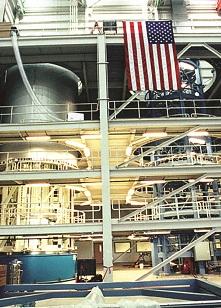
The metals industry (also referred to as metal manufacturing) covers a broad and expansive segment of the U.S. manufacturing industry. Traditionally, any industry or product that involves bending, forming, machining, welding and the assembly of a metals product or products is included within the metals industry.
Areas of Geographic Concentration/Emerging Regions
While the metals industry plays a significant role throughout the United States, several geographic concentrations have emerged historically and continue to impact metals industry location. The map on this page depicts the seven states that were consistently ranked among the top-tier metals locations based on the value of finished product shipments for each of the five NAICS industrial sectors as follows:
• Primary metal manufacturing (NAICS 331)
• Fabricated metal product manufacturing (NAICS 332)
• Machinery manufacturing (NAICS 333)
• Electrical equipment, appliance and component manufacturing (NAICS 335)
• Transportation equipment manufacturing (NAICS 336).
In addition, three of these seven states (Ohio, Texas, and California) are consistently ranked among the top 10 states for each of the five NAICS industrial sectors based on the total value of finished products.
There is also a strong correlation between the value of finished product shipments and the number of establishments, annual payroll and paid employees in each state. It is interesting to note that the traditional manufacturing belt from Pennsylvania to Illinois continues to be a major economic force within the metals industry. Adjoining states such as Wisconsin and New York also received high marks in the analysis.
While not consistently represented as a top region based on the analysis performed, the southeast United States is becoming a viable alternative to the traditional manufacturing belt. Based on information from the five NAICS industrial sectors reviewed, the following states appear to be increasing their share of metal manufacturing establishments, annual payroll and employee growth at a faster rate than the traditional manufacturing areas discussed earlier:
• Alabama
• Georgia
• North Carolina
• South Carolina
• Tennessee.
One reason for this increase could be the amount of new plant openings within this area with more efficient production capabilities versus the states to the north. Also, labor relations including right-to-work laws often favor a new location in the southeast.
Key Components / Considerations Involved in the Site Location Process
Companies will often hire a professional site location organization to assist in selecting a location for a new plant within the metals industry. Typically, most firms hiring a consultant are in the expansion mode, meaning they are looking to add a new plant for production due to product growth and positive market conditions.
Site location considerations within the metals industry, for the most part, follow a similar path with other industries when considering a new location. The approach or goal in securing the optimal plant location is finding the right location that provides a balance between the following competing interests:
• Minimizes annual estimated operating costs (including inbound raw material sources, outbound freight destinations, labor and fringe benefits, electric power, natural gas, water, wastewater, and telecommunications, taxation at the state and local level)
• Minimizes one-time costs (initial start-up costs including site purchase, site development / preparation / permitting, utility extensions and impact / connection fees, construction costs, and others determined during the study)
• Minimizes risk (including labor shortages / labor relations, site issues such as identifying all potential environmental hazards, addressing site concerns such as soils and load-bearing capacity for intended use, permitting and zoning concerns, and others determined during the study).
Again, the goal is to provide the best location that minimizes all annual and one-time costs while at the same time avoids all risk factors that could jeopardize and delay the process.
Typically, the most important annual operating costs for companies in the metals industry (based on order of significance) are:
1. Transportation Logistics / Support Services -- including inbound and outbound freight
2. Labor -- including availability and training
3. Energy -- primarily electric power and natural gas.
While other operating costs (namely, water, wastewater, state corporate and local property taxation) do influence total annual operating costs, the experience within the industry of site consulting firm Austin Consulting indicates that transportation, labor and energy will account for over 70 percent of total annual operating costs for a new plant. It is also the company's experience that if these major operating conditions are not adequately addressed during the process, all the potential incentive and assistance programs cannot overcome a poor location decision.
1. Transportation Logistics/Support Services
A transportation or logistics analysis must be conducted in the early stages of the site location process. For the metals industry in general, proximity to industrial raw materials sources as well as final-destination customers is an important site location consideration.
The company must also consider the most economical and viable mode of shipment (i.e., truck, rail, air, water) to bring products in and ship out. Shipment urgency and frequency is another important consideration that will dictate the new location.
Last, a five- or even a 10-year sales projection is necessary to assist in identifying key source locations for raw materials and in identifying current and potential customers to develop a realistic cost matrix to identify the best location for the new plant.
In addition to securing the low-cost area for major inbound and outbound freight, a location or area in close proximity to important support services is often critical to the metals industry. Depending upon the nature of the end product to be manufactured, important support services either located within the community or area (i.e., within a 60-mile radius) often include:
• tooling and maintenance support
• metal heat treating
• specialized welding
• metal plating and anodizing
• basic machine/fabrication shops.
