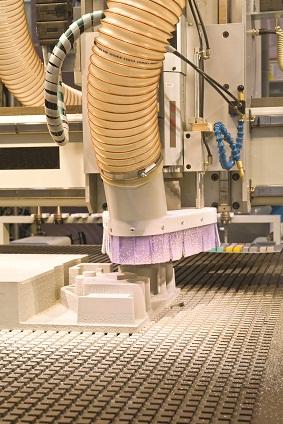
“There's so much plastic in this culture that vinyl leopard skin is becoming an endangered synthetic.”
This cryptic observation by one of America’s wittiest comediennes, Lily Tomlin, satirically points out the pervasiveness of plastics throughout daily life. Plastics are involved in virtually every industry and in most of the consumer products we come in contact with throughout our lives. The universal application of plastics even renders the term as a lexicon for social values.
To correct Ms. Tomlin, technically, vinyl is a plastic. The material has roots tracing back to the 1800s in Europe when researchers discovered a material made in a compound from gaseous vinyl chloride. Considered by many as a curious but useless rigid material, vinyl did not find commercial life until the 1930s when Polyvinyl Chloride, or vinyl, was first utilized as shock absorber seals as a substitute for natural rubber. Vinyls are now most commonly used in automobile seat covers, shower curtains, raincoats, bottles, visors, shoe soles, garden hoses and mannequins.
Defining the Plastics Industry
The production of plastics can be roughly divided into four categories. The first is the acquisition of the basic raw material or monomers, molecules that can bind themselves to other molecules. The second is the synthesizing of monomers into different combinations known as polymers. A third category is the compounding of polymers into materials that are ready for use in fabrication. And the fourth is the molding or shaping of plastic into its final form.
According to SPI, the plastics industry trade association, the industry is the third-largest manufacturing industry in the United States, providing significantly to the nation's economy. The U.S. plastics industry employs nearly 900 thousand workers and generates more than $341 billion in annual shipments. There are nearly 18,500 plastics facilities in the United States.
The plastics industry has a presence in every state. From 1980 to 2010, U.S. plastics industry shipments have grown at a 2.4 percent annual rate and productivity in plastics manufacturing has grown 2.3 percent per year, which is better than the 1.9 percent per year productivity growth for manufacturing as a whole. In 2010, the U.S. plastics industry had a $16.2 billion trade surplus.
Reshoring of the Plastics Manufacturing Industry
Due to the widespread role of petroleum by-products in basic plastic manufacturing, plants were located near major hydrocarbon production areas such Texas and Louisiana. More recently, lower-cost facilities have been located along the Gulf Coast, but also in oil-rich regions of Asia and the Middle East. Today, it is common for many plastic materials to be imported to the United States.
Plastics fabrication, on the other hand, has a much lower cost of entry, and fabricators are more likely to be located near the markets they serve rather than close to the source of raw materials or inexpensive labor. Whereas plastics production facilities cost hundreds of millions of dollars, plastics fabrication facilities can be built for far less.
Unfortunately, a large amount of fabricated plastic parts come from Asia, particularly China, which has undermined numerous facilities across the United States. However, reshoring of some plastics fabrication, notably plastic bottles, appears to be a growing trend. One reason is the impact of the rise of wages in China which have nearly doubled in the last decade. Added to this are the value of the U.S. dollar versus the Chinese RMB and the costs of fuel for ocean-transit vessels.
What may be the most significant advantage of reshoring is the issue of lead time to market. While overseas shipping often requires 30 days or more, domestic transportation can be shortened to less than a week. For distributors, that can translate into higher levels of stock availability, more efficient quality control and shorter lead times for special orders. For environmental rationale, the carbon footprint is significantly less.
Harry Moser of the Reshoring Initiative, the guru of reshoring, points out that the labor advantage of China over the U.S. may evaporate as soon as 2015, thus negating the need to offshore plastics fabrication and mold making. Mr. Moser points out that many American companies have made sourcing decisions based on a quoted price while ignoring the total cost of offshore manufacturing, thus incurring hidden costs.
Citing Mr. Moser, the costs that American companies often overlook include emergency airfreight, travel and the negative impact on innovation of separating manufacturing from engineering. These and other frequently overlooked costs usually account for as much as 20-30 percent of a company's total cost of offshoring.
