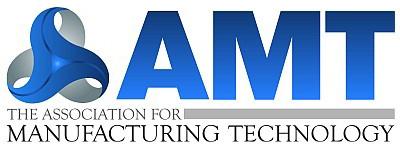
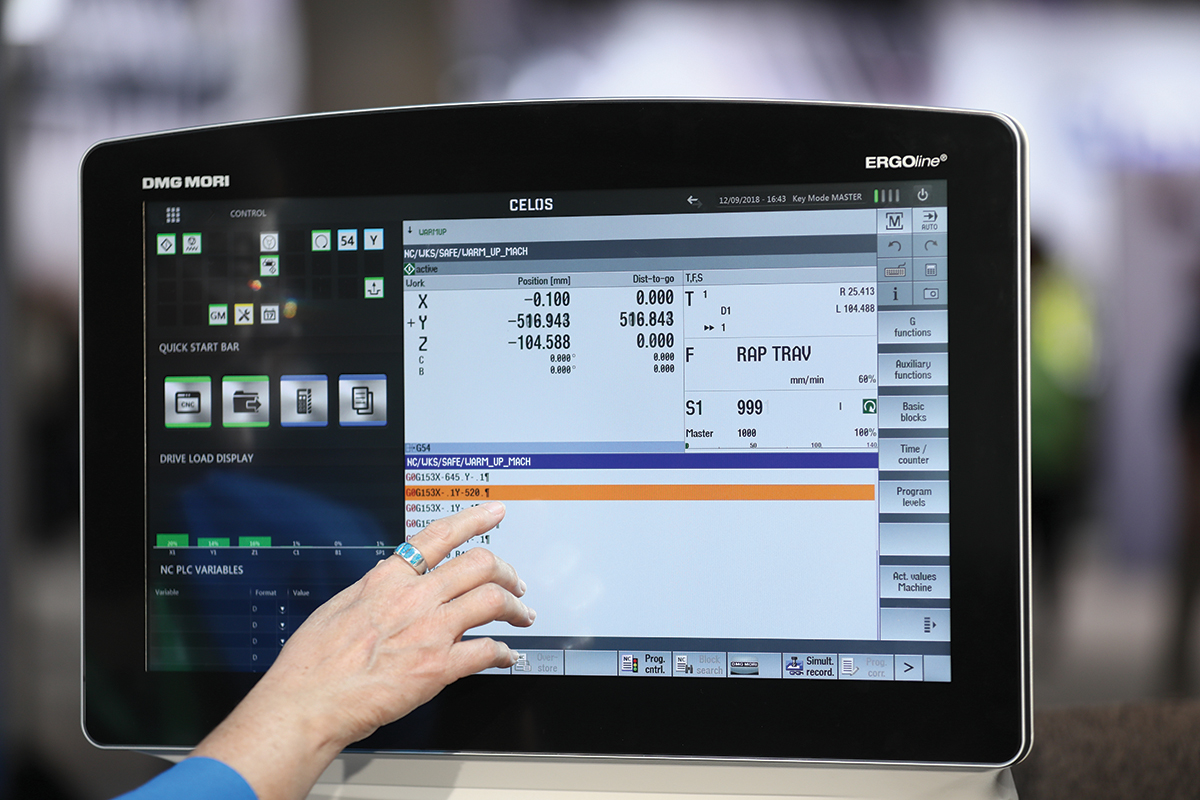
As market preferences shift toward a desire for customized products, manufacturers are left to reinvent their operations accordingly as they move toward mass customization. Consumer preference is toward a product that stands out from the crowd or meets a unique need. It’s a dramatic shift from when manufacturing was instead defined by repeatability, productivity and price point.
Case in point: Henry Ford once said of the Model T, “Any customer can have a car painted any color he wants, so long as it is black.” Now it’s said his namesake motor vehicle company can make more possible variations on the F-150 pickup than there are trucks on the road.
The industry is still a long way from achieving that “one item lot size.” That’s also just one of many radical and extraordinary shifts that are moving the industry from its mass production past — the one so familiar up until just recently — to a future that is both exciting and challenging. Following are some of the technologies that are enabling the dramatic transformation.