2. Labor
To some companies in the metals industry, labor costs and availability are the most important considerations in securing a new location. Labor costs are typically investigated by the consultant using internal wage and benefit information, government sources, local and regional wage and benefit surveys and by conducting confidential labor interviews with local area employers during the field investigation phase of the site search.
During this time the consultant should also conduct additional research to investigate labor relations including any unionization concerns at the local or regional level. This issue is also best discussed during interviews with local area employers.
In addition to costs, labor availability and trainability must be fully investigated at the community level during the site search. Most expanding companies are relying on the local or regional area to satisfy their employment needs. Before a company or consultant conducts any field work in the community, they must know ahead of time the positions, skill levels and number of employees necessary to operate the new plant.
A company must consider not only the immediate start-up needs, but also consider the projected needs (i.e., three- to five-year projection) to successfully and efficiently operate the plant. For the metals industry, important job positions for the traditional, non-exempt or hourly level include:
• tool / die / mold machinists, including CNC numerical controls experience
• machine repairers, numerical control expertise
• maintenance positions, including electrical and mechanical
• metal fabricators including certified welders and heat treating operators
• process machinery operators, numerical control expertise
• line assemblers
• warehouse operations.
In addition to the non-exempt workforce, the following exempt or salary positions are equally important to the company:
• engineering professionals, including quality control, mechanical and industrial
• quality control inspectors
• supervisors, including maintenance, production, manufacturing.
Before conducting any direct field investigation on labor, it is important for the consultant to conduct a “due diligence” on the community and surrounding area's current industrial base to determine if it is a good fit for the proposed plant.
As stated earlier, a good community for the metals industry contains good support services in that sector. Typically, if there are good support services at the community level for the metals industry, that location should contain a strong concentration of metal industries within the community’s industrial base. If this is the case, an existing workforce in the sector could be available for employment. The community may also possess a local technical school or college with a good background on training workers for the metals industry.
During the field investigation phase of the site search, the consultant will discuss with local area employers the availability of training resources at the local level and their overall satisfaction with the technical school’s ability to train the workers. The consultant will also tour and inspect the local technical college, their classrooms and equipment used to train the workforce within the metals industry.
Meeting with college administrators and instructors and a review of the curriculum is also critical during the tour, especially reviewing coursework for certification in CNC machining, welding and electrical and mechanical maintenance. In addition, the consultant should review total enrollment numbers and employment opportunities for graduating students within the community. Last, discussions on state and local training grants to train the necessary workforce must be initiated during the visit.
![]() |
125,000-Square-Foot New Manufacturing and Office Facility |
3. Utilities
Utility availability often constitutes the third major cost consideration for most metal industries. Typically, electric power and natural gas are the major cost components for the metals industry, with electric power being the most important utility consideration.
Before conducting any field investigation, the company and their consultant must have a clear determination of the anticipated electric power needs that are necessary for the new plant. Also, with some very large users in the metals industry (i.e., over 5,000 kW demand), direct service off a transmission line may be a viable option over traditional distribution service.
Important electric power considerations to be investigated at each site during field investigation include:
• estimated utility bills based on the desired service
• substation capacity, including reserve capacity
• distance to substation
• feasibility of dual-feed service from different substations
• cost of infrastructure improvements
• special incentive rates to reduce costs
• others determined during the course of the study.
A similar set of questions pertaining to natural gas availability would also be discussed with the gas provider servicing each site during field investigation.
In addition to the three major operating costs discussed, additional cost and non-cost considerations in the metals industry include:
• site acquisition and site development costs
• municipal water and wastewater costs
• corporate state and local property taxes
• fringe benefit, including Workers Compensation costs
• permitting and building costs
• determination of employee/family relocation costs
• others specific to the industry.
![]() |
Relocation and Installation of Existing and New Gear Production Equipment |
The Role of Incentives in the Metals Industry
Until now, potential incentive and assistance programs at the state and local level have not been discussed. Incentive and assistance programs offered to potential projects at the state, regional and local level are typically directly correlated to the following:
• total project investment
• expected employment
• estimated payroll.
As stated earlier, Austin Consulting strongly advises that important considerations such as minimizing transportation/logistics costs, labor (including availability) and utility costs be the prime considerations before finalizing any incentive package. Detailed incentive negotiations should only be pursued once all annual operating, one-time operating and non-operating costs, including mitigation of all perceived risks have been thoroughly reviewed, analyzed and tabulated. Once this is thoroughly completed, the company and its consultant will be in the best position to secure the necessary assistance programs that address any gaps or shortcomings at the state and local level.
This approach is also important to the finalist community and selected state since they will be in a better position to finalize a meaningful incentive package that will truly benefit the company for today and the future.