Practical Site Selection Guidance for the Plastics Industry
Leading companies in the production of plastic resins and basic shapes continue to rely on petrochemicals as raw material and the impetus for site location advantages will continue to be driven by the price of oil. As the political environment strives to narrow U.S. dependence on foreign oil, new domestic sources may encourage a wave of site locations close to finds of new oil, oil sand and shale oil. This may mean that untapped plastic production states such as Alaska and North Dakota could eventually rival traditional locations such as Louisiana and Texas.
With the paradigm shift toward green technologies, production strategies are beginning the transition to bioplastics, which are derived from renewable biomass sources such as vegetable oils and fats and corn or other starches, cane sugar or glucose. Bioplastics production facilities utilizing organic materials will be situated closer to strategic sources of the raw materials in order to take advantage of transportation efficiencies and low land costs. For example, a bioplastics plant processing cane sugar could be based in Palm Beach County, Florida, one of the largest sugar cane agricultural areas in the country.
Chemical processes are, by their nature, large users of electric power and, therefore, industrial electricity rates will continue their role as a key driver for plastic production location decisions. The U.S. Energy Information Administration has determined the U.S. states that have the lowest 2012 rates for industrial electric power, which are shown in the chart on this page.
For fabricators, labor costs will continue to influence locations tactics, and available labor and wage ranges for skilled labor, especially mold makers, will play an important role.
The Bureau of Labor Statistics classifies mold makers as having a 2011 national employment of 5,780 and a mean wage of $22.34 per hour. Leading manufacturing industries for employment of mold makers include the Motor Vehicle Parts, Aerospace Products and Parts, Motor Vehicles, and Plastics Products.
States with the highest employment level of mold makers are led by (1) Michigan, (2) Illinois, (3) Tennessee, (4) Wisconsin, and 5) California. Mean hourly wages for mold makers range from a low of $14.11 to a high of $29.16.
The 10 lowest-cost states for this occupation are as follows:
1. Tennessee $14.11
2. Louisiana $16.98
3. Texas $17.20
4. North Carolina $18.29
5. Missouri $19.32
6. Nevada $19.47
7. Colorado $19.67
8. Kansas $20.01
9. Arkansas $20.26
10. New York $20.31.
For new facilities, corporate site selectors will need to reconcile the allure of wage savings of various markets against the nature of the industry being located. Due to plastics fabrication’s high concentration of Volatile Organic Compounds, or VOCs, some municipalities have imposed strict restrictions on locating plastic companies within proximity to residential areas. Given that offshoring of many plastic industries has furloughed numerous former plastic fabrication facilities, conversion or upgrade of these available buildings may present opportunities for start-up cost savings as well as a means to leverage pre-approved or grandfathered site restrictions.
Smaller operations may be especially able to profit by the acquisition of used facilities and equipment. Capacity additions may be made by incremental investment in machinery so the investment can be scaled with business growth. Since plastics are most economically shipped in bulk by rail, former plastics fabrication facilities are often located on rail sidings.
In nearly every state, new tax incentives are being developed for recycling of plastics and fabricators should be viewing this movement as a means of developing additional revenue streams. Recapture and recycling of production output could represent a way for fabricators to lower costs for raw materials. Forward-thinking companies are analyzing the tax incentive offerings by host communities carefully in light of the need to balance the public outcry against landfill overflow by disposable plastic products.
The Future
Anyone who has ever had to rely on a pair of scissors to open new plastic packages recognizes that plastics are getting stronger. What does the future have in store? Clearly, new scientific formulation and advanced materials hold the key. Carbon Fiber Reinforced Polymers (CFRP) are making Henry Ford’s vision of plastic automobiles a reality, as evidenced by BMW’s progress on carbon fiber body panels.
The use of switchgrass as an optimum biomass source for plastics is being widely considered. New technologies for plastic production such as polymer production from carbon dioxide promise fantastic visions of curing greenhouse emission problems.
Whatever direction plastics take in the future, innovation will most likely come from the United States. That means that partnerships between industry and academia will continue to play important roles. By concentrating manufacturing operations in proximity to engineering resources, producers and fabricators can maintain quality control and reduce lead time to market. In recognition of the opportunities of domestic production, companies can benefit from plentiful sources of raw materials, available labor and facility options to keep the plastics industry as one of the premier forms of American enterprise.