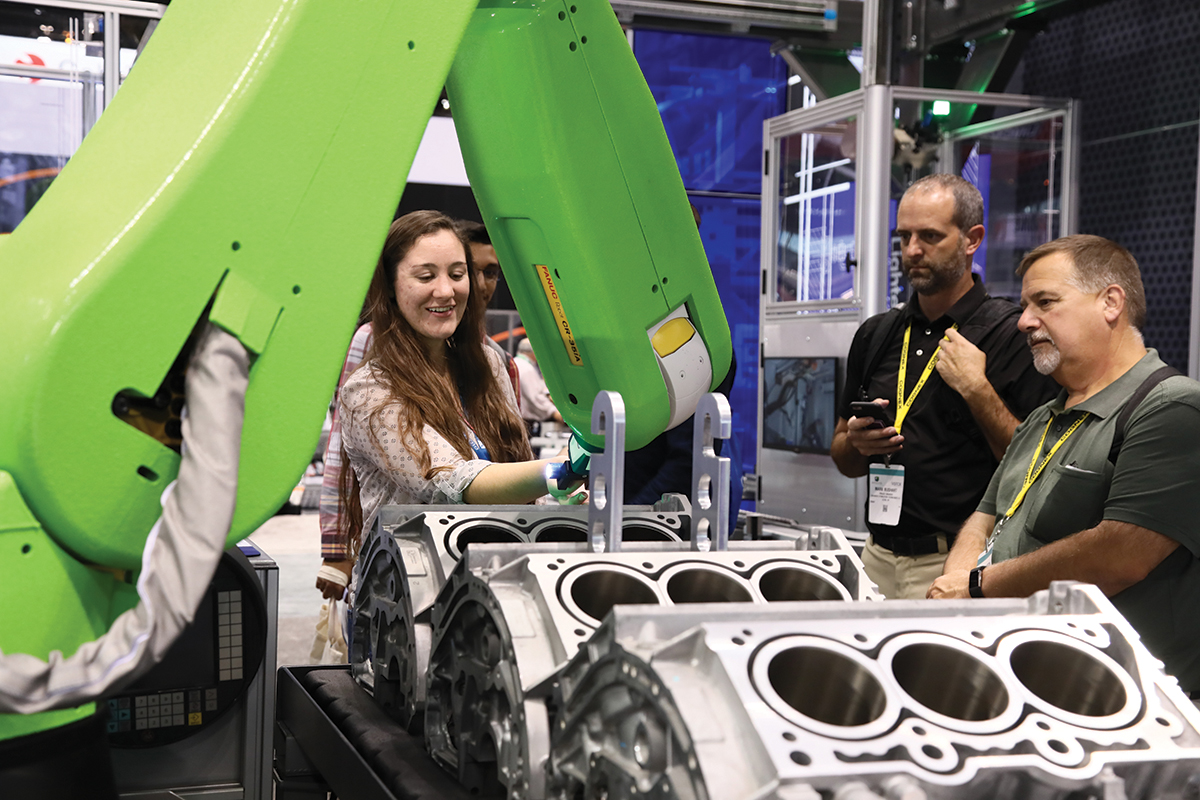
Through machine learning and artificial intelligence, those finished products can also discover opportunities for better performance. One example is how a gas turbine developed by Siemens uses sensors to continuously track temperature, pressure, stresses and other variables. By collecting and analyzing that data, then adjusting its fuel valves for optimized combustion, the turbine is able to reduce its nitrous oxide emissions by 10 to 15 percent.
On the shop floor, machine learning also allows for operational improvements by minimizing transition times, improving materials and parts inventory, maximizing machine up time and productivity and reducing waste. A recent study from PwC predicted a 38 percent increase among manufacturers in the use of predictive maintenance over the next five years, in which maintenance takes place based on a machine’s data about its conditions, vs. at prescribed, preset intervals, allowing a cost savings since maintenance is performed only when it’s needed.
