and the U.S. A few nearshore examples are displayed in Exhibit 6.
Overall, most manufacturers are pursuing an allshore model, with the U.S. playing a more important role than at any time in the recent past. Companies will continue to regionalize their supply chains and manufacturing capacity to better serve customers, reduce risk and keep costs under control. The catchphrase that most aptly describes geographic deployment strategies for manufacturers is global localization. In light of the reasons mentioned, this bodes well for impressive manufacturing growth in the U.S.
Primary Location Factors
When siting a new manufacturing plant, the first challenge is to delineate controlling parameters. This embodies the following:
1. Why is a new facility required?
2. Can anticipated demand be effectively met by expanding any existing company facility?
3. Given end-to-end supply chain and customer locations, what geography should be considered?
4. When does the new plant need to be operational?
5. What would be the ideal characteristics a new location might possess to provide a competitive edge?
6. What locational criteria are:
• must haves (no tradeoff)
• strongly preferred (some tradeoff okay)
• nice to have (desirable, but fair amount of tradeoff acceptable)?
7. What are milestone tasks for both completing the study and getting the new facility up and running?
8. How will the new operation be financed?
9. Who will assume responsibility for requisite tasks before, during and after the site selection study?
10. What are the ground rules for project confidentiality?
In evaluating any location, be as forward-looking as possible. An area’s locational assets as they appear today need to be sustainable to maximize success potential of the new plant. Therefore, addressing questions such as the following will be important:
1. Given competitive demand and talent pool depth, will there likely be a labor shortage with cost escalation and turnover consequences?
2. Will there be sufficient electric power capacity in the future?
3. Will electric power costs be relatively stable?
4. Will there be significant change in the geographic clustering of customers and/or suppliers?
5. Will transportation costs markedly increase due to considerations such as customer concentration and energy cost?
6. Are state/local governments fiscally solid so future services and taxes will be stable?
7. Does the site/building allow for sufficient and efficient future expansion?
8. Are there industry retention incentives especially for capital investment (even if few jobs are created) enhancing your ability to stay at the location and remain globally competitive?