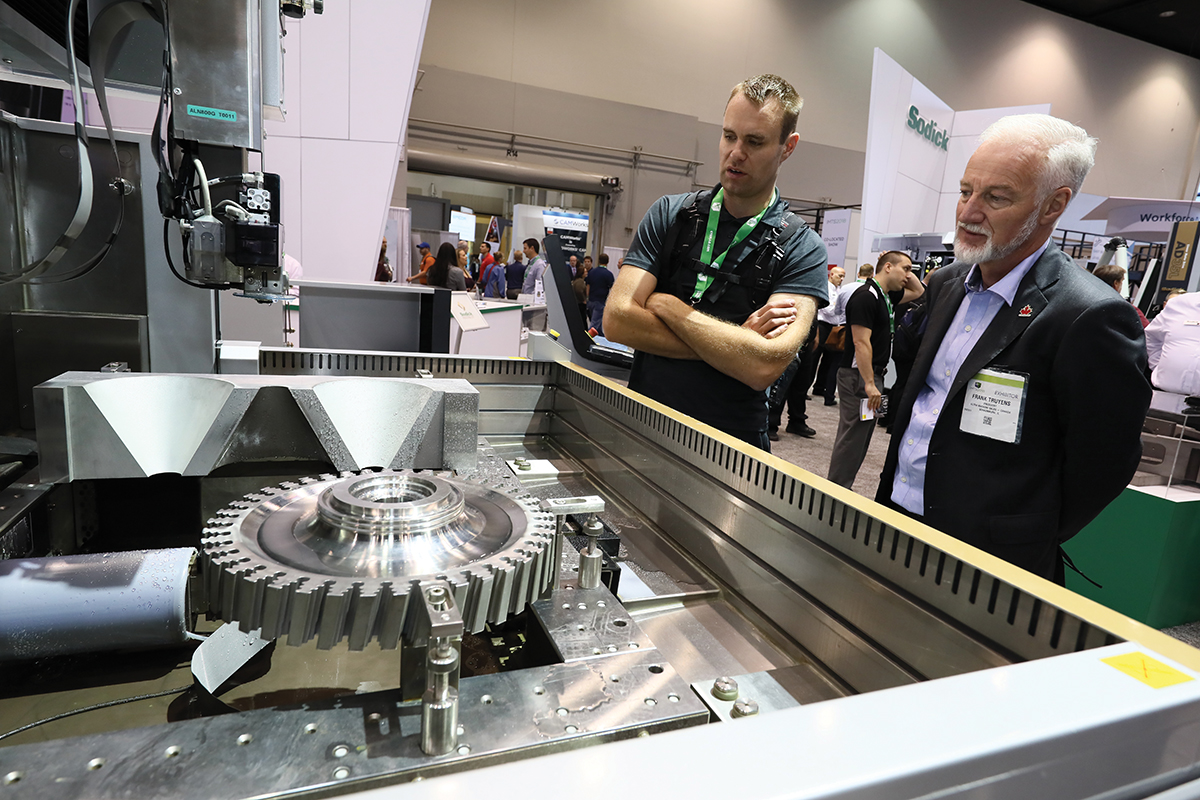
Edge computing is made possible by that above-mentioned machine learning, but also by increased reliability and lower cost for sensors, more computing power taking place in smaller devices, and the always-increasing volume of data that comes off of those sensors as they track machines, processes and products.
Virtual reality: The skills gap is the reason for a dramatic shortfall in workers for the advanced manufacturing industry. While manufacturers are seeing real opportunity to expand their capacity and output, they are often held back due to an inability to find the workers they need to keep production lines running.
While a long-term, sustainable solution to the worker shortfall will require a holistic approach between industry, academia and government, companies are scrambling to use any technology that will allow them to train and develop workers as efficiently as possible. With virtual reality, trainees can get a hands-on experience in doing tasks related to machine setup and operation, as well as installation and service, without the risks involved with training on actual machines.
Manufacturers are also using virtual reality for inventory management, product design and build, and planning factory layout. Machine builders, such as those who are members of AMT – The Association For Manufacturing Technology, are using virtual and augmented reality to diagnose service issues, allowing service techs to “look at” machines regardless of location. Customers can be walked through the repairs that they can make for themselves, or a service tech can be sent to a location already prepared with precise information about needed repairs and equipped with the right parts and tools.
Iterative design: One way to think of the concept of iterative design is “design as you go.” Rather than developing a finished product and considering it “done,” a design is instead tested at various points throughout its development to immediately receive and implement user feedback into future versions of the design. In this way, design flaws are caught sooner in the development process. The user experience and product usability improve measurably; and designs are produced more efficiently and cost effectively.
It’s both an exciting and challenging time for the industry as it explores the possibilities and challenges that come with its emerging digital revolution. The excitement of burgeoning digital technologies also brings fears about technology obsolescence, missed opportunities, or cyberphysical attacks that could harm asset or product integrity. Nonetheless, a responsive digital strategy will be a survival necessity for manufacturers of all sizes. T&ID